In the complex world of drilling, every component plays a crucial role in operational success. Among the most vital are API drill pipe thread types, the unsung heroes ensuring seamless power transfer and fluid circulation downhole. Understanding these connections is not just technical knowledge; it’s a pathway to enhancing drilling efficiency, safety, and profitability.
This ultimate guide will meticulously break down the various API drill pipe thread types, from Regular to Numbered Connections. We’ll explore their unique characteristics, ideal applications, and the critical impact they have on your drilling operations, helping you make informed decisions for superior performance.
What is API Drill Pipe Thread?
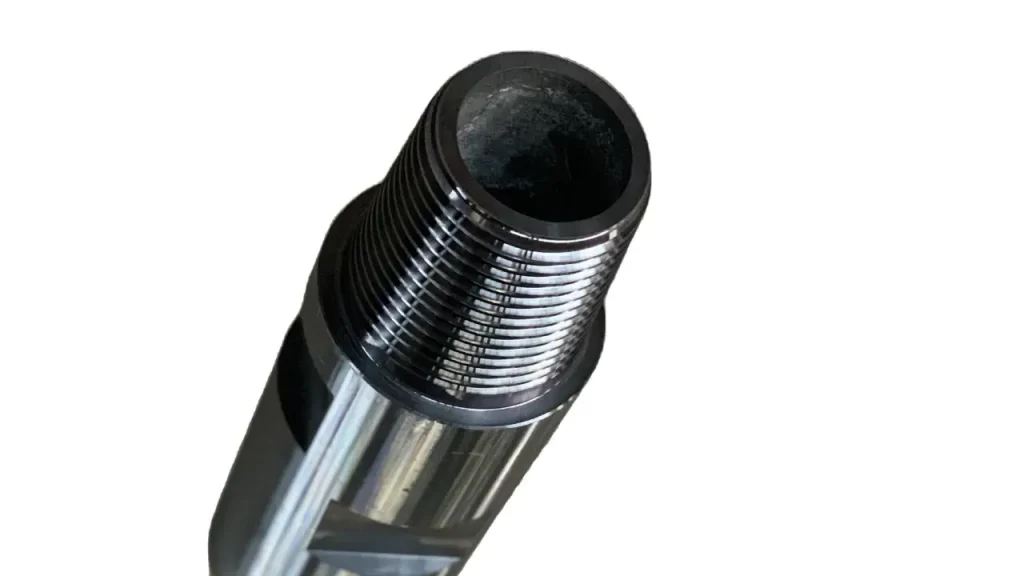
API Drill Pipe Thread refers to the standardized thread connections on drill pipes that meet the specifications of the American Petroleum Institute (API), particularly API Spec 5DP.
These API threads ensure compatibility, strength, and reliable sealing for drill strings used in demanding oil and gas drilling operations.
What is Drill Pipe Thread?
Drill pipe thread refers to the specialized mechanical connection machined onto the ends of drill pipe sections, enabling them to be joined together to form a continuous drill string. These threads are precisely engineered with specific profiles, tapers, and dimensions to ensure a secure, high-strength connection capable of transmitting rotational torque, downward force, and often drilling fluid pressure.
The male end, known as the “pin,” has external threads, while the female end, or “box,” has corresponding internal threads. The design of these threads is critical for maintaining drill string integrity under extreme stresses encountered during drilling operations, preventing costly failures and ensuring efficient well construction.
API Drill Pipe Thread Types
The American Petroleum Institute (API) has established a series of standardized thread types for drill pipe, crucial for ensuring compatibility, strength, and reliable connections within the drill string. These thread types are meticulously designed to handle the immense stresses and operational demands encountered during drilling for oil and gas. Understanding each type is key to optimizing drilling performance and preventing costly failures.
