Self-drilling anchor bolts stand out as a game-changer. These remarkable anchors combine drilling, grouting, and anchoring into a single, efficient process, offering unparalleled advantages in various challenging ground conditions. In this blog post, we’ll explore the extensive range of self-drilling anchor bolt applications, highlighting why they’ve become an indispensable tool for engineers and contractors worldwide.
What are Self-Drilling Anchor Bolts?
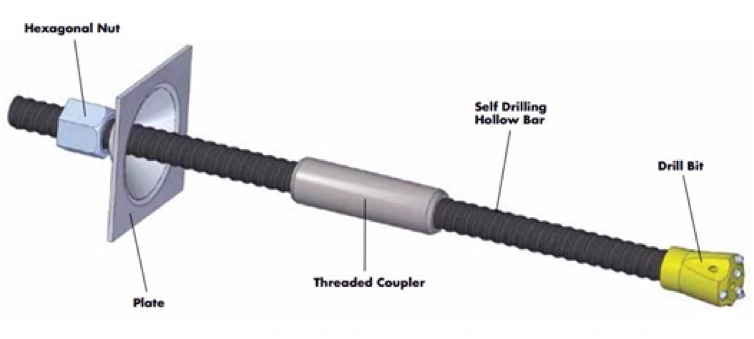
Before diving into their applications, let’s briefly understand what self-drilling anchor bolts are. Unlike traditional anchoring methods that require pre-drilling a hole, inserting an anchor, and then grouting, SDAs integrate a sacrificial drill bit with a hollow anchor bar.
As the bar rotates, it drills its own hole, and grout can be simultaneously injected through the hollow core, filling the annulus and bonding the anchor to the surrounding ground. This ingenious design not only saves significant time and labor but also enhances the reliability of the anchor in complex geological formations.
Self Drilling Anchor Bolt Applications
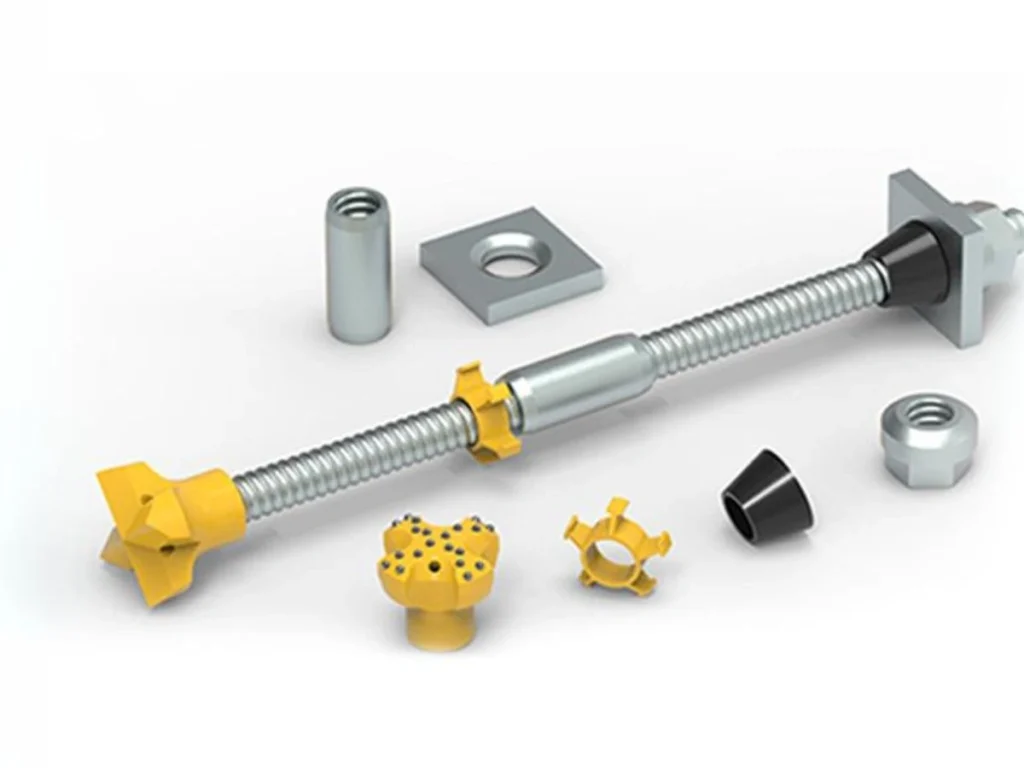
We’ve frequently encountered situations where ground conditions were less than ideal, requiring robust solutions for stability. This is where self-drilling anchor bolt applications for ground reinforcement truly shine. They’ve allowed us to tackle projects that would have been far more complex and costly with conventional methods.
