Custom Geothermal Drill Bits Manufacturer in China
We offer a comprehensive range of geothermal drill bits, specifically engineered to withstand the extreme temperatures and abrasive rock encountered in geothermal well drilling. Our bits are designed for superior durability and high penetration rates, minimizing downtime and maximizing efficiency for your projects. We provide reliable solutions for harnessing the Earth’s power.
Sinodrills - Your Trusted Geothermal Drill Bits Manufacturer from China
Battling short bit life and slow penetration in tough geothermal formations? High temperatures and abrasive rock chew through inferior tools, costing you time and money. Sinodrills is your solution. As your trusted geothermal drill bits manufacturer from China, we deliver high-performance, durable bits engineered for extreme conditions, ensuring efficient, profitable drilling.
Various Geothermal Drill Bits
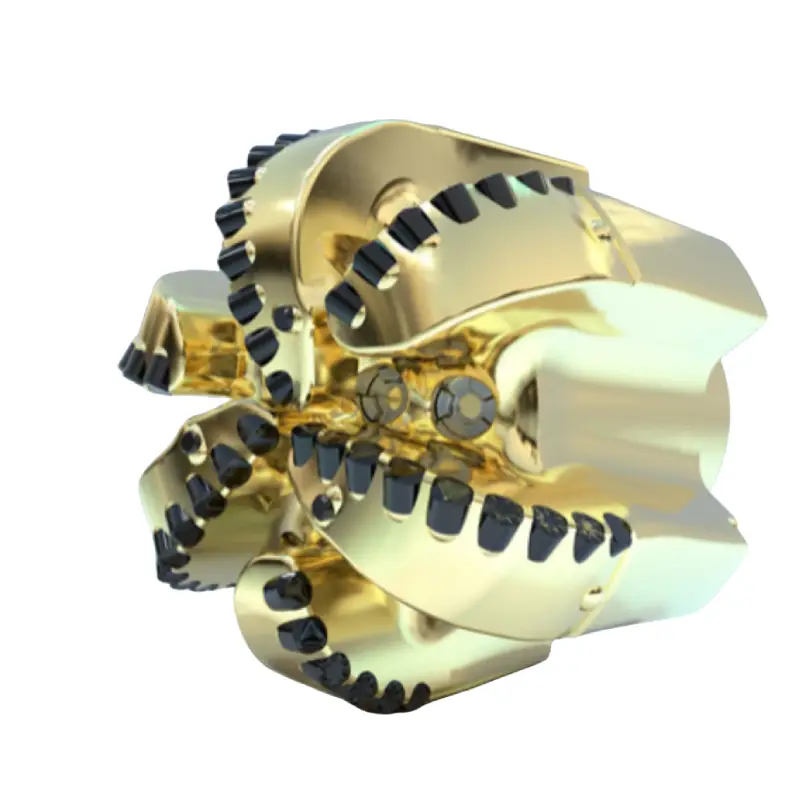
geothermal PDC drill bit
We offer high-performance geothermal PDC drill bits, specifically designed to tackle the extreme temperatures and abrasive rock prevalent in geothermal drilling. Our PDC bits feature robust synthetic diamond cutters and advanced designs that ensure superior penetration rates and exceptional durability, significantly extending bit life. We provide reliable solutions for efficient and cost-effective geothermal well construction.
