Drilling efficiency hinges on many factors, and at the heart of it lies the performance of PDC (Polycrystalline Diamond Compact) drill bits. But what exactly makes these bits so effective? It’s not just the diamond cutters; it’s the intricate interplay of various PDC bit components, each meticulously designed to optimize drilling speed, durability, and overall operational success in diverse geological formations.
Understanding the fundamental PDC bit components—from the robust bit body and strategically placed cutters to the sophisticated nozzle configurations and gage protection—is crucial for anyone involved in drilling operations. This blog will delve into how each part contributes to the bit’s ability to maximize penetration rates, minimize wear, and ultimately reduce drilling time and costs, forming the true foundation of drilling efficiency.
What are PDC Bits?
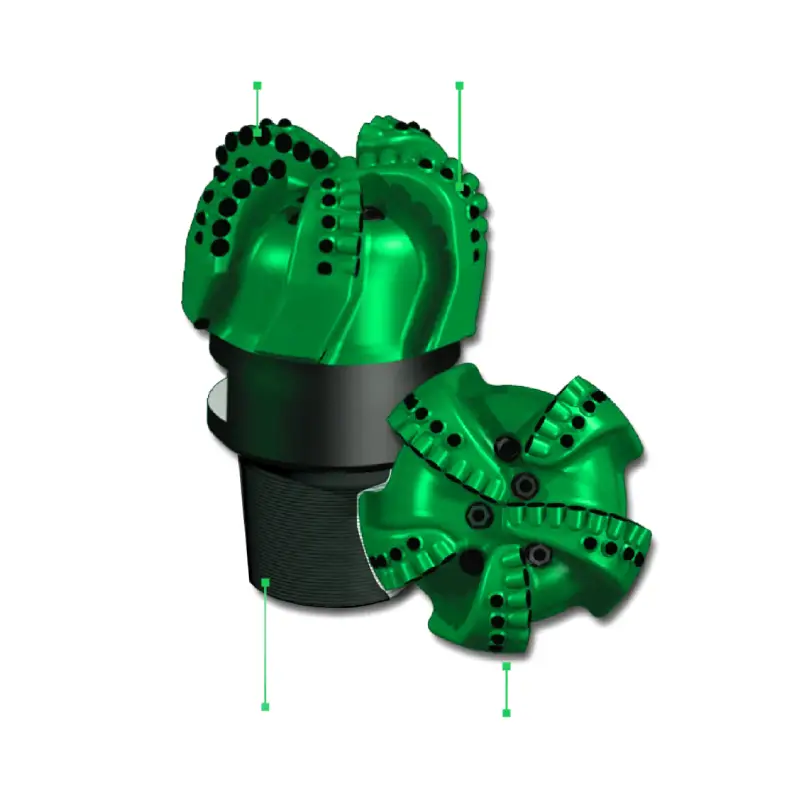
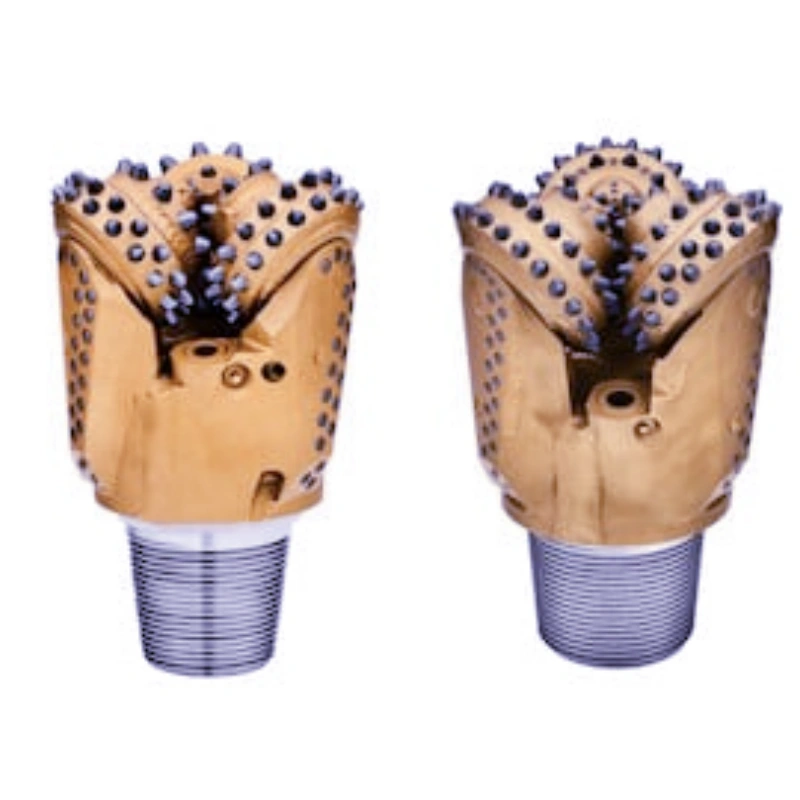
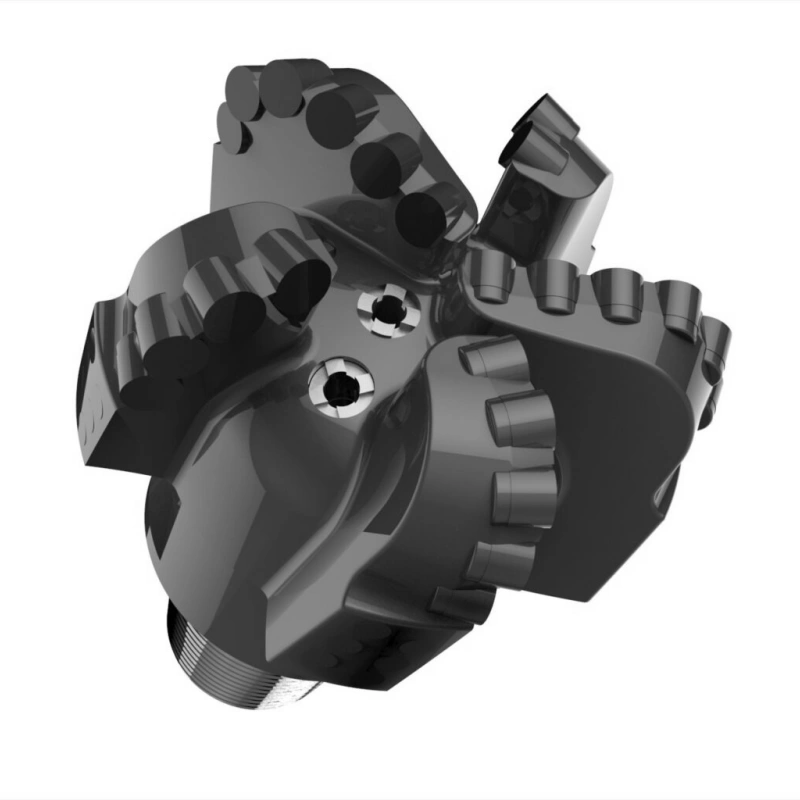
