Custom Fixed Cutter Drill Bit Manufacturer in China
We proudly offer a wide range of high-performance fixed cutter drill bits, engineered for superior efficiency and durability. Our selection includes advanced PDC bits designed to maximize penetration rates and extend bit life across various challenging formations. Trust our fixed cutter solutions to deliver exceptional drilling performance, ensuring your operations are both productive and cost-effective.
Sinodrills - Your Trusted Fixed Cutter Drill Bit Manufacturer from China
Sinodrills stands as your trusted fixed cutter drill bit manufacturer from China, specializing in high-quality PDC and other fixed cutter solutions. With advanced manufacturing capabilities, we deliver robust, high-performance drill bits designed for superior efficiency and extended durability in diverse drilling environments. Partner with Sinodrills for reliable, wholesale drilling tools that drive your projects forward.
Various Fixed Cutter Drill Bit
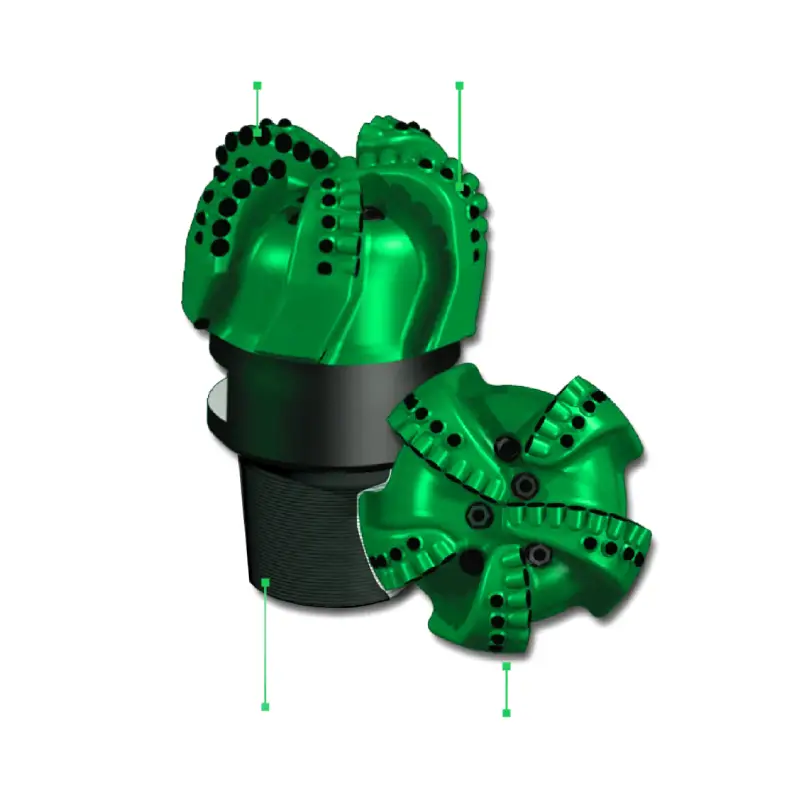
fixed cutter PDC drill bits
We offer a comprehensive selection of high-performance fixed cutter PDC drill bits, engineered to maximize drilling efficiency and longevity. Our bits feature advanced designs and premium polycrystalline diamond compact cutters, ensuring superior penetration rates and durability across diverse geological formations. Trust our fixed cutter PDC solutions for reliable, cost-effective drilling performance in your operations.
