Custom Drill Pipe Specifications Manufacturer in China
Struggling to find drill pipe that precisely matches your project’s unique demands? Generic options often lead to inefficiencies and compromised performance. Our specialized manufacturing in China delivers custom drill pipe specifications, ensuring perfect compatibility and peak drilling efficiency for your operations. Achieve superior results and extend equipment lifespan with our tailor-made solutions.
Sinodrills - Your Trusted Drill Pipe Specifications Manufacturer from China
Need a reliable drill pipe manufacturer that meets exact specifications? Poorly matched drill pipe compromises performance and safety. Sinodrills, a leading drill pipe manufacturer from China, provides precise, high-quality drill pipe built to your specifications, ensuring optimal drilling efficiency and maximum operational uptime. Trust Sinodrills for superior, dependable drill pipe solutions.
Drill Pipe Specifications
Here’s a table illustrating some common drill pipe specifications:
Specification Category | Description | Common Values/Examples |
Material Grade | Indicates the yield strength of the steel, influencing the pipe’s resistance to permanent deformation under stress. Higher grades mean higher strength. | E-75, X-95, G-105, S-135 (Yield Strength in ksi) |
Outer Diameter (OD) | The external diameter of the drill pipe body. This is a primary factor in determining the pipe’s strength and the wellbore size it can be used in. | 2 3/8″, 2 7/8″, 3 1/2″, 4″, 4 1/2″, 5″, 5 1/2″, 6 5/8″ |
Wall Thickness | The thickness of the pipe wall, affecting its weight, strength, and internal pressure rating. | Varies depending on OD and weight per foot (e.g., 0.280″, 0.362″, 0.400″) |
Weight per Foot | The nominal weight of the pipe per linear foot, impacting handling, hoisting capacity, and buoyancy. | Varies greatly based on OD and wall thickness (e.g., 10.40 lb/ft for 3 1/2″ E-75, 25.20 lb/ft for 5″ S-135) |
Internal Diameter (ID) | The internal diameter of the pipe, affecting the flow rate of drilling fluid (mud). | Varies based on OD and wall thickness |
Connection Type | The thread and shoulder design used to connect individual drill pipe sections. Critical for proper sealing and torque transfer. | API Reg (Regular), FH (Full Hole), IF (Internal Flush), XT (eXtra Torque), HT (High Torque) |
Tool Joint OD | The outer diameter of the thickened ends of the drill pipe where connections are made. | Larger than pipe body OD (e.g., 4 3/4″ for 3 1/2″ pipe, 6 5/8″ for 5″ pipe) |
Tool Joint ID | The inner diameter of the tool joint, typically smaller than the pipe body ID to allow for upset. | Varies based on connection type and pipe size |
Length Range | Standard lengths in which drill pipe is manufactured. | Range 1 (18-22 ft), Range 2 (27-30 ft), Range 3 (38-45 ft) |
Wear Pad (Hardbanding) | Applied to tool joints to reduce wear during drilling. |
Drill pipe specifications are critical parameters that define the physical characteristics and performance capabilities of drill pipes, which are essential components in drilling operations for oil, gas, and geothermal wells. These specifications ensure that the drill pipe can withstand the immense stresses encountered during drilling, including torsional forces, tension, compression, and internal pressure.
Key specifications often adhere to standards set by organizations like the American Petroleum Institute (API), covering aspects such as material grade (e.g., E-75, X-95, G-105, S-135), ensuring the pipe’s strength and durability. Understanding these specifications is vital for selecting the correct pipe for a given drilling application, optimizing drilling efficiency, and maintaining wellbore integrity and safety.
A crucial aspect of drill pipe specifications involves drill pipe sizes. These sizes refer to the external diameter of the pipe body and the tool joints, as well as the internal diameter, which impacts fluid flow. Common drill pipe sizes range from 2 3/8 inches to 6 5/8 inches in outer diameter, with different wall thicknesses and internal diameters available for various drilling conditions.
