In the demanding world of rock drilling, the integrity of your drill string is paramount. Every component plays a crucial role in transmitting power from the drill rig to the bit, and few are as critical as the rod coupling sleeve. These unsung heroes ensure a continuous and efficient drilling process, directly impacting productivity and safety.
This blog post will delve into the essential types of rod coupling sleeves: the robust full-bridge, semi-bridge, and the adaptable crossover. Understanding the distinct advantages and applications of each will help you select the ideal coupling for your specific drilling needs, ensuring optimal performance for your project.
What is Coupling Sleeve in Drilling?
In drilling, a coupling sleeve is a robust, cylindrical component with internal threads, essential for connecting various parts of a drill string. Its primary function is to securely join drill rods to each other, or to link a drill rod to a shank adapter, which connects to the drill rig.
This vital connection ensures the efficient transmission of both rotational torque and percussive impact energy from the drilling machine to the drill bit, enabling effective rock penetration in applications like mining, tunneling, and construction.
Types of Rod Coupling Sleeve
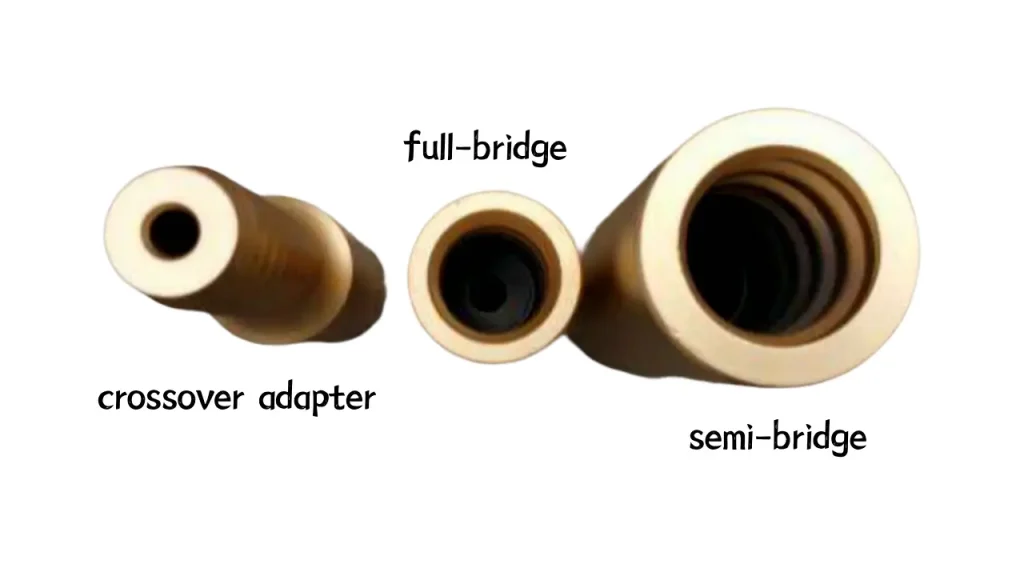
Coupling sleeves are vital for creating a continuous drill string, transmitting power from the rig to the bit. They come in distinct types, each suited for different drilling requirements and conditions, ensuring optimal performance and efficiency.
Full-Bridge Coupling Sleeve
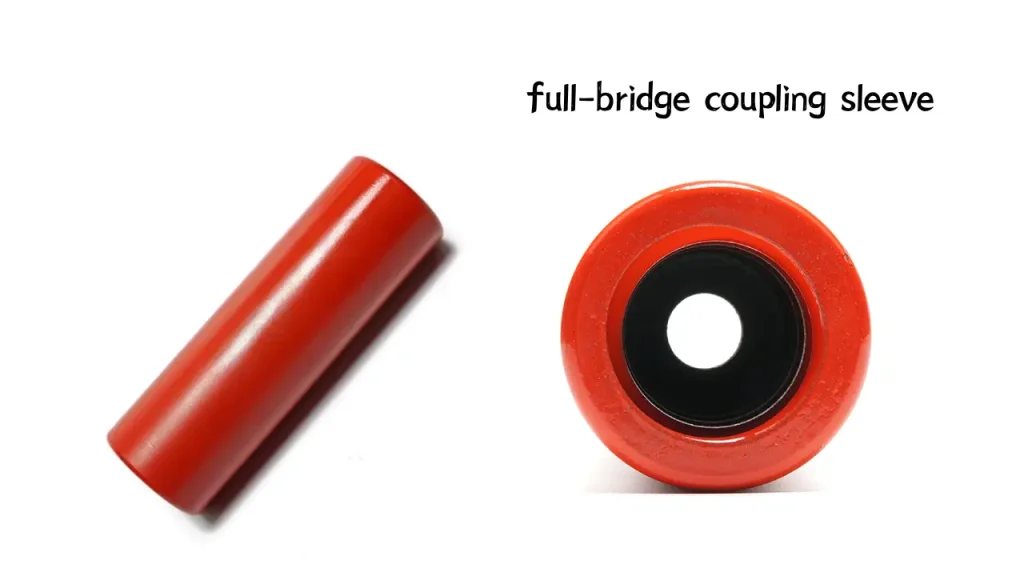
Full-bridge coupling sleeves are characterized by continuous threading along their entire internal length. This design ensures that the drill rod ends butt up against each other within the coupling, creating a very strong and rigid connection. This full thread engagement minimizes the risk of uncoupling under high torque or impact, making them ideal for demanding drilling environments.
