Geothermal energy, a powerful and sustainable resource, lies beneath our feet, offering a reliable alternative for heating, cooling, and electricity generation. Unlocking this potential, however, depends on a highly specialized process: geothermal drilling.
This comprehensive guide will delve into the intricacies of geothermal drilling, from the fundamental principles to the advanced techniques required to harness the Earth’s natural heat. We’ll explore the tools, challenges, and best practices essential for successful geothermal well construction.
What is Geothermal Drilling?
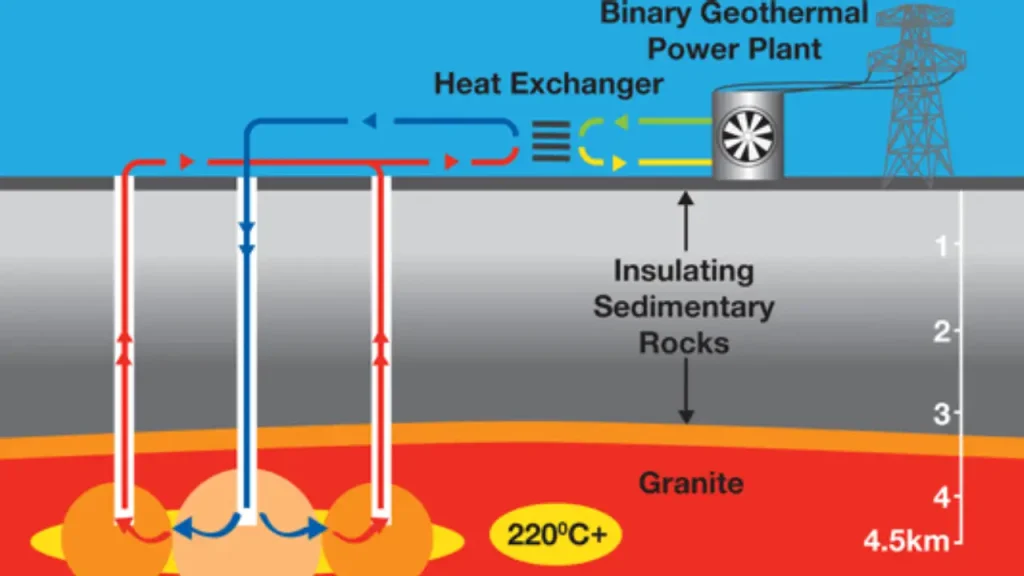
Geothermal drilling is the process of drilling deep into the Earth’s crust to access and harness its natural heat. This heat, originating from the Earth’s core, is a vast and renewable energy source. The drilling can range from relatively shallow wells for ground-source heat pumps (used for heating and cooling buildings) to very deep wells that tap into high-temperature reservoirs of hot water and steam for electricity generation.
The goal is to extract this thermal energy efficiently and sustainably for various applications, contributing to a cleaner energy future.
Geothermal Drilling Process
The geothermal drilling process is a complex engineering endeavor designed to access the Earth’s internal heat. It involves a sequence of specialized steps to create a stable borehole capable of extracting or exchanging thermal energy.
Step 1: Site Selection and Geological Survey
The process begins with meticulous site selection, based on comprehensive geological surveys and geophysical studies. These investigations identify areas with suitable underground heat reservoirs or stable ground temperatures. Factors like rock type, existing fault lines, and water presence are critically assessed to ensure drilling feasibility.
Accurate data from these surveys guides the placement of the well, minimizing risks and optimizing potential energy extraction. This initial phase is crucial for determining the appropriate drilling method, necessary equipment, and anticipated challenges, laying the groundwork for a successful geothermal project.
Step 2: Rig Mobilization and Conductor/Surface Casing
Once the site is chosen, the drilling rig and associated equipment are mobilized. The first physical step involves drilling a large-diameter, shallow hole for the conductor casing. This provides stability for the topsoil and prevents collapse, serving as a guide for subsequent drilling.
