Drilling tools operate in some of the most abrasive and corrosive environments imaginable, making their protection paramount for longevity and performance. Understanding the nuances of zinc coatings is critical to maximizing the resilience of your equipment. This blog will explore the distinctions between hot-dipped and other galvanized finishes.
Choosing the right protective coating directly impacts operational efficiency and replacement costs. We’ll delve into how these different galvanization processes affect the durability, adhesion, and overall lifespan of your valuable drilling tools, helping you make informed decisions for enhanced resilience.
What is Hot Dipped Galvanized?
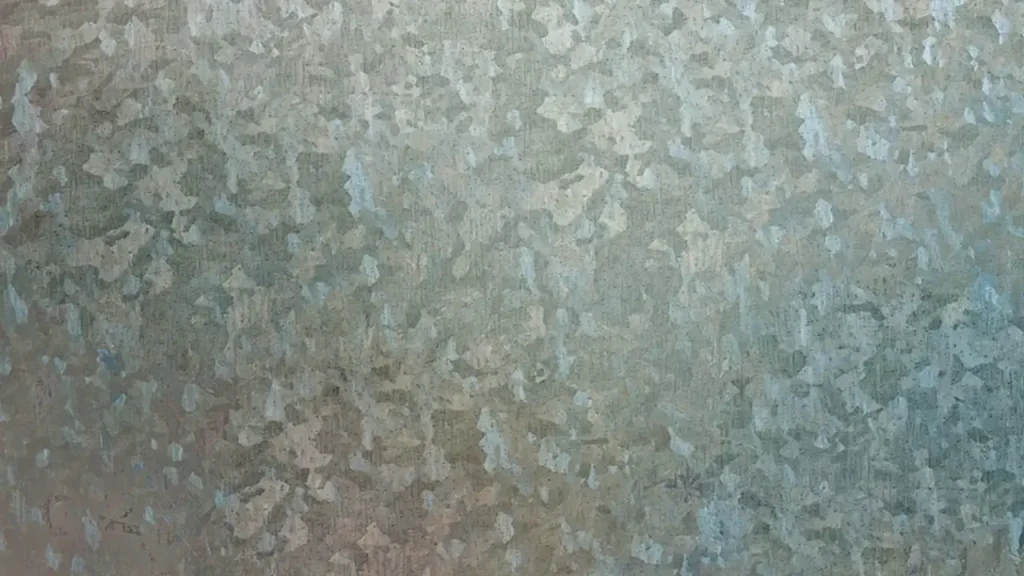
Hot-dipped galvanizing is a highly effective method of applying a protective zinc coating to steel or iron. The process involves thoroughly cleaning the steel item and then immersing it in a bath of molten zinc, typically maintained at temperatures around 450°C (840°F).
While submerged, the zinc metallurgically bonds with the iron in the steel, forming a series of durable zinc-iron alloy layers, topped by an outer layer of pure zinc. This comprehensive coating provides both a robust barrier against corrosive elements and cathodic (sacrificial) protection, where the zinc corrodes preferentially to the steel, significantly extending the lifespan of the metal, especially in harsh outdoor or industrial environments.
What is Galvanized?
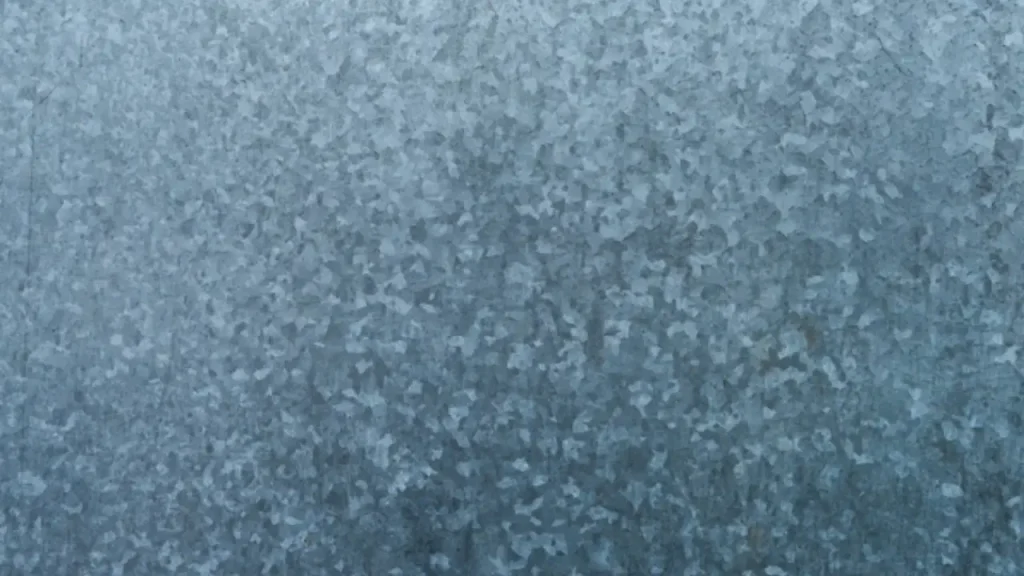
Galvanizing is a general term for the process of applying a protective zinc coating to steel or iron to prevent rusting. This can be achieved through various methods, with the most common being hot-dip galvanizing, but also including electro-galvanizing (zinc plating), sherardizing, and zinc spraying.
