In the industry of drilling , the drill string is a complex assembly of specialized components, each with a distinct role. Among the most fundamental are the drill pipe and the drill collar. While both are tubulars that connect the rig to the drill bit, their design, function, and placement within the drill string vary significantly.
Understanding these differences is crucial for anyone involved in drilling operations, from rig hands to engineers. This guide will clarify the unique characteristics and purposes of drill pipe and drill collars, highlighting why each is indispensable for efficient, safe, and successful wellbore construction.
What is a Drill Pipe?
Recommended Drill Pipes
A drill pipe is a seamless steel tube equipped with threaded tool joints at both ends, forming a crucial part of the drill string in rotary drilling operations. Its primary function is to transmit rotational torque from the rig’s top drive or rotary table to the drill bit, while also conveying drilling fluid down to the bit and back up the annulus to cool and lubricate the bit and carry cuttings to the surface.
What is a Drill Collar?
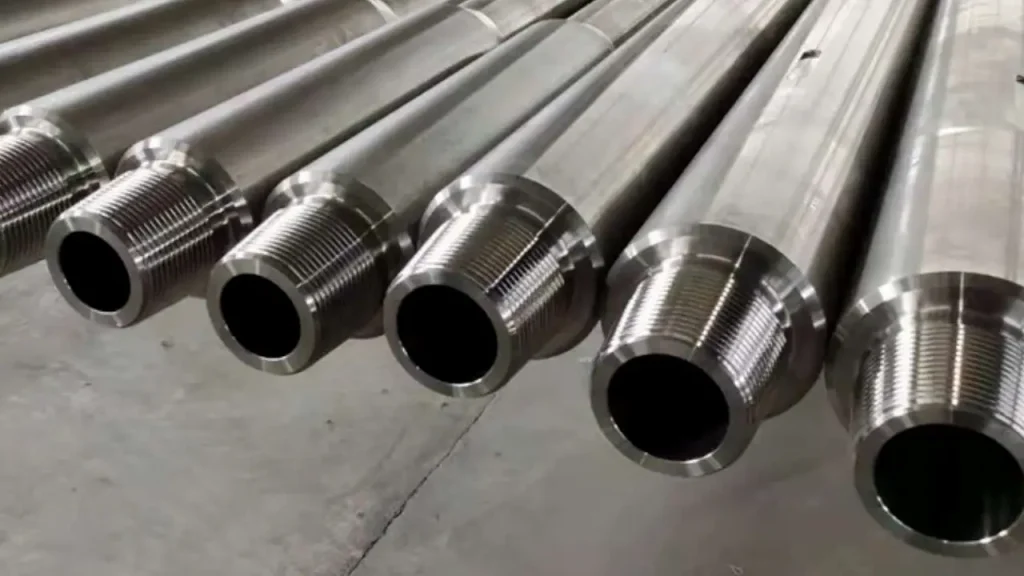
A drill collar is a heavy, thick-walled, steel pipe that is a critical component of the Bottom Hole Assembly (BHA) in a drill string. Unlike drill pipe, its primary function is not to transmit torque over long distances, but to provide concentrated weight directly above the drill bit. This weight helps to apply the necessary force for efficient rock cutting, known as weight-on-bit (WOB), and to keep the drill pipe above it in tension, preventing buckling.
Drill Pipe vs Drill Collar
Understanding the fundamental differences between drill pipe and drill collars is essential for anyone involved in drilling. While both are tubular steel components within the drill string, their design, function, and placement are distinctly different, each serving unique purposes critical to successful drilling operations.
