Have you ever wondered how the drill bits that bore through solid rock are made? We’re not talking about your average home improvement drill bits, but the powerful Polycrystalline Diamond Compact (PDC) bits used in oil and gas, geothermal, and mining industries. These engineering marvels are essential for extracting the resources that power our lives. Join us as we delve into the fascinating and intricate PDC bit manufacturing process, exploring each step that goes into creating these incredibly durable and efficient drilling tools.
What is PDC Cutters
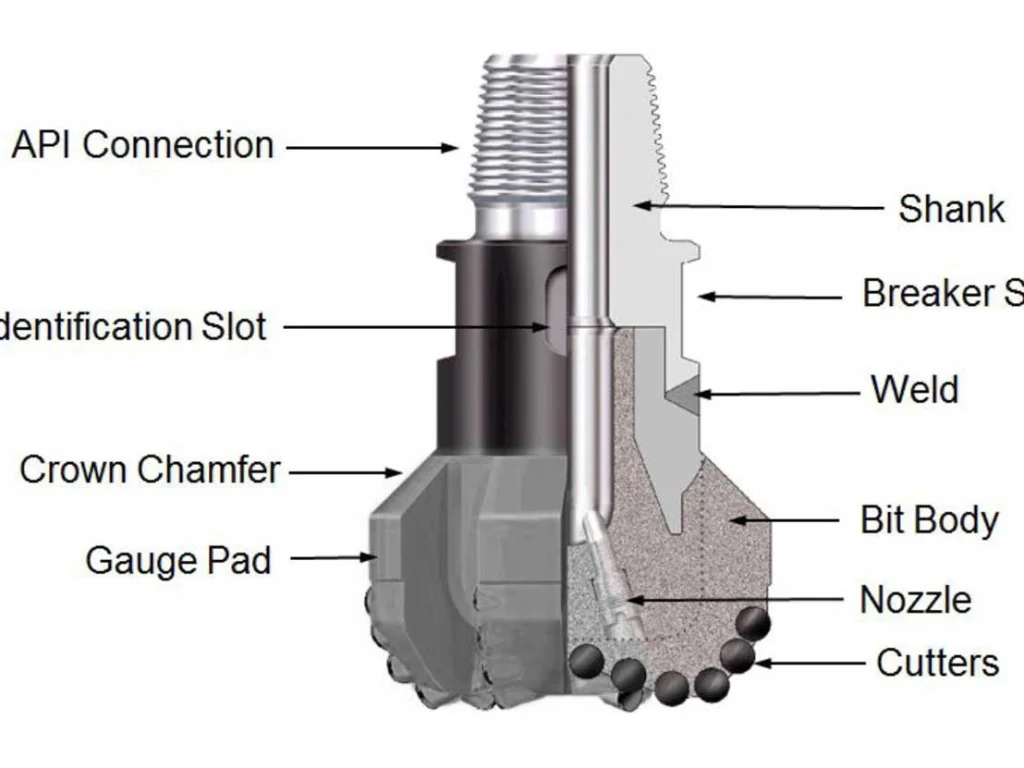
Before we dive into the manufacturing process, it’s crucial to understand the star of the show: the PDC cutters. These aren’t just any diamonds; they’re synthetic diamonds bonded to a tungsten carbide substrate, offering an exceptional combination of hardness and impact resistance. The quality and design of these cutters are paramount to a PDC bit’s performance.
The creation of PDC cutters is a sophisticated process in itself, involving high-pressure, high-temperature (HPHT) presses that simulate the conditions deep within the Earth. Tungsten carbide slugs and diamond particles are placed in these presses, and under immense pressure and heat, the diamond grains bond together and to the carbide substrate. This unique structure gives PDC cutters their superior abrasive wear resistance and thermal stability, making them ideal for challenging drilling environments.
PDC Bit Manufacturing Process: How to Make PDC Drill Bits?
