Bottom Hole Assembly (BHA) is a critical component in drilling operations, but its intricacies often go unnoticed by those outside the oil and gas industry. We’re here to change that. In this blog post, we’ll delve into the world of BHAs, examining their essential functions, diverse components, and the crucial role they play in successful drilling projects.
What is Bottom Hole Assembly?
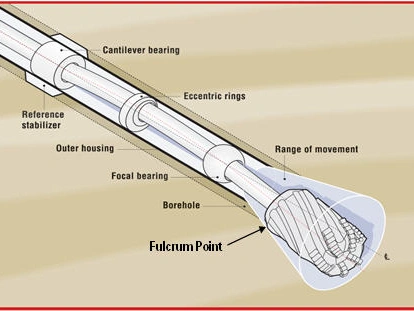
When we talk about drilling an oil or gas well, it’s easy to picture just a drill bit spinning at the bottom of a hole. However, what lies directly above that drill bit, the Bottom Hole Assembly (BHA), is a complex and highly engineered system that is critical to the success and safety of the entire drilling operation. Understanding the BHA is key to comprehending how we efficiently and accurately drill into the earth’s subsurface.
The Bottom Hole Assembly is essentially the lowermost part of the drill string, extending from the drill bit up to the drill pipe. It’s a carefully designed and assembled string of specialized tools and equipment, each serving a specific purpose. Think of it as the brain and muscle of our drilling operation at the bottom of the wellbore, where all the critical actions like cutting rock, steering the well, and collecting data take place. Its configuration varies significantly depending on the drilling objective and geological conditions.
What is the Function of the Bottom Hole Assembly?
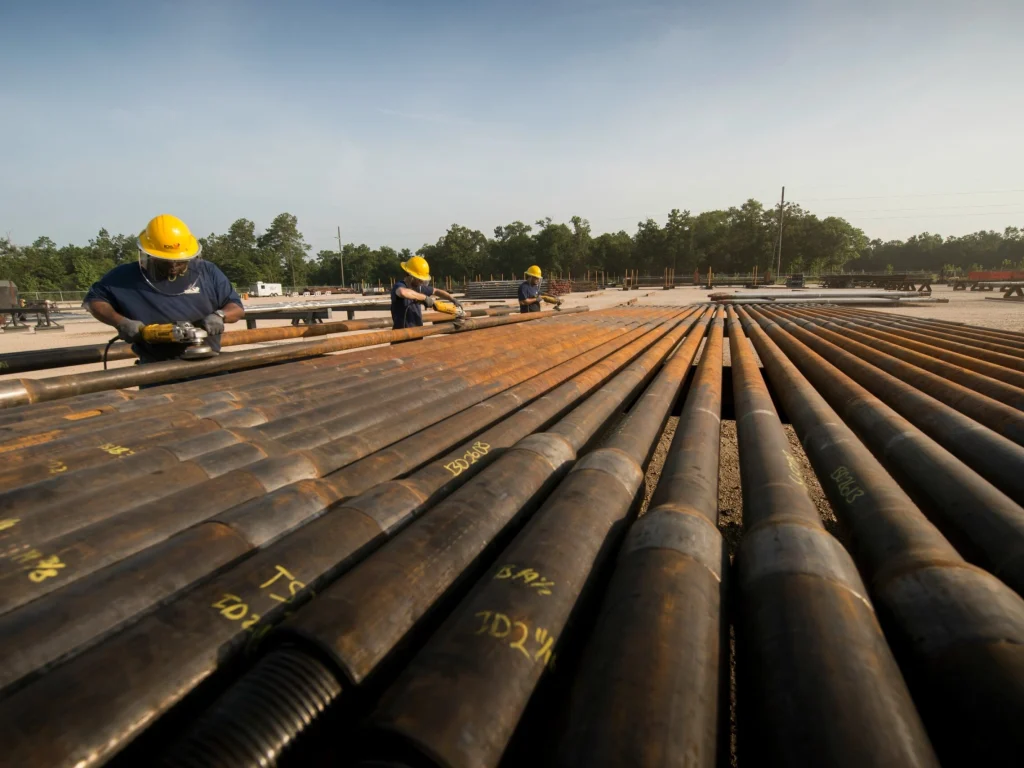
The bottom hole assembly is responsible for transferring the weight of the drill to the drill bit, controlling the direction and inclination of the wellbore, and providing real-time data on the drilling environment. Without a well-designed and fully functional bottom hole assembly, it is impossible to achieve drilling goals and reach the target formation accurately and efficiently. It is the power source for us to drill complex underground geology and extract valuable resources.
What Are the Components of BHA?
A Bottom Hole Assembly (BHA) is a modular system, meaning it’s made up of various interchangeable components that we select and arrange based on the specific demands of a drilling project. Each component plays a vital role in the overall functionality of the BHA, contributing to everything from drilling efficiency to wellbore stability and data acquisition. Let’s explore some of the most common and essential elements we include in our BHAs, often referred to as bottom hole assembly tools.
