Custom Top Hammer Drill Bits Manufacturer in China
We offer a comprehensive range of Top Hammer drill bits, engineered for durability and performance in various rock conditions. Our selection includes button bits, cross bits, and chisel bits, designed to maximize penetration rates and tool life. Manufactured with robust materials and precise heat treatment, these bits ensure efficient rock breaking and reliable operation for your drilling projects.
Sinodrills - Your Trusted Top Hammer Drill Bits Manufacturer from China
Sinodrills, a reputable manufacturer from China, provides a comprehensive selection of Top Hammer drill bits. Leveraging advanced production techniques, premium alloy steel, and precise heat treatment, their bits deliver superior strength and extended service life. Sinodrills’ offerings, including button, cross, and chisel bits, are engineered for optimal penetration and reliability across diverse rock formations in mining, quarrying, and construction applications globally.
Various Top Hammer Drill Bits
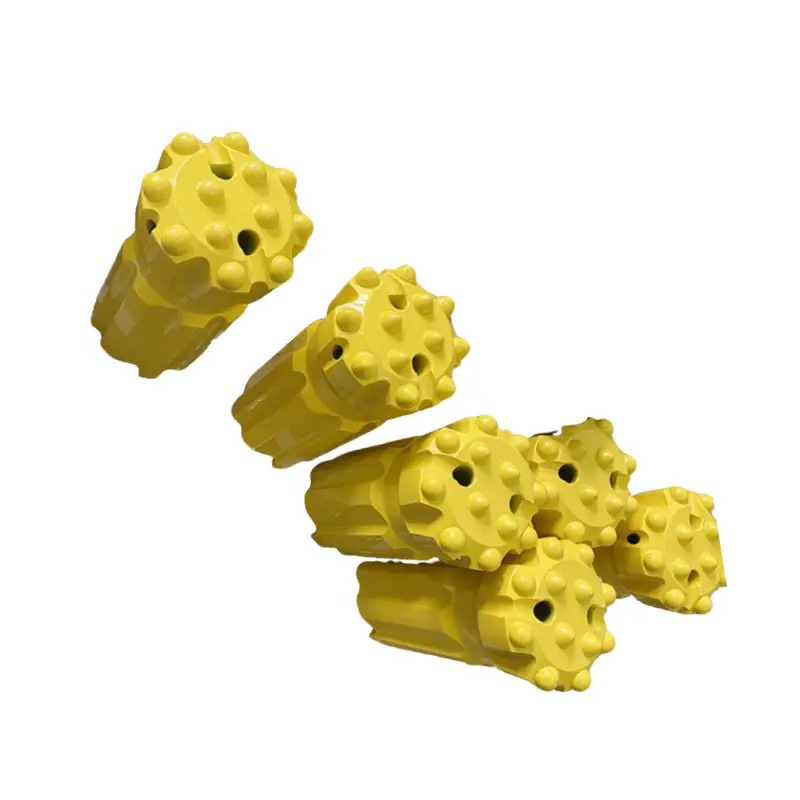
top hammer drill bits wholesale
We offer top hammer drill bits for wholesale, providing a diverse selection designed for various rock formations. Our inventory includes button bits, cross bits, and chisel bits, all crafted for superior penetration and extended operational life. Sourced from robust materials, these bits ensure reliable performance and cost-effectiveness for your large-scale drilling projects.