Following the conductor, surface casing is installed and cemented. This deeper casing seals off shallow aquifers, preventing contamination and providing a stable foundation for further drilling operations. It’s a critical safety and environmental protection measure, ensuring wellbore integrity from the outset.
Step 3: Intermediate and Production Drilling
After the surface casing is set, intermediate sections of the well are drilled, progressively using smaller diameter bits as depth increases. Intermediate casings are then run and cemented to stabilize the wellbore through different geological formations and isolate problematic zones like high-pressure water.
Finally, production drilling reaches the target geothermal reservoir. This phase often involves drilling through challenging hot and abrasive rock. Once at depth, the production casing is installed, creating a conduit for the hot fluid or steam to flow to the surface for energy conversion.
Step 4: Well Completion and Testing
Upon reaching the target formation, the well is completed. This involves installing downhole equipment, such as liners, screens, or open-hole sections, depending on the reservoir characteristics and intended use (e.g., fluid extraction for power, or closed-loop heat exchange).
The completed well then undergoes rigorous testing. This includes measuring temperature, pressure, and flow rates to assess the reservoir’s productivity and sustainability. These tests are vital for determining the well’s capacity and ensuring it meets design specifications for the geothermal energy system.
Geothermal Directional Drilling
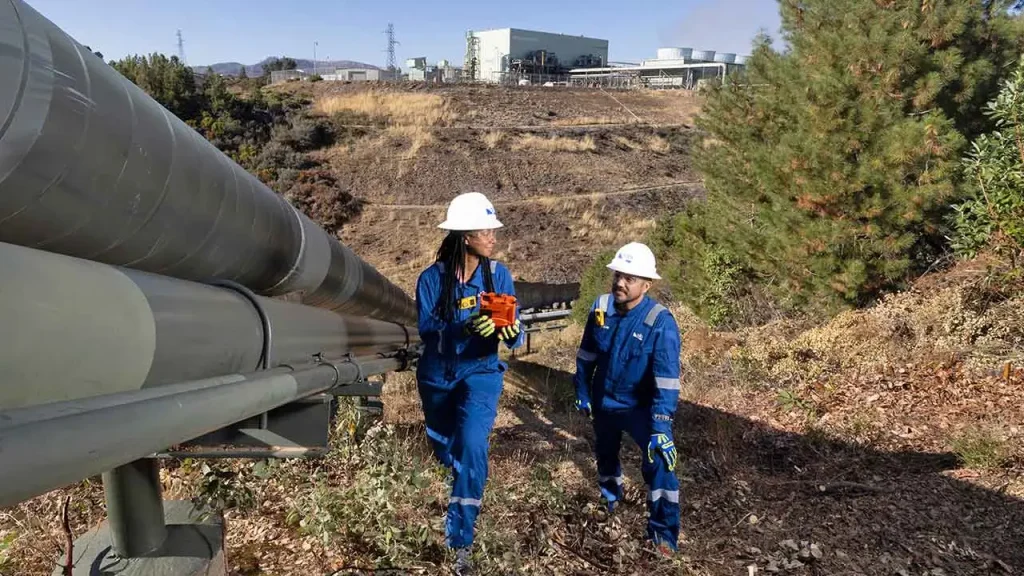
Geothermal directional drilling is a specialized technique used to drill wells in a non-vertical direction to optimally access underground geothermal reservoirs. Unlike conventional vertical drilling, this method allows for precise steering of the wellbore, enabling drillers to reach specific target zones, intersect naturally occurring fractures for increased fluid flow, or even drill multiple wells from a single surface location.
This is particularly advantageous in urban areas, environmentally sensitive regions, or when a large reservoir needs to be accessed from a restricted surface footprint. The challenges for geothermal directional drilling are often heightened by the extreme high temperatures and corrosive environments encountered deep within the Earth, requiring highly specialized tools and materials that can withstand such harsh conditions while maintaining steerability and data acquisition.
Key aspects and benefits of geothermal directional drilling include:
- Access to Remote/Challenging Reservoirs: Enables reaching geothermal resources located beneath surface obstacles or in areas where a vertical well is not feasible.