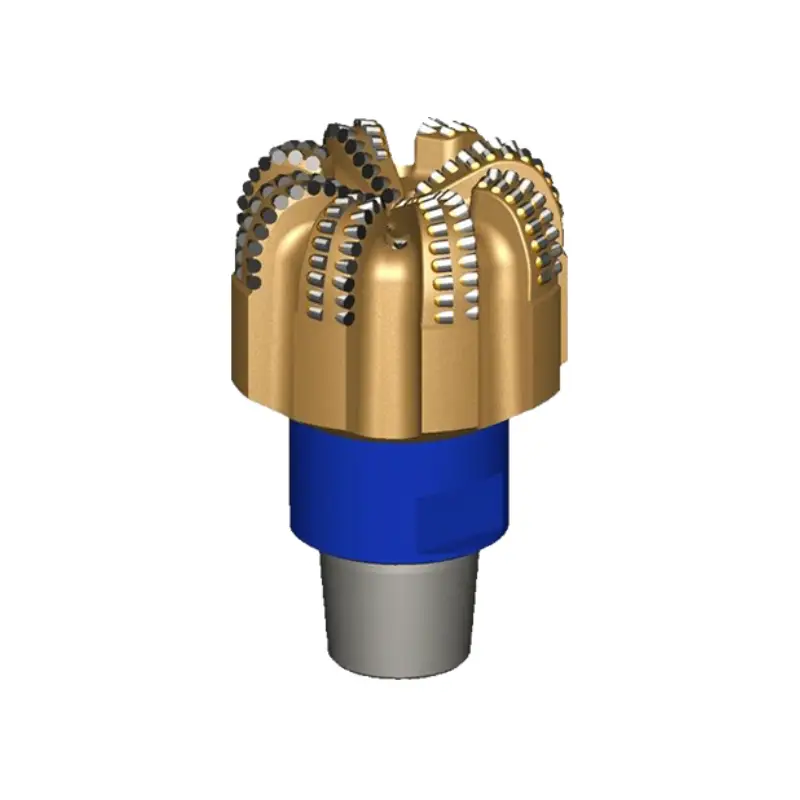
Impregnated Fixed Cutter Drill Bit
Our impregnated fixed cutter drill bits are engineered for drilling the hardest, most abrasive formations. These bits contain synthetic diamonds evenly distributed throughout the matrix material, which wears away to expose new diamond cutting points. This continuous self-sharpening action ensures consistent performance and extended bit life in extremely challenging geological conditions.
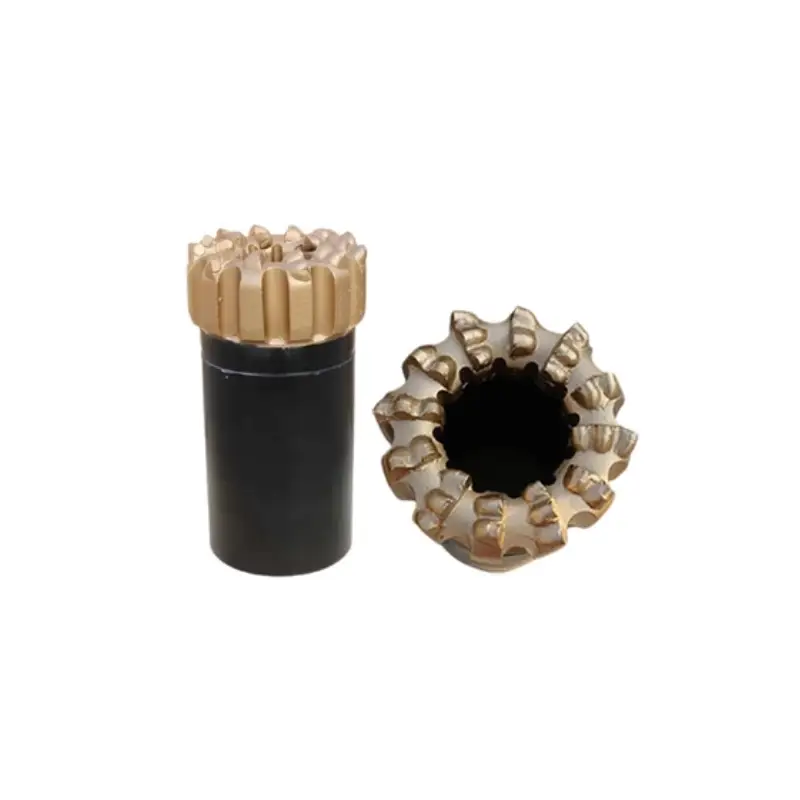
Core Fixed Cutter Drill Bit
We provide specialized core fixed cutter drill bits, designed to retrieve intact geological samples. These bits feature an annular cutting face, allowing for the collection of a core while drilling. Available in various designs, including PDC and impregnated options, they are crucial for geological evaluation, reservoir characterization, and geotechnical investigations in mining and exploration.