Here are the main API Drill Pipe Thread Types:
Regular (REG) Thread
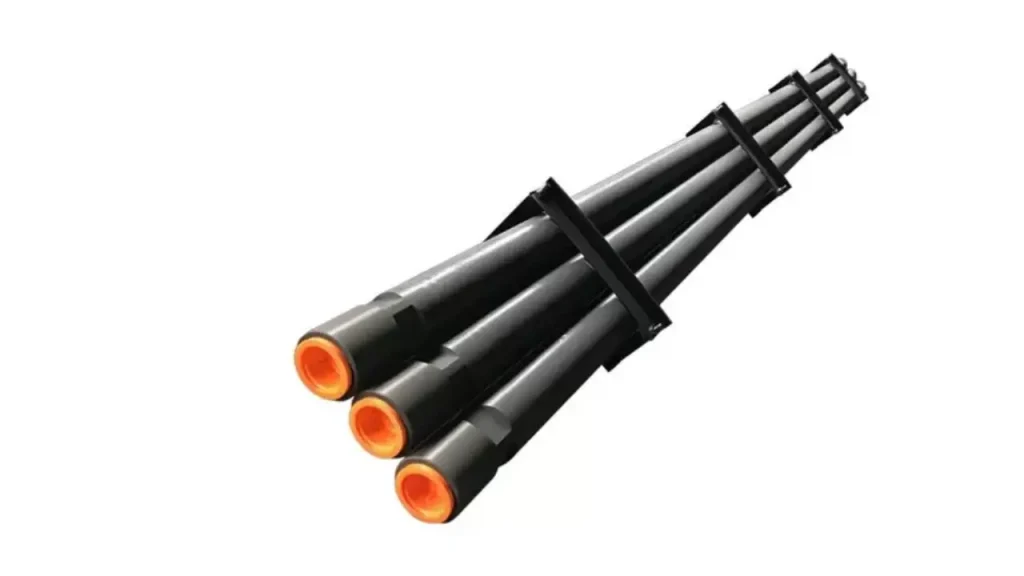
The API Regular (REG) thread is a classic, robust connection designed for general-purpose drilling applications. It features a deep thread profile and a tapered design, providing a strong mechanical interlock between the pin and box ends of the drill pipe. This design ensures efficient transmission of torque and axial loads down the drill string.
While widely used, particularly for connecting to drill bits and bottom hole assembly components, REG threads have a smaller bore compared to some other API connections. This can lead to slightly higher pressure losses when circulating drilling fluids, though their reliability and ease of use make them a common choice in many standard drilling scenarios.
Internal Flush (IF) Thread
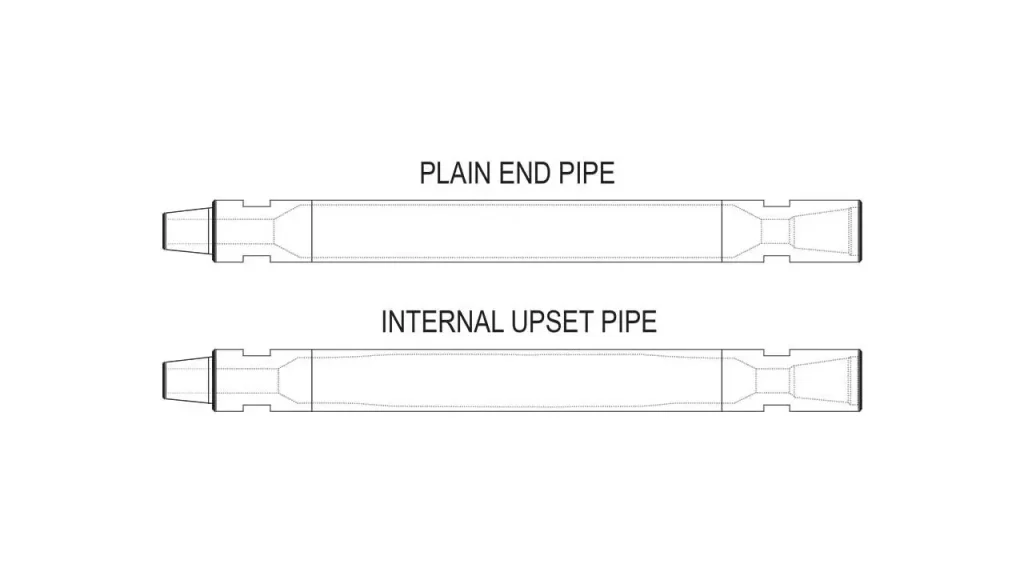
The API Internal Flush (IF) thread is engineered with a primary focus on optimizing hydraulic efficiency. Its design aims to create a smooth, continuous internal bore across the connection, minimizing turbulence and pressure drops as drilling fluid flows through the drill string. This “flush” internal diameter is achieved by thickening the pipe ends (upsetting) to accommodate the threads without constricting the fluid path.