PDC (Polycrystalline Diamond Compact) bits are advanced drill bits widely used in various drilling industries, particularly in oil and gas, mining, and geothermal. They are characterized by their fixed-cutter design, meaning they have no moving parts like roller cones. Instead, they feature synthetic diamond cutters, known as PDC cutters, which are essentially small disks composed of a layer of polycrystalline diamond bonded to a tungsten carbide substrate.
These PDC drill bit cutters shear rock through a continuous scraping motion, providing superior drilling efficiency, faster penetration rates, and longer service life compared to conventional bits, especially in soft to medium-hard rock formations.
PDC Bit Components
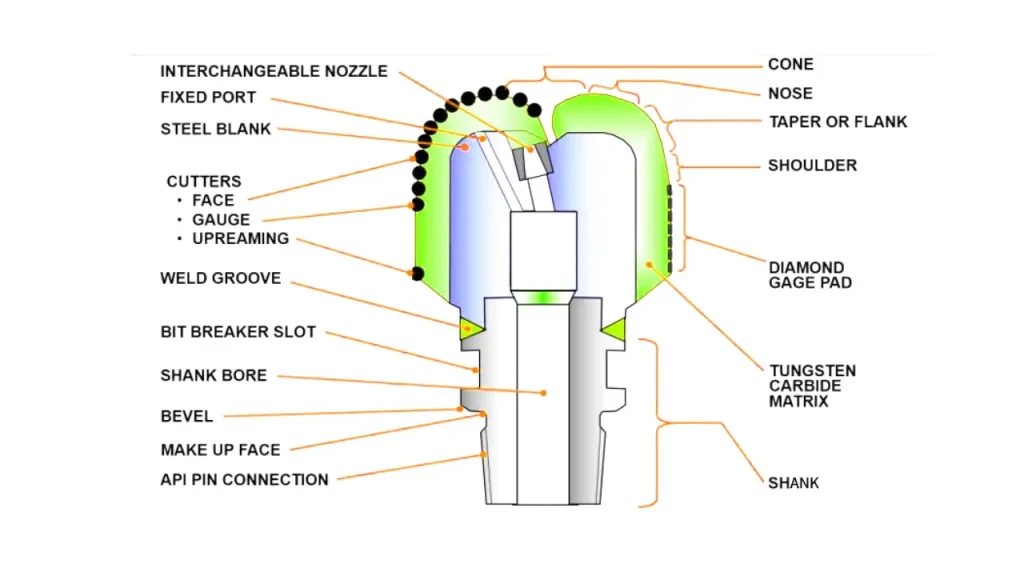
PDC drill bits are complex tools engineered for efficient drilling. Their performance hinges on the synergy of various specialized components. Understanding each part’s function is crucial for optimizing bit selection and maximizing drilling efficiency in diverse geological conditions.
