PDC bit cutters stand as the indispensable workhorses of modern drilling, tirelessly carving through challenging rock formations to access vital energy resources. Their continuous evolution and innovative design are pivotal in driving superior performance, significantly enhancing drilling speed and overall operational efficiency in demanding environments worldwide.
This blog post delves deep into the cutting-edge innovations that are fundamentally transforming PDC bit technology. We will explore how these remarkable advancements directly contribute to achieving superior durability, significantly extended bit life, and remarkably increased penetration rates, thereby revolutionizing the entire drilling landscape for unprecedented success.
What are PDC Bit Cutters?

PDC (Polycrystalline Diamond Compact) bit cutters are the primary cutting elements on PDC drill bits, designed to drill through various rock formations efficiently. Each cutter consists of a thin layer of synthetic diamond grit, manufactured at high pressure and temperature, bonded to a tungsten carbide substrate.
This unique construction provides exceptional hardness, abrasion resistance, and thermal stability, enabling PDC bits to achieve high penetration rates and extended tool life in demanding drilling environments.
Different Types of PDC Bit Cutters
PDC bit cutters are the critical components responsible for the drilling action. Their design and condition significantly impact drilling efficiency and bit longevity. Understanding the various types of wear and damage they sustain is essential for effective dull grading and optimizing future bit performance.
Bond Failure (BF)
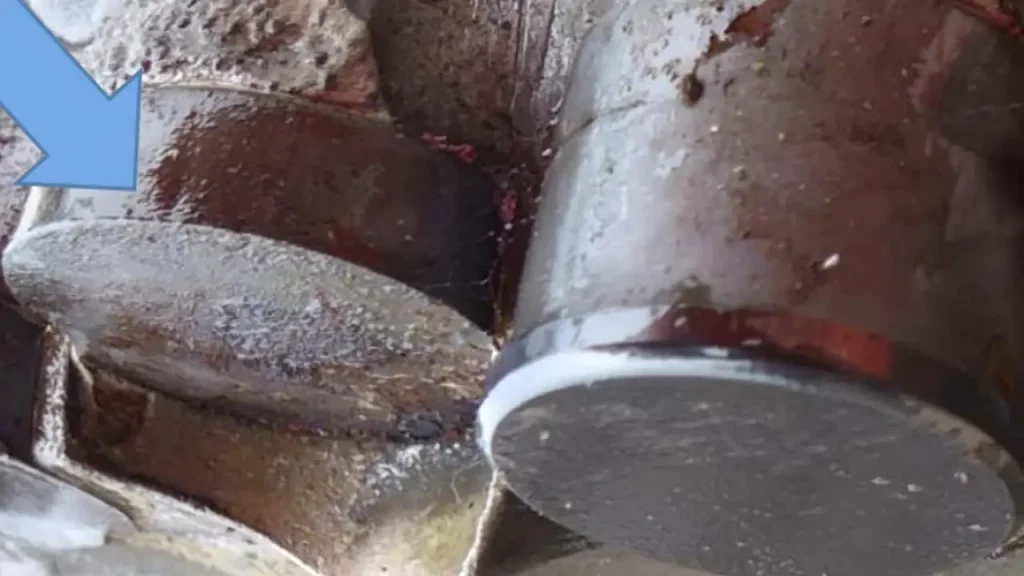
Bond failure (BF) specifically refers to the structural separation occurring either between two pieces of the carbide substrate itself, or crucially, the delamination between the diamond layer and its underlying carbide substrate. It can also manifest as spalling, where thin layers of the diamond separate from the cutter face.
This type of failure indicates a fundamental issue with the integrity of the cutter’s construction or its attachment to the bit body. Bond failure often leads to rapid cutter degradation or loss, severely impacting the bit’s ability to maintain a consistent rate of penetration and requiring prompt corrective action.
Broken Cutter (BT)
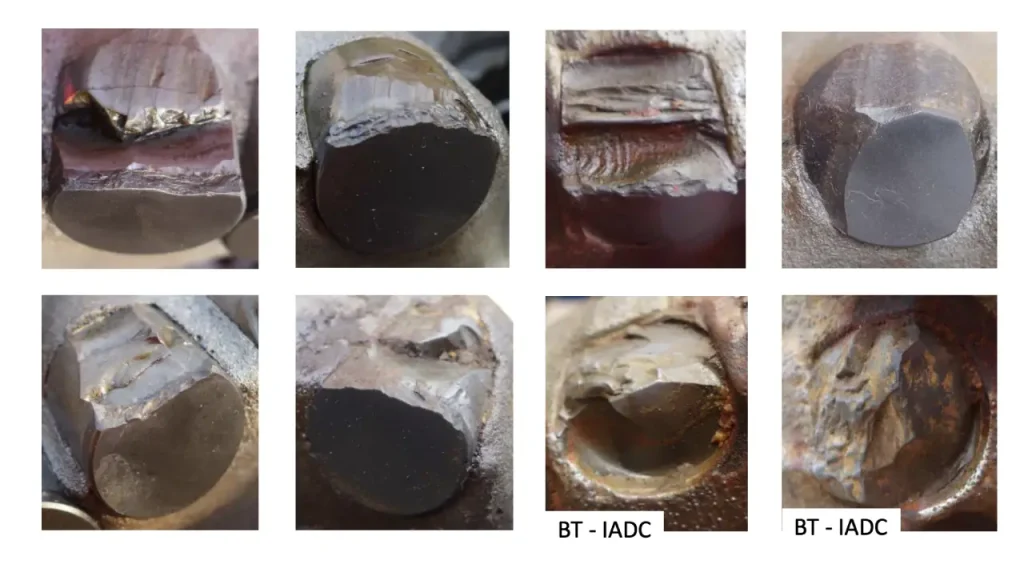
Broken cutters (BT) represent a more severe form of damage where the fracture extends completely through the diamond table and deeply into the tungsten carbide substrate. This substantial structural failure is commonly caused by severe impact events, excessive torque fluctuations, or the destructive forces of bit whirl.