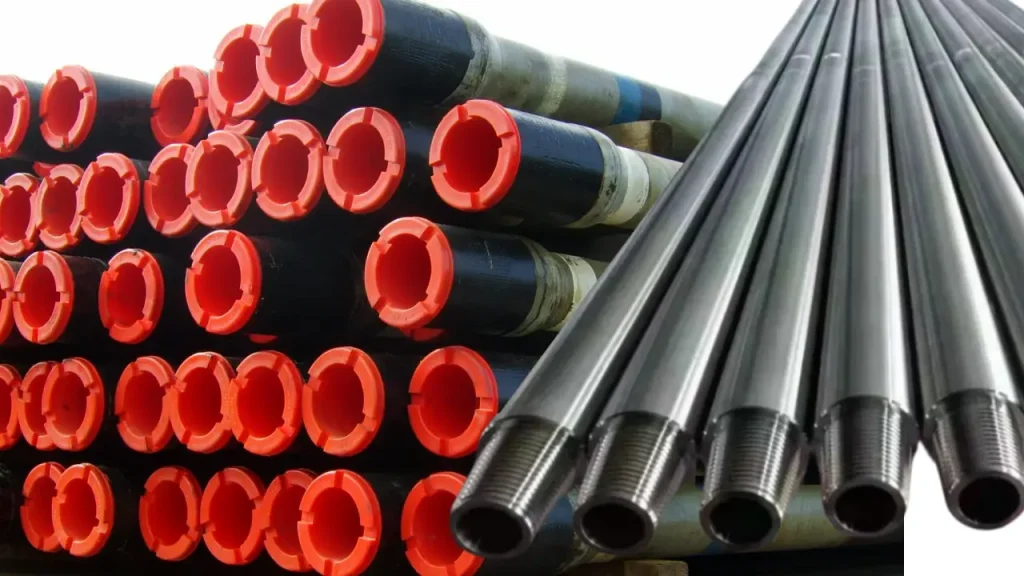
Function
Drill pipe’s primary function is to transmit rotational torque from the surface rig to the drill bit, enabling the cutting action. It also serves as the main conduit for circulating drilling fluid downhole to cool the bit and lift cuttings. Its design prioritizes rotational transfer and fluid flow.
Drill collars, conversely, are primarily designed to provide weight-on-bit (WOB). Their heavy, rigid nature applies the necessary downward force for the drill bit to penetrate rock efficiently. They also help keep the drill pipe above them in tension, preventing buckling and maintaining a stable drilling assembly.
Weight and Wall Thickness
Drill pipe is relatively lightweight with thinner walls compared to drill collars, optimized for transmitting torque over long distances and efficient fluid flow. While its overall length contributes significant weight to the drill string, this weight is distributed.
Drill collars are exceptionally heavy with very thick walls. This design concentrates significant weight in the bottom hole assembly (BHA), directly above the bit, providing the localized downward force required for effective rock cutting.
Placement in Drill String
Drill pipe constitutes the vast majority of the drill string’s length, extending from the surface (below the kelly/top drive) down to the drill collars. It forms the main “body” of the rotating column.
Drill collars are strategically placed at the very bottom of the drill string, directly above the drill bit and below the drill pipe. They form the heaviest and stiffest part of the BHA.
Flexibility and Rigidity
Drill pipe is designed to be relatively flexible, allowing it to navigate deviated and horizontal wellbores without excessive stress. Its flexibility is crucial for directional drilling applications.
Drill collars are designed to be extremely rigid and stiff. This rigidity helps to stabilize the drill bit, minimize vibration, and ensure that the weight applied to the bit translates into effective cutting rather than buckling the drill pipe above.
Stress Management
Drill pipe is primarily subjected to tensile and torsional stresses during drilling operations. Its design focuses on handling these forces over long lengths while maintaining integrity.
Drill collars are primarily subjected to compressive stresses as they provide weight-on-bit. They are designed to withstand these heavy compressive loads without buckling, ensuring consistent force application at the bit.
Comparison Table: Drill Pipe vs. Drill Collar
Aspect | Drill Pipe | Drill Collar |
Primary Function | Transmit torque; circulate drilling fluid | Provide weight-on-bit (WOB); keep pipe in tension |
Weight | Relatively lightweight (distributed along length) | Very heavy (concentrated at bottom) |
Wall Thickness | Thinner walls | Much thicker walls |
Placement | Majority of the drill string, above drill collars | Bottom Hole Assembly (BHA), directly above drill bit |
Flexibility | More flexible (designed for torque and fluid flow, directional drilling) | Highly rigid and stiff (designed to apply WOB and stabilize) |
Primary Stress | Tensile and Torsional | Compressive |
How to Choose Drill Pipe and Drill Collar?