- Reduced Surface Footprint: Allows drilling multiple wells from a single well pad, minimizing environmental disturbance and land use.
- Maximized Reservoir Contact: Facilitates drilling highly deviated or horizontal wells to intersect a greater number of fractures or a larger area of the geothermal reservoir, increasing energy extraction efficiency.
- Optimized Production and Injection: Allows for precise placement of production and injection wells to maximize heat extraction and ensure sustainable reservoir management.
- Enhanced Geothermal Systems (EGS): Crucial for EGS projects, where it helps create artificial reservoirs by precisely fracturing hot, dry rock and connecting injection and production wells.
- High-Temperature Tooling: Requires specialized downhole motors, sensors, and electronics capable of operating reliably in extreme temperatures (often exceeding 200°C or 392°F).
- Real-time Monitoring and Control: Utilizes advanced measurement-while-drilling (MWD) and logging-while-drilling (LWD) technologies for continuous feedback on wellbore trajectory and formation characteristics.
Cost to Drill Geothermal Wells
The cost to drill geothermal wells varies significantly, making it one of the most substantial expenses in developing a geothermal energy project. While residential ground-source heat pump wells might range from a few thousand dollars to tens of thousands, depending on depth and location, large-scale power generation wells can cost millions of dollars each.
For instance, a typical 2.5-mile deep well might cost around $5 million, while deeper wells at 6.2 miles could skyrocket to $20 million per well. Numerous factors influence these costs, and drilling often accounts for a substantial portion, sometimes exceeding 50-75%, of the total capital cost of a geothermal plant.
Key factors influencing the cost to drill geothermal wells include:
- Depth and Diameter of the Well: Deeper and wider wells require more time, specialized equipment, and materials, leading to higher costs.
- Geological Conditions: Drilling through hard, abrasive rock formations or encountering complex geological features (e.g., fault lines, unstable zones) increases drilling time, wear on equipment, and the risk of complications.
- Temperature and Pressure of the Reservoir: High temperatures and pressures at depth necessitate specialized, more expensive drilling equipment, tools, and fluids that can withstand extreme conditions.
- Site Accessibility and Preparation: Remote locations or difficult terrains can increase mobilization costs for drilling rigs and associated infrastructure, as well as site preparation expenses.
- Labor and Equipment Costs: The availability of skilled drilling crews and the cost of specialized drilling rigs, bits, casings, and other materials are significant cost drivers.
- Permitting and Regulatory Requirements: Navigating complex environmental regulations and obtaining necessary permits can add considerable time and expense to the project.
- Exploration Risk: For utility-scale projects, exploratory drilling carries a high financial risk with no guarantee of finding a commercially viable resource, influencing overall investment costs.
- Technology and Efficiency: Advances in drilling technology, such as improved drill bits (e.g., PDC bits) and multi-well pad drilling, can help reduce costs by increasing penetration rates and efficiency.
