Drilling is an inherently jarring process, with constant percussive forces and vibrations taking a toll on valuable equipment. This relentless pounding can lead to premature wear, costly downtime, and reduced drilling efficiency. Understanding how to mitigate these destructive forces is crucial for any successful drilling operation.
Enter the Shock Sub – a seemingly simple yet incredibly vital component in modern drilling. This blog post will delve into what a Shock Sub is, exploring its ingenious design and how it acts as a crucial buffer. We will also uncover its diverse applications across various drilling scenarios, highlighting its indispensable role in protecting your investment and optimizing performance.
What is Shock Sub?
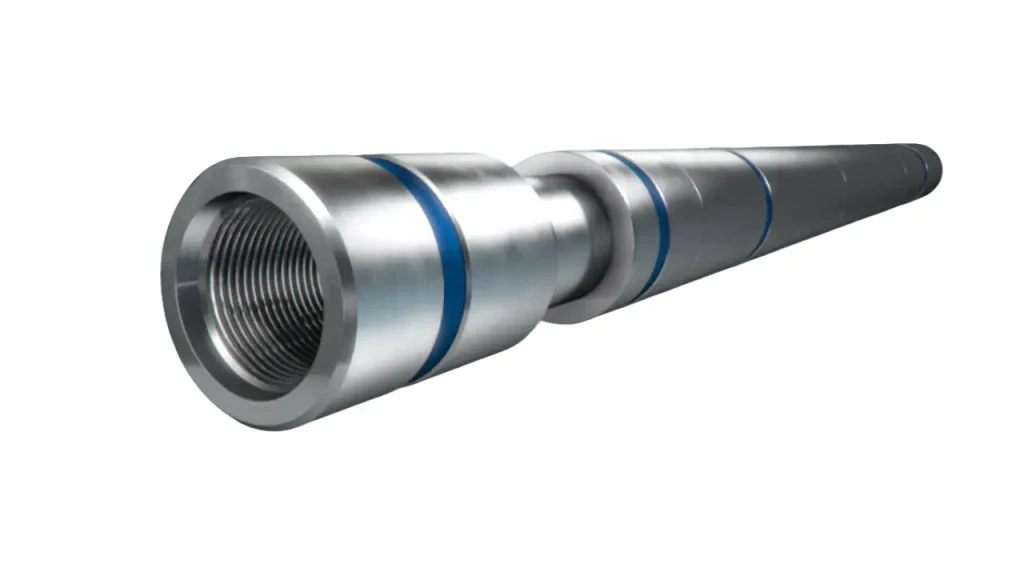
A Shock Sub is a specialized drill string component designed to absorb and dampen the significant axial and torsional dynamic loads, or “shocks,” generated by the drill bit during drilling operations.
Placed strategically in the bottom hole assembly (BHA), typically close to the drill bit or DTH hammer, it utilizes internal mechanisms like springs or elastomers to compress and expand, thereby isolating the rest of the drill string, the rig, and sensitive downhole instruments from harmful vibrations. This action mitigates stress, reduces wear and tear on equipment, improves drilling efficiency, and extends the lifespan of expensive components.
Shock Sub Structure
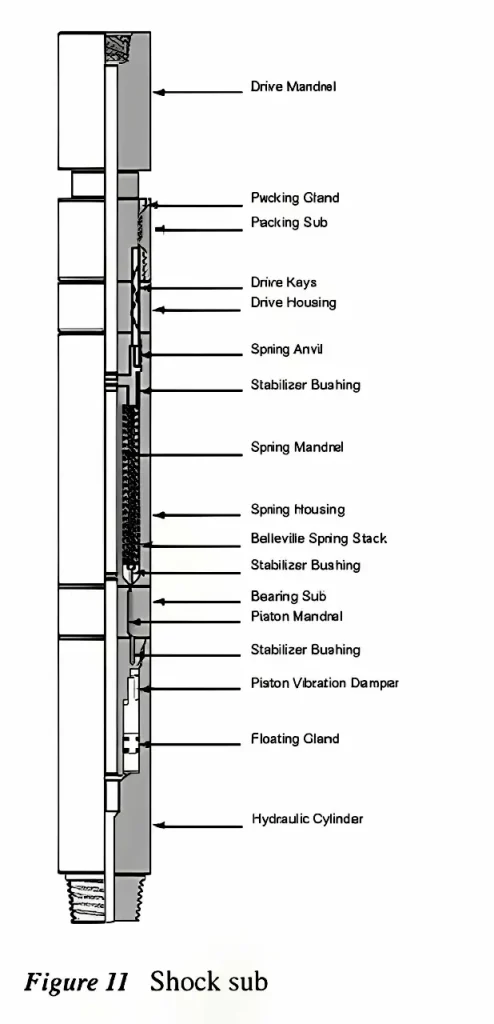
The provided shock sub’ structure presents a detailed cross-sectional view of a “Shock Sub” structure, which is an essential component in drilling operations. This device plays a critical role in absorbing and dampening the severe shocks and vibrations that occur during drilling, thereby protecting the drill bit, drill string, and surface equipment from damage and extending their lifespan.
