Choosing the right PDC (Polycrystalline Diamond Compact) drill bit is crucial for efficient and cost-effective drilling. Two primary types dominate the market: Matrix Body and Steel Body bits. Understanding their fundamental differences is key to optimizing your drilling operations.
This blog post will delve into the distinct characteristics of Matrix Body and Steel Body PDC bits, comparing their construction, durability, performance in various formations, and typical applications. By exploring these aspects, you’ll be better equipped to select the ideal bit for your specific drilling needs.
What are Matrix Body PDC Bits?
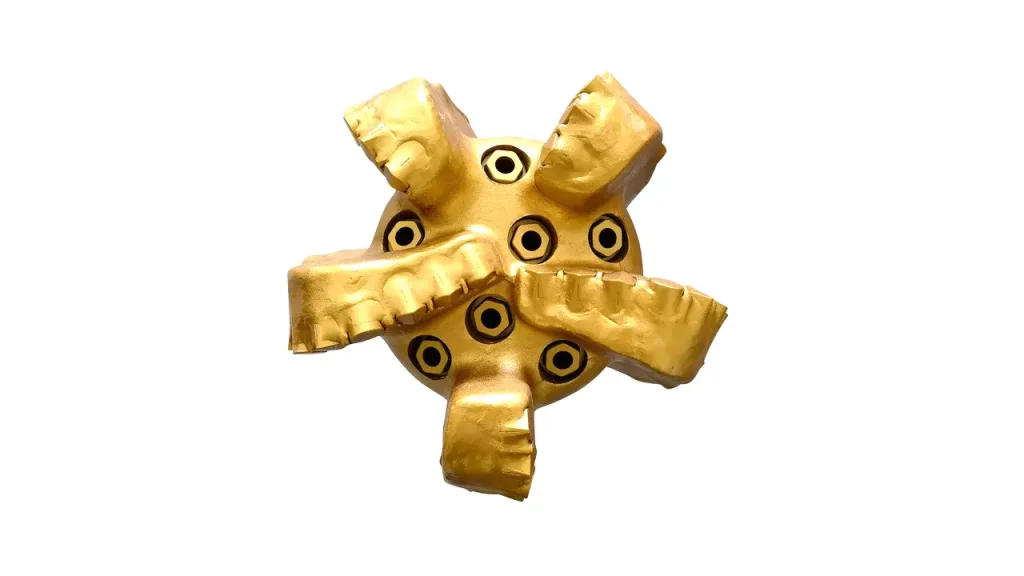
Matrix Body PDC (Polycrystalline Diamond Compact) bits are distinguished by their bit body construction, which is cast from a composite material primarily composed of tungsten carbide grains metallurgically bonded with a softer, tougher metallic binder.
This manufacturing process results in a bit body that is highly resistant to abrasion and erosion, making them ideal for drilling in challenging, abrasive formations and environments with high fluid volumes. While generally more brittle than steel body bits, their exceptional wear resistance allows for extended bit life and multiple runs in the right conditions.
What are Steel Body PDC Bits?
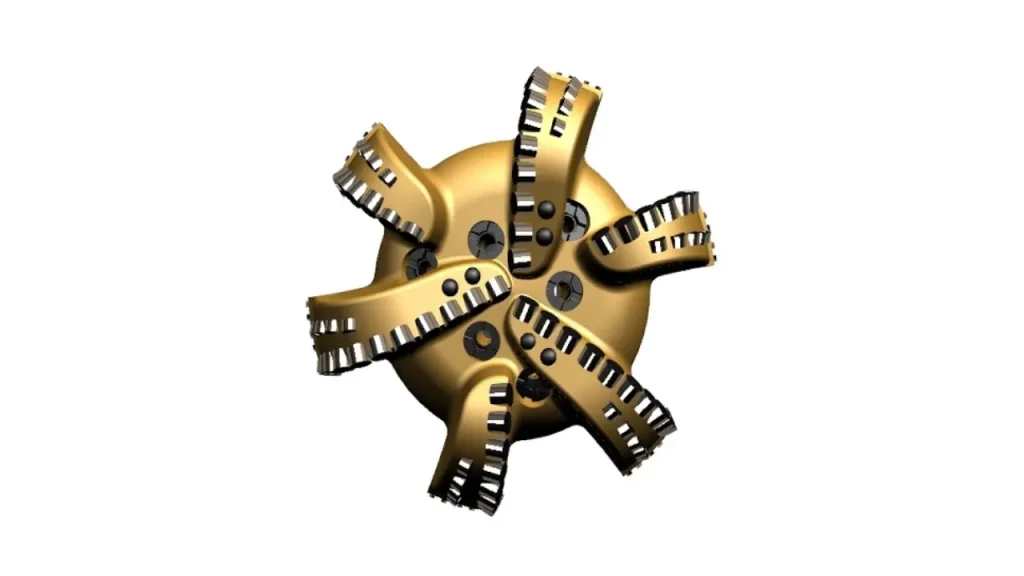
Steel Body PDC (Polycrystalline Diamond Compact) bits are crafted from high-strength alloy steel, which is machined into the desired bit profile. This construction provides excellent impact resistance and ductility, making them more resilient to sudden impacts and shock loads encountered in drilling, especially in formations with interbedded hard stringers or fractured rock.