The presence of broken cutters signifies a significant loss of the bit’s primary cutting structure, severely compromising its cutting efficiency and overall stability. This type of damage often leads to a rapid decline in penetration rate and can necessitate premature pulling of the bit from the wellbore, incurring additional operational costs.
Chipped Cutter (CT)
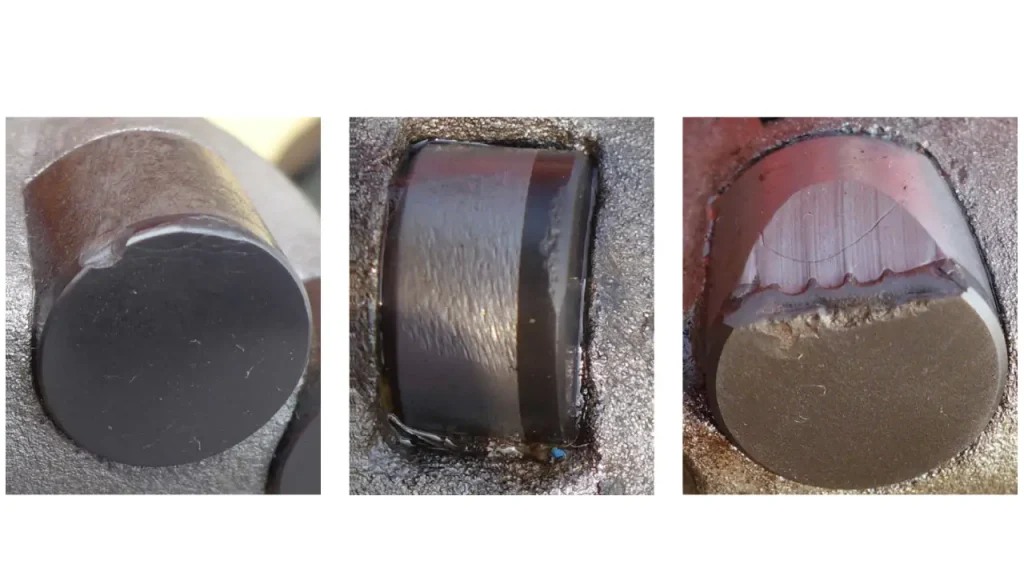
A chipped cutter (CT) refers to minor breakage occurring specifically on the diamond edge of the cutter, without the damage propagating significantly into the carbide substrate. This type of localized damage is typically a result of sudden impact, localized stress, or encountering harder inclusions within the formation.
Identifying chipped cutters during dull grading is important because it can be an early indicator of issues such as bit vibration, stick-slip, or encountering unexpected lithology. Addressing the root cause of chipping can prevent more severe damage, like broken cutters, and help maintain consistent drilling performance throughout the run.
Erosion (ER)
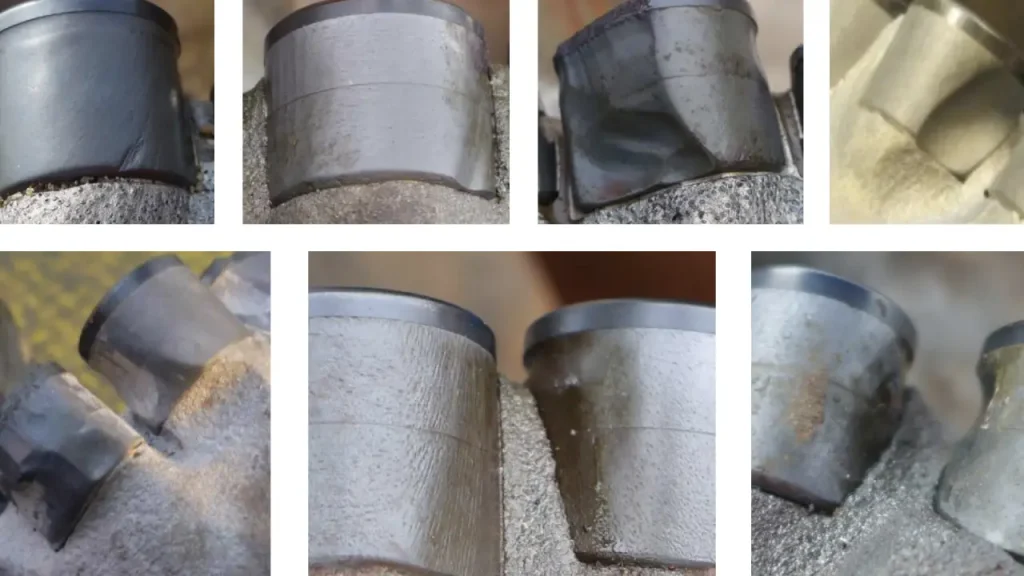
Erosion (ER) on a PDC bit cutter refers to the abrasive wear caused by the flow of drilling fluids and entrained solids over the cutter surface. This process gradually removes material, often appearing as a polished or washed-out area, particularly in areas with high fluid velocity around the cutter and bit body.