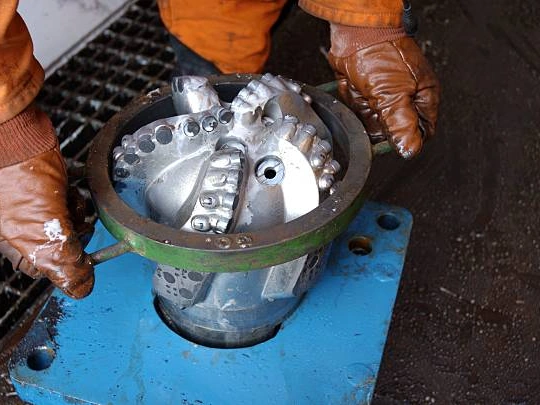
Step 1: Design and Engineering
Every great product begins with a meticulous design, and PDC drill bits are no exception. This initial stage of the PDC bit manufacturing process is critical, as it lays the foundation for the bit’s overall performance, durability, and efficiency. Our engineers leverage advanced software and extensive experience to create a blueprint tailored to specific drilling challenges.
We start by analyzing geological data, formation characteristics, and client requirements. Factors like rock type, well trajectory, and desired rate of penetration (ROP) all play a crucial role in shaping the bit’s design. Utilizing sophisticated Computer-Aided Design (CAD) and Computational Fluid Dynamics (CFD) software, we simulate fluid flow, cutting removal, and cutter engagement.
This allows us to optimize critical design elements such as the bit’s profile, blade count, cutter layout, and nozzle placement, ensuring the final product will excel in its intended application.
Step 2: What is PDC material?
The body of a PDC bit is its backbone, and selecting the appropriate material is a vital step in the PDC bit manufacturing process. The choice of material directly impacts the bit’s strength, wear resistance, and ability to withstand the harsh downhole environment. We typically use two primary types of bit bodies: matrix and steel.
Matrix Body Bits
Matrix body bits are made from a tungsten carbide powder metallurgical process. This involves pressing tungsten carbide powder with a binder and then infiltrating it with a molten copper alloy in a high-temperature furnace.
Advantages of Matrix Body Bits:
- High erosion resistance: Excellent for abrasive formations and minimizing washouts.
- Good wear resistance: The hard matrix material resists wear from cuttings.
- Ability to incorporate complex geometries: Allows for intricate designs with optimized junk slot areas.
- Suitable for high-temperature applications: The manufacturing process results in a very robust body.
Steel Body Bits
Steel body bits are machined from high-strength alloy steel. These bits offer a different set of advantages, particularly in terms of repairability and toughness.
Advantages of Steel Body Bits:
- Higher toughness and ductility: Less prone to brittle fracture in impact-prone applications.
- Easier to repair and re-tip: Steel can be welded and machined more readily.
- Lower manufacturing cost: Generally more economical to produce than matrix bits.
- Can be more easily modified: Design changes or repairs can be done with relative ease.
Feature | Description |
Material | High-Strength Alloy Steel |
Manufacturing | Machining from Solid Forging |
Key Advantage | High Toughness, Ductility, and Repairability |
Ideal Application | Softer to Medium Formations; Applications Requiring Frequent Repair |
Our selection between matrix and steel bodies is always driven by the specific drilling application, aiming to provide the most effective and economical solution for our clients.
Step 3: Body Fabrication
With the design finalized and the material chosen, the next critical phase in the PDC bit manufacturing process is fabricating the bit body. This stage differs significantly depending on whether we are producing a matrix or a steel body bit. Both methods demand precision and specialized equipment to ensure the final product meets our stringent quality standards.
For Matrix Body Bits:
The fabrication of matrix bodies is a complex powder metallurgy process. First, a graphite mold is created based on the bit’s design. This mold precisely defines the bit’s profile, blade geometry, and internal fluid passages. Tungsten carbide powder, along with a binder, is then vibrated and packed into this mold. Once filled, the mold is placed in a high-temperature, high-pressure furnace.
A copper-based alloy is melted and infiltrated into the packed tungsten carbide powder. This infiltration process creates a dense, strong, and highly wear-resistant matrix composite structure. After cooling, the graphite mold is removed, revealing the rough bit body.