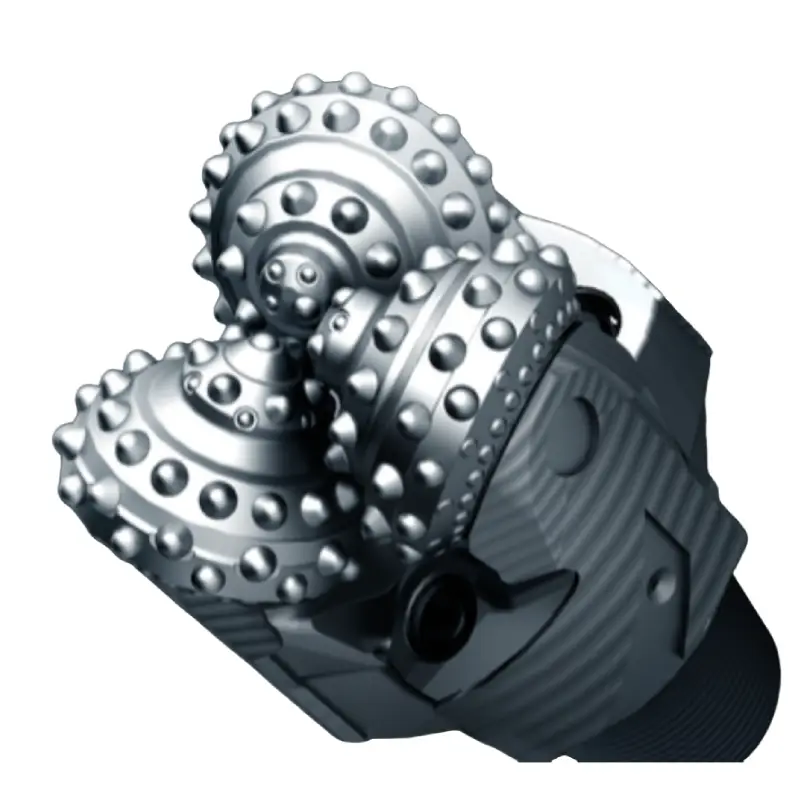
geothermal tricone drill bit
When it comes to tackling the challenging conditions of geothermal drilling, we offer a robust selection of tricone drill bits. Designed with specialized features to withstand extreme temperatures, high pressures, and abrasive rock formations, our tricone bits deliver exceptional performance. With options for both milled tooth (for softer formations) and tungsten carbide insert (TCI) designs (for harder rock), we ensure optimal penetration rates and extended bit life for your geothermal projects. We provide reliable and durable drilling solutions.
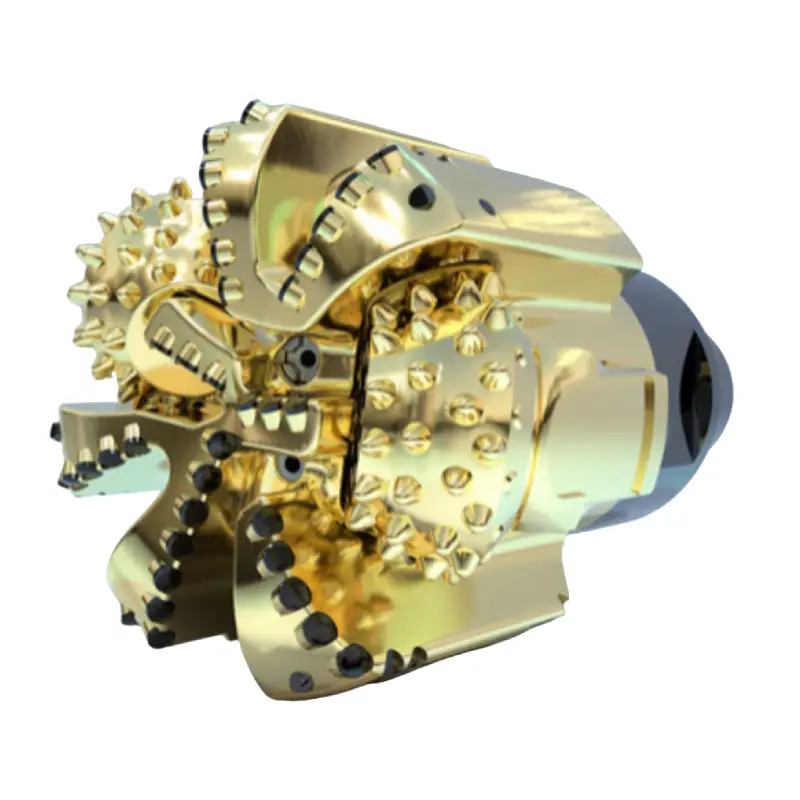
geothermal hybrid drill bit
We offer advanced geothermal hybrid drill bits, combining the best features of PDC and roller cone technologies. These innovative bits are designed for superior performance in the diverse and challenging formations encountered in geothermal drilling, including hard, abrasive rock and interbedded layers. Our hybrid bits deliver higher penetration rates, enhanced durability, and improved wellbore stability, significantly reducing drilling time and costs for your geothermal projects.
