Thermal drilling, also known as friction drilling or flow drilling, is a revolutionary chipless hole-making process that’s transforming how we create strong, robust connections in various materials, particularly thin-walled components. Unlike conventional drilling that removes material as chips, thermal drilling leverages heat generated by friction to displace and form it.
This innovative technique offers significant advantages, including the creation of integral bushings for enhanced thread strength and the elimination of swarf. In this blog, we’ll delve into the mechanics of thermal drilling, exploring its benefits, applications, and why it’s becoming an indispensable tool in modern manufacturing.
What is Thermal Drilling?
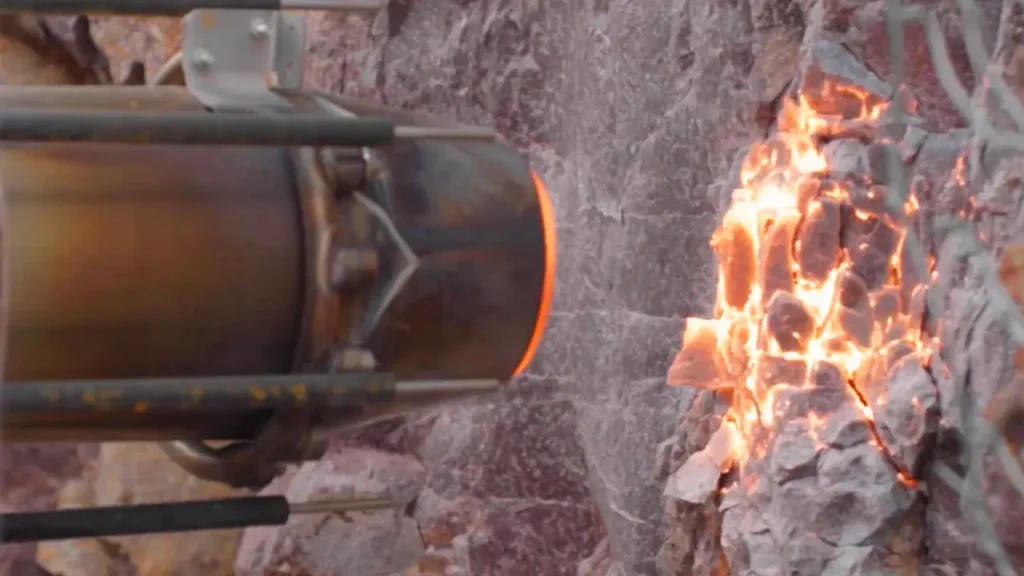
Thermal drilling, also known as friction drilling, flow drilling, or form drilling, is a unique chipless hole-making process that leverages friction-generated heat to create holes in metal, particularly thin-walled materials.
Instead of cutting and removing material as chips, a conical tool rotating at high speed and under pressure generates intense friction, rapidly heating and softening the workpiece material.
This plasticized material is then displaced by the tool to form an integral bushing around the hole, providing a robust, strong, and often threadable connection, which is ideal for applications where traditional drilling might result in weak or insufficient thread engagement.
How Does Thermal Drilling Work?
Thermal drilling operates on the principle of generating intense frictional heat to modify material, rather than removing it. A specialized conical tool, typically made of a highly heat-resistant material like cemented carbide, is pressed against the workpiece (usually thin sheet metal or tubing) while rotating at very high speeds.
This combination of rotational friction and axial pressure rapidly heats the contact area, causing the metal to become plastic and pliable.
Here’s how it works in steps:
- Friction and Heat Generation: The conical tool, spinning at high RPM, makes contact with the workpiece. The immense friction instantly generates localized heat, rapidly raising the material’s temperature above its recrystallization point, making it soft and ductile.
- Material Displacement and Forming: As the tool penetrates, it displaces the softened material. Instead of creating chips, this material flows upwards and downwards to form a robust, integrated bushing around the newly created hole.
- Bush Creation: The displaced material consolidates into a strong, seamless collar or “bushing” that extends from the original material thickness, typically up to three times its initial depth. This bushing provides a significantly increased surface area for subsequent threading.
- Finishing (Optional): Some thermal drilling tools include a cutting edge to remove the “collar” if a flush finish is desired. The resulting bushing is then typically tapped to create a strong internal thread, suitable for screws or other fasteners.
