Custom Overburden Casing System Manufacturer in China
Struggling with challenging ground conditions? Unstable boreholes and lost tools can derail your drilling projects. Our Overburden Casing System provides a complete, robust solution for unmatched stability and efficiency, ensuring seamless drilling through unconsolidated formations. Achieve superior penetration rates and significantly reduce costly delays, keeping your operations on track and under budget.
Sinodrills - Your Trusted Overburden Casing System Manufacturer from China
Struggling with challenging ground conditions? Unstable boreholes and lost tools can derail your drilling projects. Our Overburden Casing System provides a complete, robust solution for unmatched stability and efficiency, ensuring seamless drilling through unconsolidated formations. Achieve superior penetration rates and significantly reduce costly delays, keeping your operations on track and under budget.
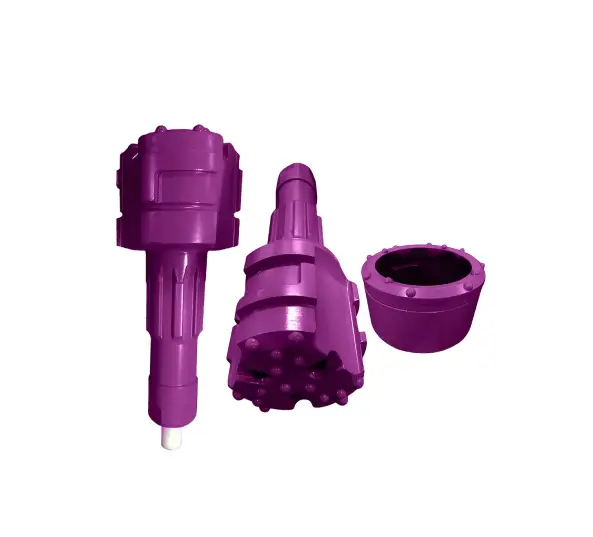
overburden casing system benefits
Enhanced Borehole Stability: Provides immediate and continuous support in challenging ground, preventing collapses and ensuring a stable drilling environment.
Faster Drilling Penetration: Enables more efficient drilling through unconsolidated formations by stabilizing the borehole and preventing jamming, leading to quicker project completion.
Reduced Risk of Tool Loss: Minimizes the chance of losing valuable drilling tools due to ground collapse or sticking, saving significant replacement costs and downtime.
Improved Safety: Contributes to a safer work environment by mitigating hazards associated with unstable ground, protecting personnel and equipment.
Cost and Time Savings: By preventing delays, reducing tool loss, and accelerating drilling, the system significantly lowers overall project expenses and shortens timelines.
Eccentric Overburden Drilling Casing System
An Eccentric Overburden Drilling Casing System is a specialized method that allows for simultaneous drilling and casing installation, particularly effective in unstable or unconsolidated ground. Here are its key advantages:
Simultaneous Drilling and Casing: It drills and installs casing at the same time, providing immediate borehole stability and preventing collapse in loose or fractured formations.
Retrievable Drilling Tools: The eccentric reamer bit can be retracted by reversing rotation, allowing the entire drill string (pilot bit and reamer) to be retrieved through the installed casing for reuse in subsequent holes, saving on tooling costs.
Efficient in Difficult Ground: Designed to handle challenging ground conditions such as sand, gravel, cobbles, boulders, and fractured rock, where conventional drilling methods might struggle with hole stability.
High Penetration Rates: Effectively transmits percussive force from the DTH hammer, enabling efficient drilling through various formations.