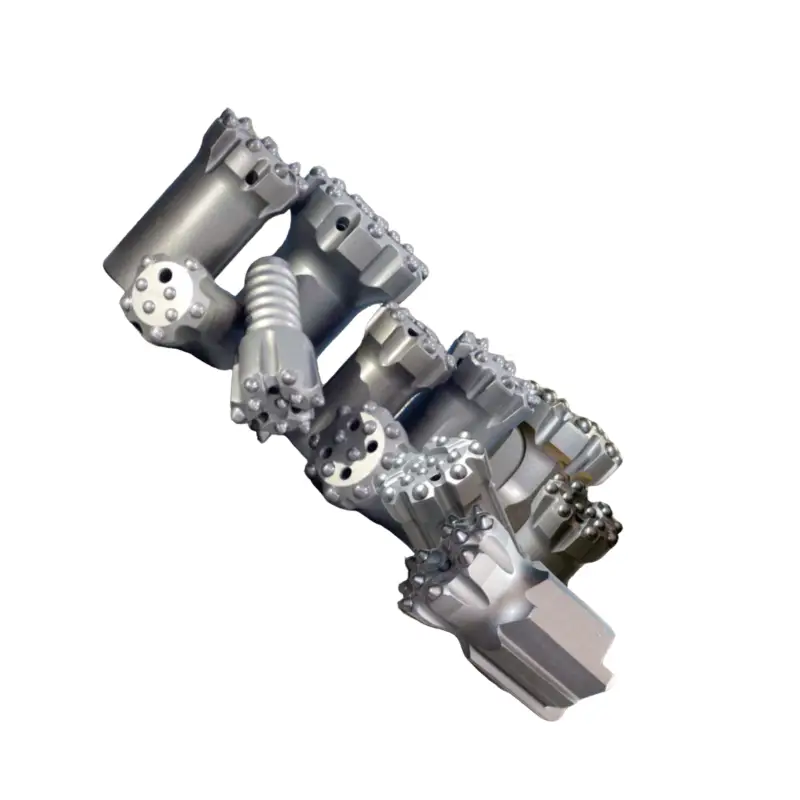
top hammer drilling bits
We offer a wide selection of top hammer drilling bits, meticulously engineered for durability and peak performance across diverse rock formations. Our range includes robust button bits, cross bits, and chisel bits, all crafted to optimize penetration rates and extend service life. Utilizing premium materials and advanced manufacturing processes, these bits deliver efficient rock breaking and reliable operation for all your drilling needs.
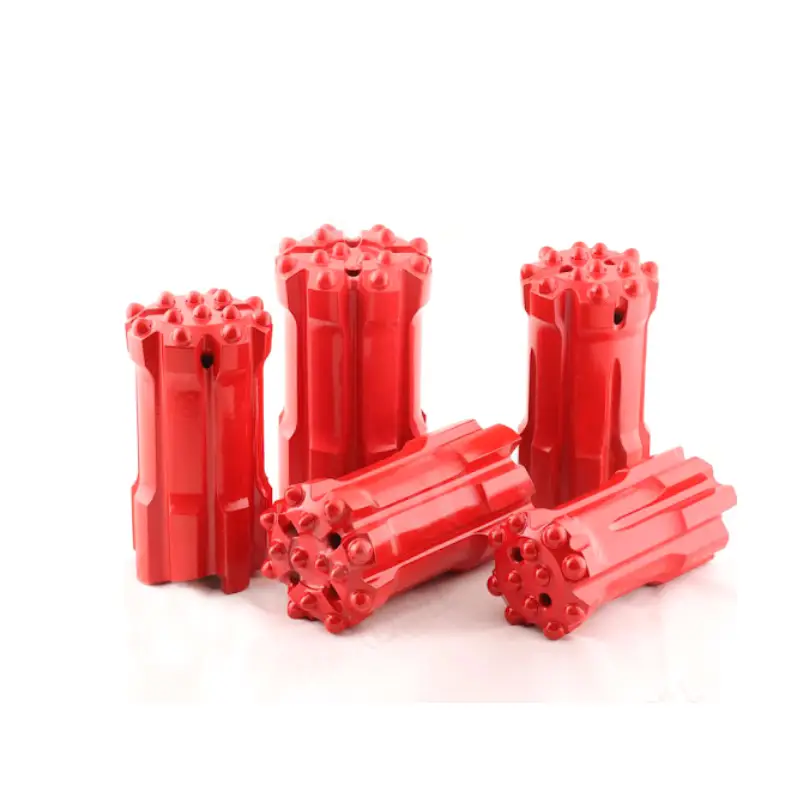
wholesale custom top hammer drill bits
We offer wholesale custom Top Hammer drill bits, precisely engineered to meet your specific drilling demands. Tailored for optimal performance in diverse rock formations, our bits feature specialized designs, carbide grades, and configurations. Partner with us for bespoke solutions that enhance penetration rates, extend tool life, and significantly reduce operational costs for your projects.