The zinc acts as a sacrificial layer, corroding before the steel, and also provides a barrier, preventing corrosive substances from reaching the base metal. This significantly extends the lifespan of steel products, making them suitable for a wide range of applications where corrosion resistance is required.
Hot Dipped Galvanized vs Galvanized
Understanding the distinction between hot-dipped and other galvanized coatings is crucial for selecting the optimal corrosion protection for your steel products, particularly drilling tools. While both involve zinc, their application methods yield vastly different results in terms of durability and performance.
This comparison will detail the key differences, helping you make an informed decision to enhance the resilience and longevity of your equipment in demanding environments.
Process of Application
Hot-dip galvanizing involves immersing thoroughly cleaned steel into a bath of molten zinc. This high-temperature process creates a metallurgical bond, forming multiple layers of zinc-iron alloys and an outer layer of pure zinc on the steel’s surface.
In contrast, other galvanizing methods like electro-galvanizing (zinc plating) apply zinc through an electrochemical process at room temperature. This results in a purely mechanical bond, typically a thinner and more uniform zinc layer, without the alloy formation characteristic of hot-dipping.
Coating Thickness
Hot-dip galvanized coatings are significantly thicker, typically ranging from 60 to 100 microns, or even more. This substantial zinc layer provides a robust barrier and a larger reserve of sacrificial protection, leading to extended service life in harsh conditions.
Zinc-plated coatings are considerably thinner, usually between 5 to 10 microns. While this thin layer offers some initial corrosion resistance, its limited thickness means it will deplete much faster, offering less long-term protection, especially in aggressive environments.
Adhesion and Durability
The metallurgical bond formed during hot-dip galvanizing creates an incredibly strong adhesion between the zinc and steel. This makes the coating highly resistant to chipping, flaking, and abrasion, ensuring its integrity even under physical stress during drilling operations.
Zinc-plated coatings, with their mechanical bond, are less adherent and more susceptible to damage. They can more easily scratch or chip, exposing the underlying steel to corrosion, which compromises the protective barrier prematurely.
Corrosion Protection Mechanism
Hot-dip galvanization provides superior barrier protection due to its thickness and robust nature. Crucially, it offers excellent cathodic (sacrificial) protection: if the coating is damaged, the surrounding zinc will corrode before the underlying steel, protecting the base metal from rust.
Zinc plating primarily offers barrier protection. While it does provide some sacrificial action, its thinness limits its effectiveness in this regard. Once the thin zinc layer is breached, the underlying steel is more quickly exposed to corrosive elements.
Appearance
Hot-dip galvanized surfaces typically have a dull grey, somewhat rough, and often non-uniform appearance, sometimes with spangle patterns, due to the thicker coating and cooling process. This finish is generally acceptable for industrial or construction applications where functionality outweighs aesthetics.
Zinc-plated items, being thinner and more uniformly applied, have a brighter, smoother, and more aesthetically pleasing finish, often with a silvery, blue, or yellow tint (from chromate conversion). This makes them preferred for applications where visual appeal is important and corrosion risk is lower.
