Custom Diamond PDC Bit Manufacturer in China
We proudly offer a comprehensive selection of high-performance diamond PDC drill bits, engineered to revolutionize your drilling operations. Our cutting-edge bits feature superior synthetic diamond cutters, designed for unmatched durability and aggression in diverse geological formations. Trust our advanced technology to deliver exceptional penetration rates, extended bit life, and ultimately, significant cost savings on your next drilling project.
Sinodrills - Your Trusted Diamond PDC Bit Manufacturer from China
Sinodrills stands as your trusted diamond PDC bit manufacturer, proudly based in China. We specialize in producing high-quality, innovative PDC drill bits engineered for superior performance and durability in the most challenging drilling environments. Our commitment to advanced technology and stringent quality control ensures you receive reliable, cost-effective solutions. Partner with us for your next drilling project.
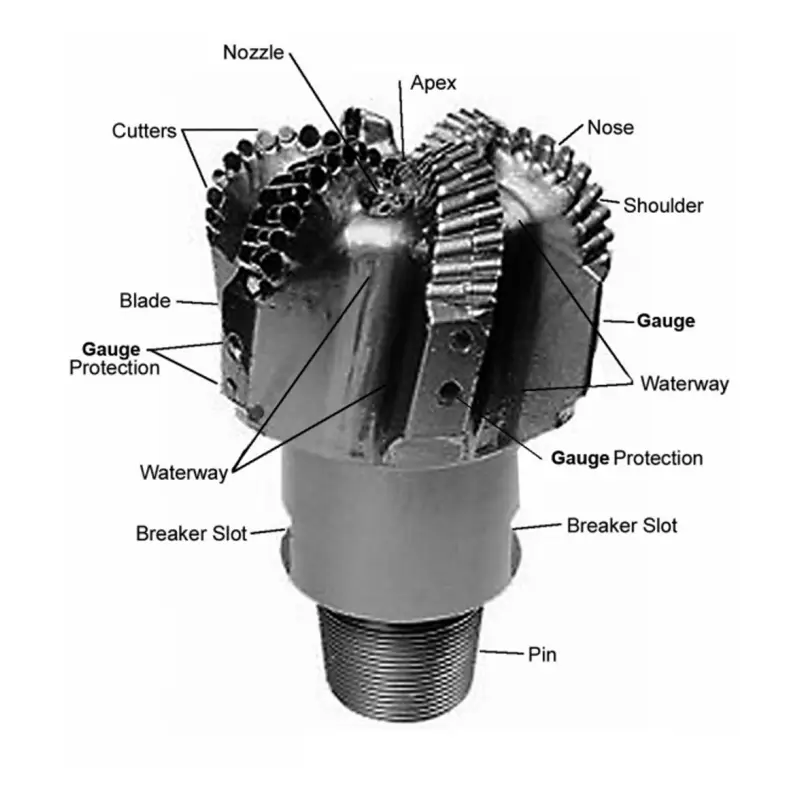
Diamond PDC bit Components
Cutters: These are the primary cutting elements, typically synthetic diamond compacts, strategically placed on the bit face to shear and remove rock.
Nozzle: Designed to direct drilling fluid jets onto the bit face for cooling cutters and clearing cuttings from the bottom of the hole.
Apex: The central highest point of the bit, often featuring cutters to initiate rock breaking at the wellbore center.
Nose: The region between the apex and the shoulder, typically containing a high concentration of cutters for aggressive drilling.
Shoulder: The transitional area between the nose and the gauge, crucial for maintaining hole size and supporting cutters.
Gauge: The outermost diameter of the bit, lined with wear-resistant elements (like PDC inserts or diamond-enhanced material) to ensure the wellbore remains at the correct diameter.
Gauge Protection: Additional features on the gauge pads, such as PDC inserts, that provide enhanced resistance against wear and help maintain hole size.
Blade: The structural elements extending from the bit body, onto which the PDC cutters and gauge protection are mounted. Blades define the bit’s profile and junk slot area.
Waterway: Channels or grooves on the bit face and between blades that facilitate the flow of drilling fluid and the efficient removal of rock cuttings from the wellbore.
Breaker Slot: Not explicitly labeled on all bits, but often refers to relief areas or secondary junk slots that aid in breaking up larger cuttings and improving fluid flow.
Pin: The threaded connection at the top of the bit that connects it to the drill string. This is typically a standard API (American Petroleum Institute) thread.
Diamond PDC bit Benefits
Higher Rate of Penetration (ROP): Their shearing cutting action allows for faster drilling speeds compared to roller cone bits in suitable formations, reducing drilling time.
Extended Bit Life: The extreme hardness and abrasion resistance of synthetic diamond cutters provide exceptional durability, allowing bits to drill for longer intervals without needing to be replaced.
Reduced Trips: Longer bit life means fewer trips out of the hole to change bits, significantly saving expensive rig time and associated operational costs.
Improved Hole Quality: PDC bits often produce a smoother, more consistent wellbore due to their continuous cutting action and stable design.