The design effectively converts the impact energy into manageable forms, often through the compression of a spring stack and the dampening action of a hydraulic system.
The key components of the shock sub, as depicted in the diagram, are:
- Drive Mandrel: The uppermost component, likely connecting to the drill string above.
- Packing Gland & Packing Sub: These components likely create a seal to contain internal fluids or prevent contaminants from entering.
- Drive Keys & Drive Housing: These parts are responsible for transmitting torque from the upper section to the lower internal components while allowing axial movement.
- Spring Anvil: A component against which the spring force is applied or transmitted.
- Stabilizer Bushing: Multiple instances of this component suggest it provides radial support and guides the movement of internal parts, reducing wear and maintaining alignment.
- Spring Mandrel: A central rod or shaft within the spring assembly.
- Spring Housing: Encloses and protects the spring mechanism.
- Belleville Spring Stack: A series of disc springs arranged to provide a specific spring rate and high load capacity, crucial for shock absorption.
- Bearing Sub: Likely contains bearings to facilitate relative rotation or axial movement between components.
- Piston Mandrel: A rod connected to a piston, part of a hydraulic dampening system.
- Piston Vibration Damper: This component, along with the hydraulic cylinder, forms a hydraulic damping system to absorb kinetic energy and smooth out impacts.
- Floating Gland: A sealing component that can move axially, likely to accommodate the movement of internal parts.
- Hydraulic Cylinder: Contains the hydraulic fluid and works in conjunction with the piston to provide dampening.
What is Shock Sub Used for?
A Shock Sub is primarily used to mitigate the destructive effects of drilling vibrations and impacts that originate at the drill bit. By acting as a shock absorber within the drill string, it protects valuable drilling equipment and enhances overall operational efficiency.
Here are some applications of the shock subs in the following:
- Protecting Drill Bits: It significantly extends the life of drill bits by reducing excessive impact loads and preventing premature wear, especially in hard or fractured rock.
- Safeguarding Drill String Components: It shields drill pipes, collars, and other bottom hole assembly (BHA) components from fatigue, cracks, and costly damage caused by high-frequency vibrations.
- Enhancing Rig Life: The absorbed shocks prevent severe vibrations from being transmitted up to the drilling rig, reducing wear and tear on rig components like mast, drawworks, and rotary drives.
- Improving Penetration Rates: By maintaining consistent bit contact and reducing bit bounce, a shock sub can lead to smoother drilling and, in many cases, increased rates of penetration (ROP).
- Protecting Downhole Instrumentation: In directional drilling, MWD (Measurement While Drilling) and LWD (Logging While Drilling) tools are sensitive to shock and vibration; a shock sub helps to protect these expensive instruments, ensuring accurate data collection and reducing failures.
- Reducing Noise and Vibrations: It contributes to a quieter and smoother drilling environment, which can be beneficial for both equipment and personnel.
How Does Shock Sub Work?
A Shock Sub operates on the principle of absorbing and dissipating kinetic energy generated by drilling impacts before it can travel up the drill string. Internally, it typically consists of a series of heavy-duty springs, often Belleville washers, or elastomeric elements housed within a sealed chamber.
As the drill bit encounters varying rock hardness or voids, causing sudden changes in load, these internal components compress and expand, effectively cushioning the blows and dampening high-frequency vibrations. This mechanical action isolates the upper drill string and rig from the severe shock waves, converting harmful impact energy into controlled movement within the sub itself.
- Compression and Expansion: When the bit hits hard rock or experiences bounce, the axial load increases, causing the internal springs/elastomers to compress. As the load lessens, they expand.
- Energy Dissipation: This repeated compression and expansion cycle absorbs and dissipates the impact energy, preventing it from propagating further up the drill string.
- Isolation: The shock sub acts as a buffer, creating a mechanical barrier that isolates the drilling rig, drill pipe, and sensitive downhole tools from the severe vibrations originating at the bit.
- Consistent Bit Weight: By smoothing out fluctuations in weight-on-bit caused by downhole vibrations, it helps maintain a more consistent and effective drilling force.