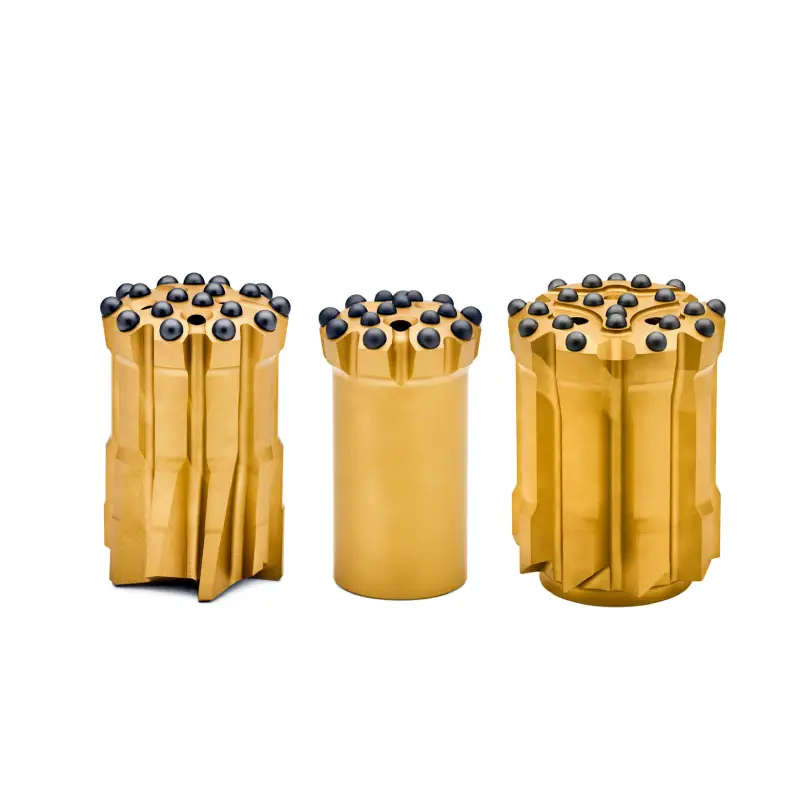
top hammer threaded bits
We offer wide selection of top hammer threaded bits, engineered for superior performance and longevity. Our range includes various thread types and button configurations to suit diverse rock formations and drilling applications. Crafted from premium alloy steel with advanced heat treatment, these bits ensure excellent penetration, reduced wear, and reliable operation in challenging drilling environments.
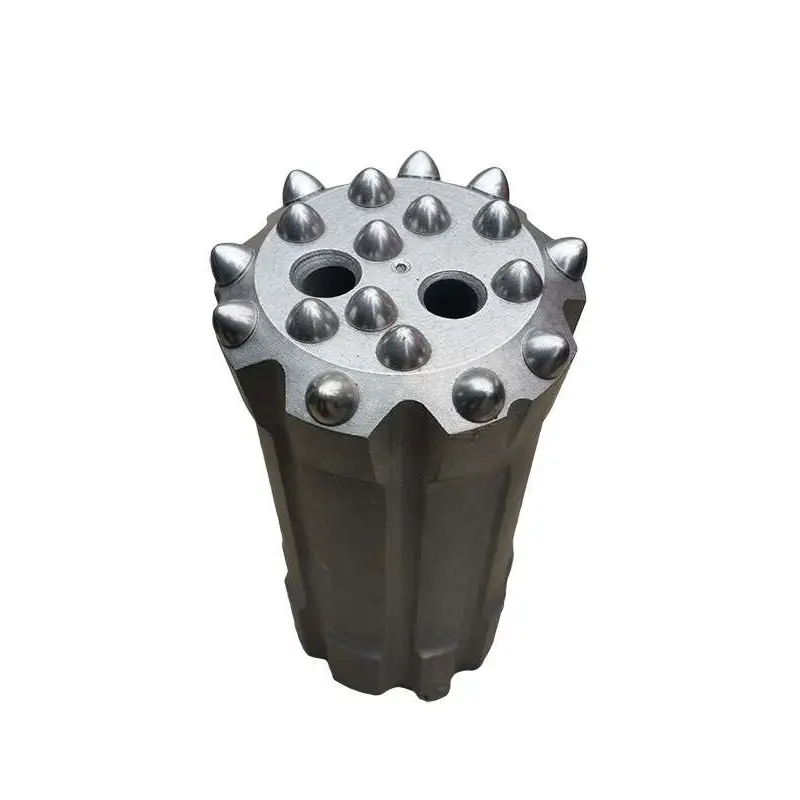
top hammer button bits
We offer a wide selection of top hammer button bits, engineered for superior performance and extended lifespan. Featuring premium carbide inserts and robust body designs, our bits provide excellent penetration rates and efficient rock fragmentation. Ideal for various rock formations, they ensure consistent drilling productivity and reduced operational costs for your top hammer drilling applications.
Customize Your Desired Top Hammer Drill Bits
Button Shape and Configuration
Customizing the button shape and configuration directly impacts drilling performance and bit life in specific rock types. Options include spherical for universal use, ballistic for faster penetration in softer rock, and parabolic for durability in abrasive conditions. Tailoring the button layout optimizes energy transfer and maximizes rock fragmentation efficiency for your specific ground.
