Have you ever wondered what goes into creating the sophisticated drill bits that bore through miles of rock to access our planet’s resources? It’s a complex blend of engineering, material science, and a deep understanding of geological forces.
At the heart of efficient and durable drilling lies exceptional PDC bit design. This isn’t just about sticking some diamonds onto a metal body; it’s a meticulous process of optimizing every element to maximize performance in the harshest environments. Join us as we explore the fascinating world of PDC bit design, uncovering the key principles and innovations that make these tools so effective.
What is the PDC Cutters’ Role in Bit Design?
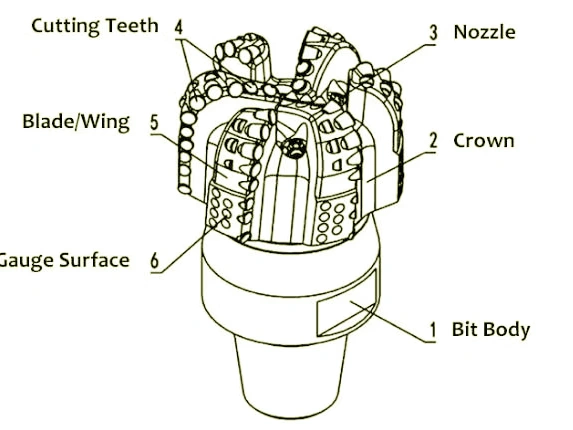
Before we delve into the intricacies of the entire bit, it’s crucial to understand that the PDC cutters are the heart of any PDC drill bit design. These polycrystalline diamond compacts are what actually shear the rock, and their specific characteristics significantly influence the overall performance of the bit. The quality, size, shape, and even the manufacturing process of these cutters are fundamental considerations from the very first stages of design.
Our engineers spend considerable time evaluating the latest advancements in PDC cutter technology. We examine factors such as diamond layer thickness, carbide substrate properties, and the interface bonding strength. Different applications demand different cutter properties – for instance, a cutter designed for highly abrasive formations will differ from one optimized for softer, more ductile rocks. This deep understanding of cutter capabilities allows us to select the ideal elements that will form the aggressive cutting structure of our PDC bits.
How Does Bit Profile Impact PDC Bit Design?
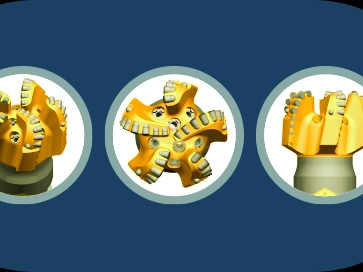
The bit profile is arguably the most fundamental aspect of PDC bit design, dictating how the bit interacts with the rock formation as it drills. It’s the overall shape of the bit from its cutting face to the gauge, influencing everything from stability and steerability to cleaning efficiency and rate of penetration (ROP). A well-designed profile ensures smooth drilling and optimal performance across various rock types.
There are several common bit profiles, each suited for different drilling conditions:
- Short Profile (Aggressive/Fast)
- Advantages: High ROP in soft to medium formations, good for vertical drilling.
- Disadvantages: Less stable in harder formations, can be prone to stick-slip.
- Medium Profile (Versatile)
- Advantages: Good balance of ROP and stability, suitable for a wider range of formations, effective for directional drilling.
- Disadvantages: May not be optimized for extremely hard or soft conditions.
- Long Profile (Stable/Steerable)
- Advantages: Excellent stability and steerability, ideal for directional drilling and interbedded formations, good for maintaining gauge.
- Disadvantages: Lower ROP in very soft formations, which can lead to increased torque.
Our PDC bit design process involves careful selection and refinement of the bit profile based on the target formation, desired well trajectory, and drilling objectives. We use advanced simulation software to model how different profiles will perform under various downhole conditions, ensuring we select the most efficient shape for each specific application.
Optimizing Cutter Layout and Density in PDC Bit Design
The strategic arrangement and number of PDC cutters on the bit face, known as cutter layout and density, are paramount in optimizing the PDC bit design for specific drilling challenges. This aspect directly impacts the bit’s ability to shear rock effectively, manage torque, and resist wear. It’s a delicate balance between maximizing cutting efficiency and ensuring durability.