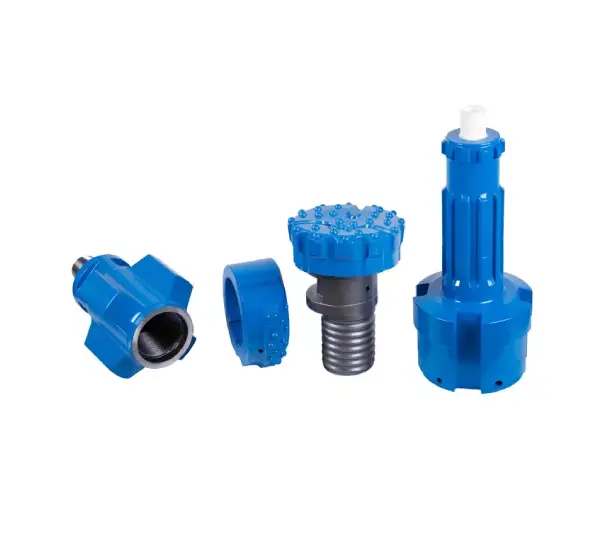
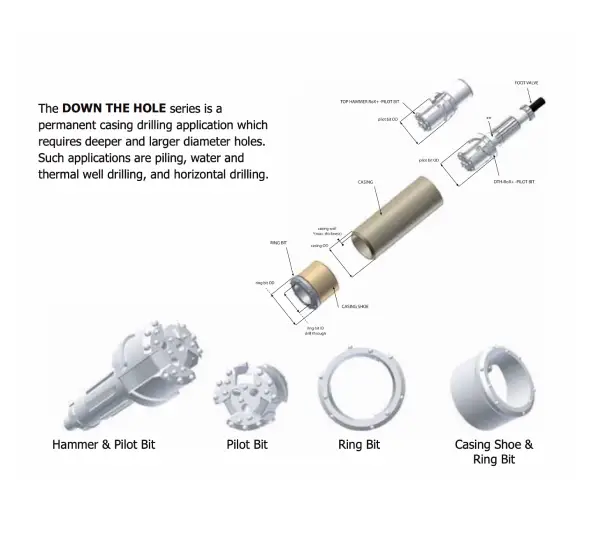
overburden drilling system components
Hammer & Pilot Bit: This integrated assembly typically initiates the drilling process, with the pilot bit leading the way to create a guide hole while the hammer mechanism delivers percussive energy to break through tough ground formations.
Pilot Bit: The pilot bit is the initial cutting tool that drills a small-diameter lead hole, guiding the rest of the drilling assembly and ensuring the desired trajectory for the subsequent larger diameter casing.
Ring Bit: This crucial component, often surrounding the pilot bit, reams the hole to a larger diameter, allowing the casing to be installed simultaneously with the drilling process, maintaining borehole stability.
Casing Shoe & Ring Bit: This combined unit is attached to the bottom of the casing, facilitating its advancement. The ring bit portion drills the hole, while the casing shoe provides a durable interface for driving the casing through overburden.
Casing: The casing is a steel pipe that follows the drilling assembly, permanently lining the borehole to prevent collapse, isolate different geological layers, and ensure the long-term integrity of the drilled well or foundation.
Customize Your Desired Overburden Casing System
Casing Diameter and Wall Thickness
We can customize the casing diameter to precisely fit your required borehole size, from smaller geothermal applications to large-diameter piling. We also offer various wall thicknesses to match the anticipated ground pressure and abrasive conditions, ensuring optimal strength and longevity for your specific project.
Drive Shoe and Bit Design
We tailor the drive shoe to optimize penetration and minimize wear in your specific ground conditions, whether it’s soft soil, gravel, or fractured rock. Our bit designs, including eccentric and concentric options, are also customized to maximize drilling efficiency and tool life based on the geology you’re encountering.
Connection Type and Length
We provide a range of connection types, such as API threads or proprietary interlocking systems, to ensure secure and efficient make-up and break-out of casing strings. The length of individual casing sections can also be customized to suit your rig’s capabilities and project depth requirements, streamlining your operations.
Material Grade and Coating
We offer various material grades for the casing, selected based on the corrosiveness of the ground and the required tensile strength. Additionally, we can apply specialized coatings to enhance wear resistance, reduce friction, or provide extra corrosion protection, extending the life of your system in challenging environments.
what is Overburden Casing System?
An Overburden Casing System simultaneously drills and installs casing to prevent hole collapse in unstable ground like loose soil, gravel, or fractured rock. It uses specialized drill bits (eccentric or concentric) that create a bore slightly larger than the casing, allowing it to follow directly behind, ensuring borehole stability.
what does Overburden Casing System have?
An Overburden Casing System is a specialized drilling method designed to simultaneously drill a borehole and install casing, which is crucial for maintaining hole stability in unconsolidated or unstable ground.