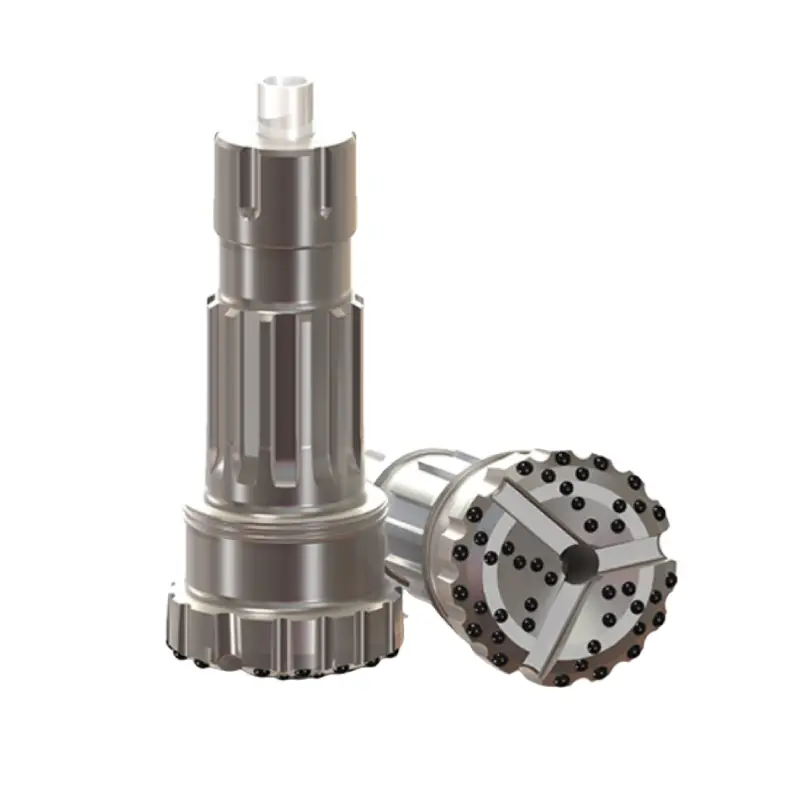
Concave Fixed Cutter Drill Bit
Our concave fixed cutter drill bits offer enhanced stability and directional control during drilling. The concave profile helps to centralize the bit, reducing deviation and improving borehole quality. Frequently employing PDC cutters, these bits are particularly effective in directional drilling applications where precise wellbore placement is critical for reaching target zones efficiently.
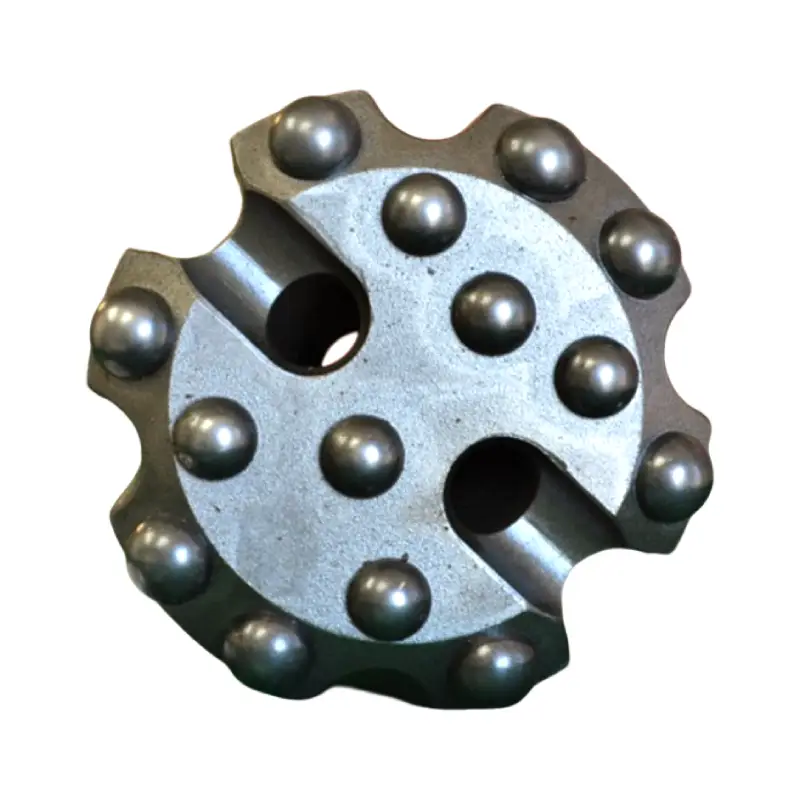
Flat-Face Fixed Cutter Drill Bit
We supply flat-face fixed cutter drill bits, optimized for maximum ROP in less consolidated formations. Their aggressive cutting structure and large junk slots facilitate efficient cuttings removal, preventing regrinding and optimizing drilling performance. These flat faced drilling bits are commonly used in top-hole sections and for fast drilling in softer, less abrasive lithologies.