Our engineers meticulously plan the placement of each cutter, considering factors like:
- Face Coverage: Ensuring uniform coverage of the bit face to prevent uncut rock sections.
- Redundancy: Providing backup cutters in case of damage to primary cutters, extending bit life.
- Gauge Protection: Strategically placing cutters on the outer diameter to maintain hole size.
- Interaction with Formation: Optimizing the back-rake and side-rake angles of the cutters for efficient rock shearing and reduced friction.
High cutter density is often preferred for drilling harder, more abrasive formations, as it distributes the load over more cutters, reducing individual cutter wear. Conversely, lower cutter density can be more effective in softer formations, allowing for deeper cutter penetration and higher ROP. The table below illustrates some general guidelines:
Feature | High Cutter Density | Low Cutter Density |
Application | Hard, Abrasive Formations; High-Torque Control | Soft, Ductile Formations; High ROP |
Wear Resistance | Excellent | Moderate |
ROP Potential | Moderate to High | High |
Torque Control | Generally more stable | Can be more reactive |
Cleaning Needs | Requires robust hydraulics for efficient cleaning | Less critical, but still important |
This intricate planning ensures that every part of the bit face contributes effectively to the drilling process, providing maximum efficiency and longevity for our PDC bit design.
Why Blade Count is Key in PDC Bit Design
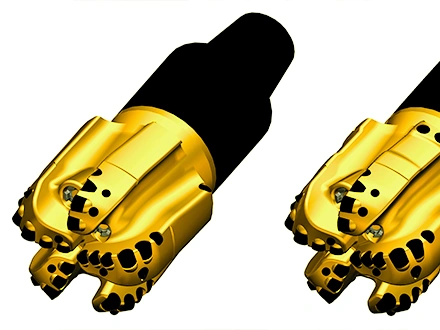
The blade count and configuration form the structural framework of the PDC bit design, providing support for the cutters and defining the junk slots that facilitate cuttings removal. The number of blades, their height, and their specific arrangement profoundly impact the bit’s stability, cleaning efficiency, and overall durability in various downhole conditions.
We carefully determine the optimal number of blades based on the anticipated formation hardness and the need for stability versus cutting efficiency. Bits designed for softer formations might feature fewer, taller blades to allow for larger junk slots and better cuttings evacuation. In contrast, bits for harder, more abrasive formations often have more blades to provide increased structural support and distribute the cutting forces more evenly across a larger area, protecting the bit body.
- Fewer Blades:
- Advantages: Larger junk slots for better cleaning in soft, sticky formations; higher ROP potential in soft rock.
- Disadvantages: Less stable, higher individual cutter loading, less wear resistance in hard formations.
- More Blades:
- Advantages: Increased stability, better wear resistance, more cutters for harder formations, improved gauge protection.
- Disadvantages: Smaller junk slots, potentially reduced cleaning efficiency in sticky formations, lower ROP in very soft rock.
The configuration of the blades, including their spiral angle and face shape, is also crucial for directing cuttings efficiently into the junk slots and away from the bit face. This thoughtful approach in PDC bit design ensures that the bit not only cuts effectively but also cleans itself optimally, preventing balling and maximizing drilling efficiency.
How Does Hydraulic System Design Affect PDC Bits?
The hydraulic system design is an often-underestimated yet critical component of PDC bit design, directly influencing the bit’s cleaning efficiency, cutter cooling, and overall rate of penetration. Without an optimized hydraulic system, even the most advanced cutters and robust body designs will underperform. It’s all about effectively managing the drilling fluid.
Our engineers meticulously design the internal fluid passages and nozzle placement to ensure optimal mud flow. Key elements include:
- Nozzle Count and Placement: Strategic positioning of nozzles to direct high-velocity fluid streams onto the cutters and the bottom of the hole. This washes away cuttings and cools the PDC cutters, extending their life.
- Nozzle Size: Carefully selected based on pump capacity and desired pressure drop across the bit. Larger nozzles provide higher flow rates, while smaller nozzles offer higher jet impact force.