While less resistant to abrasive wear than matrix body bits, steel body bits offer greater design flexibility, allowing for larger junk slot areas for efficient cuttings evacuation and more aggressive cutting structures. A significant advantage is their repairability, as worn or damaged cutters can often be replaced and the bit refurbished, extending its lifespan and reducing overall drilling costs.
Matrix Body PDC Bits vs Steel Body
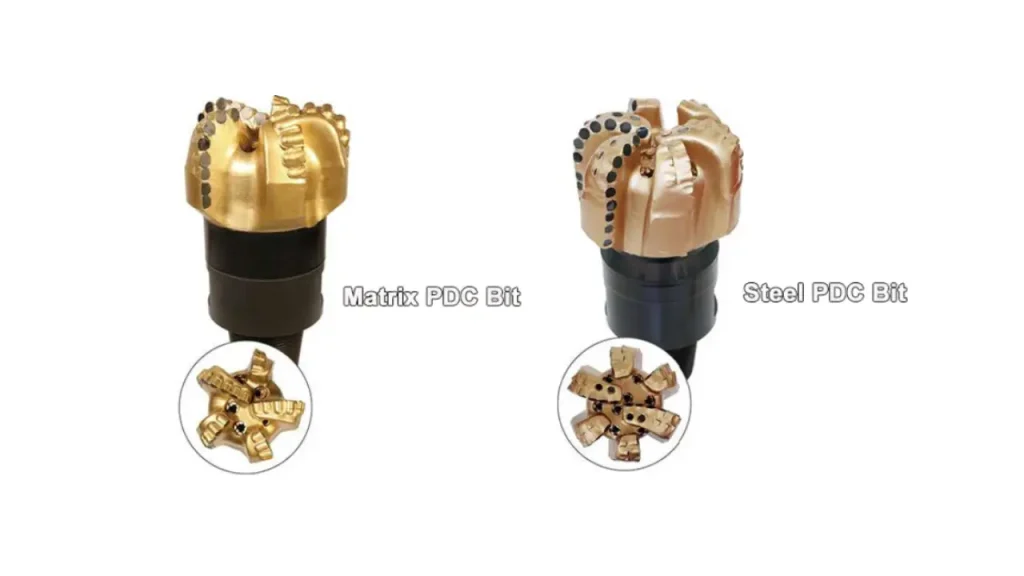
Construction Material
Matrix Body PDC bits are manufactured by sintering a composite material primarily made of tungsten carbide grains with a metallic binder. This process creates a dense, hard, and erosion-resistant body that is well-suited for demanding drilling environments.
In contrast, Steel Body PDC bits are machined from high-strength alloy steel. This material is known for its inherent ductility and toughness, allowing for a different set of performance characteristics and manufacturing advantages.
Durability and Wear Resistance
Due to their tungsten carbide composition, Matrix Body PDC bits offer superior resistance to abrasion and erosion. This makes them highly durable in abrasive rock formations and in drilling applications where high fluid volumes are used, which can otherwise quickly wear down the bit body.
While Steel Body PDC bits are inherently less resistant to abrasive wear, modern advancements in hard-facing materials and protective coatings significantly enhance their durability. These applied layers help protect the steel body from erosion and abrasion, extending the bit’s lifespan in various conditions.
Impact Resistance
Matrix Body PDC bits, being a hard and relatively brittle composite, exhibit lower impact resistance. They are more prone to damage when encountering sudden shock loads or drilling through highly fractured or interbedded formations.