Significant erosion can reduce the effectiveness of the cutter, altering its geometry and compromising its ability to efficiently shear rock. Monitoring erosion helps in optimizing drilling fluid properties and hydraulic designs, such as nozzle configuration, to minimize abrasive wear and extend overall bit life.
Flat Crested Wear (FC)
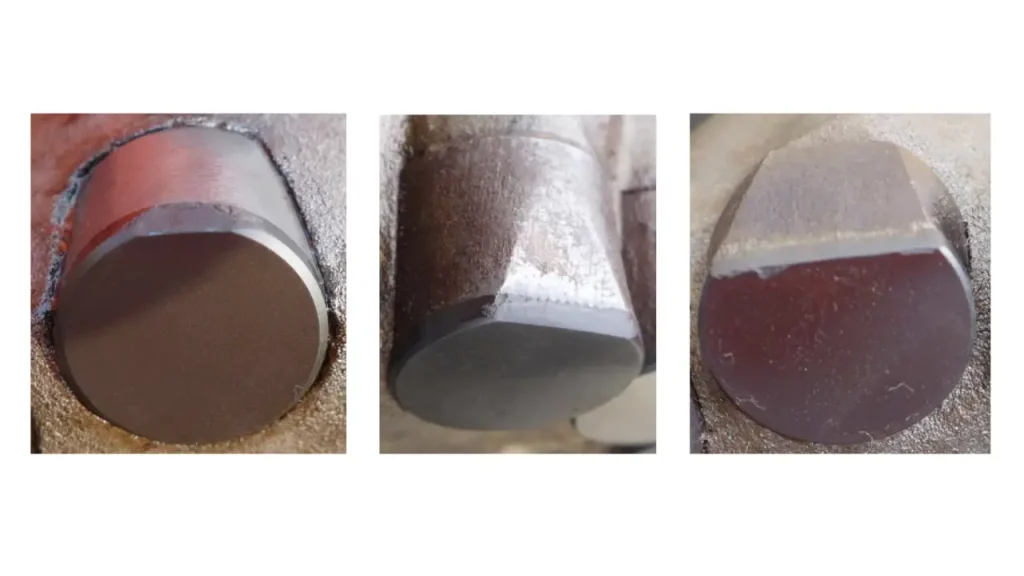
Flat crested wear (FC) is a specific type of cutter degradation characterized by a smooth, uniform wear flat across the diamond table, which may sometimes extend into the underlying carbide substrate. Unlike general wear, FC suggests a consistent and perhaps high-pressure contact between the cutter and the rock, leading to a steady, even abrasion over time.
While FC can be categorized under general worn cutters, its distinct planar nature provides specific insights into drilling dynamics. It often indicates stable drilling without excessive impact or vibration, allowing the bit to achieve its design potential for sustained cutting. Monitoring FC helps optimize weight on bit and rotary speed for maximum efficiency.
