Drilling efficiency in down-the-hole (DTH) operations hinges significantly on selecting the appropriate bit face design for the prevailing rock conditions. This crucial choice directly influences factors like penetration rate, hole straightness, and the overall lifespan of your drilling tools.
Understanding the unique characteristics of different DTH bit face designs—such as flat, convex, concave, and DGR—is essential. Each design is engineered to perform optimally in specific rock types and drilling scenarios, ensuring you achieve the best results for your project.
What is DTH Bit Face?
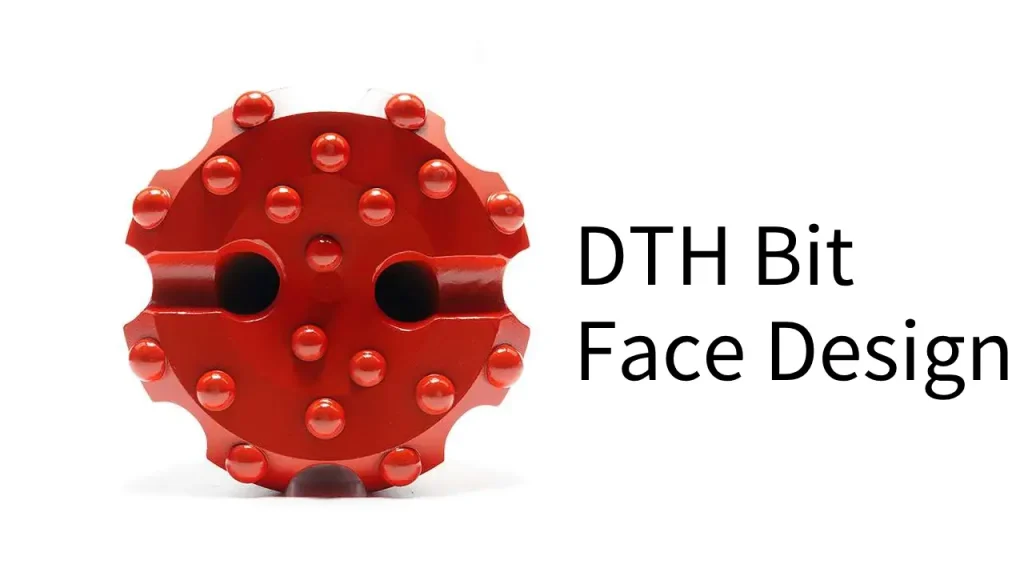
A DTH (Down-The-Hole) bit face refers to the front-end design of a drilling bit, specifically the surface that makes direct contact with the rock during drilling. This face is equipped with carbide buttons arranged in various patterns and shapes, which are crucial for breaking and crushing the rock.
Different face styles, such as flat, convex, concave, and DGR, are engineered to optimize drilling performance based on the hardness, abrasiveness, and fracture characteristics of the rock formation.
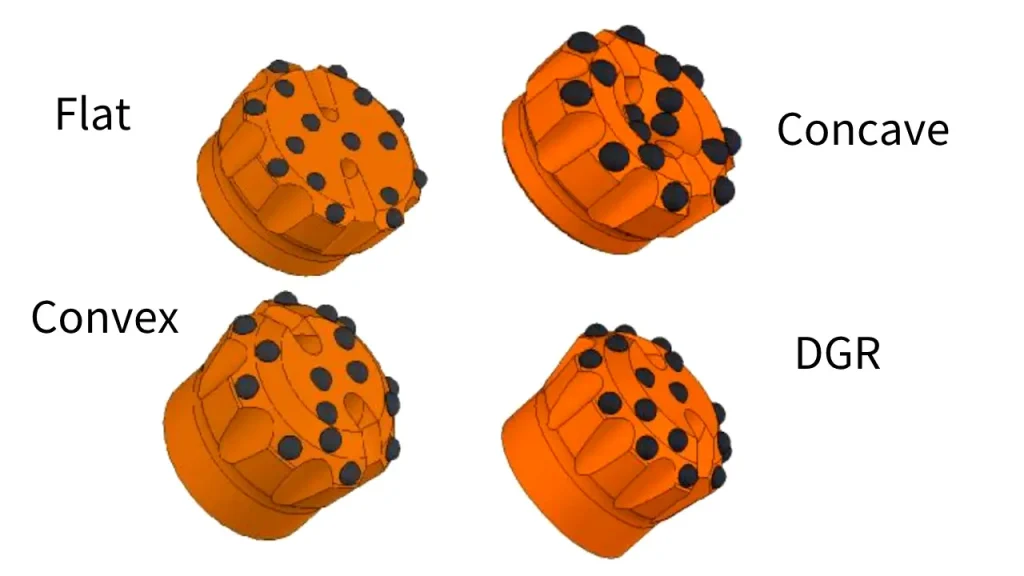
DTH Bit Face Design Types
DTH button bits utilize various face styles, each optimized for specific rock formations and drilling conditions. The choice of face style significantly impacts drilling efficiency, hole deviation control, and bit lifespan, adapting to the abrasiveness and hardness of the rock.