Better Steerability: Their fixed-cutter design can offer better control and responsiveness in directional drilling applications, improving trajectory accuracy.
Fewer Moving Parts: Unlike roller cone bits, PDC bits have no moving parts on the bottom, which reduces the risk of mechanical failure downhole.
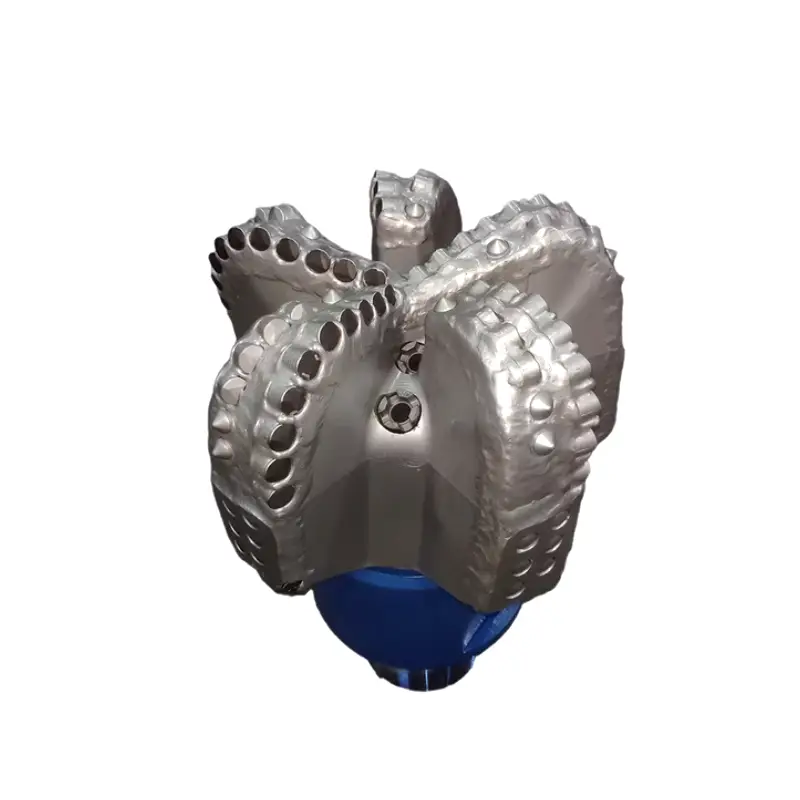
Customize Your Desired Diamond PDC Bit
Cutter Selection and Placement
We meticulously choose cutter size, shape, and grade based on your target formation’s abrasiveness and hardness. Our engineers strategically place each cutter to optimize shearing action and maximize ROP. This bespoke approach ensures enhanced cutting efficiency and extended bit life, delivering superior performance precisely tailored to your drilling challenges.
Bit Body Profile
We design the bit body profile—flat, parabolic, or short/long taper—to match your specific drilling application. A customized profile ensures optimal stability, efficient cuttings removal, and effective weight transfer. This critical aspect prevents balling, minimizes vibration, and maximizes torque control, allowing us to achieve smooth, high-performance drilling for your project.
Hydraulics (Nozzle Configuration)
We precisely configure the bit’s hydraulics, including nozzle count, size, and orientation, to optimize fluid flow. This ensures efficient bit cleaning, effective cutter cooling, and optimal bottom hole cleaning. Our tailored hydraulic designs prevent cuttings recirculation and minimize bit balling, significantly enhancing ROP and extending the bit’s operational lifespan in your wells.
Gauge Protection
We integrate advanced gauge protection into our PDC bit designs, using wear-resistant materials like diamond-enhanced inserts. This customized protection maintains exact hole diameter throughout the run, even in abrasive formations. Our robust gauge solutions prevent undersized holes, minimize reaming, and ensure bit stability, optimizing your directional control and overall drilling efficiency.
what is a diamond PDC Bit?
A diamond PDC (Polycrystalline Diamond Compact) bit is a type of drill bit characterized by its fixed cutting structure, where synthetic diamond cutters are brazed onto a tungsten carbide matrix or steel body.
These diamond PDC drill bits leverage the extreme hardness and abrasion resistance of industrial diamonds to shear rock efficiently. Designed for high-speed drilling and long runs, diamond PDC bits are widely used across the oil and gas, geothermal, and mining industries for their superior Rate of Penetration (ROP) and extended durability in a range of geological formations.
diamond PDC Bit Uses
Diamond PDC bits are highly versatile and widely used across various drilling applications due to their high efficiency and durability. Their primary uses include:
Oil and Gas Drilling: Commonly employed for drilling long sections in soft to medium-hard, homogeneous formations like shales, limestones, and sandstones, where high Rate of Penetration (ROP) is crucial.
Geothermal Drilling: Effective in drilling through geothermal formations that can be abrasive or have varying hardness, leveraging their heat resistance and durability.
Mining: Used in certain mining operations for faster penetration in softer ore bodies or overburden.