Choosing the appropriate drill pipe and drill collar is paramount for the safety, efficiency, and economic success of any drilling operation. This selection process is not arbitrary but is carefully guided by the specific demands of the well being drilled, the geological formations expected, and the capabilities of the drilling rig. Misjudging these factors can lead to costly failures, non-productive time, and compromised well integrity.
A thorough understanding of the distinct roles and specifications of each component is vital. While drill pipe primarily handles torque and fluid circulation over long lengths, drill collars provide the necessary weight and stiffness at the bottom of the hole. Balancing these elements ensures optimal drilling performance and a stable, reliable drill string.
Here’s how to choose drill pipe and drill collars:
Choosing Drill Pipe:
- Well Depth and Design: Consider the total depth of the well and its trajectory (vertical, deviated, horizontal). Deeper wells require higher strength drill pipe (e.g., S-135) to withstand increased tension, while directional wells may need pipe with specialized fatigue properties to handle bending stresses.
- Drilling Fluid Characteristics: Evaluate the density and rheological properties of the drilling fluid. The drill pipe’s internal diameter impacts fluid hydraulics and pressure losses, so selecting the correct size ensures efficient circulation and effective hole cleaning, preventing pressure-related issues downhole.
- Rig Capacity: Match the drill pipe’s weight and length to the drilling rig’s hoisting capacity and setback area. Overloading the rig can compromise safety and operational efficiency, making it crucial to select pipe that the rig can safely handle and store during drilling operations.
- Formation Abrasiveness: For abrasive formations, consider drill pipe with external hardbanding on tool joints. Hardbanding reduces wear on the tool joints and protects the pipe body from external abrasion, extending the lifespan of the pipe and reducing the frequency of costly replacements.
- Connection Type: Select drill pipe with tool joint connections suitable for the anticipated torque requirements and well conditions. Various API and proprietary connections offer different levels of strength and sealing capability, crucial for preventing unscrewing or leaks during drilling.
Choosing Drill Collar:
- Weight on Bit (WOB) Requirement: Determine the optimal weight on bit needed for efficient penetration of the expected rock formations. The total weight provided by the drill collars must be sufficient to achieve target penetration rates without buckling the drill pipe above them.
- Hole Size: The outer diameter of the drill collars must be compatible with the planned hole size. Typically, there’s a specific clearance required between the drill collar OD and the hole ID to allow for proper fluid flow and to prevent differential sticking in the wellbore.
- Stiffness and Stability: Consider the stiffness required to prevent drill string buckling and ensure bit stability. Larger diameter and thicker-walled drill collars provide greater stiffness, which is crucial for maintaining a straight hole and reducing harmful vibrations that can damage the bit and other BHA components.
- Fatigue Resistance: In challenging drilling environments (e.g., highly deviated wells), select drill collars with enhanced fatigue resistance. This ensures the collars can withstand repeated bending and torsional stresses over their service life, minimizing the risk of fatigue-related failures downhole.
- Connection Compatibility: Ensure the drill collar connections are compatible with the drill pipe connections and other BHA components. Standardized API connections are common, but proprietary connections may be used in specialized BHA designs, requiring careful matching to avoid operational issues.
Conclusion
This guide has illuminated the fundamental distinctions between drill pipe and drill collars, two critical, yet functionally diverse, components of the drill string. We’ve seen how drill pipe, with its lighter weight and primary role in torque transmission and fluid circulation, forms the bulk of the drill string.
Conversely, drill collars, with their significantly greater weight and rigidity, are strategically placed at the bottom to provide the essential weight-on-bit, crucial for efficient rock cutting. Understanding these specific roles is vital for designing effective drill strings, preventing failures, and optimizing drilling parameters for various geological conditions.
For high-quality, reliable drill pipe and drill collars that meet stringent industry standards, consider wholesale drill pipes from Sinodrills. Our commitment to precision manufacturing ensures that your drill string components perform optimally, contributing to the safety and success of your drilling projects.