Shank
The shank is the lower, cylindrical part of the PDC bit that connects to the drill string. It’s designed to withstand immense torque and axial loads, transmitting the rotational power from the rig down to the bit face. Key features like the API pin connection and make-up face ensure a secure and precise interface with the drilling assembly.
Bit Breaker Slot
Located on the shank, the bit breaker slot is a crucial feature for safe and efficient bit handling. This slot provides a secure point for gripping the bit with a bit breaker tool, allowing for easy and controlled make-up and break-out of the bit from the drill string without damaging the bit face or cutters.
Weld Groove
The weld groove is a channel or recess typically found on the bit body, designed to facilitate the welding process during manufacturing or repair. This groove ensures a strong and consistent weld, securely attaching different sections of the bit or reinforcing critical areas, contributing to the overall structural integrity and longevity of the PDC bit.
Cutters (Face, Gauge, Upreaming)
PDC cutters are the primary cutting elements of the bit, responsible for shearing rock.
- Face cutters are located on the bit’s front face, directly engaging the formation to create the bore.
- Gauge cutters are positioned on the outer diameter of the bit, ensuring the borehole maintains the correct diameter.
- Upreaming cutters (if present) are designed to enlarge the hole behind the primary cutting action, often used for stability or specific hole geometry requirements.
Steel Blank
The steel blank forms the foundational structure of a matrix body PDC bit. It’s a precisely machined steel core onto which the tungsten carbide matrix material and PDC cutters are hot-pressed or cast. The steel blank provides the structural integrity and connection points for the bit, ensuring its robustness during drilling.
Fixed Port / Interchangeable Nozzle
Nozzles are critical for fluid dynamics.
- Fixed ports are integral passages within the bit body that direct drilling fluid.
- Interchangeable nozzles are removable inserts that allow for customization of fluid flow. Both types serve to clean the bit face, cool the cutters, and evacuate cuttings from the wellbore, significantly impacting drilling efficiency and preventing bit balling.
Tungsten Carbide Matrix
The tungsten carbide matrix is a highly abrasion-resistant material that forms the body of many PDC bits. This composite material, often infiltrated with a binder, provides a robust and wear-resistant platform for mounting the PDC cutters. Its strength and durability are crucial for resisting erosion and protecting the cutters in abrasive formations.
Diamond Gage Pad
The diamond gage pad, located on the shoulder and flank of the bit, is a reinforced area designed to maintain the borehole’s precise diameter. These pads are impregnated with small diamonds or feature robust PDC material to resist wear and ensure the bit continues to cut a true-to-gauge hole throughout its operational life, preventing premature bit wear in this critical area.
Shoulder
The shoulder is the transitional area of the bit located between the cone/nose and the gauge section. It’s a critical zone for stabilizing the bit in the wellbore and often carries a significant number of cutters and gage pads. The design of the shoulder influences the bit’s steerability, stability, and its ability to maintain hole size.
Taper or Flank
The taper or flank refers to the conical or curved section of the bit that extends from the nose towards the shoulder. This area of the bit is responsible for progressively enlarging the pilot hole created by the nose and guiding the bit into the formation. The angle and design of the taper significantly impact the bit’s aggressiveness and cleaning capabilities.
Nose
The nose is the central, leading-edge section of the PDC bit that first engages the rock formation. It is typically the most aggressive part of the bit, designed for maximum penetration rate. The geometry and cutter placement on the nose are critical for initiating the cutting action and dictating the bit’s overall drilling performance in various rock types.
Cone
The cone refers to the overall conical shape of the bit face, extending from the nose outwards. While not a distinct physical component in the same way as a cutter, “cone” describes the general profile of the bit’s cutting structure. The design of the cone impacts how the bit distributes weight on bit and generates cutting forces across the formation.