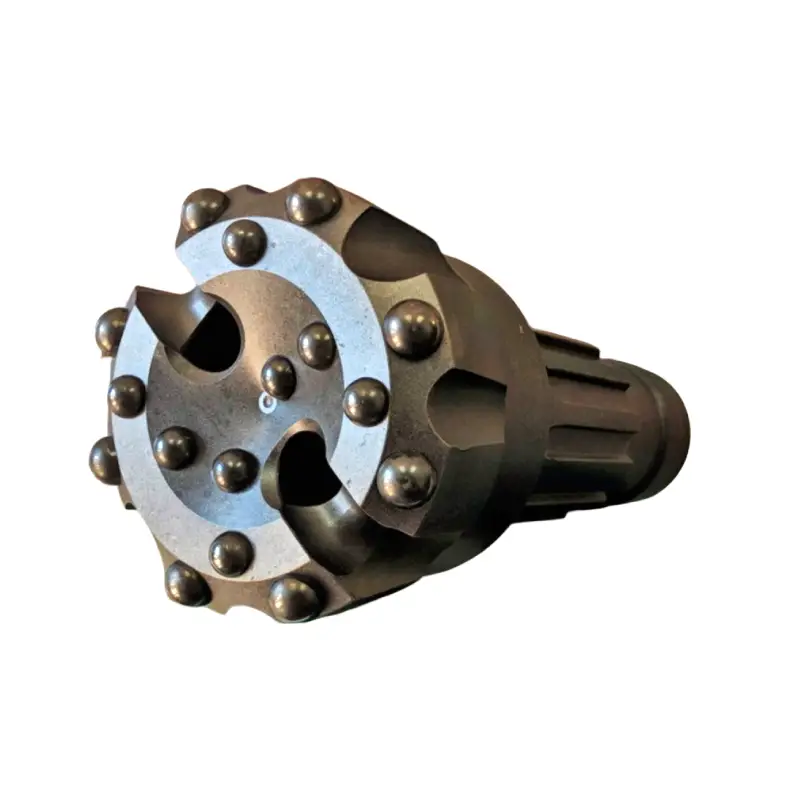
Domed Fixed Cutter Drill Bit
Our domed fixed cutter drill bits are designed for improved durability and impact resistance in interbedded formations. The domed profile provides a stronger structure, protecting cutters from damage when encountering harder stringers. Often featuring PDC cutters, they offer a balance of aggressive drilling and enhanced robustness in variable rock conditions.
Blade-Type Fixed Cutter Drill Bit
We offer versatile blade-type fixed cutter drill bits, characterized by their distinct cutting blades that extend from the bit body. These bits provide excellent cleaning and are effective in a wide range of formations, from soft shales to moderately hard sandstones. Their open design facilitates efficient fluid flow and cuttings evacuation.