Slope Stabilization
Slopes, whether natural or man-made, are constantly subject to erosion and instability. I’ve personally overseen numerous projects where self-drilling anchor bolts were the key to effectively stabilizing these critical areas.
Challenge | SDA Solution | Benefits I’ve Observed |
Eroding soil slopes | Installing a grid of SDAs to create a reinforced soil mass, often combined with geogrids or shotcrete. | Minimized excavation, rapid installation, effective in loose or cohesive soils, and reduced risk of landslides. |
Rockfall mitigation | Anchoring mesh or netting to rock faces using SDAs to prevent dislodged rocks from endangering structures or infrastructure. | Precise placement, ability to drill into variable rock types, and enhanced safety. |
Tunneling and underground excavation
Tunneling projects always present unique geotechnical challenges. We place particular emphasis on the efficiency and reliability of self-drilling anchors in such environments.
Key Applications in Tunneling
- Temporary Support for Tunnel Faces: As we excavate, immediate support is crucial to prevent collapse. SDAs provide rapid and reliable temporary support, allowing for safe progression.
- Permanent Rock Support: For long-term stability, SDAs are used to create a durable support system, often in conjunction with shotcrete or steel lagging.
- Portal Stabilization: Securing the entrance and exit points of tunnels is paramount, and SDAs offer an excellent solution for stabilizing the surrounding rock and soil.
Mining and Specialized Geotechnical Applications
The mining industry, with its unique set of challenges, has also extensively adopted self-drilling anchor bolt applications. Their ability to perform in often harsh and unpredictable conditions makes them ideal for ensuring safety and operational efficiency. Beyond mining, there are several specialized geotechnical scenarios where SDAs are my go-to choice.
Ground Support in Mines
Safety is paramount in mining operations. I’ve seen SDAs used for:
- Roof and rib support: Providing immediate and long-term stability in underground mine workings.
- Shaft lining reinforcement: Ensuring the integrity of vertical access shafts.
- Rescue and escape route stabilization: Maintaining safe passage in emergency scenarios.
The speed of installation and the ability to grout simultaneously are particularly beneficial in dynamic mining environments where ground conditions can change rapidly.
Disaster Mitigation and Emergency Repairs
In times of natural disaster, rapid response is crucial. I’ve been involved in emergency projects where self-drilling anchor bolts were deployed to quickly stabilize areas affected by landslides or washouts, preventing further damage and facilitating recovery efforts. Their deployability in difficult-to-access areas makes them invaluable in such critical situations.
Advantages of Self-Drilling Hollow Bolt
Self-drilling hollow anchors offer significant benefits for a wide range of construction and geotechnical projects. These innovative anchors, commonly referred to as SDAs, offer an attractive alternative to traditional methods by streamlining the entire anchoring process. Their unique design combines drilling, grouting, and anchoring in one package, with benefits that translate directly into greater efficiency, improved safety, and superior field performance.
Installation Speed and Efficiency
Unlike traditional anchor systems that require a multi-stage process (first drilling, then inserting the anchor, and finally grouting), self-drilling hollow anchors can perform all of these operations simultaneously. The hollow rod itself acts as the drill rod, and as it penetrates deeper into the ground, grout is simultaneously injected through its core, filling the annulus and forming a strong bond.