Here are some differences between hot-dip galvanized and galvanized coatings:
Feature | Hot-Dipped Galvanized | Other Galvanized (e.g., Zinc Plated) |
Application Process | Immersion in molten zinc; metallurgical bond formed | Electrochemical deposition; mechanical bond |
Coating Thickness | 60-100+ microns (thick) | 5-10 microns (thin) |
Adhesion | Excellent (metallurgical bond), highly durable | Good (mechanical bond), less resistant to chipping |
Corrosion Protection | Superior barrier and sacrificial (cathodic) protection | Primarily barrier, limited sacrificial protection |
Appearance | Dull grey, rough, sometimes non-uniform (spangle) | Bright, smooth, uniform (silvery, blue, or yellow tint) |
Cost | Generally higher initial cost for the coating process | Generally lower initial cost for the coating process |
Durability in Harsh Environments | Excellent; long lifespan | Moderate; shorter lifespan in corrosive conditions |
Application Suitability | Outdoor, industrial, marine, highly corrosive environments | Indoor, mild environments, aesthetic applications |
Hot Dipped Galvanized vs Galvanized Self Drilling Anchors
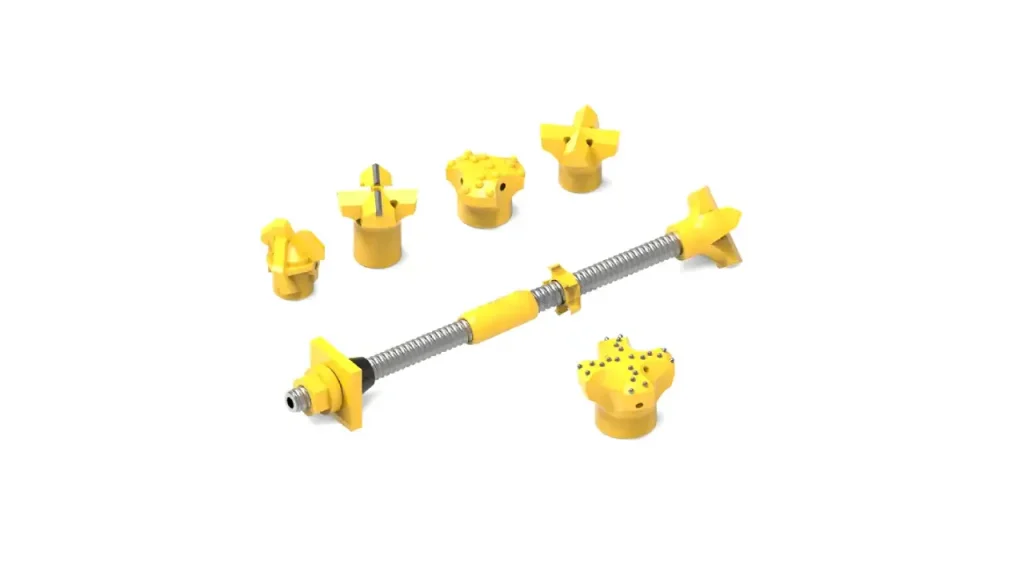
When selecting self-drilling anchors for demanding geotechnical projects, the type of zinc coating significantly impacts performance and longevity. While both “galvanized” and “hot-dipped galvanized” refer to zinc protection, their application methods yield vastly different results crucial for your SDA tools.
This comparison highlights the key differences, helping you choose the optimal corrosion protection for enhancing the resilience and lifespan of your self-drilling anchors in challenging environments.
Process of Application
Hot-dip galvanization for self-drilling anchors involves immersing the fully fabricated steel components (bars, nuts, plates, bits, couplings) into a bath of molten zinc. This high-temperature process creates a metallurgical bond, forming multiple layers of zinc-iron alloys and an outer layer of pure zinc on the steel’s surface, ensuring a comprehensive and durable coating that adheres strongly to the complex shapes of SDA components.
Conversely, other galvanizing methods, such as electro-galvanizing (zinc plating) for SDAs, apply zinc through an electrochemical process at room temperature. This results in a purely mechanical bond, typically a thinner and more uniform zinc layer, without the alloy formation characteristic of hot-dipping. This process can be more controlled for specific thread tolerances but offers less robust overall protection.
Coating Thickness
Hot-dip galvanized self-drilling anchors boast significantly thicker zinc coatings, generally ranging from 60 to 100 microns, or even more, depending on the steel thickness. This substantial layer provides an unparalleled barrier against corrosive elements and a larger reserve of sacrificial zinc, which is critical for the long-term integrity of anchors buried in aggressive ground conditions.
Zinc-plated self-drilling anchors, by contrast, feature considerably thinner coatings, usually between 5 to 10 microns. While this thin layer offers some initial corrosion resistance, its limited thickness means it will deplete much faster, offering substantially less long-term protection against the highly corrosive groundwaters and soils encountered in geotechnical applications.
Adhesion and Durability
The metallurgical bond formed during hot-dip galvanizing provides exceptional adhesion of the zinc to the steel surface of the self-drilling anchor. This robust bond, including the formation of tough zinc-iron alloy layers, makes the coating highly resistant to chipping, flaking, and abrasion, which is crucial given the mechanical stresses and ground friction experienced during SDA installation and long-term service.
Zinc-plated coatings, relying on a mechanical bond, are inherently less adherent and more susceptible to damage from impact, abrasion, or bending. For self-drilling anchors, which undergo significant stress during drilling and grouting, a compromised coating can quickly lead to exposed steel and premature corrosion.