Conversely, Steel Body PDC bits possess superior impact resistance and toughness. The ductile nature of steel allows them to absorb and dissipate energy from impacts more effectively, making them a more robust choice for drilling in challenging and inconsistent geological conditions.
Repairability
Repairing Matrix Body PDC bits can be challenging due to their cast construction. While individual PDC cutters can often be replaced, significant damage to the bit body itself typically renders the bit unrepairable, leading to higher replacement costs.
Steel Body PDC bits are highly repairable. Their steel composition allows for easier welding, machining, and re-tipping. This means that worn or damaged sections and cutters can be more readily replaced or refurbished, extending the bit’s useful life over multiple runs and offering a more cost-effective solution in the long term.
Design Flexibility
The manufacturing process for Matrix Body PDC bits, involving casting, can sometimes limit the complexity of achievable bit profiles and hydraulic designs. This may result in thicker blades and smaller junk slots, potentially affecting cuttings removal efficiency.
Steel Body PDC bits offer greater design flexibility due to their machining process. This allows manufacturers to create more intricate bit geometries, including taller and thinner blades, and larger junk slots, which can significantly improve hydraulic efficiency and the evacuation of drill cuttings from the borehole.
Ideal Applications
Matrix Body PDC bits are best suited for drilling in hard, highly abrasive, and consolidated formations, particularly in deep wells where high temperatures and significant erosion are concerns. Their excellent wear resistance ensures prolonged performance in these demanding environments.
Steel Body PDC bits are often preferred for drilling in softer to medium formations, interbedded rock, and applications where high impact loads are anticipated. Their superior toughness and repairability also make them a versatile and economical choice for various drilling scenarios.
Here are the differences between matrix body PDC bits and steel body PDC bits:
Feature | Matrix Body PDC Bits | Steel Body PDC Bits |
Construction Material | Tungsten carbide composite (cast) | High-strength alloy steel (milled) |
Wear & Erosion Resistance | Excellent | Good (often enhanced with hard-facing/coatings) |
Impact Resistance | Lower (more brittle) | Higher (more ductile) |
Repairability | Limited (body repair difficult) | High (easily welded and refurbished) |
Design Flexibility | More limited (due to casting process) | High (allows complex geometries, larger junk slots) |
Ideal Applications | Hard, abrasive formations; high fluid volume; deep wells | Soft to medium formations; interbedded rock; high impact |
Other PDC Bit Body
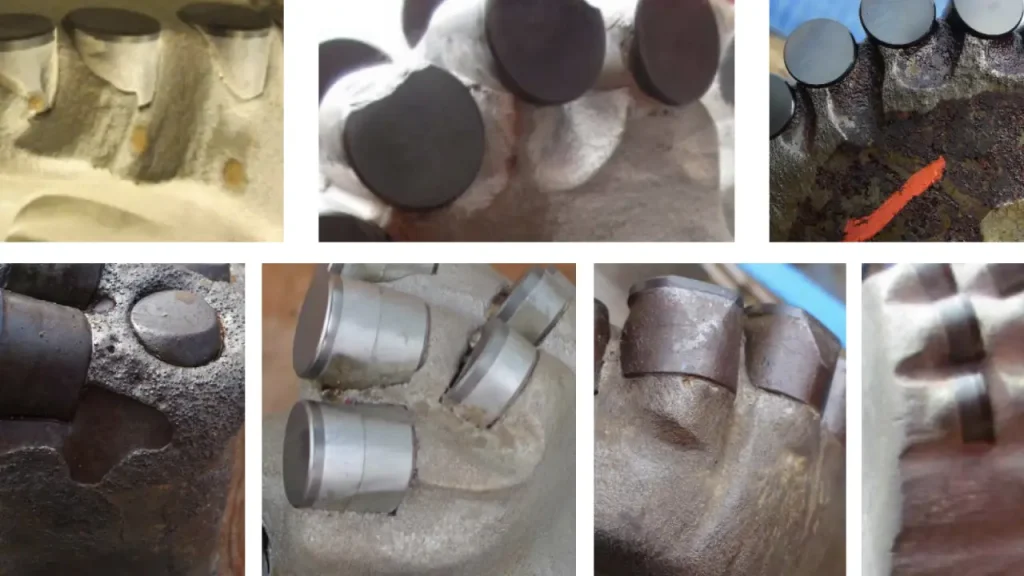
PDC drill bit bodies are engineered for specific drilling conditions, providing the foundation for the cutters and managing fluid flow. After a run, evaluating the body’s dull characteristics is as crucial as assessing the cutters themselves. These observations inform future bit design and operational adjustments for optimal performance.