Heat Checking (HC)
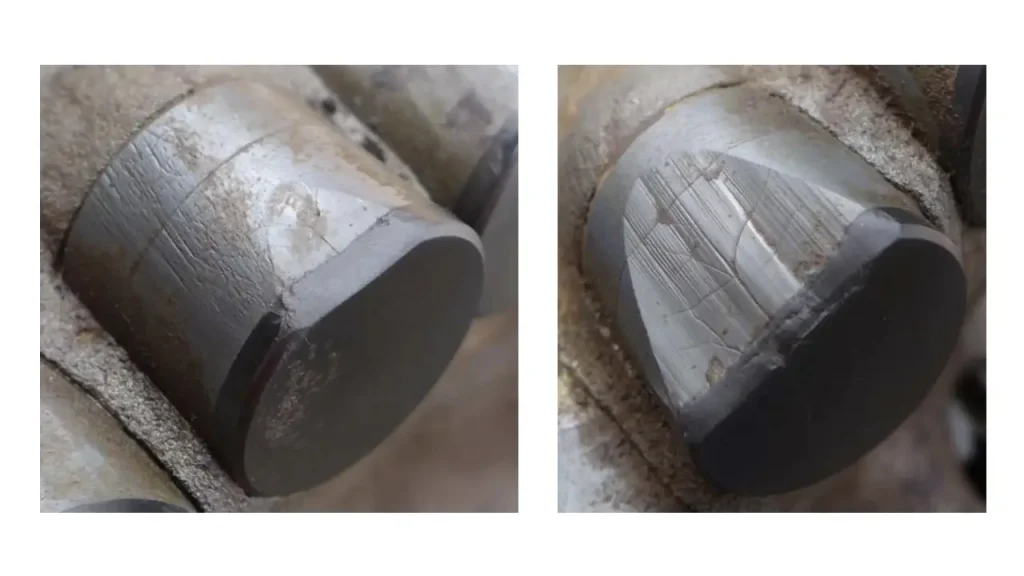
Heat checking (HC) manifests as a pattern of fine cracks on the surface of the carbide substrate, frequently accompanied by a distinct wear flat on the diamond layer. This damage is primarily attributed to excessive heat generation at the cutter-rock interface, often due to insufficient cooling by drilling fluid or high frictional forces.
The development of heat checking indicates thermal degradation, which can weaken the cutter’s integrity and accelerate further wear or breakage. Effective mitigation strategies, such as optimizing hydraulics for better cooling and adjusting drilling parameters to reduce friction, are crucial to prevent HC and extend bit life.
Lost Cutter (LT)
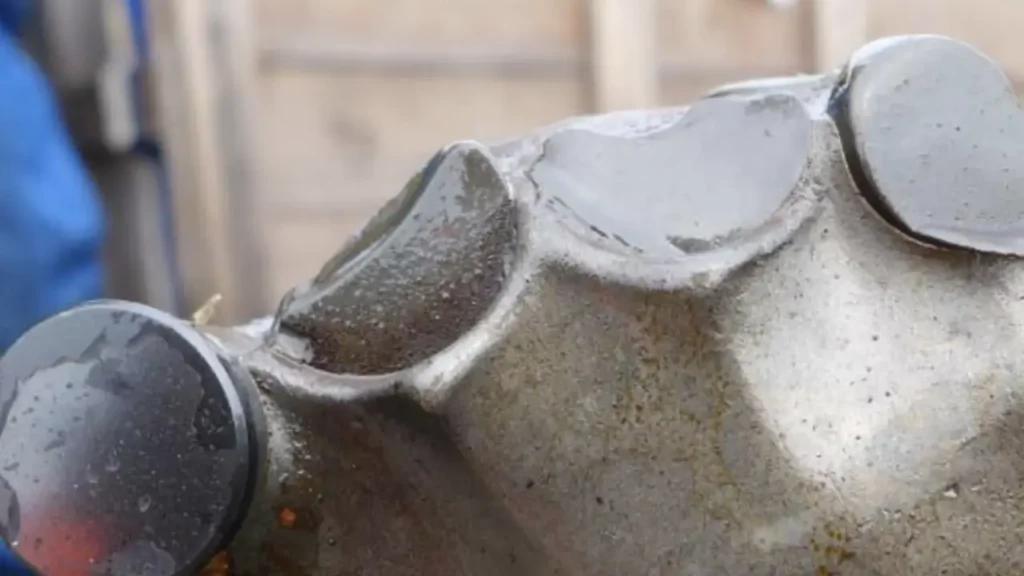
A lost cutter (LT) describes the complete absence of a cutting element from its designated pocket on the bit body. This critical failure can occur due to various reasons, including a complete bond failure between the diamond layer and its substrate, or a severe impact event that forcibly dislodges the entire cutter from its seat.
The loss of cutters significantly compromises the bit’s balance, cutting efficiency, and ability to maintain hole gauge. Each missing cutter creates an uncompensated void, leading to increased load on remaining cutters and potential bit instability, often necessitating an immediate bit pull and replacement.