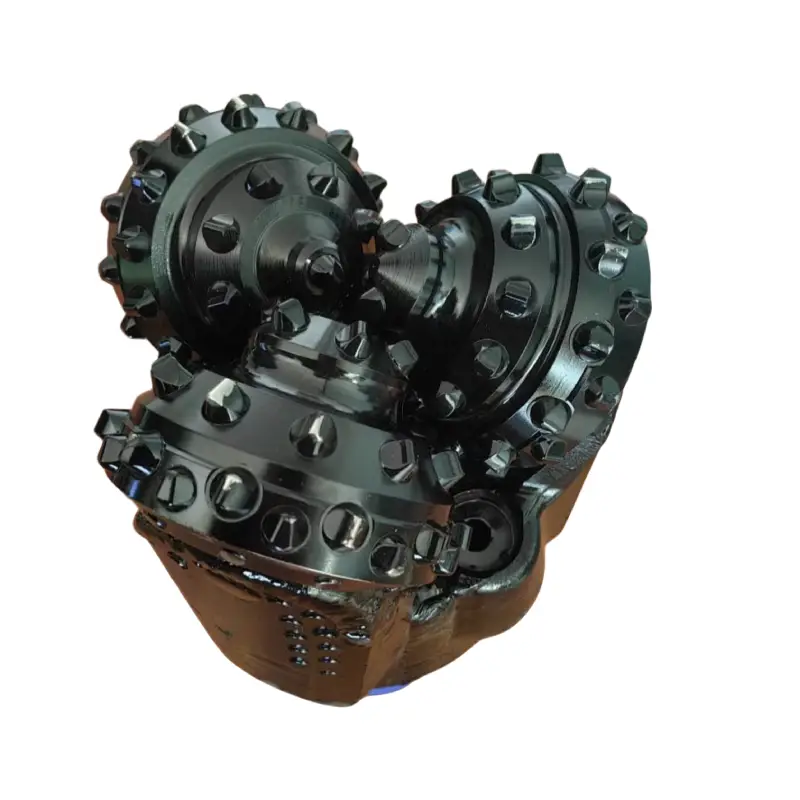
geothermal drilling tricone drill bit
We offer a range of geothermal tricone drill bits, engineered for exceptional performance in the demanding conditions of geothermal well drilling. Featuring robust designs with either durable milled steel teeth for softer formations or tough tungsten carbide inserts (TCI) for hard and abrasive rock, our tricone bits ensure efficient penetration rates and extended operational life. Special high-temperature seals and bearings are incorporated to withstand extreme downhole temperatures, minimizing costly bit trips and maximizing your drilling efficiency.