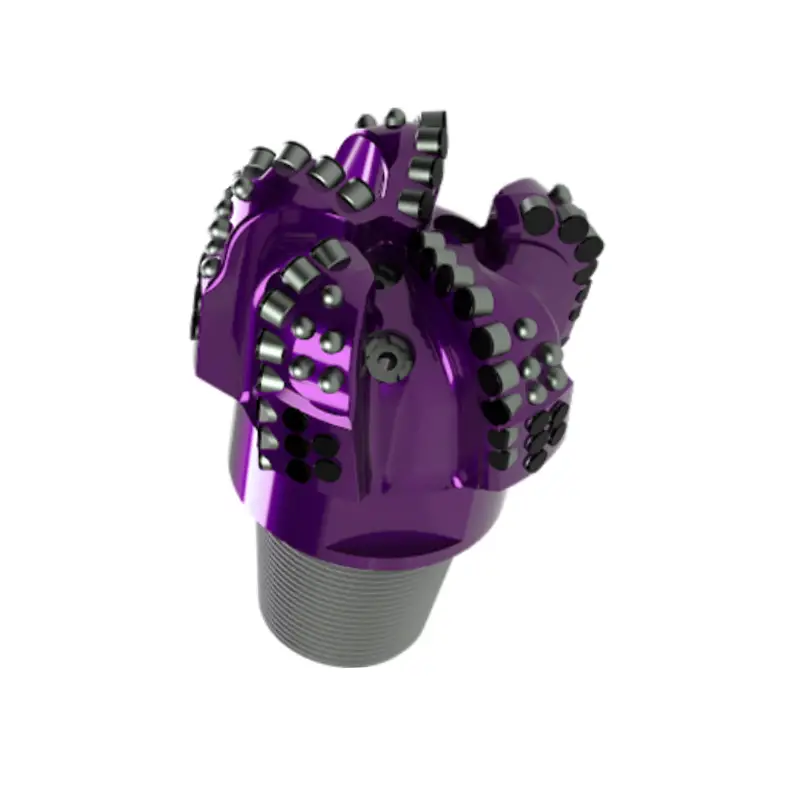
Steerable Fixed Cutter Drill Bit
Our steerable fixed cutter drill bits are engineered for integration with steerable drilling systems, enabling precise directional control. These bits often feature asymmetrical cutter layouts or specific gage pad designs to facilitate controlled steering. They are essential for complex well trajectories, horizontal drilling, and maximizing reservoir exposure.
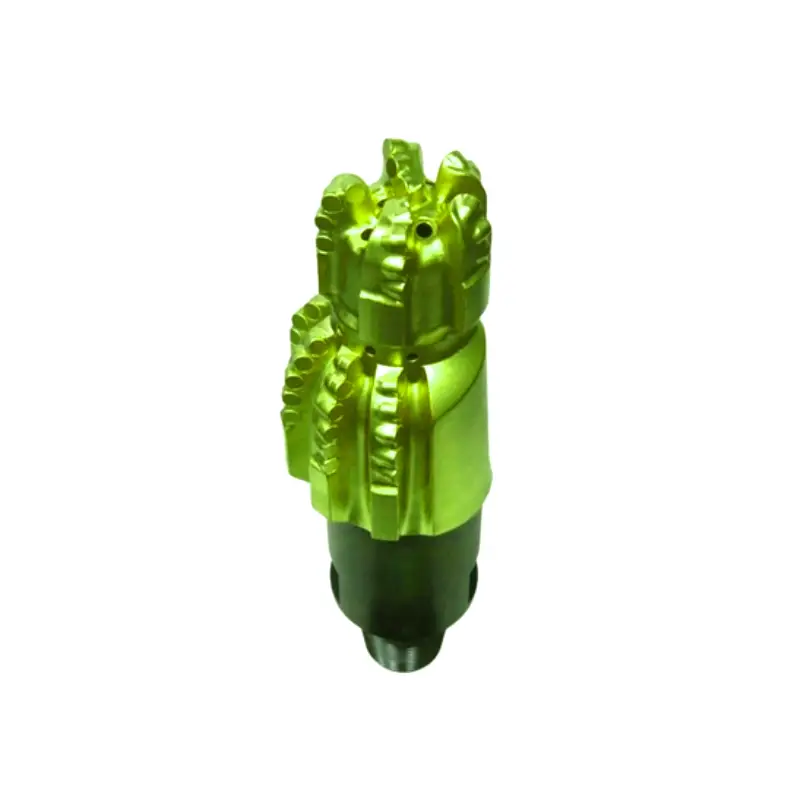
Bi-Center Fixed Cutter Drill Bit
We supply innovative bi-center fixed cutter drill bits, designed to drill an oversized hole while tripping through a smaller restriction. This unique design saves significant rig time by eliminating the need for reaming. Primarily used in wellbore enlargement applications, they allow for larger casing to be run in a single pass.