The size, coupled with the pipe’s weight per foot, significantly influences its suitability for different well depths, drilling techniques, and rig capacities. Furthermore, connection types (e.g., API REG, FH, IF, XT, HT) are also part of the specifications, ensuring proper make-up torque and sealing for the drill string.
Drill Pipe Specifications | ||||||||||||||||||||||||||||||||||||||||||||||||||||||||||||||||||||||||||||||||||||||||||||||||||||||||||||||||||||||||||||||||||||||||||||||||||||||||||||||||||||||||||||||||||||||||||||||||||||||||||||||||||||||||||||||||||||||||||||||||||||||||||||||||||||||||||||||||||||||||||||||||||||||||||||||||||||||||||||||||||||||||||||||||||||||||||||||||||||||||||||||||||||||||||||||||||||||||||||||||||||||||||||||||||||||||||||||||||||||||||||||||||||||||||||||||||||||||||||||||||||||||||||||||||||||||||||||||||||||||||||||||||||||||||||||||||||||||||||||||||||||||||||||||||||||||||||||||||||||||||||||||||||||||||||||||||||||||||||||||||||||||||||||||||||||||||||||||||||||||||||||||||||||||||||||
|
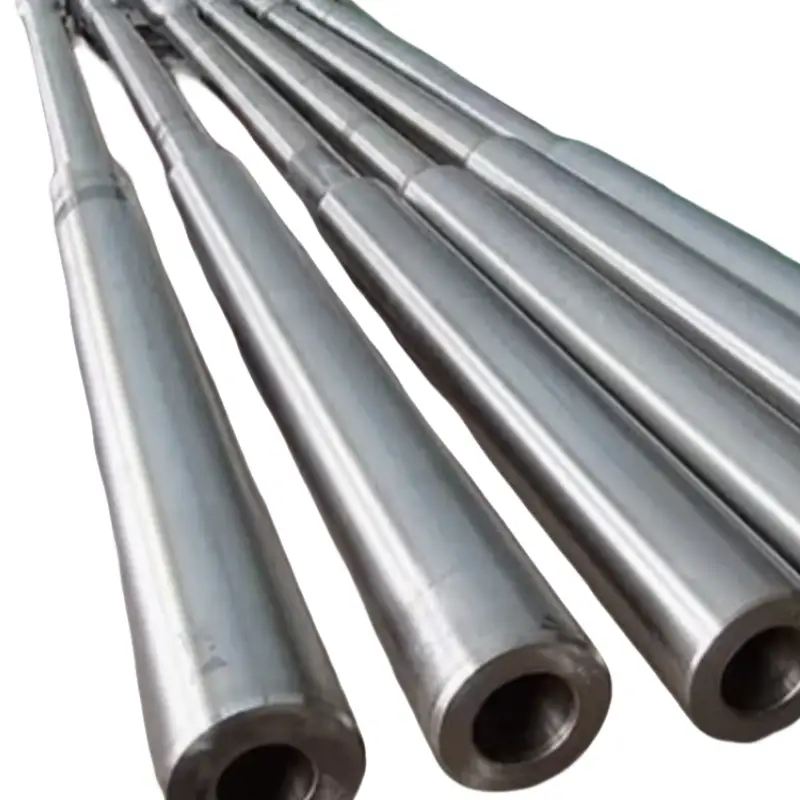
heavy weight drill pipe specifications
Experiencing severe vibration or buckling in your drill string? Inadequate heavy weight drill pipe specifications can lead to premature fatigue and costly downhole failures. We understand the intense demands of complex drilling. Our precisely manufactured heavy weight drill pipe offers superior stiffness and weight distribution, preventing buckling and significantly extending string life. Achieve enhanced stability and optimize your drilling performance with our robust solutions.