Drill Bit: The Cutting Edge
The drill bit is the very first component of the BHA, and arguably the most recognizable. It’s the part that directly interfaces with the rock formation, designed to cut and break through various types of rock. The choice of drill bit is crucial and depends heavily on the geology we expect to encounter.
We typically categorize drill bits into two main types:
- Roller Cone Bits: These bits have cones with rotating cutters that crush and shear the rock. They are versatile and widely used in a variety of formations, from soft to hard.
- Fixed Cutter Bits (PDC Bits): These bits feature fixed cutters made of polycrystalline diamond compact (PDC) material. They are known for their high drilling efficiency and durability, especially in softer to medium-hard formations.
Drill Collars: Adding Weight and Stiffness
Immediately above the drill bit, we typically place drill collars. These are thick-walled, heavy steel pipes that serve several critical functions. Their primary purpose is to provide the necessary weight on bit to enable the drill bit to effectively cut through rock.
Beyond just adding weight, drill collars also provide stiffness to the BHA. This stiffness helps to keep the drill bit running true, preventing deviation and ensuring a straight wellbore. Without adequate drill collar weight and stiffness, we would struggle to achieve optimal penetration rates and maintain a wellbore trajectory.
Stabilizers: Keeping Us On Track
Stabilizers are another essential component within the BHA, designed to centralize the drill string in the wellbore and prevent excessive wobbling or spiraling. They are crucial for maintaining directional control and ensuring the quality of the wellbore.
We use different bottom hole assembly types of stabilizers depending on the application:
- Sleeve Stabilizers: These have replaceable sleeves that can be changed out on site.
- Blade Stabilizers: These are integrated into the stabilizer body with fixed blades.
- Adjustable Stabilizers: These allow for adjustments to the diameter, offering greater flexibility.
By centralizing the BHA, stabilizers help us achieve a smoother drilling operation, reduce vibrations, and minimize wear and tear on the drill bit and other BHA components. You might also encounter specialized designs, like a bottom hole spring assembly, used in specific applications to manage weight or provide shock absorption.
Measurement While Drilling (MWD) and Logging While Drilling (LWD) Tools: Our Eyes and Ears Downhole
In modern drilling, Measurement While Drilling and Logging While Drilling tools are indispensable. These sophisticated instruments provide us with real-time data from the bottom of the wellbore, allowing us to make informed decisions and adjustments as we drill.
- MWD tools provide critical drilling parameters such as inclination, azimuth, toolface orientation, and temperature. This information is vital for steering the well and ensuring we are on the correct trajectory.
- LWD tools provide formation evaluation data, similar to wireline logging, but collected while drilling. This includes resistivity, gamma ray, neutron porosity, and density measurements, which help us identify hydrocarbon-bearing zones and understand the reservoir characteristics.
The ability to obtain this data in real time significantly reduces drilling risks, improves efficiency, and enhances our understanding of the subsurface.
Motors and Rotary Steerable Systems (RSS): Steering the Course
When we need to drill deviated or horizontal wells, we often incorporate either downhole motors or Rotary Steerable Systems (RSS) into our BHA. These tools allow us to precisely control the direction of the wellbore, which is crucial for bottom hole assembly for directional drilling.
- Downhole Motors (Mud Motors): These are positive-displacement motors powered by the drilling fluid. They rotate the drill bit independently of the drill string, allowing for directional changes without rotating the entire string from the surface. This is particularly useful for drilling complex well paths.
- Rotary Steerable Systems (RSS): RSS are more advanced tools that allow us to steer the well while continuously rotating the drill string from the surface. They offer superior control, higher rates of penetration, and improved wellbore quality compared to traditional motor drilling. RSS technology has revolutionized directional drilling, enabling us to reach previously inaccessible reservoirs.
Here’s a simplified comparison of these steering technologies:
Feature | Downhole Motor (Mud Motor) | Rotary Steerable System (RSS) |
Drill String Rotation | The drill string rotates continuously | Generally, higher penetration rates |
Control | Steers by sliding the motor | Steers while rotating, continuous steering |
Penetration Rate | Can be lower in some applications | Produces a smoother, higher-quality wellbore |
Wellbore Quality | Can result in a more tortuous wellbore | Produces a smoother, higher quality wellbore |
Complexity | Simpler, more conventional | The drill string remains stationary during steering |
Bottom Hole Assembly Design: Factors We Consider
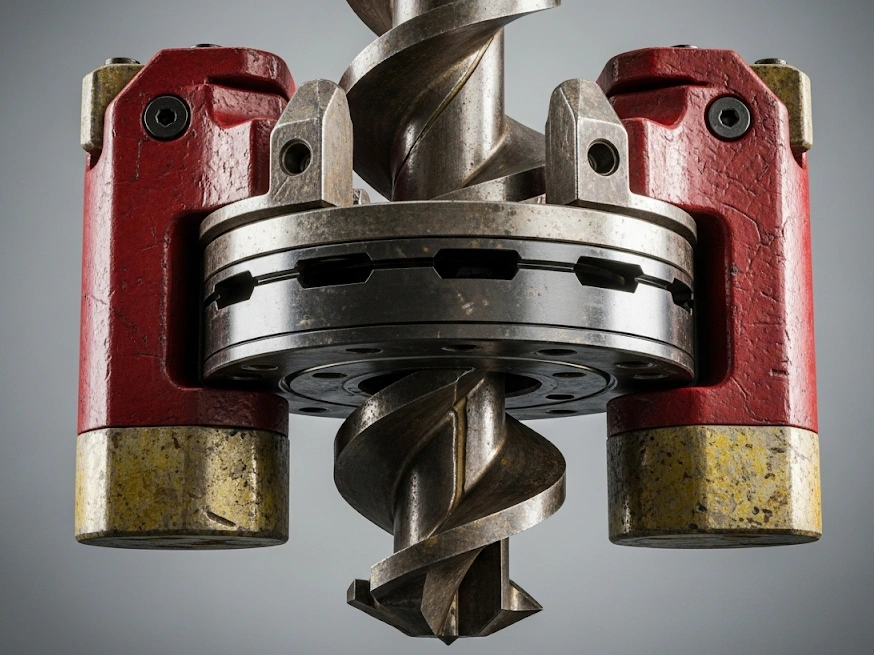
Designing the right Bottom Hole Assembly (BHA) for a particular drilling operation is a complex process that requires careful consideration of numerous factors. Our goal is always to optimize bottom-hole assembly drilling services, ensure wellbore stability, and achieve our geological objectives safely and efficiently. We take into account everything from the type of rock we expect to drill to the specific well path we need to follow.