Flat Face
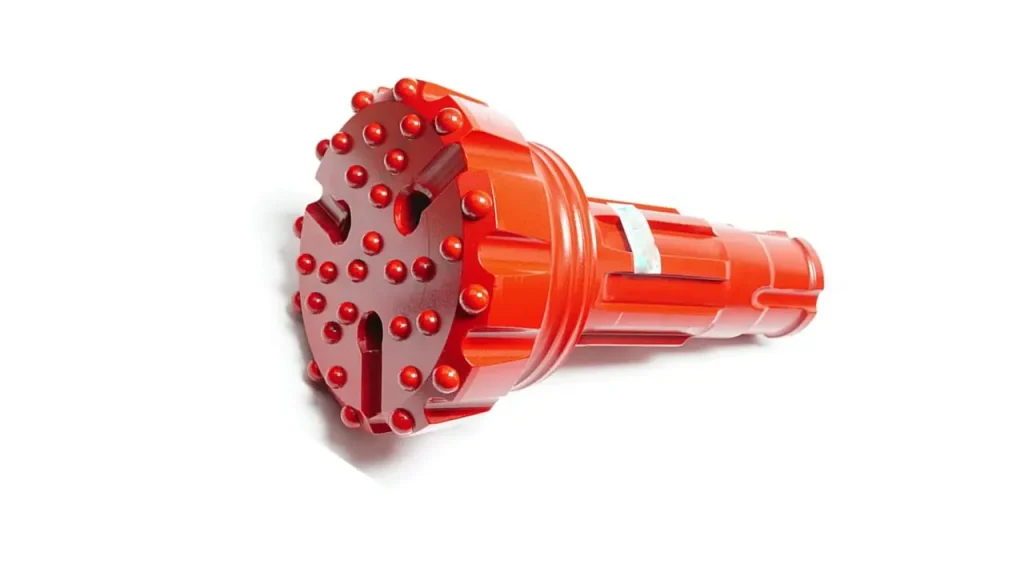
The flat face DTH drill bit design is an all-around option frequently chosen for its versatility and effectiveness, particularly in hard and abrasive rock formations. This design typically features hemispherical buttons, which are considered the most popular choice due to their universal application across various rock types and their suitability for the hardest and most abrasive conditions.
This robust design ensures high resistance to wear and tear, making it ideal for environments where the drill bit experiences significant friction and impact. The combination of a flat face with hemispherical buttons provides consistent and reliable drilling performance even in challenging geological conditions, where durability and longevity are paramount.
Convex Face
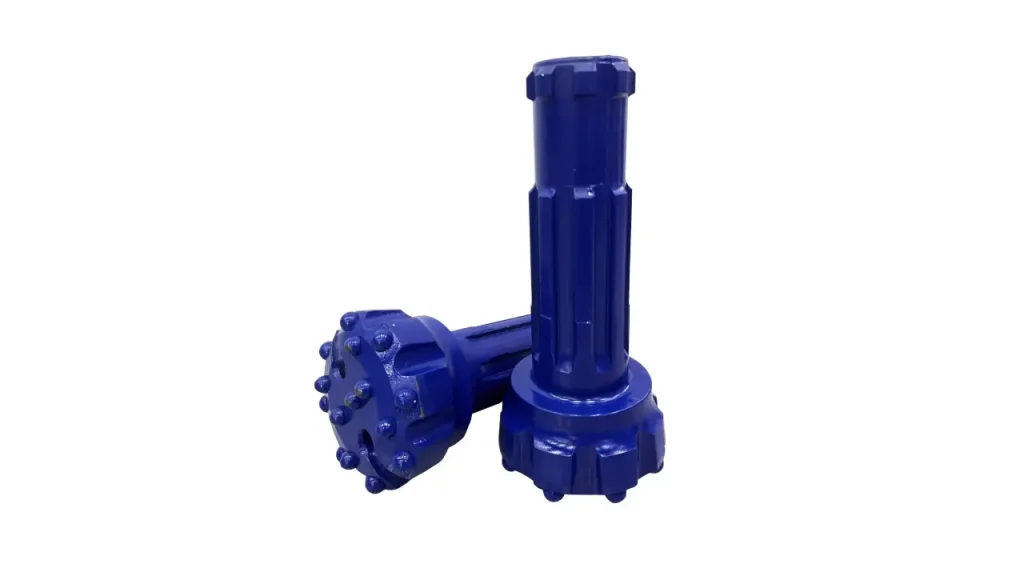
The convex face DTH bit is a classic design specifically tailored for drilling in soft to medium-hard rock formations that are not highly abrasive. This face style is renowned for its excellent penetration rate, allowing for rapid drilling progress in suitable ground conditions.
However, a notable disadvantage of the convex face is its tendency for poor hole deviation control when drilling through hard rocks. This means that in inconsistent or very hard formations, the bit may struggle to maintain a straight hole, potentially leading to inaccuracies in the drilling path.