These threaded coupling sleeves for drilling are particularly well-suited for percussive drilling in hard rock formations where maximum energy transfer and connection stability are paramount. Their robust construction provides excellent resistance to vibration and premature wear, contributing to a longer lifespan for the drill string components. They are often favored in surface mining and large-scale construction projects due to their reliability and durability.
Semi-Bridge Coupling Sleeve
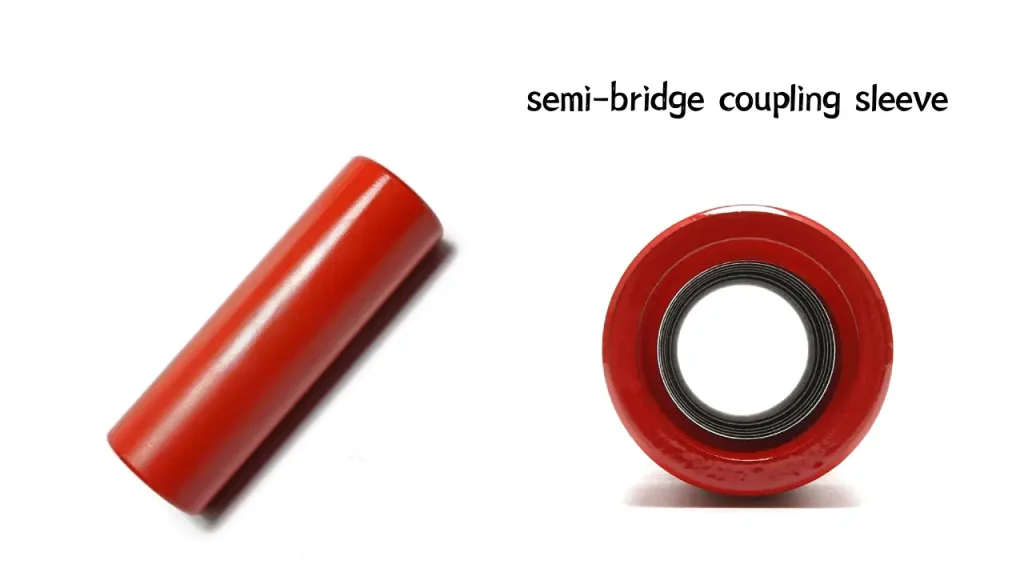
Semi-bridge coupling sleeves, also known as standard couplings, feature threads at both ends with a central, unthreaded section in the middle. The drill rod ends meet and butt against each other within this unthreaded portion. This design allows for easier make-up and break-out of the drill string, which can be advantageous in operations requiring frequent rod changes.
While still providing a strong and secure connection, the semi-bridge design offers a good balance between strength and operational convenience. They are widely used in various drilling applications, including underground mining, tunneling, and civil engineering, where their ease of use can significantly improve efficiency. The “bridge” prevents the rods from over-screwing, ensuring consistent performance.
Crossover Adapter Coupling Sleeve
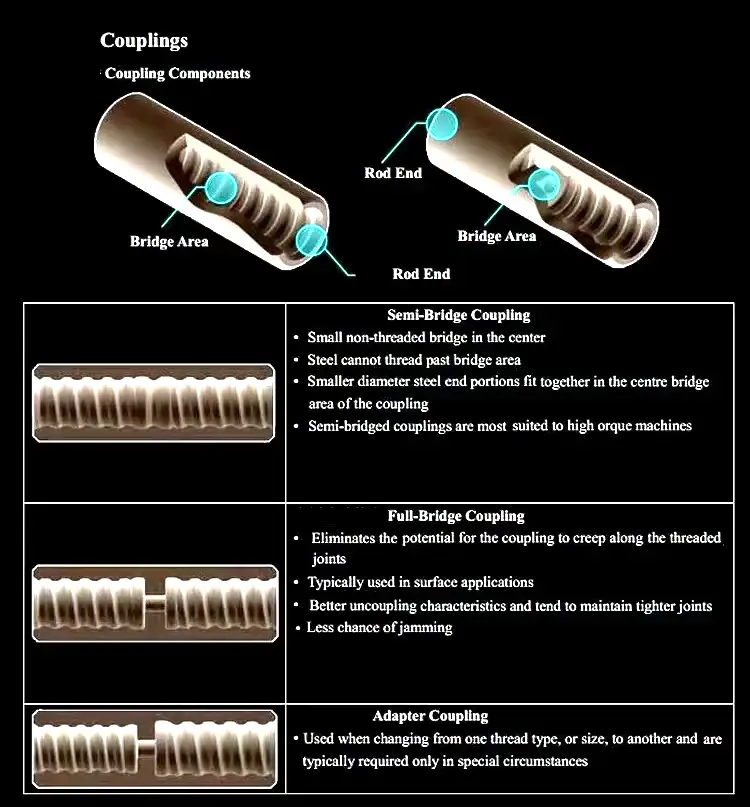
Crossover adapters are specialized coupling sleeves designed to connect drill rods or other drilling components that have different thread types or diameters.
