As explorers of the Earth’s subsurface, we continually seek ways to enhance our understanding of the geological formations encountered during drilling operations. This quest for knowledge has led to revolutionary advancements, one of the most significant being Measurement While Drilling (MWD).
MWD technology provides real-time data from the bottom of the wellbore, allowing us to make informed decisions and optimize our drilling processes like never before.
What is Measurement While Drilling?
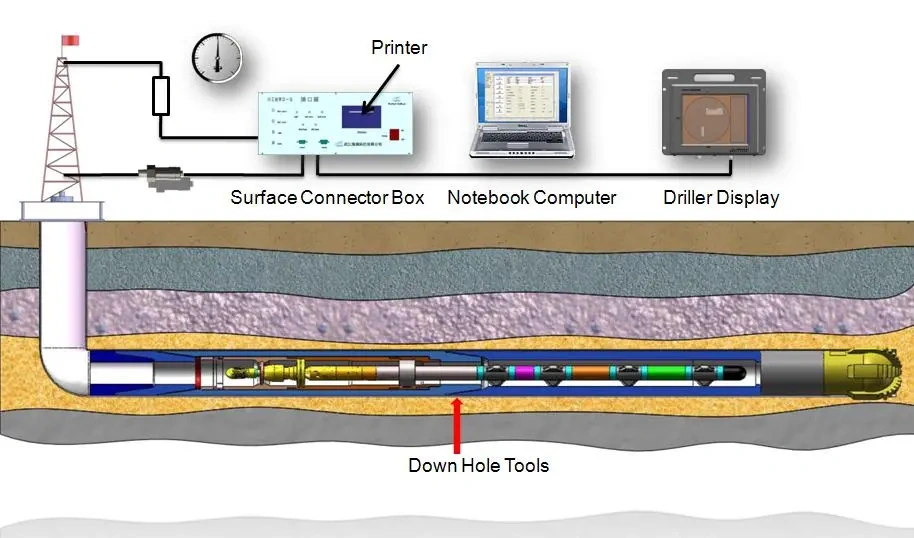
Measurement While Drilling (MWD) is a sophisticated technology that has transformed the way we approach oil and gas exploration and other drilling activities.
Simply put, MWD involves equipping the drill string with specialized sensors that gather critical downhole data. This information is then transmitted to the surface in real-time, providing our engineers and geologists with an immediate snapshot of conditions deep within the Earth.
Before MWD, we relied on taking the drill pipe out of the hole to acquire data, a time-consuming and expensive process. MWD eliminates this need, allowing for continuous data collection and significantly improving drilling efficiency and safety.
How Does Measurement While Drilling Work?
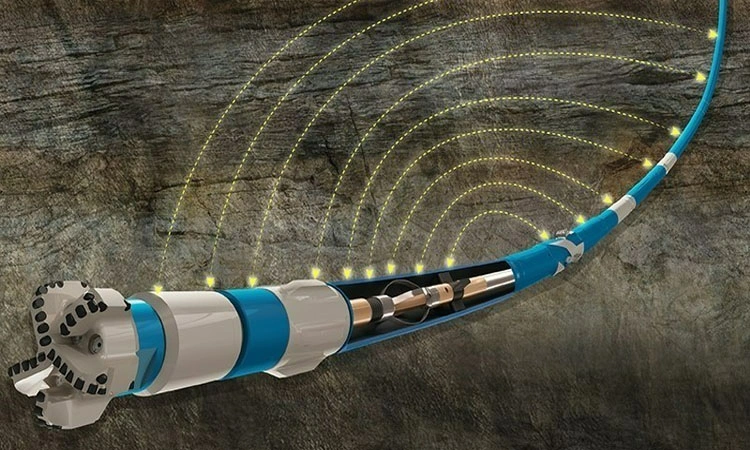
The core of Measurement While Drilling (MWD) lies in its ability to transmit data from the harsh downhole environment to the surface. This is achieved through a combination of sophisticated sensors and reliable communication methods. Understanding these mechanisms helps us appreciate the complexity and ingenuity of MWD technology.