No Characteristic (NO)
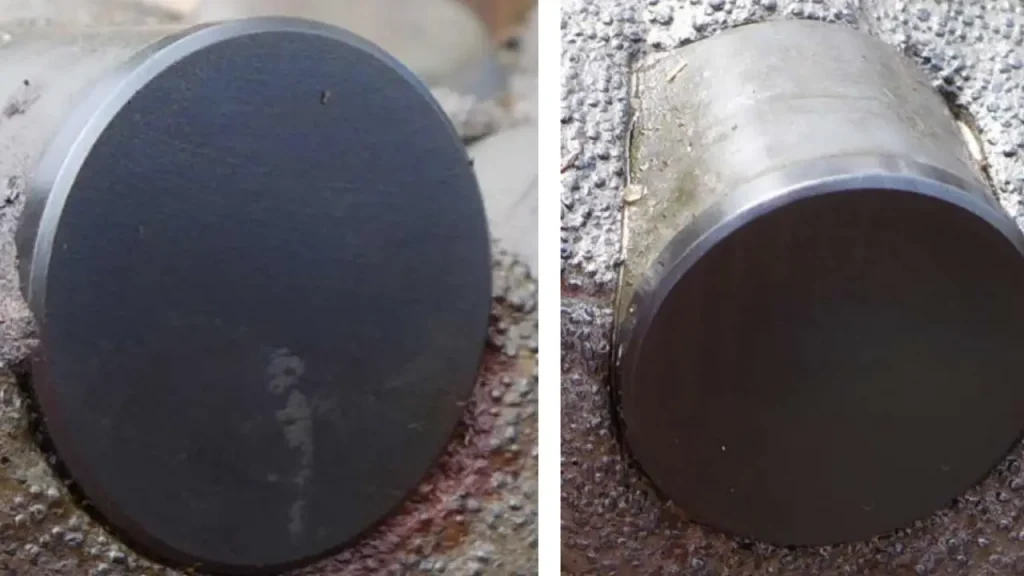
“No Characteristic” (NO) in dull grading indicates that the bit was pulled without exhibiting any significant or identifiable wear patterns that would typically be coded as a primary dull characteristic. This suggests the bit may have been pulled for reasons unrelated to bit wear itself, such as reaching total depth, a planned formation change, or issues with the drilling rig or downhole equipment.
When “NO” is the primary dull characteristic, it implies the cutters are largely intact and show minimal degradation. This is often a desirable outcome, as it indicates that the bit had more drilling potential remaining and could have been run longer if not for external operational factors, representing efficient use of the tool.
Rounded Gauge (RG)
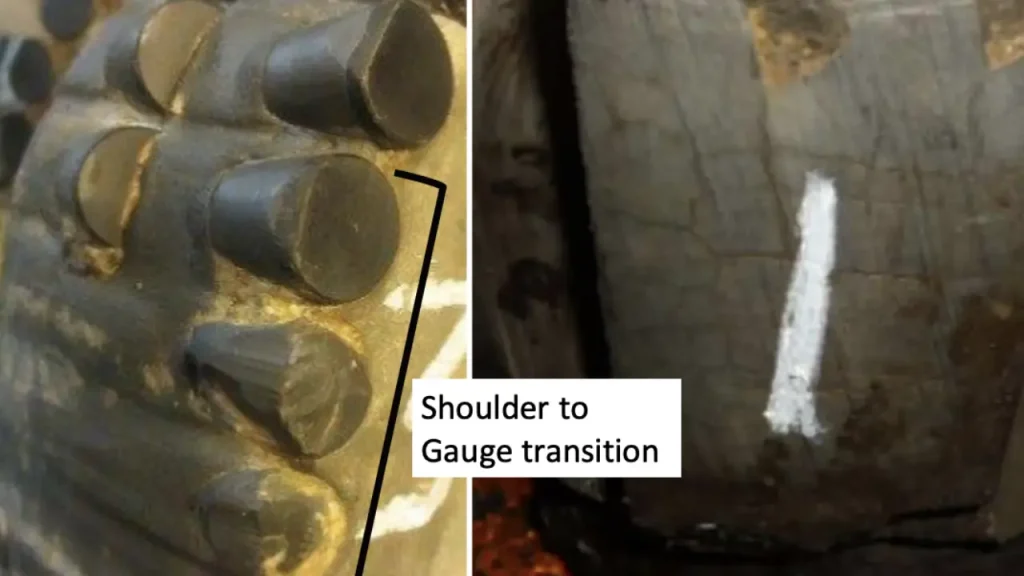
Rounded gauge (RG) describes a significant amount of diamond loss and wear specifically in the upper shoulder to gauge transition area of the bit, resulting in a distinctly rounded profile of the gauge pads. While not a “cutter” in the same sense as the primary cutting elements, it’s a critical dull characteristic affecting hole quality.
The presence of a rounded gauge indicates substantial abrasive wear along the wellbore wall. This can lead to the bit drilling an undersized hole, requiring additional reaming passes, or impacting subsequent casing runs. Accurately assessing RG helps in selecting bits with more robust gauge protection for abrasive formations.