Skirt Design and Gauge Buttons
The choice between R-thread and T-thread profiles impacts the anchor’s bonding characteristics and load transfer efficiency. R-threads provide continuous engagement, suitable for various soils, while T-threads offer a deeper, more robust profile for higher load capacities and enhanced grout bond in challenging ground.
Carbide Grade and Insert Quality
The choice of carbide grade and insert quality directly influences the bit’s wear resistance and toughness. Customization involves selecting specific tungsten carbide compositions tailored for the rock’s abrasiveness and hardness. Superior carbide grades ensure prolonged bit life, consistent penetration rates, and reduced downtime, especially in challenging drilling environments.
Face Design and Flushing Holes
The drill bit’s face design and the number/placement of flushing holes are critical for efficient cuttings removal and preventing regrinding. Customizing the face (e.g., flat, drop-center, convex) optimizes contact with the rock. Optimized flushing holes ensure rapid removal of cuttings, preventing blockages and maintaining a clean drilling face for maximum penetration.
what are top hammer drill bits?
Top hammer drill bits are cutting tools specifically designed for use with top hammer drilling rigs, where the percussive mechanism is located on the surface. These top hammer bits are threaded onto the end of drill rods and receive their impact energy indirectly from the surface hammer.
They are characterized by their robust construction, often featuring carbide inserts (buttons) on the face, and are engineered to efficiently break rock through a combination of percussive impact and rotation.
Top hammer bits come in various designs, including button bits, cross bits, and chisel bits, each optimized for different rock formations and drilling conditions.
What is top hammer drilling method?
Top hammer drilling is a percussive drilling method where the hammer mechanism is located at the top of the drill string, on the surface drill rig.
The impact energy generated by this surface-mounted hammer is transmitted down through the drill rods, via their threaded connections, to the drill bit at the bottom of the hole.
This method combines both rotation and percussion to break rock and is commonly used for smaller diameter holes in a wide range of applications, including construction, quarrying, and road building, where its versatility and mobility are advantageous.
what are top hammer drill bits used for?
Top hammer drill bits are essential tools used across a variety of surface drilling applications, leveraging their design to efficiently break rock through indirect percussive energy. Their versatility makes them suitable for projects where the drill rig’s mobility and adaptability to diverse rock types are crucial. Key uses include:
- Construction: Widely employed in general construction for drilling blast holes, trenching, and site preparation, especially where smaller diameter holes are required.
- Quarrying: Used for bench drilling in aggregate quarries and dimension stone operations to fragment rock for crushing or extraction.
- Road Construction: Integral for rock excavation in road building projects, creating stable foundations and cuttings through challenging terrain.
- Tunneling and Underground Development: While DTH is common, top hammer drills are used for face drilling in smaller tunnels and for bolting applications.
- Anchoring and Bolting: Utilized for drilling holes for rock bolts and various anchoring systems in civil engineering and mining.
top hammer vs DTH drilling
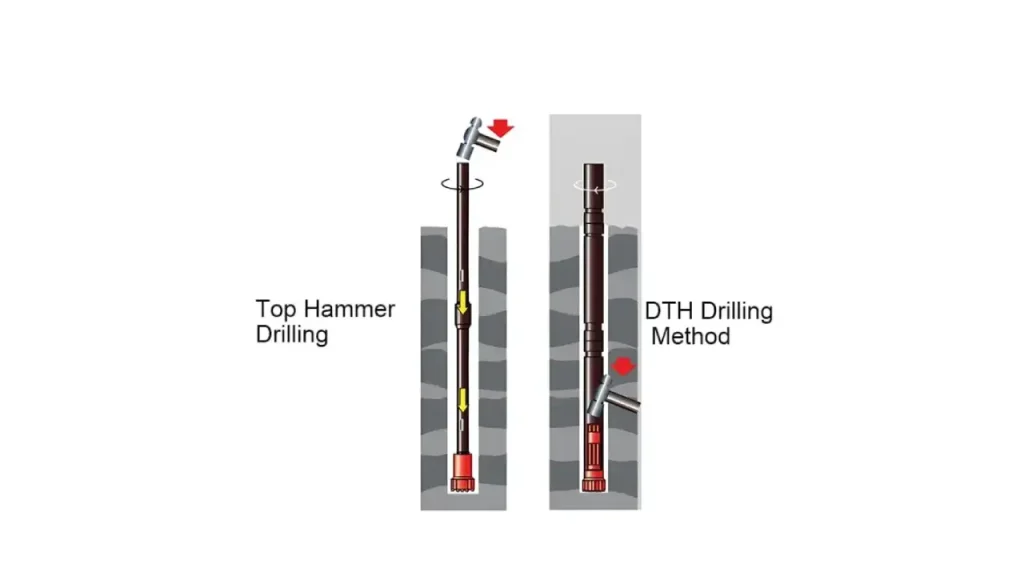
Understanding the fundamental operational differences between DTH (Down-The-Hole) and Top Hammer drilling methods is crucial for optimizing project efficiency. This comparison delves into their distinct mechanics, suitability for various conditions, and overall performance characteristics, guiding optimal equipment selection.