PDC Drill Bit Design Features
PDC drill bit design incorporates several key features to optimize drilling performance and durability. These include:
- Bit Body Material: Can be either steel (for toughness and repairability) or matrix (for abrasion resistance in harder formations).
- Cutter Layout and Density: The number, size, and strategic placement of PDC cutters (face, gauge, upreaming) are crucial for optimizing cutting efficiency, cleaning, and wear resistance.
- Blade Count and Profile: The number of blades and their overall shape (e.g., flat, spiral, parabolic) affect stability, cutting action, and cuttings removal.
- Nozzle Placement and Size: Strategically positioned nozzles direct drilling fluid to cool cutters, clean the bit face, and transport cuttings, preventing bit balling.
- Gauge Protection: Features like diamond gage pads or robust PDC cutters on the bit’s outer diameter maintain hole size and extend bit life in abrasive formations.
- Junk Slot Area: Optimized spaces between blades allow for efficient evacuation of cuttings from the bit face, preventing recirculation and maximizing penetration rates.
Applications of PDC Drilling Bits
PDC drilling bits are highly versatile and widely adopted across various industries due to their exceptional efficiency and durability. Their design allows them to excel in a broad range of geological conditions, significantly improving penetration rates and reducing overall drilling costs. Key applications include:
- Oil and Gas Drilling: PDC bits are extensively used for drilling exploration and production wells, effectively penetrating diverse formations like shale, sandstone, and limestone for efficient hydrocarbon extraction.
- Geothermal Drilling: These bits are crucial in geothermal projects, where they withstand high temperatures and abrasive rock, ensuring reliable and extended performance in demanding underground conditions for energy production.
- Mining Operations: In the mining sector, PDC bits are utilized for exploration and production drilling, breaking through various hard rock formations to access valuable mineral resources with improved speed and longevity.
- Water Well Drilling: PDC bits prove highly efficient in drilling water wells, rapidly penetrating different soil and rock types, which significantly reduces the time and cost associated with groundwater access projects.
- Construction and Infrastructure: For civil engineering and construction, PDC bits are employed in drilling foundation piles, tunnels, and other structural elements, providing precise and rapid excavation in various ground conditions.
How to Choose Suitable PDC Drill Bits?
Choosing the most suitable PDC drill bit involves a careful assessment of several factors to optimize drilling performance and maximize bit life. The ideal selection balances the bit’s design features with the specific demands of the drilling environment. Considerations include:
- Formation Type: Identify the geological characteristics, including rock hardness, abrasiveness, and unconfined compressive strength, as these dictate the required cutter strength, bit body material (steel vs. matrix), and overall aggressiveness.
- Drilling Parameters: Consider available weight on bit (WOB), rotary speed (RPM), and flow rate, as these parameters influence bit design choices like cutter size, blade count, and nozzle configuration for optimal energy transfer.
- Hole Size and Profile: The desired bore diameter and any specific wellbore trajectory requirements (e.g., straight hole, directional drilling) will determine the bit’s gauge protection, shoulder design, and steerability features.
- Drilling Fluid Properties: Evaluate the type and properties of the drilling mud, as this impacts the selection of nozzle sizes and junk slot area to ensure effective cuttings removal and prevent bit balling in various fluid systems.
- Cost vs. Performance: Balance the initial cost of the bit with its expected performance, including penetration rate, footage drilled, and potential for reduced trip times, aiming for the most cost-effective solution over the entire drilling interval.
Conclusion
The journey through the world of PDC bit components reveals a complex synergy where each element plays a vital role in achieving peak drilling efficiency. We’ve explored how the design and material of the bit body, the precision of the PDC cutters, and the strategic placement of nozzles collectively dictate a bit’s performance. Optimizing these components is key to tackling challenging formations and reducing overall drilling costs, making every run count.
Ultimately, the success of your drilling project often comes down to the quality and suitability of your PDC drill bits. Investing in high-performance bits means less downtime, faster operations, and a more profitable bottom line. Recognizing the critical impact of each component empowers you to make informed decisions when selecting your drilling tools, ensuring you’re always equipped for success.
For top-tier PDC drill bits or a comprehensive range of drilling tools, consider Sinodrills. We offer wholesale solutions designed to meet the rigorous demands of modern drilling, providing the reliability and efficiency your operations require. Partner with us for cutting-edge technology and robust tools that will keep your drilling projects on track and within budget.