For instance, they can be used to join a drill rod with an R-series thread to one with a T-series thread, or to adapt between different rod sizes. They are essentially a transitional piece that allows for flexibility within a drill string system.
These adapters are invaluable in situations where a drilling operation utilizes a mix of equipment or when transitioning between different drilling phases requiring varied rod specifications. They eliminate the need for entirely new drill strings, saving costs and increasing versatility on the job site. Crossover adapters ensure seamless compatibility and maintain the integrity of the drill string despite differing component specifications.
Here are the differences of coupling sleeve types:
Aspect | Full-Bridge Coupling Sleeve | Semi-Bridge Coupling Sleeve | Crossover Adapter |
Internal Threading | Continuous threads along entire length | Threads at both ends with central unthreaded section | Different thread types/diameters on each end |
Connection Strength | Maximum strength and rigidity, full thread engagement | Good strength, rods butt in unthreaded section | Designed to bridge incompatible threads/diameters |
Ease of Make-up/Break-out | More difficult due to full thread engagement | Easier due to unthreaded central section | Varies, designed for specific thread transitions |
Primary Application | Demanding, high-torque, percussive drilling | Versatile, general drilling, frequent rod changes | Connecting components with differing thread specifications |
Energy Transfer | Highly efficient due to solid connection | Efficient, good for various drilling conditions | Facilitates energy transfer between dissimilar components |
Full-Bridge vs Semi-Bridge Coupling Sleeve
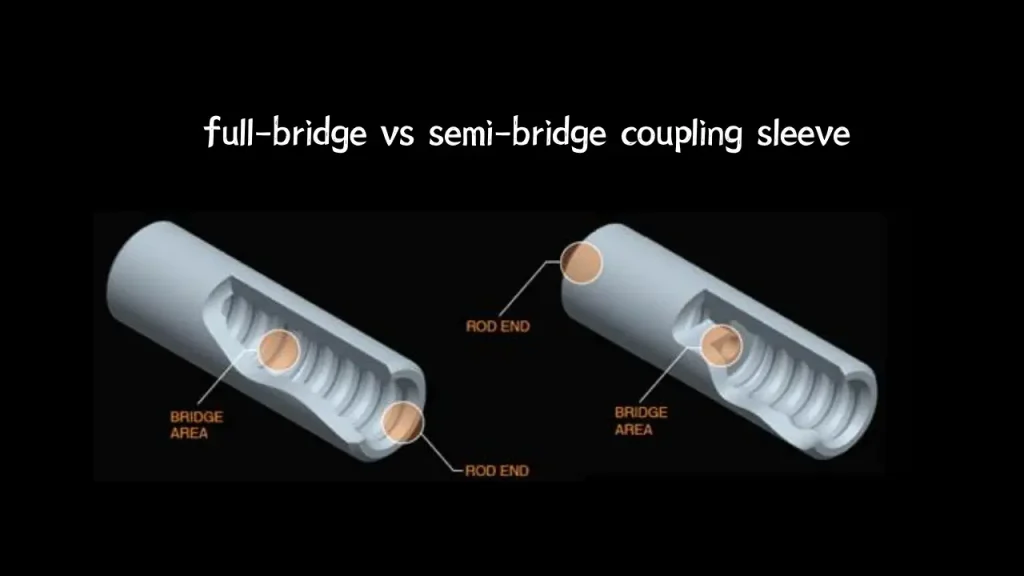
Full-bridge and semi-bridge coupling sleeves are two primary types of threaded connectors used in drilling, differing in their internal design. Understanding their distinctions is key to selecting the appropriate sleeve for optimal performance and efficiency in various drilling applications.