Corrosion Protection Mechanism
Hot-dip galvanized self-drilling anchors provide superior barrier protection due to their impressive thickness and a highly effective cathodic (sacrificial) protection mechanism. If the coating on an SDA bar or component is scratched or compromised by rocks, the surrounding zinc will preferentially corrode, protecting the underlying steel from rust and maintaining the anchor’s structural integrity over decades.
Zinc plating on SDAs primarily offers barrier protection. While it does provide some sacrificial action, its thinness severely limits its effectiveness in this regard. Once the thin zinc layer is breached, especially in aggressive geotechnical environments, the underlying steel of the self-drilling anchor is much more quickly exposed to corrosive elements, accelerating degradation.
Suitability for Harsh Environments
Hot-dip galvanized self-drilling anchors are unequivocally better suited for highly aggressive and corrosive environments, such as those found in marine applications, contaminated soils, acidic groundwaters, or areas with high saline content. Their thick, durable coating ensures maximum longevity and performance, making them the preferred choice for critical, long-term ground support in challenging geotechnical projects.
Zinc-plated self-drilling anchors, due to their thinner coating and weaker adhesion, are generally only suitable for very mild, non-corrosive environments or for temporary applications where a short service life is expected. They are rarely recommended for permanent ground support in typical construction or mining conditions due to their limited long-term corrosion resistance.
Hot Dipped Galvanized vs. Other Galvanized Self-Drilling Anchors
Feature | Hot-Dipped Galvanized SDA | Other Galvanized SDA (e.g., Zinc Plated) |
Application Process | Immersion in molten zinc; metallurgical bond formed | Electrochemical deposition; mechanical bond |
Coating Thickness | 60-100+ microns (thick, consistent coverage on complex shapes) | 5-10 microns (thin, uniform but limited protection) |
Adhesion & Durability | Excellent (metallurgical bond), highly resistant to abrasion/impact | Good (mechanical bond), more susceptible to chipping/flaking |
Corrosion Protection | Superior barrier and sacrificial (cathodic) protection | Primarily barrier, limited sacrificial protection |
Suitability for Harsh Environments | Excellent; long-term performance in aggressive ground | Poor; short-term or mild environments only |
Cost (typically) | Higher initial cost | Lower initial cost |
Typical Lifespan | Decades | Months to a few years in corrosive conditions |
How to Choose Hot Dipped Galvanized and Galvanized Drilling Tools
Choosing between hot-dipped galvanized and other forms of galvanized drilling tools hinges on understanding your project’s specific environmental conditions and expected lifespan requirements.
For applications in highly corrosive environments like marine, industrial, or acidic/alkaline ground conditions, hot-dipped galvanized tools are the superior choice due to their thick, durable, and sacrificially protective coating, ensuring maximum longevity and reducing replacement costs.
Conversely, if your drilling operations are in mild, indoor, or less corrosive environments where aesthetics or tighter tolerances are paramount, and a shorter lifespan is acceptable, then other galvanized (e.g., zinc-plated) tools might suffice.
- Corrosivity of Environment: For aggressive environments (saltwater, acidic soil, industrial pollution), choose hot-dipped galvanized for its robust, long-lasting protection. For mild, dry conditions, other galvanized coatings may be adequate.
- Expected Lifespan: If long-term durability and minimal maintenance are critical, hot-dipped galvanized tools are the better investment. For temporary use or short-term projects, other galvanized options can be more economical.
- Physical Abrasion/Impact: Drilling tools often experience significant wear. Hot-dipped coatings offer superior resistance to chipping and flaking due to their metallurgical bond, making them more durable under physical stress.
- Tolerance Requirements: While hot-dipping adds thickness, which might affect very tight tolerances, it’s generally manageable. For extremely precise fits where even minimal coating thickness is an issue, alternatives might be considered if corrosion is not severe.
- Budget vs. Lifecycle Cost: Hot-dipped tools have a higher initial cost but offer a lower lifecycle cost due to their extended durability and reduced need for replacement or maintenance in harsh conditions.
Conclusion
In conclusion, the choice between hot-dipped galvanized and other forms of galvanized coatings for your drilling tools significantly impacts their long-term performance and cost-effectiveness. Hot-dip galvanization offers a superior, thicker, and more metallurgically bonded zinc layer, providing unparalleled corrosion resistance and durability crucial for harsh drilling environments.
While other galvanizing methods offer some protection, the robust nature of hot-dip galvanization ensures your drilling tools withstand aggressive conditions, reducing wear, minimizing maintenance, and extending operational life. This translates directly into greater efficiency and significant savings over time, safeguarding your investment in vital equipment.
For all your drilling tool needs, including those requiring superior corrosion protection, consider sourcing wholesale drilling tools from Sinodrills. We are committed to providing high-quality, durable products, ensuring your equipment is built to last in the toughest conditions. Trust Sinodrills for reliable and resilient solutions.