The Downhole Component: Sensors and Data Acquisition
At the heart of the drill string, just above the drill bit, sits the MWD tool. This tool houses an array of sensors designed to measure various parameters. These sensors are incredibly robust, built to withstand extreme temperatures, pressures, and vibrations inherent in the drilling process.
- Gamma Ray (GR): Measures natural radioactivity of formations, helping to identify lithology (rock type) and differentiate between shales and sandstones.
- Resistivity (Res): Measures the electrical resistance of formations, which can indicate the presence of hydrocarbons or water.
- Inclination and Azimuth: Essential for determining the wellbore’s deviation from vertical and its directional orientation. These are crucial for accurate, good placement.
- Annular Pressure: Monitors the pressure in the annulus (the space between the drill pipe and the wellbore wall), vital for good control and preventing kicks.
- Vibration and Shock: Detects vibrations and shocks experienced by the drill bit and bottom hole assembly, helping us optimize drilling parameters and prevent equipment damage.
- Temperature: Measures the downhole temperature, important for understanding fluid properties and tool limitations.
The Transmission System: Getting Data to the Surface
Once the data is acquired, it needs to be transmitted to our surface monitoring stations. The most common method for data transmission in Measurement While Drilling (MWD) is through pressure pulses in the drilling fluid (mud pulse telemetry).
- Data Encoding: The acquired sensor data is converted into a digital format.
- Pulse Generation: A pulse mechanism within the MWD tool creates pressure fluctuations (pulses) in the drilling fluid flowing inside the drill pipe. These pulses are either positive (pressure increases) or negative (pressure decreases) and are generated by briefly restricting or releasing the flow of drilling fluid.
- Pulse Transmission: These pressure pulses travel up the drilling fluid column at the speed of sound, reaching the surface in a matter of seconds.
- Surface Reception: At the surface, transducers detect these pressure pulses.
- Data Decoding: A sophisticated surface system decodes the pulses back into meaningful data, which is then displayed and analyzed by our engineers.
While mud pulse telemetry is dominant, other, less common methods include electromagnetic (EM) telemetry, which transmits data as electromagnetic waves through the Earth, and wired drill pipe systems, which use an internal cable for high-speed data transfer.
Applications of Measurement While Drilling
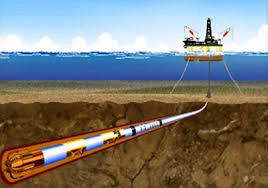
Drilling Optimization
Measurement While Drilling (MWD) plays a crucial role in optimizing the drilling process by providing real-time data on downhole conditions. This includes parameters such as weight on bit, torque, and revolutions per minute, allowing drillers to make immediate adjustments to improve efficiency and reduce non-productive time. By continuously monitoring these variables, operators can maintain optimal drilling parameters, leading to faster penetration rates and reduced wear on equipment.
Geosteering
MWD is indispensable for geosteering, enabling precise well placement within desired geological targets. By integrating real-time gamma ray, resistivity, and other formation evaluation measurements, drillers can steer the wellbore horizontally or vertically to maximize reservoir exposure. This ensures the well stays within the most productive zones, enhancing hydrocarbon recovery and overall field development.
Wellbore Positioning
Accurate wellbore positioning is critical for avoiding collisions with existing wells and for efficient field development. MWD systems provide real-time directional surveys, including inclination, azimuth, and tool face, allowing for precise tracking of the wellbore’s path. This data is vital for ensuring the well reaches its intended target safely and efficiently, minimizing the risk of sidetracks or environmental incidents.
Safety and Risk Mitigation
MWD contributes significantly to drilling safety and risk mitigation by providing early detection of potential hazards. Real-time monitoring of downhole pressure, temperature, and gas detection allows operators to identify and respond quickly to abnormal conditions such as kicks or lost circulation. This proactive approach helps prevent well control incidents, protects personnel, and safeguards the environment.