Thermal Drilling Process
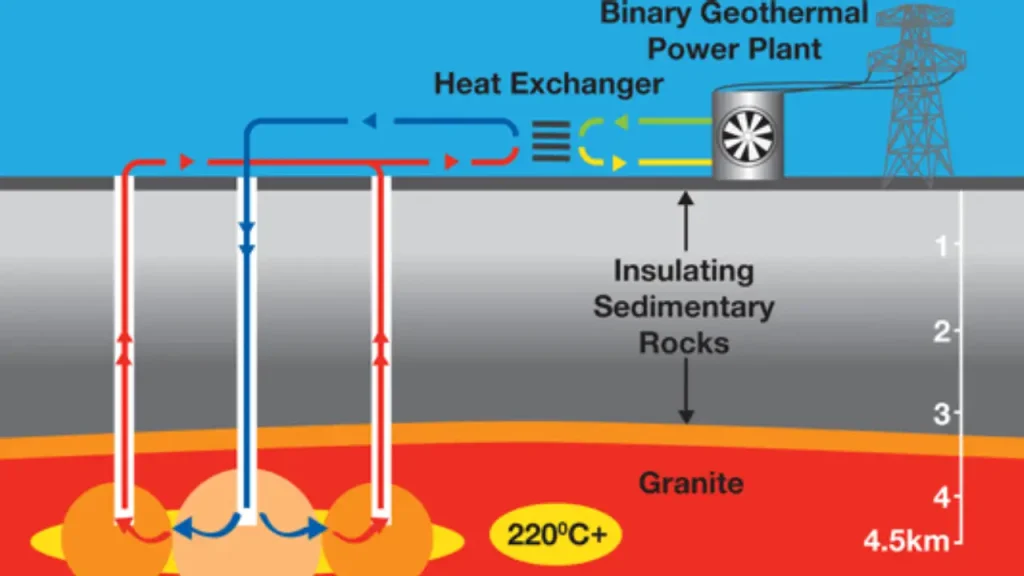
Thermal drilling in the field of well drilling, particularly for geothermal applications, refers to specialized techniques that harness heat to facilitate borehole creation, differing significantly from mechanical friction drilling for sheet metal. It’s about optimizing rock penetration using thermal principles.
Step 1: Initial Borehole Creation (Traditional or Advanced)
The process typically begins with the conventional mechanical drilling of an initial pilot hole using standard drill bits. This establishes the well path and allows for the introduction of subsequent thermal drilling tools or techniques. The aim is to create a starting point for the more advanced thermal methods.
Depending on the geological formation, this initial phase might employ rotary drilling, DTH (Down-The-Hole) hammering, or even specialized percussive methods. The integrity of this initial bore is crucial as it guides the subsequent thermal drilling operations, ensuring accuracy and efficiency in reaching target depths for geothermal resources.
Step 2: Thermal Fragmentation/Melting of Rock
Once the pilot hole is established, thermal energy is introduced to fragment or melt the rock. This can involve high-temperature jets (e.g., plasma torches, flame jets) that induce thermal stresses, causing brittle rocks to spall and fracture, or even melt less refractory formations.
The extreme heat significantly weakens the rock structure, making it easier to remove. This thermal effect reduces the mechanical energy required for drilling, potentially increasing penetration rates in hard or abrasive formations. The goal is to efficiently break down the rock face for continuous advancement.
Step 3: Material Removal and Wellbore Development
As the rock is thermally fragmented or melted, the loosened material (spalled fragments or re-solidified melt) must be continuously removed from the wellbore. This is typically achieved through traditional flushing methods, using drilling fluids or compressed air to carry cuttings to the surface.
Effective material removal is paramount to prevent re-drilling of cuttings and maintain a clear wellbore for continuous drilling operations. The combination of thermal rock alteration and efficient material transport allows for the progressive deepening of the well, crucial for geothermal energy extraction.
Key Aspects of Thermal Drilling
Thermal drilling is a fascinating process that diverges significantly from conventional methods, offering unique advantages. Its core principle revolves around using heat, generated either through friction or direct thermal energy, to manipulate material for hole creation.