Worn Cutters (WT)
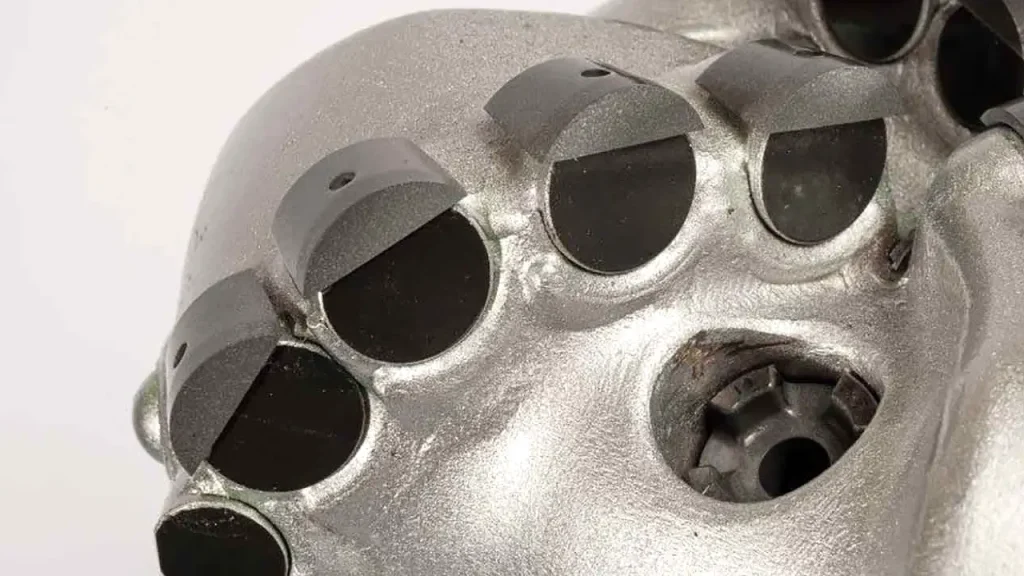
Worn cutters, denoted as WT in dull grading, represent a general and widespread degradation of the diamond cutting face. This includes non-planar wear across the diamond table, or a combination of various other damages such as chipping, breaking, flat cresting, or erosion. This collective damage indicates the cutter has undergone significant abrasive contact and fatigue from its prolonged interaction with the downhole formation.
Identifying worn cutters is crucial for assessing the overall lifespan achieved by the bit and evaluating the effectiveness of the chosen drilling parameters. Widespread WT often suggests that the bit operated efficiently for a considerable duration but has reached its natural wear limit, prompting an informed decision on bit pull or adjustments for subsequent runs.
Unofficial: Delamination (DL)
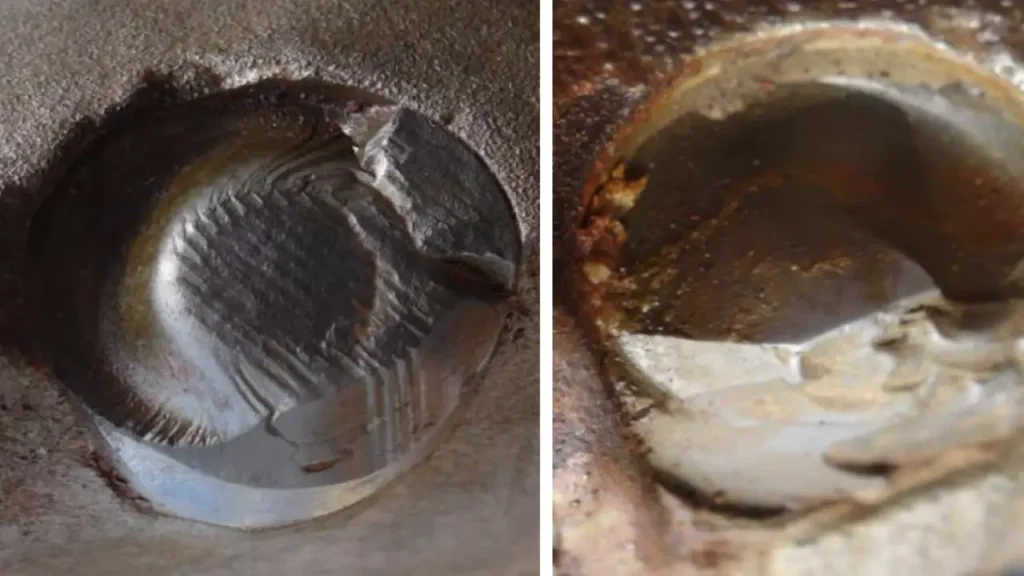
Delamination (DL), often considered an unofficial dull code in some industry practices, specifically describes the separation of the diamond layer from its underlying tungsten carbide substrate. This critical structural failure compromises the integrity of the cutter, preventing its effective rock-cutting action and potentially leading to its premature loss from the bit face.
While closely related to general bond failure, delamination focuses on the distinct interface between the diamond and carbide. Identifying DL helps pinpoint issues in cutter manufacturing quality or extreme downhole conditions causing the adhesion breakdown, guiding improvements in both bit design and operational parameters.