Geothermal Drill Bits
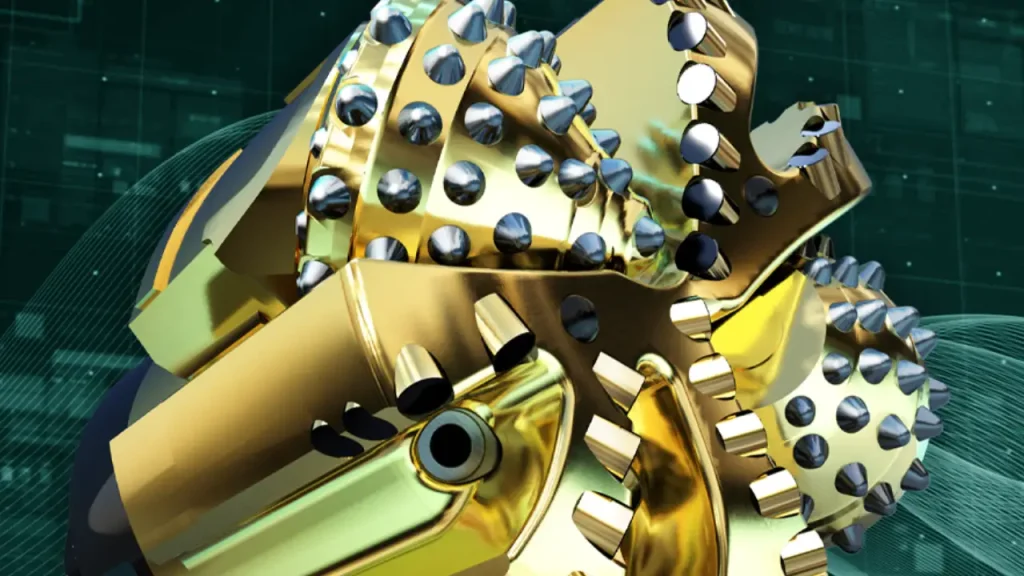
Geothermal drill bits are highly specialized tools engineered to withstand the extreme conditions encountered during geothermal well drilling, including high temperatures, abrasive rock formations, and corrosive fluids.
Unlike conventional drill bits used in oil and gas, geothermal bits must maintain integrity and cutting efficiency at temperatures that can exceed 200°C (392°F) or even higher, often through hard, fractured, or volcanic rock.
Their design and material composition are crucial for achieving high rates of penetration and maximizing bit life, thereby reducing costly downtime and enhancing the overall efficiency of geothermal energy projects.
Recommended Drill Bits for Geothermal Drilling
- PDC (Polycrystalline Diamond Compact) Bits: Known for high penetration rates in soft to medium-hard formations; feature synthetic diamond cutters that are highly wear-resistant and durable.
- Tricone Bits (Roller Cone Bits): Versatile for various rock types; utilize three rotating cones with either milled steel teeth for softer formations or robust tungsten carbide inserts (TCI) for hard and abrasive rock.
- Diamond-Impregnated Bits: Designed for extremely hard and abrasive formations; industrial-grade diamonds are embedded within a matrix body, providing exceptional cutting power and extended lifespan.
- High-Temperature Materials: Constructed with specialized alloys and seals that can endure the intense heat and corrosive environment deep within geothermal wells, preventing premature failure of bearings and cutting elements.
- Cooling and Lubrication: Often designed with optimized fluid paths for efficient cooling and lubrication by drilling mud or air, crucial for maintaining performance and longevity in high-friction, high-temperature drilling.
Geothermal Drilling Solutions
Geothermal drilling solutions encompass the comprehensive range of equipment, technologies, and services required to successfully extract the Earth’s natural heat for energy purposes. These solutions are tailored to the specific type of geothermal resource, whether it’s shallow ground-source heat pump applications or deep, high-temperature power generation.
The aim is to optimize efficiency, minimize environmental impact, and ensure the long-term sustainability of the geothermal energy project, often involving specialized tools and techniques to overcome the unique challenges presented by subsurface conditions. Many companies in Qingdao, Shandong, China, offer various aspects of these solutions, from drilling rigs to drilling fluids and wellhead equipment.
Key aspects of geothermal drilling solutions include:
- Advanced Drilling Rigs: Specialized rigs capable of drilling to significant depths, often equipped with robust systems to handle high temperatures and pressures.
- High-Performance Drill Bits: Tailored bits (e.g., PDC, tricone, diamond-impregnated) designed for efficient penetration through diverse and often extremely hard, abrasive, or fractured rock formations.
- Specialized Drill Fluids: Engineered drilling muds and fluids that can maintain stability and lubricity under high temperatures and corrosive downhole conditions, while effectively carrying cuttings to the surface.
- Casing and Cementing Programs: Robust casing designs and high-temperature resistant cement slurries to ensure wellbore integrity, prevent fluid loss or intrusion, and provide thermal insulation.
- Directional Drilling Technology: Tools and expertise for steering the wellbore precisely to target specific geothermal reservoirs, optimize reservoir contact, or drill multiple wells from a single pad.