- Junk Slot Area: Ensuring sufficient space between blades for efficient evacuation of cuttings from the bit face into the annulus. Inadequate junk slot area can lead to bit balling, where cuttings pack around the bit, severely reducing ROP.
- Internal Flow Paths: Designing smooth, unobstructed pathways for the drilling fluid to minimize pressure losses and maximize hydraulic energy delivery at the bit face.
An efficient hydraulic system prevents regrinding of cuttings, reduces wear on the cutters, and maintains a clean bottom hole, all of which contribute to higher ROP and extended bit life. This integrated approach to PDC bit design highlights our commitment to holistic performance.
Why is Gauge Protection Vital in PDC Bit Design?
Maintaining the integrity and precise diameter of the drilled borehole, known as the “gauge,” is paramount for seamless drilling operations and subsequent wellbore activities. This makes gauge protection and stability a critical element in advanced PDC bit design. Without adequate gauge protection, the bit can drill an undersized hole, leading to costly reaming operations and potential wellbore instability.
Our design incorporates several features to ensure the bit maintains gauge and provides stability during drilling:
- Gauge Pads: The non-cutting, outer diameter sections of the bit that maintain contact with the wellbore wall. These are often reinforced with:
- PDC Gauge Cutters: Small PDC inserts embedded directly into the gauge pads for superior abrasion resistance. These are especially effective in abrasive formations.
- Tungsten Carbide Inserts: Durable carbide inserts provide additional wear resistance to the gauge pads, particularly on steel-body bits.
- Hardfacing: Application of highly wear-resistant materials to the gauge pads through welding, offering an additional layer of protection.
- Stabilizer Blades: Some PDC bit designs incorporate extra-long gauge pads or separate stabilizer blades to enhance bit stability, especially in directional drilling applications or interbedded formations. This helps minimize vibration and reduce torque fluctuations.
- Spiral Gauge: A spiral design of the gauge pads can improve cuttings evacuation along the wellbore and provide smoother rotational contact, further enhancing stability.
By meticulously designing these elements, we ensure our PDC drill bits not only cut efficiently but also maintain a consistent and accurate borehole, contributing significantly to overall drilling success and wellbore quality.
What Materials are Used in PDC Bit Design?
The choice of material for the bit body is a foundational decision in PDC bit design, directly impacting the bit’s structural integrity, wear resistance, and ability to withstand the harsh downhole environment. The primary options are matrix body and steel body, each with distinct characteristics that lend themselves to different drilling applications.
Matrix Body PDC Bits:
- Composition: Made from tungsten carbide powder infiltrated with a molten copper-based alloy in a high-temperature process.
- Advantages:
- Excellent erosion resistance: Ideal for highly abrasive formations, resisting wear from cuttings and fluid flow.
- Superior wear resistance: The hard tungsten carbide matrix provides exceptional resistance to abrasive wear.
- High compressive strength: Very robust and can withstand significant downhole forces.
- Complex geometries: Allows for intricate junk slot designs and internal fluid passages.
- Ideal Applications: Hard, abrasive formations; high-temperature drilling; minimizing washouts.
Steel Body PDC Bits:
- Composition: Machined from high-strength alloy steel forgings, then heat-treated for enhanced mechanical properties.
- Advantages:
- High toughness and ductility: More resistant to impact damage and brittle fracture, making them suitable for interbedded or impact-prone formations.
- Repairability: Easier to repair and re-tip cutters due to the weldable nature of steel.
- Lower manufacturing cost: Generally more economical to produce.
- Slim hole applications: Can often be manufactured with smaller body diameters.
- Ideal Applications: Softer to medium formations; applications where impact is a concern; situations requiring frequent repair or re-tipping.
Our PDC bit design team carefully evaluates the anticipated drilling conditions-including formation hardness, abrasiveness, and potential for impact-to select the most appropriate bit body material. This strategic material selection ensures the bit’s resilience and longevity in its intended application.
Conclusion
The ultimate goal of PDC bit design remains consistent: to maximize drilling efficiency, extend bit life, and reduce overall drilling costs. As we continue to innovate, we are not just designing tools; we are shaping the future of energy exploration and resource extraction.
What aspects of PDC bit design do you find most fascinating? Share your thoughts!