Unofficial: Spalled Cutter (SP)
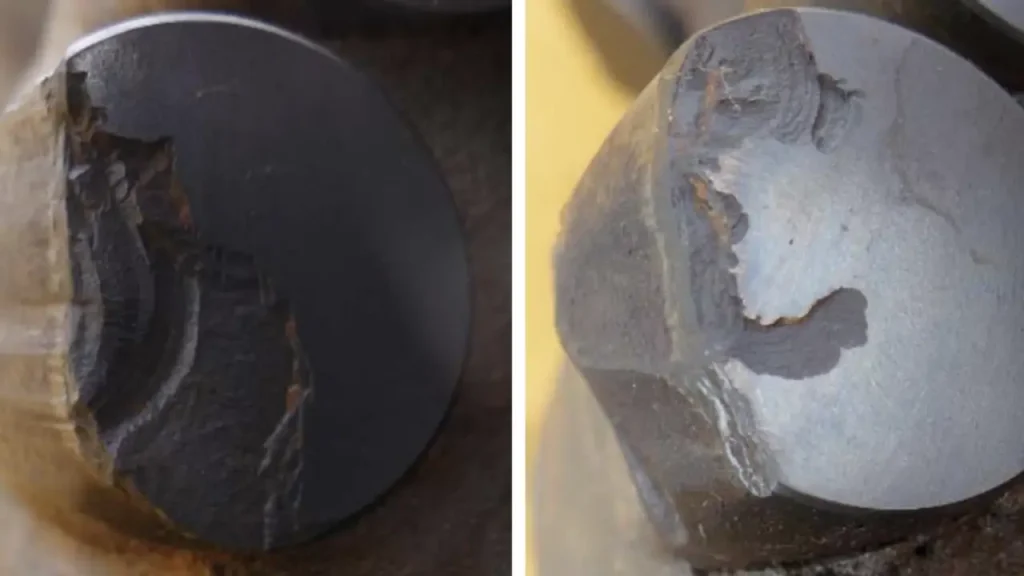
Spalled cutter (SP), another unofficial dull code used in some detailed grading systems, refers to the breaking away of thin layers or small fragments of the diamond material from the cutter’s active face. This often appears as shallow craters or pits on the diamond table, distinct from larger chips or breaks.
Spalling typically occurs due to localized stress concentrations, thermal cycling, or micro-fracturing within the diamond layer itself. While initially minor, extensive spalling can significantly reduce the cutter’s efficiency and aggressive shearing action, impacting penetration rates and overall bit performance over the drilling interval.
Here is a table summarizing the different types of PDC drill bit cutter dull characteristics:
Code | Characteristic | Description |
BF | Bond Failure | Structural separation within the cutter, either between carbide pieces or delamination between diamond and substrate, leading to reduced cutting efficiency or cutter loss. |
BT | Broken Cutter | Severe fracture damage extending through the diamond table and into the carbide substrate, often caused by significant impact or excessive forces, leading to substantial loss of cutting structure. |
CT | Chipped Cutter | Minor breakage on the diamond edge of the cutter, without deep penetration into the carbide. Typically results from impact or localized stress, potentially indicating drilling dynamics issues. |
ER | Erosion | Abrasive wear on the cutter surface caused by the flow of drilling fluids and entrained solids. Appears as polished or washed-out areas, gradually reducing cutter effectiveness. |
FC | Flat Crested Wear | Smooth, uniform wear flat across the diamond table, sometimes extending into the carbide. Indicates consistent, even abrasion under stable drilling conditions. |
HC | Heat Checking | Fine cracks on the carbide substrate, often with a wear flat on the diamond. Caused by excessive heat due to insufficient cooling or high friction, leading to thermal degradation. |
LT | Lost Cutter | The complete absence of a cutting element from its pocket on the bit body, resulting from bond failure or severe impact, compromising bit balance and cutting efficiency. |
NO | No Characteristic | Indicates the bit was pulled for reasons other than significant cutter wear, such as reaching total depth or a formation change, with cutters showing minimal degradation. |
RG | Rounded Gauge | Significant diamond loss and wear in the upper shoulder to gauge transition area, resulting in a rounded profile of the gauge pads. Affects hole size and stability. |
WT | Worn Cutters | General degradation with non-planar wear, or a combination of other damage types across the diamond face. Indicates widespread abrasion and fatigue from prolonged contact with the formation. |
DL | Delamination | (Unofficial) Specific separation of the diamond layer from its tungsten carbide substrate. A critical structural failure that leads to loss of cutting action. |
SP | Spalled Cutter | (Unofficial) Breaking away of thin layers or small fragments of diamond material from the cutter’s face, appearing as shallow craters or pits, reducing cutting aggression. |
Fixed Cutter Drill Bits vs Roller Cone
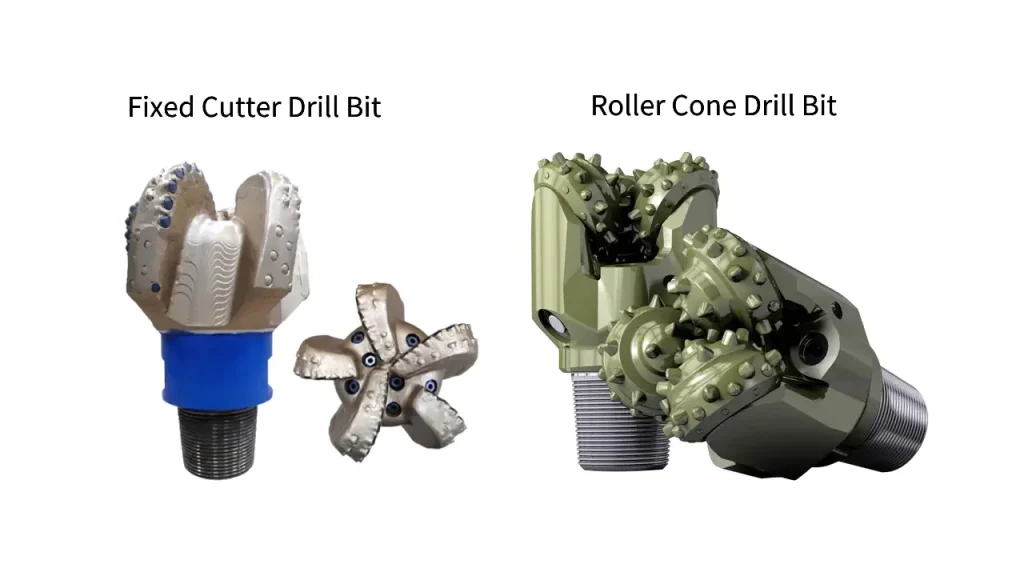
Fixed cutter drill bits and roller cone drill bits are the two main types of drill bits used in various drilling applications, particularly in the oil and gas industry. While both are designed to excavate rock, they achieve this through fundamentally different mechanisms, leading to distinct advantages and disadvantages depending on the drilling environment.