Full-Bridge Coupling Sleeve
Full-bridge coupling sleeves feature continuous threading throughout their entire internal length. This design allows the ends of the drill rods to be screwed deeply into the coupling until they butt against each other, creating a solid and highly rigid connection. The extensive thread engagement provides maximum strength and minimizes any potential for loosening or “creeping” along the joint, even under extreme torsional and percussive forces.
This type of sleeve is particularly well-suited for the most demanding drilling conditions, such as those encountered in hard rock formations or deep hole drilling where high thrust and torque are consistently applied. The robust connection ensures optimal energy transfer from the drill rig to the bit, enhancing drilling efficiency and reducing the risk of tool failure, making them a preferred choice for heavy-duty applications in surface mining and large construction.
Semi-Bridge Coupling Sleeve
Semi-bridge coupling sleeves, also commonly referred to as standard couplings, are designed with internal threads at both ends but include a distinct unthreaded “bridge” section in the middle. When drill rods are connected, their ends meet and butt against each other within this central unthreaded area. This design prevents the rods from being over-screwed into the coupling, maintaining a consistent and reliable connection point.
The semi-bridge design offers a balance between connection strength and operational convenience. Its structure allows for easier make-up and break-out of the drill string compared to full-bridge sleeves, which can save significant time in operations requiring frequent rod additions or removals. This makes them a versatile and widely used option across various drilling applications, including underground mining, tunneling, and general construction, where their efficiency and reliability are highly valued.
Here’s a comparison table of full-bridge and semi-bridge coupling sleeves:
Aspect | Full-Bridge Coupling Sleeve | Semi-Bridge Coupling Sleeve |
Internal Threading | Continuous threads along entire length | Threads at both ends with central unthreaded section |
Connection Point | Rod ends butt within fully threaded section | Rod ends butt in the central unthreaded “bridge” |
Connection Strength | Maximum strength and rigidity, full thread engagement | Strong and reliable, good for various conditions |
Ease of Make-up/Break-out | More difficult due to extensive thread engagement | Easier due to the central unthreaded section |
Primary Application | Heavy-duty, high-torque, hard rock drilling | Versatile, general drilling, frequent rod changes |
Risk of Loosening | Minimized due to full engagement | Reduced, but designed for specific applications |
How to Choose Full-Bridge, Semi-Bridge and Crossover Coupling Sleeves?
Choosing the correct type of coupling sleeve — full-bridge, semi-bridge, or crossover — is critical for optimizing drilling performance, ensuring safety, and extending the lifespan of your drilling tools. The decision hinges on specific project requirements, geological conditions, and the existing equipment setup.
Making an informed choice will significantly impact drilling efficiency, reduce operational costs, and prevent unnecessary downtime. Consider the demands of your drilling environment to select the most suitable coupling sleeve for a secure and productive operation.
- For Demanding Applications (Full-Bridge): Choose full-bridge coupling sleeves when facing extremely hard rock formations, high torque demands, or deep drilling projects. Their continuous threading provides maximum strength and rigidity, ensuring a highly secure connection that can withstand severe percussive and rotational stresses without compromise.
- For Versatility and Ease of Use (Semi-Bridge): Opt for semi-bridge coupling sleeves in general drilling applications where a balance of strength and operational efficiency is desired. Their unthreaded central section facilitates easier make-up and break-out of the drill string, making them ideal for projects requiring frequent rod changes or diverse geological conditions.
- For Bridging Incompatibilities (Crossover): Select crossover adapters when your drilling operation involves connecting components with different thread types or diameters. These specialized sleeves are essential for creating seamless transitions between varied drill rods or tools, providing flexibility and avoiding the need for multiple, incompatible drill string setups.
- Considering Operational Efficiency: Evaluate how frequently you anticipate adding or removing drill rods. Semi-bridge sleeves excel in situations demanding quick and easy assembly/disassembly, while full-bridge sleeves offer a more robust, but potentially slower, connection process due to their extensive thread engagement.
- Assessing Geological Conditions: The type of rock being drilled heavily influences the choice. Hard, abrasive, or fractured rock typically benefits from the superior strength and stability of full-bridge sleeves, whereas softer or less demanding formations might be well-served by the versatility of semi-bridge options.
Conclusion
Understanding the distinct advantages of full-bridge, semi-bridge, and crossover coupling sleeves is crucial for optimizing your drilling operations. Each type offers specific benefits in terms of strength, ease of use, and adaptability, directly impacting drilling efficiency and the lifespan of your equipment.
Selecting the right coupling sleeve ensures maximum energy transfer, minimizes wear and tear, and ultimately contributes to a more productive and cost-effective drilling project. This informed choice prevents downtime and enhances overall performance in diverse geological conditions.
For reliable, high-quality, and competitively priced wholesale coupling sleeves for drill rods, look no further than Sinodrills. We are committed to providing durable and precisely manufactured solutions tailored to your specific drilling needs.