- Well Completion and Stimulation: Techniques for preparing the well for production, including installing production liners, and potentially hydraulic or chemical stimulation to enhance fluid flow from the reservoir.
- Monitoring and Logging Tools: Advanced downhole sensors and surface equipment for real-time data acquisition on temperature, pressure, lithology, and wellbore trajectory, crucial for decision-making.
Geothermal Well Drilling Rigs
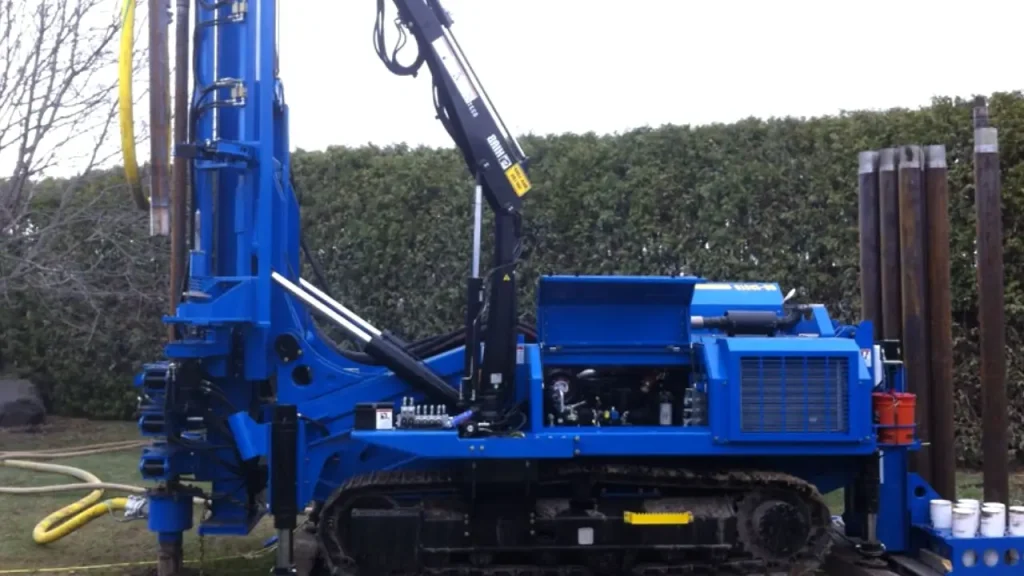
Geothermal well drilling rigs are specialized machines designed to penetrate the Earth’s crust to access geothermal energy resources.
Unlike standard oil and gas rigs, they often need to withstand extremely high temperatures, abrasive rock formations, and corrosive fluids found deep underground. These rigs are robust, capable of drilling to significant depths, and are equipped with advanced systems for precise control, fluid management, and safety, ensuring efficient and sustainable extraction of the Earth’s natural heat.
Their specific features depend on whether they are for shallow ground-source heat pump wells or deep, utility-scale power generation.
Key aspects of geothermal well drilling rigs include:
- High-Temperature Resistance: Components, particularly downhole tools and parts exposed to circulating fluids, are built with materials and seals that can endure temperatures often exceeding 200°C (392°F).
- Robust Pullback/Pulldown Capacity: Designed with significant force capabilities to manage heavy drill strings and casing through challenging rock formations at great depths.
- Advanced Mud Systems: Equipped with specialized mud pumps, fluid circulation systems, and often mud coolers to handle high-temperature drilling fluids and maintain wellbore stability.
- Precise Control Systems: Feature advanced instrumentation and controls for accurate drilling parameters, directional drilling capabilities, and real-time monitoring of downhole conditions.
- Safety Features: Incorporate specialized blowout preventers (BOPs) and well control systems designed for high-pressure, high-temperature geothermal environments to ensure operational safety.
- Mobility (for some types): Smaller rigs for ground-source heat pump applications are often truck-mounted or crawler-mounted for easier mobilization to various sites.