This improved fluid flow is particularly beneficial in operations requiring high circulation rates or when drilling through formations that produce significant cuttings, as it enhances the ability to clean the wellbore and cool the drill bit effectively. While offering excellent hydraulic performance, the larger external diameter of the tool joint can sometimes lead to increased wear in abrasive formations.
Full Hole (FH) Thread
The API Full Hole (FH) thread is another connection type designed for maximum internal fluid passage, similar to the IF thread but often with an even larger internal diameter. This design ensures minimal restriction to the flow of drilling fluid, which is critical for maintaining optimal hydraulic performance, especially in large-diameter drilling or applications where high pump rates are essential.
FH connections are particularly advantageous in situations where maximizing fluid returns and minimizing pressure losses are paramount. They are commonly found on larger diameter drill pipes and are selected when the priority is to achieve the highest possible flow efficiency through the drill string, contributing to faster penetration rates and more effective wellbore cleaning.
Numbered Connection (NC)
The API Numbered Connection (NC) series was introduced to standardize and replace many older API thread designs, including some IF and FH connections. The “NC” designation is followed by a number that indicates the approximate pitch diameter of the thread in inches and tenths of an inch, providing a clear and consistent naming convention.
NC connections are highly versatile and widely adopted across the industry due to their standardized dimensions and robust performance. They are designed to withstand high torsional and tensile stresses, making them suitable for a broad range of drilling depths and challenging geological conditions. Their interchangeability simplifies inventory management and ensures compatibility across different drilling equipment.
Standard Rotary Shoulder Connection (SRSC)
The Standard Rotary Shoulder Connection (SRSC) is a broad category encompassing various tapered, rotary shouldered connections used throughout the drilling industry, including API threads like REG, IF, FH, and NC. These connections rely on a precisely machined shoulder that “makes up” (comes into firm contact) to provide a primary seal and transfer compressive loads. The threads primarily serve to pull the shoulders together and transmit torsional loads.
SRSC designs are fundamental to drill string integrity, allowing for quick and secure make-up and break-out while ensuring robust performance. Their reliability under high torque and tension makes them ubiquitous in conventional drilling applications, forming the backbone of most drill strings from the surface to the bottom-hole assembly.
Double Shoulder (DS) Connection
Double Shoulder (DS) connections are advanced proprietary or premium thread designs that offer enhanced performance compared to standard API connections by incorporating an additional, secondary shoulder. This second shoulder engages after the primary shoulder, providing an extra point of contact and load bearing. This innovative design significantly increases the connection’s torsional strength and resistance to jump-out.
The added shoulder in DS connections allows them to handle higher torque values and provides superior resistance to fatigue, making them ideal for challenging drilling environments such such as extended reach drilling, horizontal drilling, or operations in hard, abrasive formations where conventional connections might fail. Their enhanced robustness contributes to improved drilling efficiency and reduced non-productive time.
Here’s a table listing the types of API drill pipe threads in the following:
API Drill Pipe Thread Type | Key Characteristics | Advantages | Common Applications |
Regular (REG) Thread | Robust, tapered, deep thread profile; external and internal shoulder contact. | Strong mechanical interlock; reliable for general use; good torque transmission. | Standard drilling, connecting to drill bits/BHAs, general purpose. |
Internal Flush (IF) Thread | Streamlined, large internal diameter; external upset provides flush internal bore. | Excellent hydraulic efficiency; minimizes turbulence and pressure drop; enhances cuttings removal. | High circulation rate drilling, efficient wellbore cleaning, various drilling operations. |
Full Hole (FH) Thread | Largest internal diameter; external upset for maximum fluid passage. | Superior hydraulic performance; minimizes pressure losses; maximizes fluid flow. | Large diameter drilling, high pump rate operations, maximizing flow efficiency. |
Numbered Connection (NC) | Standardized series (e.g., NC26, NC31, NC38, NC46, NC50); replaces older API types. | High interchangeability; robust performance; standardized dimensions; good torsional and tensile strength. | Wide range of drilling depths and formations, versatile industry standard. |
Standard Rotary Shoulder Connection (SRSC) | Broad category including REG, IF, FH, NC; relies on shoulder make-up for primary seal/load transfer. | Quick make-up/break-out; reliable under high torque/tension; fundamental to drill string integrity. | Ubiquitous in conventional drilling for entire drill string. |
Double Shoulder (DS) Connection | Features a secondary, additional shoulder that engages after the primary. | Enhanced torsional strength; increased resistance to jump-out; superior fatigue resistance. | Extended reach drilling, horizontal wells, hard rock drilling, demanding environments. |
API Drill Pipe Thread Dimensions
API Drill Pipe Thread dimensions are highly standardized and rigorously defined by the American Petroleum Institute, primarily under API Spec 5DP and API Spec 7-2. These precise dimensions ensure interchangeability and consistent performance across various manufacturers and drilling operations worldwide.