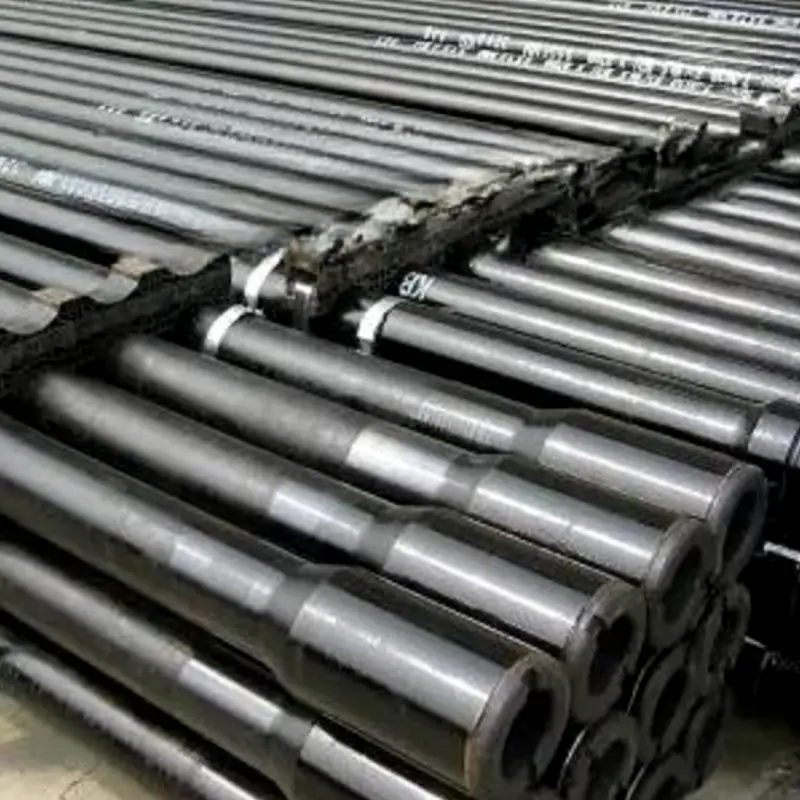
Heavy Weight Drill Pipe 4 1/2”
Is your current heavy-weight drill pipe failing in demanding downhole conditions? Inconsistent performance from standard 4 1/2″ options can lead to costly delays and compromised drilling integrity. We offer premium 4 1/2″ heavy-weight drill pipe, meticulously manufactured in China to withstand extreme stress and provide superior weight-on-bit. Achieve enhanced stability, reduced fatigue, and optimized drilling efficiency for your most challenging projects.
Download Your Desired Drill Pipe Specifications
Material Grade and Strength
We offer a range of API-compliant steel grades, from E-75 for standard drilling to S-135 for high-stress applications. Selecting the right material ensures the pipe withstands specific tensile and torsional forces encountered in your drilling environment. Our expertise helps you balance strength with cost-effectiveness, optimizing performance and extending the lifespan of your drill string.
Dimensions and Weight
We can customize drill pipe outer diameter, wall thickness, and internal diameter to match your wellbore design and rig capabilities. This includes specialized drill pipe sizes like 1/2 inch drill pipe for slim-hole operations or heavy-weight drill pipe 4 1/2″ for increased weight-on-bit. Precise sizing optimizes hydraulic performance, reduces drag, and enhances overall drilling efficiency.
Connection Type and Design
We provide various API and proprietary connection types, including REG, FH, IF, and high-torque connections. Customizing the connection ensures secure make-up, efficient torque transfer, and minimizes washout risks. Our team helps you choose the optimal connection for your specific drilling method, whether it’s conventional rotary drilling or challenging directional operations.
Hardbanding and Wear Protection
We apply advanced hardbanding solutions to tool joints, significantly extending their service life in abrasive formations. Options include various tungsten carbide and chrome-carbide formulations. Customizing hardbanding patterns and materials based on your drilling conditions minimizes wear, reduces maintenance costs, and enhances the overall durability and reliability of your drill pipe.
what is a drill pipe?
A drill pipe is a seamless steel tube equipped with threaded tool joints at both ends, forming a crucial part of the drill string in rotary drilling operations.