Cored (CR)
“Cored” (CR) on a PDC bit body indicates that the center of the bit has been preferentially worn away or “cored out” by the formation, leading to a loss of the central cutting structure or bit stability. This dull characteristic suggests that the rock in the center of the borehole was particularly aggressive or the bit’s central cutters were unable to efficiently engage and remove it.
The formation of a core can significantly impact the bit’s steerability and its ability to maintain a consistent rate of penetration. An excessively cored bit often experiences reduced stability, leading to increased vibration and potentially damaging other bit components or the bottom hole assembly (BHA), making precise drilling challenging.
Erosion (ER)
Erosion (ER) on a PDC bit body refers to the gradual removal of material from the bit’s matrix or steel body due to the abrasive action of drilling fluids laden with rock cuttings. This process typically occurs in areas of high fluid velocity, such as around the junk slots, nozzles, or leading edges of the blades.
Significant erosion can compromise the bit’s hydraulic efficiency by altering flow paths, leading to reduced cleaning of cutters and inadequate cooling. Furthermore, severe body erosion can weaken the structural integrity of the bit, potentially exposing cutter pockets or leading to more catastrophic failures during the drilling operation.
Heat Checking (HC)
Heat checking (HC) on a PDC bit body manifests as fine, spiderweb-like cracks on the surface of the matrix or steel material. While more commonly associated with cutters, it can occur on the bit body, especially in areas subjected to high friction and localized heat, such as near worn gauge pads or in junk slots where cuttings may pack.
These cracks are a result of thermal fatigue caused by repeated heating and cooling cycles during drilling. Although initially superficial, extensive heat checking can indicate underlying thermal stress, potentially leading to material spalling or weakening the bond between the cutters and the bit body, ultimately reducing bit durability.
Junk Damage (JD)
Junk damage (JD) occurs when the PDC bit encounters foreign objects in the wellbore, leading to deformation, gouging, or impact marks on the bit body, blades, or even the cutters themselves. These foreign objects, often referred to as “junk,” can include broken downhole tools, metal debris, or lost equipment from previous operations.
The impact from junk can cause significant and localized damage to the bit body, potentially breaking blades, creating imbalances, or altering the bit’s cutting profile. This not only impairs the bit’s performance but can also lead to premature bit failure, requiring costly and time-consuming fishing operations or bit trips.
Ring Out (RO)
“Ring Out” (RO) describes a distinct circumferential wear pattern or groove that forms on the bit body, typically around the periphery of the bit face or on the gauge pads. This damage is often indicative of severe bit whirl or lateral vibration, where the bit is not rotating concentrically but instead undergoing an orbital motion within the borehole.
Ring out signifies unstable drilling dynamics that can severely impact drilling efficiency and bit life. This lateral movement causes excessive and uneven wear on the bit body, leading to reduced steerability, increased torque fluctuations, and potential damage to the wellbore wall, compromising overall drilling performance.
Wash Out (WO)
Wash out (WO) on a PDC bit body refers to the formation of a localized hole or channel in the bit’s matrix or steel structure, typically caused by focused and high-velocity fluid flow. This differs from general erosion in that it creates a specific, often deep, perforation through the bit material, commonly occurring near nozzles or fluid passages.
A significant wash out can lead to a severe loss of hydraulic pressure, compromising the bit’s ability to effectively clean cutters and transport cuttings out of the wellbore. More critically, a wash out can weaken the structural integrity of the bit, potentially leading to catastrophic failure of a blade or the entire bit, risking leaving debris downhole.
Unofficial: Broken Blade (BB)
“Broken Blade” (BB) is an unofficial dull characteristic that describes a partial or complete fracture and separation of one or more of the bit’s primary blades from the main bit body. This is a severe structural failure that directly impacts the bit’s ability to function, as the blades house the PDC cutters and provide structural support.
The loss of a blade fundamentally alters the bit’s balance and cutting structure, leading to immediate and significant reductions in penetration rate, increased vibration, and potential damage to the wellbore. Identifying a broken blade necessitates an immediate bit trip due to the severe compromise of the tool’s integrity and performance.