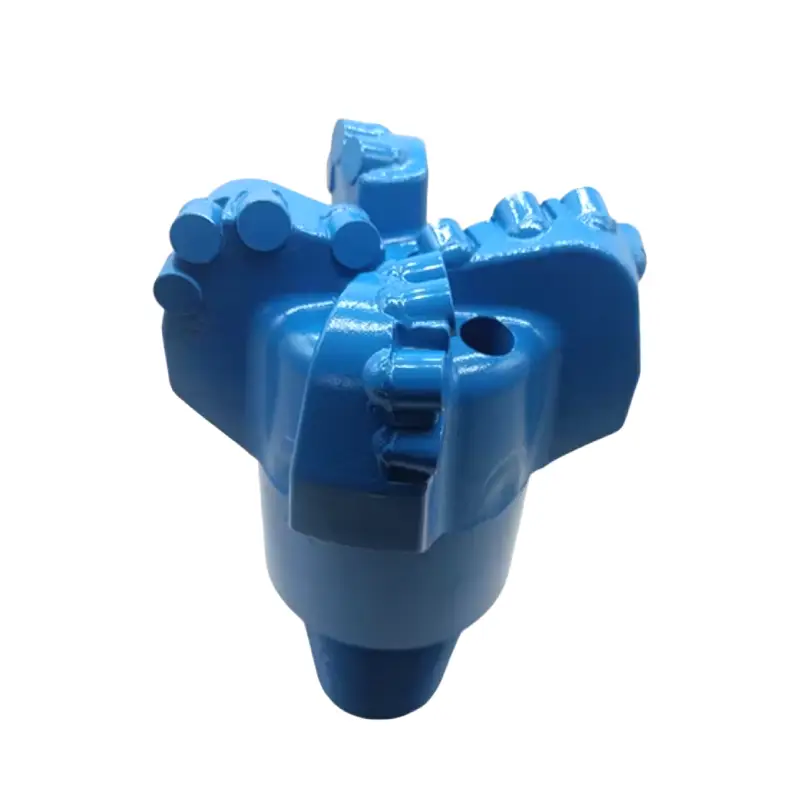
geothermal hole pCD diamond speed drilling bits
We offer high-performance geothermal hole PCD (Polycrystalline Diamond Compact) diamond speed drilling bits. Engineered for the extreme temperatures and abrasive rock formations in geothermal wells, these bits feature synthetic diamond cutters that provide exceptional wear resistance and aggressive cutting action. Our PCD bits deliver superior penetration rates and extended tool life, minimizing drilling time and maximizing efficiency for your complex geothermal projects.
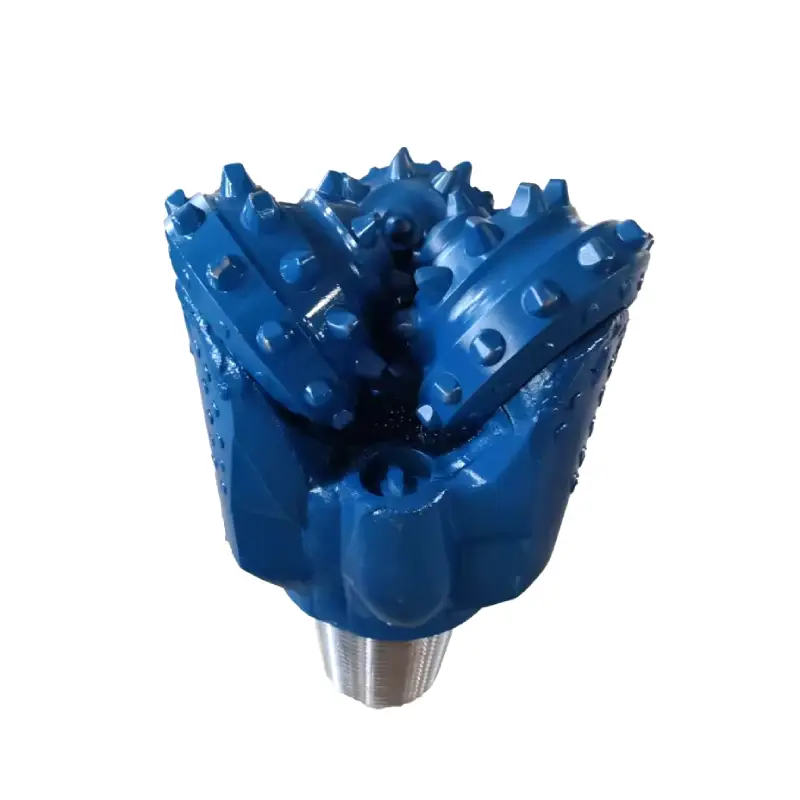
geothermal drill bit for mining operation
We offer specialized geothermal drill bits for mining operations, designed to excel in the harsh conditions often found when accessing deep mineral resources or for related geological studies. These bits feature high-temperature resistant materials and robust cutting structures like PDC cutters or tungsten carbide inserts, ensuring exceptional durability and high penetration rates through hard, abrasive formations. Our bits reduce downtime and optimize efficiency in your demanding mining projects.