Precision Heat Application
A key aspect of thermal drilling is the precise control over heat generation and application. In friction drilling, this means managing rotational speed and axial pressure to create localized heat, softening only the material directly in the tool’s path. This minimizes thermal distortion in the surrounding workpiece, preserving its structural integrity and preventing unwanted material changes.
Material Displacement vs. Removal
Unlike traditional drilling that generates chips by cutting material, thermal drilling primarily focuses on material displacement. The heated and plasticized material is flowed and formed into an integral bushing around the hole. This fundamental difference means no material is wasted as swarf, leading to a cleaner process and maximizing the utilization of the workpiece material itself.
Enhanced Joint Strength
The creation of an integrated bushing is a crucial aspect. This thickened collar provides a significantly increased surface area for subsequent threading or fastening. This results in much stronger and more durable connections, especially in thin-walled materials where conventional tapping directly into the material’s original thickness would yield weak and unreliable threads.
Versatility in Application
Thermal drilling encompasses various techniques, from friction-based methods for sheet metal to high-temperature jets for hard rock well drilling. This versatility allows the application of thermal principles to a wide range of materials and drilling challenges, demonstrating its adaptability across different industries and engineering requirements.
Thermal Drilling Tools
Thermal drilling tools, often referred to as friction drill bits, flow drills, or form drills, are specialized instruments designed for the unique chipless hole-making process known as thermal drilling. Unlike conventional drill bits that have cutting edges to remove material, these tools feature a conical or cylindrical shape that generates intense friction when rotated at high speeds and pressed against a workpiece.
This friction rapidly heats the material, making it malleable, allowing the tool to displace and form it into a robust, integrated bushing around the created hole, rather than producing metal chips.
- Conical/Cylindrical Shape: Designed to generate maximum friction and effectively displace material.
- High-Strength Material: Typically made from wear and heat-resistant materials like solid cemented carbide to withstand extreme temperatures and pressures.
- Variety of Finishes: Available in “standard” types that create a raised collar/bushing, or “flat” types that include a cutting edge to remove the collar for a flush finish.
- No Cutting Edges (Primary Function): Their primary function is to deform and displace material, not to cut or shear it.
- Heat Dissipation Features: Some tools or their holders incorporate features to help dissipate the immense heat generated during repetitive operations.
What is Geothermal Drilling Used For?
Geothermal drilling is a specialized process that involves drilling into the Earth’s crust to access and harness its natural heat, which originates from the planet’s core. This heat is a vast, renewable energy source used for a variety of applications, primarily for generating electricity and for efficient heating and cooling of buildings.
The drilling depths can range from shallow wells for residential heat pumps to very deep wells (several kilometers) for large-scale power generation, depending on the specific geothermal resource being targeted.
Common applications of geothermal drilling include:
- Electricity Generation: Drilling deep wells to extract hot water and steam from underground reservoirs, which then drives turbines to produce electricity.
- Heating and Cooling Systems (Geothermal Heat Pumps): Creating boreholes to install ground loops that exchange heat with the stable underground temperatures, providing efficient and environmentally friendly heating and cooling for homes and commercial buildings.
- Direct Use Applications: Tapping into hot water reservoirs for direct heating purposes in homes, greenhouses, aquaculture, and various industrial processes.
- Enhanced Geothermal Systems (EGS): Drilling and stimulating hot, dry rock formations by injecting water to create fractured reservoirs, where naturally occurring geothermal activity is not sufficient for power generation.
- District Heating and Cooling: Utilizing a central geothermal system to provide heating and cooling for entire communities or large complexes of buildings.
Conclusion
Thermal drilling stands as a testament to innovative engineering, offering a unique solution for creating strong, chipless holes and integral bushings. Its ability to work with thin materials and produce robust, threadable openings makes it invaluable across diverse industries, from automotive to construction.
Embracing thermal drilling means enhanced structural integrity and reduced material waste, paving the way for more efficient and sustainable manufacturing processes. This technology not only simplifies assembly but also elevates the overall quality and durability of your end products.
For your well and rock drilling needs, remember Sinodrills. Located in Qingdao, Shandong, China, we offer a comprehensive range of wholesale thermal drilling tools designed for superior performance and reliability, ensuring your projects achieve optimal results.