Shock Sub Drilling Tool
The Shock Sub drilling tool is an essential component in modern drilling, designed to mitigate the harsh impacts and vibrations encountered during rock penetration. By acting as a crucial buffer within the drill string, it protects valuable equipment and enhances drilling efficiency.
Mechanical Shock Subs
Mechanical shock subs utilize a system of heavy-duty springs, often Belleville washers, to absorb axial and torsional vibrations. These springs compress and expand in response to dynamic loads, effectively cushioning the drill bit’s impact with the rock formation. This design offers robust and consistent shock absorption across a wide range of drilling conditions, providing reliable protection for the drill string and surface equipment without relying on hydraulic fluids.
Hydraulic Shock Subs
Hydraulic shock subs employ fluid-filled chambers and pistons to dampen vibrations. As the drill string experiences axial loads, the fluid is forced through small orifices, creating resistance that absorbs shock. This hydraulic dampening provides a smooth and controlled response to impacts, often preferred in applications requiring very precise control over weight-on-bit and where the drilling environment might benefit from fluid-based dampening.
Elastomer Shock Subs
Elastomer shock subs utilize specialized rubber or polymer compounds to absorb and dissipate drilling shocks. These resilient materials deform under load, converting impact energy into heat, thereby protecting the drill string. Elastomer designs are known for their simplicity, durability, and effectiveness in attenuating high-frequency vibrations, making them a cost-effective solution for various drilling applications.
Shock Sub Benefits
Shock subs offer a multitude of benefits that significantly enhance the efficiency, longevity, and safety of drilling operations. By integrating a shock-absorbing mechanism into the drill string, these tools mitigate the harsh realities of downhole impacts and vibrations, translating into tangible improvements across the entire drilling process.
- Offering faster drilling rates, since optimum bit weight and rotary speed may be used on the bit constantly. By dampening vibrations and maintaining consistent bit contact with the rock, shock subs allow for more stable and optimized drilling parameters, leading to increased penetration rates.
- Increasing the bit length by reducing shock loads. The reduction of severe impact loads protects the drill bit from premature wear and damage, thereby extending its operational lifespan and reducing the need for frequent bit changes.
- Cutting damage to drill collars, drill pipe, and downhole tools by reducing bouncing. Shock subs act as a buffer, preventing excessive bouncing and jarring that can lead to fatigue, cracking, and failure in expensive drill string components.
- Reduced connection damage, because the elastomeric element absorbs both torsional and axial loads, so that connections are not at risk if the bit stalls. The ability of some shock subs to absorb both rotational and longitudinal stresses protects threaded connections from stripping or loosening, especially during unexpected bit stalls.
- Reduced damage to surface equipment, including swivels, blocks, and wirelines. By preventing vibrations from propagating up the drill string to the rig, shock subs safeguard critical surface equipment from premature wear and mechanical stress, lowering maintenance costs and increasing equipment longevity.
How to Choose the Best Shock Subs
Choosing the best shock sub for your drilling operation requires careful consideration of several factors to ensure optimal performance and protection. The ideal selection will depend heavily on the specific drilling conditions, the type of formation being drilled, and the overall goals for efficiency and equipment longevity.
A well-chosen shock sub can significantly reduce operational costs and enhance drilling productivity by mitigating harmful vibrations and extending the lifespan of your valuable drilling tools.
- Drilling Application: Consider whether you are performing top-hammer, DTH, rotary, or directional drilling, as different methods generate varying types and magnitudes of shock.
- Formation Type: Evaluate the geological conditions, including rock hardness, abrasiveness, and presence of fractured zones, as these directly influence the severity of impacts.
- Drill Rig and Equipment: Match the shock sub’s specifications (e.g., connection threads, OD, weight capacity) with your existing drill rig and drill string components for seamless integration.
- Desired Performance: Determine your priorities, whether it’s maximizing penetration rate, extending drill bit life, protecting sensitive downhole tools, or reducing wear on the rig.
- Maintenance and Durability: Assess the shock sub’s design for ease of maintenance and its construction materials for resistance to wear and fatigue in your specific drilling environment.
Conclusion
In conclusion, the Shock Sub is an indispensable tool for enhancing drilling efficiency and prolonging equipment life. By effectively absorbing detrimental shock and vibration, it safeguards your drill string, bits, and rig, ensuring smoother operations and significant cost savings over time.
Investing in quality shock subs directly translates to increased penetration rates and reduced downtime. Their ability to protect against the harsh realities of drilling makes them a smart addition to any professional drilling setup, from mining to construction.
For reliable and high-performance shock sub drilling tools, look no further than Sinodrills. As a trusted provider, we offer wholesale solutions designed to meet your project’s demands and optimize your drilling operations.