Cutting Mechanism
Fixed cutter drill bits, most commonly Polycrystalline Diamond Compact (PDC) bits, feature stationary cutting elements that shear and scrape the rock as the entire bit rotates. The diamond cutters are fixed to the bit body, providing a continuous cutting action. In contrast, roller cone drill bits have two or three conical rollers that rotate independently on bearings as the bit turns. These cones are equipped with teeth or inserts that crush, gouge, and chip the rock.
Moving Parts
A key difference is the presence of moving parts. Fixed cutter bits have no moving mechanical components, which simplifies their design and reduces potential failure points related to bearings or seals. Roller cone bits, however, rely on the rotation of their cones, which are mounted on bearings. These moving parts are subject to wear and can be a limiting factor in their lifespan, especially in harsh downhole conditions.
Formation Suitability
Fixed cutter bits are generally preferred in softer to medium-hard, homogeneous formations where their shearing action is highly efficient, leading to high rates of penetration. They excel in shales, sandstones, and carbonates. Roller cone bits are more versatile and perform well across a wider range of formations, from very soft to extremely hard and abrasive rocks, including those with interbedded layers, where their crushing action is more effective.
Rate of Penetration (ROP)
In formations where fixed cutter bits are well-suited, they typically achieve higher rates of penetration due to their continuous cutting action and superior cleaning capabilities. This can significantly reduce drilling time. While roller cone bits can also achieve good ROP, especially in harder formations, their intermittent crushing action might result in a slower overall ROP compared to fixed cutter bits in optimal conditions for the latter.
Durability and Lifespan
Fixed cutter bits often boast exceptional durability and a longer lifespan in their ideal drilling environments, frequently allowing operators to drill entire sections without needing to pull the bit out of the hole. This is largely due to the robust nature of their fixed diamond cutters and the absence of complex moving parts. Roller cone bits, while durable, can have their lifespan limited by the wear of their bearings and seals, especially in high-temperature or high-impact drilling scenarios.
How to Choose PDC Bit Cutters?
Choosing the right PDC bit cutters is crucial for optimizing drilling performance and extending bit life. Selection involves considering various factors to match the cutter’s properties with downhole conditions:
- Formation Hardness and Abrasivity: Select tougher, more abrasion-resistant cutters for hard, abrasive rock, and sharper, more aggressive cutters for softer formations.
- Impact Resistance: For interbedded or fractured formations prone to vibration, choose cutters with enhanced impact resistance to prevent chipping or breaking.
- Thermal Stability: In high-temperature drilling environments or when drilling very hard rock, cutters with superior thermal stability prevent heat-checking and delamination.
- Cutter Size and Density: Larger cutters can be more durable, while smaller, more numerous cutters offer higher rates of penetration in certain applications. The density should match the required aggressiveness.
- Application-Specific Design: Consider the overall bit design, including blade count and junk slot area, as these interact with cutter placement and type.
Conclusion
Ultimately, the relentless pace of innovation in PDC bit cutters is profoundly redefining the very capabilities of modern drilling. These significant advancements consistently deliver faster, remarkably more durable, and ultimately highly cost-effective operations, directly boosting your project’s overall efficiency and profitability in challenging conditions.
Leveraging these transformative technological leaps is crucial for profoundly improving all aspects of your drilling programs. Companies can achieve unprecedented levels of reliability and exceptional performance by diligently selecting and deploying optimal PDC bit tools precisely engineered for their specific geological challenges and operational requirements.
For truly superior performance and to acquire wholesale PDC drill bits that fully embody all these cutting-edge innovations, we urge you to trust Sinodrills. We are committed to consistently providing the highest quality, exceptional durability, and reliable performance that your most demanding drilling projects unequivocally require, ensuring your success.