Directional Drilling and Wellbore Placement
One of the most prominent applications of Measurement While Drilling (MWD) is in directional drilling. By continuously monitoring the wellbore’s inclination and azimuth, we can precisely guide the drill bit to hit specific geological targets. This is especially crucial in unconventional reservoirs, where wells need to be drilled horizontally for extended distances to maximize contact with the pay zone.
- Real-time Course Correction: MWD allows us to make immediate adjustments to the drilling trajectory, ensuring we stay on target and avoid costly sidetracks.
- Multi-well Pads: We can drill multiple wells from a single surface location, minimizing the environmental footprint and infrastructure requirements.
- Complex Well Paths: MWD enables the creation of highly complex well paths, such as “snake wells” or “fish hooks,” to optimize reservoir drainage.
Geosteering: Hitting the Sweet Spot
Geosteering is the art and science of navigating the drill bit within a specific geological formation (the “sweet spot”) based on real-time MWD logging data. This application is paramount for maximizing hydrocarbon recovery and optimizing production.
MWD Parameter | Geosteering Application | Benefit |
Gamma Ray | Identifying shale boundaries and staying within hydrocarbon-rich sand layers. | Maximizes exposure to hydrocarbons, avoids non-productive zones. |
Resistivity | Differentiating between oil/gas-bearing zones and water-bearing zones. | Optimizes well placement within the most productive parts of the reservoir. |
Annular Pressure | Maintaining optimal drilling parameters and preventing formation damage. | Reduces drilling risks and ensures wellbore stability. |
By analyzing changes in gamma-ray and resistivity readings, our geologists can interpret the subsurface in real-time and guide the drillers to keep the wellbore within the most productive zones.
Drilling Optimization and Efficiency
Measurement While Drilling (MWD) plays a vital role in optimizing the overall drilling process, leading to significant time and cost savings.
- Real-time Performance Monitoring: MWD data allows us to monitor drilling parameters like weight on bit, revolutions per minute, and torque, helping us identify and correct inefficiencies.
- Reduced Non-Productive Time (NPT): By providing immediate feedback, MWD helps us identify and mitigate potential issues like stuck pipes, lost circulation, or equipment failures before they escalate, thereby reducing costly downtime.
- Improved Bit Performance: Understanding downhole vibrations and forces through MWD helps us select the most appropriate drill bits and optimize drilling parameters for maximum penetration rates and bit life.
Wellbore Safety and Integrity
The real-time information provided by Measurement While Drilling (MWD) is crucial for ensuring the safety and integrity of the wellbore, protecting both personnel and the environment.
- Early Kick Detection: Monitoring annular pressure and flow rates in real-time allows for early detection of formation influxes (“kicks”), enabling prompt action to prevent blowouts.
- Pressure Management: MWD provides vital information for maintaining safe operating pressures within the wellbore, preventing lost circulation and wellbore instability.
- Optimized Casing Design: Understanding formation pressures and temperatures from MWD data helps us design more effective casing programs, ensuring long-term wellbore integrity.
Difference Between Logging While Drilling and Measurement While Drilling
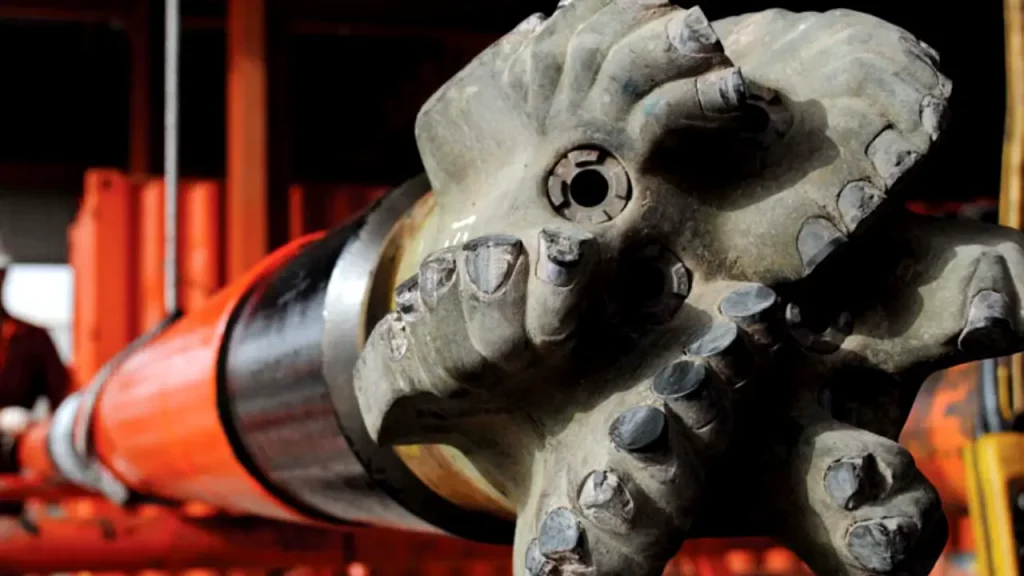
While the terms Measurement While Drilling (MWD) and Logging While Drilling (LWD) are often used interchangeably, there’s a subtle but important distinction in their primary functions.