- Simultaneous Drilling Capabilities: Some advanced rigs can drill with both drill pipe and casing simultaneously, improving efficiency in certain geological conditions.
How Deep Do You Need to Drill for Geothermal?
The depth required for geothermal drilling varies significantly depending on the application. For residential and commercial heating and cooling systems, often called ground-source heat pumps, the wells are relatively shallow.
Horizontal loop systems typically involve digging trenches 6 to 8 feet deep, while vertical loop systems require boreholes ranging from 100 to 400 feet deep. These shallower depths are sufficient to access the stable underground temperatures that act as a heat source in winter and a heat sink in summer.
However, for large-scale electricity generation, which requires much higher temperatures (typically above 182°C or 360°F), geothermal wells must be drilled significantly deeper. These wells can extend anywhere from 3 kilometers (1.9 miles) to 10 kilometers (6.2 miles) or more into the Earth’s crust.
The exact depth depends on the geothermal gradient of the specific location and the temperature requirements of the power plant, with deeper wells generally incurring higher drilling costs but accessing hotter, more potent resources.
How to Drill Geothermal Well?
Drilling a geothermal well is a meticulous multi-step process, crucial for harnessing the Earth’s natural heat. It requires specialized techniques and equipment to ensure efficiency, safety, and long-term well integrity.
Step 1: Site Evaluation and Planning
Before any drilling begins, a thorough site evaluation is conducted. This includes geological surveys to understand subsurface formations, rock types, and potential heat resources. Planning involves determining the optimal well depth, diameter, and the most suitable drilling method for the specific geological conditions to maximize energy extraction.
This initial phase is critical for minimizing risks and optimizing the well’s future performance. It also helps in selecting the appropriate drilling rig and tools, as well as developing a comprehensive drilling program that considers environmental regulations and safety protocols.
Step 2: Conductor and Surface Casing Installation
Once the site is prepared and the rig is mobilized, the first physical step involves drilling a shallow, large-diameter hole. A conductor casing is then installed and cemented into place to stabilize the topsoil and prevent shallow formation collapse, acting as a guide for subsequent drilling.
Following the conductor, deeper surface casing is installed. This seals off near-surface aquifers, protecting groundwater from contamination and providing a stable foundation for the wellbore. This crucial step ensures environmental protection and structural integrity for the entire drilling operation.
Step 3: Intermediate and Production Drilling
After the surface casing is set, intermediate drilling proceeds to greater depths, progressively using smaller diameter bits. Intermediate casings are installed and cemented to stabilize various geological layers and isolate problematic zones like high-pressure formations, maintaining wellbore integrity.
Finally, production drilling reaches the hot geothermal reservoir. This often involves navigating challenging rock formations at high temperatures. Production casing is then run and cemented, creating the conduit for hot geothermal fluids or steam to flow to the surface for energy conversion.
Step 4: Well Completion and Testing
Upon reaching the target reservoir, the well is completed. This involves installing downhole equipment, such as liners or screens, depending on the fluid type and reservoir characteristics. The well is prepared for connection to the surface energy conversion system.
Finally, the completed well undergoes rigorous testing. Parameters such as temperature, pressure, and flow rates are measured to assess the reservoir’s productivity and sustainability. These tests are essential to confirm the well’s viability and to optimize its long-term performance within the geothermal energy system.
Conclusion
Geothermal drilling represents a critical frontier in our pursuit of sustainable energy. As explored in this ultimate guide, mastering its complexities, from initial surveys to well completion, is essential for successfully harnessing the Earth’s immense and renewable heat beneath our feet.
Embracing geothermal technology means investing in a future of clean energy, reducing our carbon footprint, and securing a reliable power source. It’s a testament to human ingenuity, pushing the boundaries of what’s possible in energy extraction and environmental stewardship.
For your geothermal drilling needs, look no further than Sinodrills. As a trusted provider in Qingdao, Shandong, China, we offer a comprehensive range of wholesale geothermal drilling tools designed for superior performance and durability, ensuring your projects achieve optimal results.