Energy Transfer Mechanism
In DTH drilling, the percussive hammer is located directly at the bottom of the borehole, striking the drill bit from within. Compressed air powers a piston inside the hammer, transmitting energy directly to the rock. This direct impact minimizes energy loss as depth increases, ensuring consistent power for efficient rock breaking.
Conversely, Top Hammer drilling involves a percussive unit mounted on the drill rig at the surface. Impact energy is transmitted down the drill string through a series of threaded drill rods to the bit. This indirect energy transfer means power can diminish with increasing drill string length, affecting efficiency in deeper holes.
Hole Straightness
DTH hammers are renowned for their ability to produce exceptionally straight holes, even in challenging and variable rock formations. The hammer’s position at the bottom of the hole acts as a natural stabilizer, guiding the bit and minimizing deviation. This precision is critical for applications requiring strict borehole alignment, such as foundation work.
Top Hammer drilling, due to the energy being transmitted through flexible rods, can sometimes result in more hole deviation, particularly in fractured ground or over longer drilling lengths. While skilled operators can mitigate this, maintaining perfect straightness can be more challenging compared to the inherent stability offered by DTH.
Depth Capability
DTH drilling is the preferred method for deep holes, often exceeding hundreds of meters. The direct impact mechanism ensures that the effectiveness of the percussive action is maintained regardless of the depth. This makes DTH highly efficient for large-scale mining, deep water wells, and extensive geotechnical investigations.
Top Hammer drilling is generally more suitable for shallower holes, typically up to 20-30 meters, though this can vary. As depth increases, the energy loss through the longer drill string becomes more pronounced, leading to reduced penetration rates and efficiency. Its strength lies in quick setups for less demanding depths.
Bit Wear and Longevity
DTH drilling generally results in longer drill bit life, especially in very hard and abrasive rock. The efficient flushing system, coupled with the direct and consistent impact, reduces the risk of regrinding cuttings. This minimizes wear on carbide inserts, leading to extended service intervals and lower consumable costs.
Top Hammer drilling can, in some conditions, lead to faster drill bit wear. The indirect energy transfer may cause more erratic bit movement and increased stress on the cutting elements. Less efficient removal of cuttings in certain applications can also contribute to abrasive wear, necessitating more frequent bit changes.
Noise and Vibration
DTH hammers typically produce lower noise levels at the surface. Since the primary percussive action occurs deep within the borehole, much of the sound is absorbed and muffled by the surrounding rock and overburden. This makes DTH a more environmentally friendly option for noise-sensitive areas or urban projects.
Top Hammer drills tend to generate higher noise and vibration levels at the surface. The exposed percussive mechanism on the rig produces significant sound that propagates easily. This often requires stringent noise control measures, potentially impacting operational hours or requiring additional sound dampening equipment in populated zones.
Application Focus
DTH drilling excels in applications requiring high penetration rates in very hard, competent rock, and where large-diameter, straight holes are critical. Its primary focus is on maximizing drilling efficiency and achieving precise boreholes in challenging geological conditions, making it ideal for deep mining and large construction.
Top Hammer drilling offers greater versatility for projects with varied rock conditions, smaller hole diameters, and frequent moves between drilling spots. It’s often chosen for surface applications like general construction, road building, and quarrying, where rapid setup, mobility, and adaptability to changing ground are key priorities.
Send Your Inquiry Now
All-in-one Top Hammer Drill Bits Solutions for Your Project
Sinodrills provides all-in-one Top Hammer drill bit solutions for diverse projects. Our comprehensive range includes optimized button bits, cross bits, and chisel bits, engineered from premium carbide for superior wear resistance. These solutions ensure maximum penetration rates, extended service life, and consistent performance across various rock formations, streamlining your drilling operations.