MWD fundamentally focuses on the mechanical aspects of drilling and borehole trajectory. It provides real-time data crucial for guiding the drill bit, such as inclination (the angle of deviation from vertical), azimuth (the direction of the wellbore relative to North), toolface (the rotational orientation of the drilling assembly), and basic drilling dynamics, including vibrations and pressures. This information is vital for accurate good placement and ensuring the drill path follows the design.
On the other hand, it is specifically designed for formation evaluation. Although it is often integrated with MWD for data transmission, its core purpose is to collect detailed petrophysical information about the rock formation being drilled through.
LWD tools measure properties like gamma ray (natural radioactivity, indicating rock type), resistivity (electrical conductivity, hinting at fluid content), porosity (pore space in the rock), and density. This “logging” data helps us understand the reservoir’s characteristics, identify hydrocarbon-bearing zones, and make informed decisions about completing the well, making LWD the “eyes” that see the geology.
Why Choose Measurement While Drilling
Measurement While Drilling (MWD) technology has revolutionized the drilling industry by providing immediate, accurate data directly from the bottom of the well, eliminating the need to halt operations for data acquisition.
This real-time insight empowers drillers to make informed decisions quickly, leading to significant improvements in efficiency, safety, and ultimately, cost savings. Key reasons to choose MWD include:
- Enhanced Drilling Efficiency: Real-time data on drilling parameters like weight on bit, torque, and RPM allows for immediate adjustments, optimizing drilling performance, reducing non-productive time, and increasing penetration rates.
- Improved Wellbore Placement: MWD provides precise directional surveys, including inclination and azimuth, enabling accurate steering of the wellbore to hit specific geological targets, which is crucial for maximizing reservoir exposure in directional and horizontal drilling.
- Reduced Operational Costs: By optimizing drilling parameters, preventing costly errors, and minimizing the need for sidetracks or separate wireline logging runs, MWD directly contributes to lower overall drilling expenses.
- Increased Safety and Risk Mitigation: Continuous monitoring of downhole conditions helps in early detection of potential hazards like abnormal pressures or wellbore instability, allowing for proactive measures to prevent incidents and ensure personnel safety.
- Better Formation Evaluation: When combined with Logging While Drilling (LWD), MWD systems provide valuable real-time geological information, enabling better understanding of the rock types, fluid content, and other formation characteristics, which aids in reservoir characterization and development decisions.
Conclusion
Measurement while drilling has revolutionized the drilling industry. From enabling precise directional drilling and intelligent steering to improving safety and optimizing operational efficiency, MWD provides the real-time information we need to navigate complex subsurface environments.
Ready to revolutionize your drilling operations? Don’t settle for anything less than precision and performance. Choose Sinodrills for your premium Measurement While Drilling (MWD) tools and unlock unparalleled efficiency, accuracy, and safety in every well.
Contact us today to discuss your specific drilling needs and discover how Sinodrills’ cutting-edge MWD technology can optimize your projects and drive your success. Invest in the future of drilling with Sinodrills – where innovation meets reliability.