Its primary function is to transmit rotational torque from the rig’s top drive or rotary table to the drill bit, while also conveying drilling fluid down to the bit and back up the annulus to cool and lubricate the bit and carry cuttings to the surface.
what is drill pipe used for?
Drill pipe serves several essential functions in the drilling of oil, gas, and geothermal wells. It is primarily used to:
Transmit Torque: Transfer rotational power from the drilling rig’s surface equipment (top drive or rotary table) to the drill bit at the bottom of the wellbore, enabling it to cut through rock formations.
Circulate Drilling Fluid: Act as a conduit for pumping drilling fluid (mud) down to the drill bit. This fluid cools and lubricates the bit, carries rock cuttings back to the surface, and helps maintain wellbore stability.
Apply Weight on Bit (WOB): While drill collars primarily provide WOB, the weight of the drill pipe itself also contributes to the force applied to the drill bit, aiding in efficient penetration.
Lower and Hoist the Bit: Form the main body of the drill string, allowing the drill bit and bottom hole assembly (BHA) to be lowered into the well and retrieved as needed for bit changes or other operations.
how to customize different drill pipe sizes?
Customizing drill pipe sizes involves a precise process to ensure the pipe meets specific operational requirements for optimal drilling performance and safety. Here’s how we approach customizing different drill pipe sizes:
Step 1: Assess Project Requirements
We begin by thoroughly assessing your drilling project’s unique demands, including target well depth, formation types, desired hole size, and rig capabilities. This initial evaluation helps us understand the specific stresses and environmental conditions the drill pipe will encounter downhole.
Step 2: Determine Optimal Dimensions
Based on the project assessment, we determine the optimal outer diameter, wall thickness, and internal diameter for your custom drill pipe. This includes considering specialized drill pipe sizes like 1/2 inch drill pipe for slim-hole drilling or larger diameters for heavy-duty applications, balancing strength and hydraulic efficiency.
Step 3: Select Appropriate Material Grade
We then select the most suitable material grade (e.g., E-75, X-95, G-105, S-135) to match the required yield strength and resistance to fatigue and corrosion. This ensures the customized drill pipe can withstand the specific tensile, torsional, and compressive loads anticipated during your drilling operations.
Step 4: Design Custom Connections
Finally, we design or select the appropriate tool joint connection type and dimensions. This includes considerations for thread form, upset design, and hardbanding. Custom connections ensure secure make-up, efficient torque transfer, and extended lifespan, minimizing non-productive time during your drilling projects.
where you can Use Drill Pipes?
Drill pipes are indispensable in various drilling applications across the globe, primarily within the energy and resource extraction sectors.
They are extensively used wherever boreholes need to be created to access subsurface resources or for specific geological investigations.
Oil and Gas Exploration and Production: This is the most common application, where drill pipes form the backbone of the drill string to reach hydrocarbon reservoirs deep underground, both on land and offshore.
Geothermal Drilling: Used to drill wells for harnessing geothermal energy, accessing hot water and steam from beneath the Earth’s surface for power generation and heating.
Mining Operations: Employed in various mining techniques, including exploration drilling to identify mineral deposits and for creating shafts or blast holes in hard rock.
Water Well Drilling: While often using lighter equipment, drill pipes are used for drilling deeper, larger diameter water wells, especially in areas requiring access to confined aquifers.
Geotechnical and Environmental Drilling: Utilized for site investigations, soil sampling, and installing monitoring wells for environmental studies or construction projects.
Send Your Inquiry Now
All-in-one Drill Pipe Specifications Solutions for Your Project
Struggling with fragmented drill pipe sourcing and inconsistent quality? Incompatible specifications can lead to costly operational delays and compromised safety. We provide all-in-one Drill Pipe Specifications Solutions, custom-engineered and manufactured in China to meet your project’s exact needs. Streamline your procurement, ensure optimal performance, and achieve reliable drilling success with our comprehensive expertise.