Directional and Horizontal Drilling: Their stable cutting action and steerability make them preferred for complex well paths and horizontal sections.
Underbalanced Drilling: Suitable for drilling with reduced hydrostatic pressure due to their ability to clean the bit face efficiently.
diamond PDC Bit Features
Diamond PDC bits are highly engineered tools, designed with specific features to maximize drilling efficiency and durability. Their innovative construction integrates advanced components.
Understanding these key features is essential for appreciating their superior performance and optimizing their application in diverse challenging drilling environments.
Polycrystalline Diamond Cutters
At the core of a PDC bit are its polycrystalline diamond cutters. These synthetic diamonds, bonded to a tungsten carbide substrate, provide extreme hardness and abrasion resistance. They efficiently shear rock, leading to high rates of penetration and extended bit life, making them superior for rapid, continuous drilling operations in suitable formations.
Robust Bit Body
The bit body, crafted from either steel or matrix material, provides the structural foundation. A steel body offers high strength and ease of repair, while matrix bodies excel in abrasive environments due to their wear resistance. This robust construction ensures durability, provides secure seating for cutters, and withstands harsh downhole conditions during drilling.
Optimized Hydraulic System
An efficient hydraulic system is crucial, featuring strategically placed nozzles. These nozzles direct drilling fluid jets to cool the PDC cutters, prevent bit balling by clearing cuttings from the bit face, and transport debris up the annulus. Optimized hydraulics are vital for maintaining high ROP and extending the bit’s operational lifespan.
Engineered Blade Design
The bit’s blades are structural extensions supporting the cutters and defining the junk slots. Their design, including number, height, and spiral arrangement, impacts stability, cutting efficiency, and cuttings removal. Well-engineered blades prevent bit whirl and facilitate smooth drilling, directly contributing to consistent penetration rates and longer bit life.
Integrated Gauge Protection
Gauge protection on a PDC bit ensures the drilled hole maintains its precise diameter. This involves wear-resistant elements, often additional PDC inserts or diamond-enhanced material, placed along the bit’s outermost diameter. Robust gauge protection prevents bit wear, minimizes reaming, and maintains directional control throughout the drilling process.
Specific Bit Profile
Each PDC bit possesses a specific profile (e.g., flat, parabolic, short/long taper) tailored for different applications. This profile dictates how cutters engage the formation across the bit face, influencing stability and ROP. A customized profile optimizes weight distribution, enhances steering capabilities, and improves cuttings evacuation for efficient drilling performance.
how to choose diamond PDC Bits?
Selecting the ideal diamond PDC bit is crucial for maximizing drilling efficiency and minimizing costs. It requires a deep understanding of your specific project needs.
By carefully considering key factors, you can ensure the chosen bit delivers optimal performance, reducing operational time and enhancing overall well profitability.
Formation Characteristics
Understanding the geological formation’s properties is paramount. For soft to medium-hard, homogeneous rocks like shales, select PDC bits with aggressive, high-exposure cutters. For harder, more abrasive formations, opt for more robust cutters and reinforced bit bodies to withstand wear and maintain cutting efficiency.
Drilling Dynamics and Stability
Consider the potential for downhole vibrations, stick-slip, or bit whirl. In unstable environments, choose PDC bits with enhanced stability features, such as specific blade designs or shock-absorbing elements, to ensure smooth drilling. This minimizes damage and maintains consistent ROP in challenging conditions.
Desired Rate of Penetration (ROP)
Your target ROP influences bit aggressiveness. For maximizing ROP in softer formations, a PDC bit with higher cutter density and greater cutter exposure might be chosen. Balance this with bit durability requirements for extended runs in varying rock strengths to optimize overall drilling speed.
Bit Profile and Hydraulics
The bit’s profile (e.g., flat, parabolic) affects cutter engagement and cleaning. A flatter profile may be better for softer formations, while a parabolic profile offers more stability. Optimize hydraulics (nozzle count, size) to ensure efficient cuttings evacuation and cutter cooling, preventing bit balling and maximizing ROP.
Gauge Protection Needs
For abrasive formations prone to gauge wear, prioritize PDC bits with robust gauge protection, like additional diamond inserts or wear pads. Effective gauge protection maintains the hole diameter, prevents reaming, and extends bit life, ensuring a high-quality wellbore throughout the drilling process.
Cost-Effectiveness
While PDC bits have higher initial costs, evaluate their total cost per foot drilled. A bit that lasts longer and drills faster, reducing trip time, can be more economical. Consider the trade-off between upfront investment and the long-term operational savings achieved through superior performance.
Send Your Inquiry Now
All-in-one Diamond PDC Bit Solutions for Your Project
Inconsistent drilling performance and escalating project costs can severely impact your operations. The complexities of varied formations often lead to inefficient hole-making and budget overruns, causing significant project delays. Discover our all-in-one Diamond PDC Bit Solutions, meticulously engineered for your project. We deliver unmatched durability and superior penetration, ensuring optimized efficiency, reduced expenses, and successful well completion for your specific challenges.