Customize Your Desired Fixed Cutter Drill Bit
Cutter Selection and Placement
We meticulously choose the type, size, and grade of PDC cutters, from standard to premium diamond elements, to match formation hardness and abrasiveness. Their strategic placement and back-rake angles are optimized to maximize cutting efficiency, improve steerability, and ensure superior rate of penetration (ROP) and durability in specific drilling environments.
Bit Body Profile and Blade Count
We design the bit body profile—concave, flat, or parabolic—and determine the optimal number of blades to enhance stability, cleaning, and directional control. This customization ensures efficient cuttings evacuation, minimizes bit balling, and provides the necessary strength and wear resistance for the intended application, from soft to hard rock.
Hydraulics and Nozzle Configuration
We engineer the bit’s hydraulics, including the number, size, and orientation of nozzles, to optimize fluid flow and cuttings removal. This ensures efficient cooling of the cutters, prevents regrinding of cuttings, and maximizes bottom-hole cleaning. Proper hydraulic design is crucial for achieving peak drilling performance and extending bit life.
Gage Design and Wear Protection
We customize the gage design, including the length and type of gage pads, to maintain borehole quality and stability. Enhanced wear protection, often through the application of hardfacing materials or specialized inserts, is incorporated to prevent premature wear of the bit’s diameter, ensuring the wellbore remains in gauge for subsequent operations.
what is a fixed cutter drill bit?
A fixed cutter drill bit is a type of drilling tool characterized by having no moving parts.
Unlike roller cone bits, its cutting elements, typically made of super-hard materials like polycrystalline diamond compact (PDC) or impregnated diamonds, are permanently brazed or integrated onto the bit body. This design allows the bit to shear, scrape, or grind rock as it rotates, offering high rates of penetration and durability, particularly in challenging formations. They are widely used in the oil and gas industry for efficient and precise wellbore construction.
fixed cutter drill bit features
Fixed cutter drill bits are engineered with several key features that contribute to their high performance and efficiency in drilling operations.
These drill bits with fixed cutter features are meticulously designed and integrated to optimize rock removal, enhance durability, and improve overall drilling economics.
Key features include:
Polycrystalline Diamond Compact (PDC) Cutters: These synthetic diamond cutters are the primary cutting elements, known for their extreme hardness and wear resistance, enabling efficient shearing of rock.
Bit Body Material: Typically made of steel or a tungsten carbide matrix, the body provides structural integrity and dictates the bit’s resistance to erosion and impact.
Blade Design: The number, height, and geometry of the blades influence bit stability, cuttings evacuation, and directional control.
Hydraulic System: Optimized nozzle placement and flow paths ensure efficient cooling of cutters and effective removal of rock cuttings from the bottom of the hole.
Gage Protection: Reinforced areas on the bit’s outer diameter maintain borehole integrity and prevent premature wear, ensuring the hole remains in gauge.
fixed cutter drill bit benefits
Fixed cutter drill bits offer numerous benefits that make them a preferred choice for various drilling applications, particularly in the oil and gas industry. Their inherent design and advanced materials translate into significant operational advantages, contributing to more efficient and cost-effective drilling campaigns.
Key benefits include:
High Rate of Penetration (ROP): Their aggressive shearing action and durable cutters allow for faster drilling speeds, significantly reducing drilling time.
Extended Bit Life: The robust construction and wear-resistant materials, especially PDC cutters, lead to longer downhole time, minimizing the need for frequent bit trips.
Improved Wellbore Quality: The stable design and consistent cutting action contribute to a smoother and more in-gauge borehole, which can simplify subsequent casing and completion operations.
Reduced Drilling Costs: Faster drilling and fewer bit changes translate directly into lower rig time expenses and overall project costs.
Versatility: With various designs and customizable features, fixed cutter bits can be optimized for a wide range of formations, from soft to extremely hard and abrasive.
fixed cutter drill bit vs roller cone drill bits
Fixed cutter and roller cone drill bits represent the two primary categories of drilling tools, each employing distinct mechanisms to break rock.
Understanding their differences is crucial for selecting the optimal bit for specific geological conditions and drilling objectives.