The exact specifications include a multitude of parameters for each thread type, ensuring the robust and reliable connections essential for the demanding conditions of oil and gas drilling.
Key dimensions defined by API for drill pipe threads include:
- Outer Diameter (OD) and Inner Diameter (ID): The nominal pipe body dimensions, which then dictate the size of the tool joint and thread.
- Threads Per Inch (TPI) / Pitch: The number of threads within a given linear inch or the distance between corresponding points on adjacent threads.
- Taper Per Foot (TPF): The rate at which the diameter of the thread changes along its length. API threads typically have tapers of 1 1/4″, 1 1/2″, 2″, or 3″ per foot.
- Thread Form: The specific shape of the thread, including flank angle (e.g., 60°), root radius, crest truncation, and thread height.
- Pitch Diameter: The diameter of an imaginary cylinder that would pass through the threads at the point where the width of the thread and the width of the space between threads are equal.
- Pin Length and Box Length: The axial dimensions of the threaded portions on both the male (pin) and female (box) ends of the tool joint.
- Make-up Depth: The distance the pin enters the box when the connection is fully torqued.
- Upset Dimensions: The specific dimensions of the internal, external, or internal-external upsets on the pipe body near the tool joint, which reinforce the pipe to compensate for material removed during threading.
How to Choose the Suitable API Drill Pipe Thread Types?
Choosing the suitable API drill pipe thread type is a critical decision that directly impacts drilling efficiency, safety, and overall project cost. The selection process involves a careful assessment of various factors related to the specific drilling environment and operational requirements. A mismatch can lead to premature wear, connection failures, and costly downtime.
Here are the key factors to consider when choosing the suitable API drill pipe thread types:
- Well Depth and Design: Deeper wells and complex well designs (e.g., horizontal, extended reach) impose higher tensile and torsional stresses on the drill string, necessitating stronger connections like API NC or Double Shoulder threads.
- Drilling Fluid Properties and Circulation Rate: Operations requiring high flow rates for efficient cuttings removal or specific fluid properties (e.g., heavy muds) benefit from connections with larger internal bores, such as API Internal Flush (IF) or Full Hole (FH) threads, to minimize pressure losses.
- Formation Type and Abrasiveness: Drilling through hard, abrasive formations can accelerate thread wear. In such cases, robust connections with excellent wear resistance or those designed for superior fatigue life (e.g., some premium connections or hardbanded tool joints) are preferred.
- Drilling Rig Capacity and Torque Requirements: The maximum torque capacity of the rig and the expected torque required to drill through the formation will influence the thread strength needed. Connections like NC and Double Shoulder are designed for higher torque transmission.
- Compatibility with Existing Equipment: It’s crucial to ensure that the chosen thread type is compatible with existing drill collars, drill bits, and other bottom hole assembly components to avoid costly modifications or inventory issues.
- Cost vs. Performance: While premium or double shoulder connections offer superior performance in challenging conditions, they come at a higher cost. A cost-benefit analysis based on the project’s demands is essential.
Conclusion
Mastering API drill pipe thread types is undeniably crucial for any successful drilling operation. From the robust simplicity of REG to the optimized flow of IF and FH, and the standardized reliability of NC connections, each thread serves a vital purpose in ensuring downhole integrity and operational efficiency.
By understanding these distinctions, you’re empowered to select the optimal connections that minimize downtime, enhance safety, and maximize productivity for your specific projects. This knowledge directly translates into more efficient power transfer and fluid circulation, leading to superior drilling performance.
Ready to elevate your drilling projects? Get wholesale API drill rods and API drill pipes, manufactured to the highest standards, directly from Sinodrills. Contact us today for reliable, high-performance drilling solutions.