Formation Characteristics: The Earth’s Blueprint
The geological formation we are drilling through is perhaps the most significant factor influencing our BHA design. Different rock types require different drilling strategies and BHA configurations.
- Hard, Abrasive Formations: For these, we might opt for more robust drill bits (like PDC bits with specific cutter designs) and BHA components designed to withstand high wear and tear. We’ll prioritize weight on the bit and stiffness to ensure efficient rock cutting.
- Soft, Unconsolidated Formations: In contrast, softer formations might require less weight on bit, and we might use drill bits designed for faster penetration rates. Wellbore stability becomes a major concern, so we’ll select stabilizers and potentially incorporate components to minimize vibration and hole enlargement.
- Faults and Fractures: When drilling through areas with faults or natural fractures, we need to design a bottomhole assembly (BHA) that reduces the risk of stuck pipe, lost circulation, or wellbore instability. This may involve adjusting the number and location of stabilizers.
Wellbore Trajectory: Navigating the Subsurface
Whether we are drilling a vertical well, a highly deviated well, or a complex horizontal well, the desired wellbore trajectory determines many of our bottom-hole assembly design choices. This is especially true for bottom-hole assemblies used in directional drilling.
- Vertical Wells: For relatively straight vertical wells, our BHA might be simpler, focusing on maintaining verticality. We’ll typically use heavier drill collars and strategically placed stabilizers to ensure a straight hole.
- Directional and Horizontal Wells: These require much more sophisticated BHAs, often incorporating downhole motors or Rotary Steerable Systems (RSS) for precise steering. The BHA must be capable of building angle, dropping angle, and turning with precision to reach the target reservoir. We also consider the dogleg severity – how quickly the wellbore changes direction – when selecting our BHA components.
Hole Size: Scaling Our Approach
The diameter of the wellbore we are drilling directly affects the size and type of BHA components we can use. Larger wellbore sizes require larger, more robust tools, while smaller wellbore sizes require more compact, specialized equipment. We must ensure that all BHA components fit the planned wellbore diameter and have adequate clearance for drilling fluid circulation and efficient operation.
Drilling Parameters and Performance Objectives: Our Operational Goals
Finally, our specific drilling parameters and overall performance objectives heavily influence BHA design. These include:
- Rate of Penetration (ROP): If high ROP is a priority, we’ll design a BHA that maximizes drilling efficiency, often involving optimized bit selection and potentially RSS.
- Wellbore Quality: For a smooth, in-gauge wellbore, we focus on BHA stability and vibration reduction.
- Cost Efficiency: We always strive for a balance between performance and cost. Selecting the right BHA components can significantly impact drilling time and overall project expenses. For some projects, we might even consider bottom hole assembly rental equipment to manage costs.
- Data Acquisition Needs: If extensive real-time data is required, we’ll incorporate more MWD and LWD tools into the BHA.
By carefully evaluating all these factors, we can custom-design a bottom hole assembly that is tailored to the unique challenges and objectives of each drilling project, leading to safer, more efficient, and more successful operations. Companies like Bottom Hole Assembly Schlumberger are at the forefront of developing advanced BHA solutions.
Conclusion
We hope this comprehensive overview has shed some light on the crucial role of the Bottom Hole Assembly in modern drilling operations. From the cutting edge of the drill bit to the intricate sensors providing real-time data, every component of the BHA plays a vital role in successfully navigating the subsurface. If you’re ever looking for a detailed bottom hole assembly diagram or more information on specific bottom hole assembly components, remember that this vital section of the drill string is the key to successful well delivery.
What aspects of Bottom Hole Assemblies intrigue you the most? We’d love to hear your thoughts in the comments below!