Cutting Mechanism
Fixed cutter drill bits, predominantly PDC bits, operate by shearing and scraping the rock. Their polycrystalline diamond compact cutters are fixed to the bit body and continuously engage the formation, removing rock through a continuous cutting motion. In contrast, roller cone drill bits feature three independently rotating cones equipped with steel teeth or tungsten carbide inserts. These cones roll across the bottom of the hole, crushing, gouging, and chipping the rock as they rotate.
Moving Parts
A significant distinction lies in their construction. Fixed cutter bits have no moving parts; their cutting elements are stationary relative to the bit body. This simplicity reduces mechanical failure points. Conversely, roller cone bits rely on the rotation of their cones, which are mounted on bearings. These moving parts, while enabling their crushing action, also introduce potential wear points, particularly in the bearings.
Formation Suitability
Fixed cutter bits excel in soft to medium-hard formations, especially shales, sandstones, and carbonates, where their shearing action is highly effective. They are also increasingly used in harder formations with advanced cutter technology. Roller cone bits, with their crushing and chipping action, are generally more versatile and perform well across a broader range of formations, from very soft to extremely hard and abrasive rocks, including those with interbedded layers.
Rate of Penetration (ROP)
In suitable formations, fixed cutter bits typically achieve higher rates of penetration (ROP) due to their continuous shearing action and efficient cuttings removal. This often leads to faster drilling times. While roller cone bits can also achieve good ROP, especially in harder formations, their crushing mechanism might be slower in formations where shearing is more effective.
Durability and Lifespa
Fixed cutter bits, particularly PDC bits, are known for their exceptional durability and longer lifespan in appropriate formations, often completing entire sections without needing to be pulled out. The absence of moving parts contributes to their robustness. Roller cone bits, while robust, have bearings and seals that are susceptible to wear, which can limit their lifespan, especially in high-temperature or high-impact drilling environments.
how to choose the best fixed cutter drill bit?
Choosing the best fixed cutter drill bit requires a thorough understanding of the drilling environment and performance objectives. The ideal bit is a balance of design features tailored to the specific rock properties, desired drilling speed, and overall cost efficiency.
Here’s how to choose the best fixed cutter drill bit:
Formation Characteristics
Understanding the geological formation is paramount. This includes assessing the rock’s hardness, abrasiveness, and homogeneity. Softer formations might benefit from bits with more aggressive cutter layouts and higher blade counts for maximum rate of penetration (ROP), while harder, more abrasive formations demand bits with more durable cutters and robust body materials to withstand wear and impact.
Drilling Parameters
Consider the available drilling parameters, such as weight on bit (WOB), rotary speed (RPM), and hydraulic capacity. The bit design should be compatible with these parameters to ensure optimal performance and prevent premature wear or damage.
For instance, higher RPMs might require bits with improved thermal management for the cutters.
Performance Goals
Define your primary performance goals for the drilling interval. Are you prioritizing maximum ROP to reduce drilling time, extended bit life to minimize trips, or superior directional control for complex well paths?
The drill bit’s profile, cutter density, and gage design can be customized to emphasize one or more of these objectives.
Bit Design and Features
Evaluate specific bit design elements. This includes the type and placement of PDC cutters (e.g., standard, shaped, or thermally stable), the bit body material (steel or matrix), the number and geometry of blades, and the hydraulic configuration (nozzle size and placement). Each element plays a role in the bit’s interaction with the formation.
Cost-Benefit Analysis
While the initial cost of a fixed cutter drill bit can be higher than other types, it’s crucial to perform a comprehensive cost-benefit analysis. A more expensive, high-performance bit that significantly reduces drilling time and minimizes trips can lead to substantial overall cost savings, making it the more economical choice in the long run.
Send Your Inquiry Now
All-in-one Fixed Cutter Drill Bit Solutions for Your Project
We offer all-in-one Fixed Cutter Drill Bit Solutions, providing a comprehensive suite of services from initial design to on-site performance optimization. Our expertise in customizing cutter selection, body profiles, hydraulics, and gage protection ensures a perfectly tailored bit for your specific geological conditions. This integrated approach guarantees maximum drilling efficiency, reduced operational costs, and superior wellbore quality for your project.