Concave Face
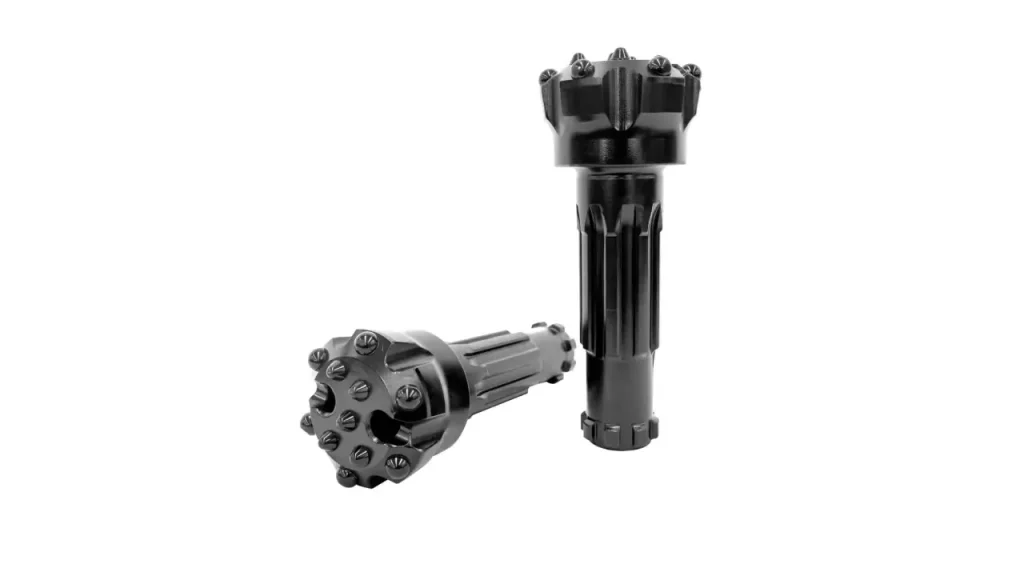
The concave face design is best suited for medium-hard to hard rock formations, particularly those that are less abrasive and fractured. This design offers exceptional control over hole deviation, making it an excellent choice for deep hole drilling applications where maintaining precise straightness is critical.
The unique shape of the concave face helps to stabilize the drill bit within the bore, minimizing any tendency for the hole to deviate from its intended path. This characteristic is highly beneficial for projects requiring high accuracy and consistent hole geometry over extended depths.
DGR Face
The DGR (Double Gauge Row) face is a specialized design developed for drilling in hard or very hard rock conditions. Its distinctive feature is the inclusion of double gauge row buttons, which provide superior wear resistance and significantly extend the bit’s operational lifetime.
This advanced design is typically employed only for larger diameter button bits. The enhanced durability offered by the double gauge row buttons ensures that these bits can endure the extreme forces and abrasive conditions encountered in the toughest rock formations, maximizing productivity and reducing the need for frequent bit replacements.
How to Choose a Suitable DTH Bit Face
Choosing a suitable DTH bit face is critical for optimizing drilling performance, ensuring efficiency, and maximizing bit lifespan. The selection process depends on several key factors related to the geological conditions and the desired drilling outcome. Matching the bit face style to the specific rock formation and drilling requirements is essential for achieving the best results.
Considerations such as rock hardness, abrasiveness, and the presence of fractures significantly influence which DTH bit face will perform most effectively. Each face design offers distinct advantages and disadvantages, making a careful assessment of drilling conditions paramount for selecting the right tool for the job.
Here’s how to choose a suitable DTH bit face:
- Assess Rock Hardness: For extremely hard and abrasive rock formations, a flat face design with hemispherical buttons is generally recommended as it offers superior durability and wear resistance in challenging conditions.
- Consider Abrasiveness: In abrasive rock conditions, a flat face is often preferred due to its robust design, which helps withstand friction and wear, leading to a longer bit life and consistent performance.
- Evaluate Rock Fractures: For less fractured rock formations, the concave face provides excellent hole deviation control, ensuring a straight bore, which is crucial for precision in deep drilling applications.
- Prioritize Penetration Rate: When drilling in soft to medium-hard, non-abrasive rocks, a convex face is ideal for achieving a high penetration rate, allowing for faster drilling progress and increased productivity.
- Account for Hole Deviation Control: If maintaining a straight hole is paramount, especially in medium-hard to hard, less abrasive, and unfractured rocks, the concave face is the best choice for its superior accuracy.
- Determine Bit Diameter and Rock Type: For larger diameter bits drilling in very hard rock, the DGR (Double Gauge Row) face provides enhanced wear resistance and extended bit life due to its specialized button configuration.
Conclusion
Drilling efficiency in down-the-hole (DTH) operations hinges significantly on selecting the appropriate bit face design for the prevailing rock conditions. This crucial choice directly influences factors like penetration rate, hole straightness, and the overall lifespan of your drilling tools, ensuring optimal performance.
Understanding the unique characteristics of different DTH bit face designs—such as flat, convex, concave, and DGR—is essential. Each design is engineered to perform optimally in specific rock types and drilling scenarios, enabling you to achieve the best results for your project.
For wholesale DTH drill bits and hammers, you can find a comprehensive range of quality products to suit your specific drilling needs from Sinodrills. Their expertise ensures you get the right tools for optimal drilling performance.