Customize Your Desired Geothermal Drill Bits
Tailored Bit Design and Type
We can customize the overall bit design and type to perfectly match your specific drilling application and geological conditions. Whether you need a robust tricone for diverse formations, a high-penetration PDC for softer rocks, or a diamond-impregnated bit for extreme hardness, we tailor the bit’s architecture, including cone count, cutter layout, and junk slot area, for optimal performance.
Specialized Cutter Materials and Geometry
For superior performance in harsh geothermal environments, we offer customization of cutter materials and their geometry. This includes selecting the most suitable PDC cutter grades, specific diamond types for impregnated bits, or optimal tungsten carbide insert (TCI) designs for tricone bits. We fine-tune cutter size, shape, and placement to maximize wear resistance and cutting efficiency against abrasive and hot formations.
Optimized Hydraulics and Nozzle Configuration
Effective hydraulics are crucial for cooling and cleaning the bit. We customize the nozzle configuration and flow paths within the drill bit to ensure optimal fluid distribution. This allows for efficient cuttings removal, prevents bit balling in sticky formations, and provides critical cooling to the cutting structures, significantly extending bit life in high-temperature geothermal wells.
High-Temperature and Corrosion-Resistant Materials
Given the extreme downhole conditions, we utilize specialized materials for the bit body and seals that are inherently resistant to high temperatures and corrosive geothermal fluids. This extends beyond just the cutters to include robust bearing systems and seals in tricone bits, ensuring structural integrity and reliable operation even when exposed to superheated water, steam, and aggressive chemicals.
what are Geothermal Drill Bits?
Geothermal drill bits are highly specialized tools designed to cut through the Earth’s crust to access geothermal energy.
Unlike conventional drilling, geothermal environments present unique challenges such as extremely high temperatures (often exceeding 200°C), abrasive and hard rock formations (like granite, basalt, and fractured volcanic rock), and sometimes corrosive fluids.
Therefore, these bits are constructed from advanced, heat-resistant materials and employ specific designs, such as Polycrystalline Diamond Compact (PDC) cutters, tungsten carbide inserts (TCI) in tricone bits, or diamond-impregnated matrices, to ensure durability, high penetration rates, and reliable performance in these severe downhole conditions.
what are Geothermal Drill Bits used for?
Geothermal drill bits are specifically designed and utilized for creating boreholes in the Earth’s crust to access and harness its natural heat. This involves drilling through extremely challenging geological formations, which often include very hard, abrasive igneous and metamorphic rocks (like granite, basalt, and fractured volcanic rock), as well as encountering high temperatures and sometimes corrosive fluids deep underground.
Their primary purpose is to efficiently penetrate these severe conditions, ensuring the successful development of geothermal energy projects for power generation or heating/cooling applications.
Their main uses include:
Creating Production and Injection Wells: Drilling the boreholes necessary to extract hot geothermal fluids (production wells) and re-inject cooler fluids (injection wells) back into the reservoir to maintain pressure and sustainability for electricity generation.
Ground-Source Heat Pump Installations: Drilling shallower wells for the installation of closed-loop pipe systems that exchange heat with the stable temperatures of the shallow subsurface for residential and commercial heating and cooling.