How to Choose Matrix Body PDC Bits vs Steel Body
Choosing the optimal PDC bit type, whether Matrix Body or Steel Body, is a critical decision that directly impacts drilling efficiency, cost-effectiveness, and overall project success. This choice should be a well-informed one, based on a comprehensive analysis of the specific drilling environment and operational priorities. Below, we detail the key considerations to guide your selection:
Formation Type:
- Matrix Body Bits: These bits are the go-to choice for drilling in hard, highly abrasive, and consolidated formations. Their exceptional erosion and abrasion resistance, derived from their tungsten carbide composite body, allows them to maintain cutting efficiency and extend bit life in challenging rock types like granite, quartzite, and hard sandstones. They also perform well in environments with high drilling fluid volumes, where erosive wear is a significant factor. If you’re encountering formations that rapidly wear down other bit types, a matrix body is likely your best bet.
- Steel Body Bits: Conversely, Steel Body bits are often preferred for softer to medium formations, including shales, soft sandstones, and limestones. Their inherent toughness and ductility make them more resilient when drilling through formations with interbedded hard streaks or variable rock strengths, where the bit might encounter sudden changes in resistance. While less resistant to pure abrasion, their robust nature handles the fluctuating loads better.
Impact Risk:
- Matrix Body Bits: Due to their hard and more brittle nature, Matrix Body bits have lower impact resistance. They are more susceptible to damage (such as blade cracking or lost cutters) if they encounter severe shock loads, sudden changes in formation hardness, or debris (junk) in the borehole. In environments where the risk of such impacts is high, their use may lead to premature bit failure and increased tripping costs.
- Steel Body Bits: Steel Body bits possess superior impact resistance and toughness. The ductile nature of steel allows them to absorb and distribute energy from impacts more effectively, making them significantly more robust in drilling environments prone to high shock loads. This makes them ideal for formations with fractured rock, rubble zones, or when there’s a higher likelihood of encountering foreign objects downhole. If the integrity of the bit against sudden forceful impacts is a primary concern, steel body is the clear winner.
Repairability & Cost:
- Matrix Body Bits: While highly durable in abrasive conditions, Matrix Body bits are generally difficult and sometimes impossible to repair if the bit body itself sustains significant damage. Though individual PDC cutters can often be replaced, extensive body erosion or cracking usually means the bit is beyond economical repair, leading to a higher long-term replacement cost per foot drilled if damaged prematurely.
- Steel Body Bits: Steel Body bits are highly repairable, which is a significant advantage in terms of cost-effectiveness over the bit’s operational lifespan. Their steel construction allows for easy welding, machining, and re-tipping of worn or damaged sections and cutters. This capability means a single steel body bit can often be refurbished multiple times, significantly extending its useful life and reducing the overall cost per foot drilled. If minimizing bit replacement expenses and maximizing asset utilization are key priorities, steel body bits offer a compelling economic argument.
Hydraulics & Cuttings Removal:
- Matrix Body Bits: The casting process used for Matrix Body bits can sometimes impose limitations on the complexity of bit profiles and the size of hydraulic features. This may result in thicker blades and smaller junk slots, which can potentially restrict the flow of drilling fluid and the efficient removal of cuttings, particularly in formations that produce large volumes of cuttings.
- Steel Body Bits: Due to the precision machining process, Steel Body bits offer greater design flexibility. This allows for the creation of more intricate bit geometries, including thinner and taller blades, and significantly larger junk slots. These design advantages translate into improved hydraulic efficiency and superior cuttings evacuation, which is crucial for maximizing ROP (Rate of Penetration) and preventing re-grinding of cuttings in soft, sticky, or high-volume formations.
Conclusion
In conclusion, both Matrix Body and Steel Body PDC bits offer distinct advantages depending on your drilling environment. Matrix body bits excel in abrasive, harder formations due to their superior erosion resistance, while steel body bits provide greater impact strength and are more easily repaired, making them suitable for softer to medium formations and where cost-effectiveness is a priority.
Careful consideration of factors like formation type, drilling conditions, and cost will guide you in selecting the optimal PDC bit for maximum efficiency and longevity.
Looking for reliable and high-quality PDC drill bits? Get wholesale PDC drill bits directly from us, a trusted manufacturer in Qingdao, Shandong, China. Contact us today to discuss your specific drilling needs.