This system essentially has components that work in tandem to create a bore and immediately reinforce it, preventing collapse. Key components typically include:
Drill Bit Assembly: This usually consists of a pilot bit for initial penetration and a reaming component (like a ring bit or an eccentric reamer) that enlarges the hole to allow the casing to follow.
Casing Shoe: A robust ring attached to the bottom of the casing, designed to withstand the forces of drilling and to guide the casing into the freshly drilled hole.
Casing: The steel pipe itself, which is advanced into the ground as drilling progresses, forming a permanent or retrievable lining for the borehole.
Drill Hammer/Rig: The power source, such as a Down-The-Hole (DTH) hammer or a top hammer rig, which provides the percussive and/or rotary force to drive the drill bit assembly and advance the casing.
Drill Rods/Inner Rods: Connect the drill hammer to the pilot bit, transmitting power and allowing for flushing of cuttings.
What Are the Primary Advantages of Using an Overburden Casing System?
The primary advantages of an overburden casing system revolve around its ability to simultaneously drill and install casing, which is crucial for maintaining borehole stability in challenging ground conditions.
This concurrent process effectively prevents borehole collapse, a common and costly issue encountered with conventional drilling methods in unstable formations like unconsolidated soils, gravels, or highly fractured rock.
By continuously casing the hole as it’s drilled, the system significantly reduces:
Risk of borehole collapse: Direct and immediate casing prevents unstable ground from falling into the bore.
Loss of drilling tools: Tools are less likely to get stuck or lost in collapsing ground.
Need for additional stabilization methods: Eliminates the necessity for drilling fluids or other temporary support in many cases.
Project time and costs: Speeds up overall completion by reducing delays and rework associated with hole instability.
How Do Different Overburden Casing Systems (e.g., Eccentric, Concentric) Vary in Operation and Suitability?
Overburden casing systems primarily differ in their reaming mechanism, which influences their operation and suitability for various ground conditions. Eccentric casing systems utilize a pilot bit that is offset and expands outwards to ream a hole larger than the casing.
This design allows for the drill string (pilot bit and hammer) to be retrieved through the casing after drilling.
Eccentric Systems:
- Operation: Pilot bit is offset and reams the hole by expanding outwards, driven by the hammer.
- Suitability: Often preferred in less challenging ground, offering easier retrieval of the drill string through the casing.
Concentric systems (e.g., Ring Bit, Tubex) feature a pilot bit surrounded by a reaming ring (often sacrificial) that drills a consistent hole perfectly sized for the casing. These systems are generally more robust and perform well in difficult, boulder-rich, or highly fractured ground, as their reaming action is more consistent.
Concentric Systems:
- Operation: Pilot bit and surrounding reaming ring drill a full-face hole for the casing.
- Suitability: More robust for very difficult ground, including boulders and highly fractured rock, but drill components may be lost in hole.
how to use Overburden Casing System?

Overburden casing systems efficiently drill and install casing simultaneously, providing borehole stability in challenging ground conditions. This method is vital for preventing collapse in loose or fractured formations, ensuring successful drilling operations.
Step 1: Initial Setup and Drilling Commencement
The drilling process begins with the assembly of the overburden system, attaching the drill bit and casing shoe to the casing. The entire assembly is then positioned at the desired drilling location. Rotation and percussive force are applied, initiating penetration into the overburden material.
Step 2: Simultaneous Drilling and Casing Advancement
As the drill bit cuts through the ground, the casing shoe, attached to the leading edge of the casing, follows immediately behind. The reaming action of the drill bit creates a slightly larger diameter hole, allowing the casing to be driven or rotated into place concurrently with the drilling. This continuous process ensures the borehole is cased as it’s formed, preventing collapse.
Step 3: Completion and System Retrieval
Once the desired depth is reached, or stable ground is encountered, the drilling operation ceases. The internal drilling components, such as the drill bit and hammer, are then retrieved from inside the installed casing. The permanent casing remains in place, providing a stable and secure borehole for subsequent operations or for the intended purpose of the well.
Send Your Inquiry Now
All-in-one Overburden Casing System Solutions for Your Project
Struggling with collapsing boreholes in challenging ground? Our all-in-one overburden casing system eliminates this frustration, ensuring stable, secure drilling. Achieve project success faster and more reliably with our integrated, high-performance solutions, designed for seamless simultaneous drilling and casing installation, saving you time and costly delays.