Geothermal Exploration: Drilling pilot holes or exploration wells to identify and characterize potential geothermal reservoirs before full-scale development.
Enhanced Geothermal Systems (EGS) Development: Crucial for drilling into hot, dry rock formations and creating artificial fracture networks to allow water circulation for heat extraction.
Navigating Difficult Formations: Designed to withstand and efficiently drill through highly abrasive, fractured, or extremely hard rock, which would quickly destroy conventional drill bits.
How to drill for geothermal?
Drilling for geothermal energy is a complex undertaking, involving several distinct steps to efficiently access the Earth’s heat. It demands specialized equipment and expertise to ensure a productive and safe well.
Step 1: Site Evaluation and Planning
The process begins with extensive geological and geophysical surveys to identify optimal locations with accessible geothermal resources. This involves analyzing rock formations, temperature gradients, and potential fracture zones. Detailed planning then determines well depth, diameter, and the most effective drilling strategy.
This initial phase is crucial for de-risking the project and designing a well that can efficiently extract thermal energy. It also guides the selection of the appropriate drilling rig, drill bits, and associated drilling fluids, all tailored to the anticipated subsurface conditions.
Step 2: Conductor and Surface Casing
Once the site is prepared and the drilling rig is set up, a large-diameter, shallow hole is drilled to install the conductor casing. This first casing segment stabilizes the loose topsoil layers and prevents collapse, providing a sturdy guide for subsequent drilling operations.
Following the conductor, a deeper, smaller-diameter surface casing is run and cemented. This critical step seals off shallow groundwater aquifers, preventing contamination and providing a stable foundation for the deeper sections of the well, ensuring environmental protection and wellbore integrity.
Step 3: Intermediate and Production Drilling
After the surface casing is securely cemented, drilling continues to greater depths through various rock formations. Intermediate casing strings are installed and cemented in stages to stabilize the wellbore, isolate different geological zones, and manage downhole pressures, progressively narrowing the hole diameter.
Finally, production drilling reaches the hot geothermal reservoir. This phase often involves drilling through extremely hard and hot rock. Production casing is then run and cemented, creating the main conduit through which hot geothermal fluids or steam will flow to the surface.
Step 4: Well Completion and Testing
Upon reaching the target geothermal reservoir, the well is completed. This involves installing specialized equipment, such as perforated liners or screens, within the production zone to maximize fluid inflow. The well is then prepared for connection to the surface energy conversion systems.
The final step is rigorous testing of the completed well. Engineers measure critical parameters like temperature, pressure, and flow rates to assess the reservoir’s productivity and sustainability. These tests are vital for confirming the well’s viability and optimizing its long-term performance for geothermal energy generation.
What is one drawback of drilling geothermal wells?
One significant drawback of drilling geothermal wells is the exceptionally high initial capital cost. Unlike many other energy projects, a substantial portion of the overall investment in a geothermal power plant, often ranging from 35% to 75% of the total capital cost, is directly attributable to the drilling of wells.
This includes the cost of specialized drilling rigs, high-performance drill bits capable of withstanding extreme temperatures and abrasive rock, complex casing programs, and highly skilled labor.
These high upfront expenses can act as a major barrier to entry for new projects and deter potential investors, especially in regions with limited financial resources. Furthermore, there’s always an inherent exploration risk; extensive geological surveys and exploratory drilling are required, and there’s no guarantee that a commercially viable geothermal resource will be found, adding to the financial uncertainty and making the initial investment even more daunting.
Send Your Inquiry Now
All-in-one Geothermal Drill Bits Solutions for Your Project
Tired of premature bit failure and slow progress in your geothermal projects? The extreme heat and abrasive rock found in geothermal drilling demand more than standard bits, leading to costly downtime and inefficient operations. We provide the ultimate solution. We offer all-in-one geothermal drill bit solutions, meticulously engineered for superior durability, high penetration rates, and optimal performance, ensuring your project succeeds with maximum efficiency.