This “drill-and-inject” approach significantly reduces overall installation time, reduces labor costs, and generally speeds up project schedules, which is critical in today’s fast-paced construction environment.
Versatility
Self-drilling hollow anchors excel in challenging and changing ground conditions where traditional methods often fail. I have witnessed their effective installation in a variety of situations, from loose, cohesionless soils and gravel to highly fractured rock mass, and even through pebbles and boulders. The continuous flushing action of the grout during drilling helps stabilize the borehole and prevent collapse of unstable ground, a common problem in pre-drilling.
This adaptability minimizes the need for specialized drilling techniques or casing, making the Self-Drilling Hollow Bolt (SDA) a versatile solution for a variety of geological formations and reducing the risk of project delays due to unforeseen complex geological conditions.
Enhanced Safety and Environmental Benefits
In addition to efficiency, enhanced safety and environmental benefits are key benefits. The integrated drilling and grouting process means fewer individual components to handle and separate operations, which inherently reduces the possibility of accidents on site.
The minimal vibration generated during installation makes the SDA ideal for use in existing sensitive structures, near historic buildings, or in urban environments where ground disturbance must be minimized. In addition, injecting the grout directly into the borehole ensures more efficient material utilization and reduces waste, which contributes to cleaner, more environmentally friendly construction practices.
Superior bond and reliability
The superior bond and reliability achieved by self-drilling hollow bolts are critical to the long-term integrity of any structure they support. Simultaneous grouting ensures that the drilled hole is completely filled, preventing voids and creating a strong, continuous bond between the bolt and the surrounding ground.
This improves load-bearing capacity and creates a more reliable bolting system, even in conditions where traditional bolt installations may fail. From slope stabilization and tunnel support to foundation reinforcement and retaining wall construction, the consistent performance and proven durability of self-drilling hollow bolts give engineers and contractors greater confidence in the stability and durability of their projects.
Self-drilling Hollow Anchor Bar V.S. Mortar Bolt
When we talk about ground anchoring, Self-Drilling Hollow Anchor Bars (SDAs) and Mortar Bolts (often referring to traditional grouted rock bolts) represent two distinct approaches, each with specific strengths and applications. I’ve used both extensively, and understanding their differences is crucial for choosing the right solution.
Self-Drilling Hollow Anchor Bars are the more advanced, all-in-one system. Their key advantage lies in their integrated drilling and grouting capability. As the hollow bar, equipped with a sacrificial drill bit, penetrates the ground, grout is simultaneously injected through its core. This makes them exceptionally efficient in challenging ground conditions like loose soils, fractured rock, or water-bearing formations, where pre-drilling a stable hole for a conventional bolt would be difficult or impossible. They offer high installation speed and minimal site disturbance.
In contrast, a Mortar Bolt typically refers to a solid steel bar that requires a pre-drilled borehole before it can be inserted and then grouted with cementitious mortar or resin. This method relies on the integrity of the pre-drilled hole.
While simpler and often more cost-effective in stable, competent rock or concrete, it becomes problematic in collapsing or unstable ground, often requiring casing, which adds time and expense. Mortar bolts are commonly used in structural applications where ground conditions are predictable or for reinforcing existing concrete/masonry.
Conclusion
From stabilizing precarious slopes and underpinning historic buildings to securing vital infrastructure and supporting complex mining operations, self-drilling anchor bolt applications are as diverse as the challenges we face in ground engineering. The efficiency, adaptability, and reliability they offer have not only streamlined our work processes but also enabled us to achieve results that were once considered difficult or impossible.
As we continue to push the boundaries of civil engineering, we anticipate that the innovation in self-drilling anchor bolt applications will only grow, further cementing their role as a cornerstone of modern construction. They are more than just anchors; they are a testament to how smart design can provide powerful, elegant solutions to some of our most persistent geotechnical challenges.