For Steel Body Bits:
Steel body bits begin as solid forgings of high-strength alloy steel. These forgings are then meticulously machined using advanced Computer Numerical Control (CNC) machines. The CNC machines precisely cut and shape the steel forging according to the detailed CAD design, creating the bit’s blades, junk slots, and internal fluid channels.
This process allows for high precision and repeatability, ensuring each steel body bit conforms to exact specifications. After machining, the steel body typically undergoes heat treatment to enhance its mechanical properties, such as hardness and toughness.
Step 4: Cutter Brazing – Uniting the Diamond Power
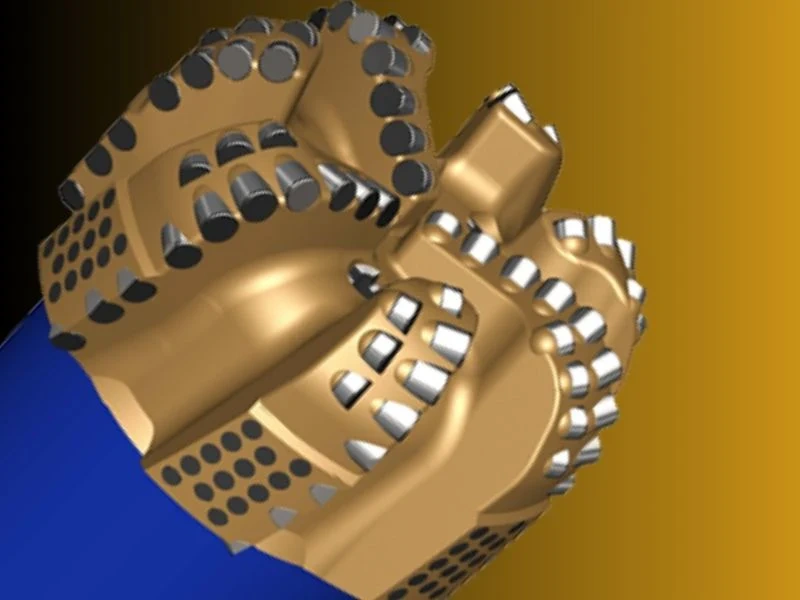
The PDC cutter brazing process is arguably one of the most critical steps in the entire PDC bit manufacturing process. This is where the powerful PDC cutters are permanently attached to the bit body, transforming it into a functional drilling tool. The success of this step dictates the bit’s performance and longevity in the challenging downhole environment.
We employ a specialized high-temperature brazing process to achieve a strong metallurgical bond between the PDC cutters and the bit body. Each PDC cutter is carefully positioned and then brazed into precisely machined pockets on the bit blades.
The brazing alloy, typically a silver-based material, flows into the joint between the cutter and the pocket when heated, creating a robust connection. Careful control of temperature, time, and atmosphere within the brazing furnace is essential to prevent damage to the PDC cutters while ensuring a strong bond that can withstand the extreme forces encountered during drilling.
Step 5: Nozzle Installation and Fluid Course Optimization
Efficient drilling isn’t just about cutting rock; it’s also about effectively removing the cuttings from the wellbore and cooling the PDC cutters. This is where the strategic placement of nozzles and optimization of fluid courses come into play, a crucial aspect of the PDC bit manufacturing process. The design of the internal fluid passages and the selection of nozzle sizes directly impact hydraulic efficiency and bit cleaning.
We meticulously install specialized nozzles, typically made from tungsten carbide for their wear resistance, into designated ports on the bit face. These nozzles direct the drilling fluid (mud) at high velocity onto the cutters and the bottom of the hole.
The size and angle of the nozzles are carefully chosen during the design phase to optimize fluid flow, ensuring effective cuttings removal (which prevents regrinding) and efficient cooling of the PDC cutters (extending their lifespan). Proper hydraulic design prevents bit balling and enhances the overall drilling efficiency, leading to faster penetration rates and reduced operational costs.
Step 6: Gauge Protection and Wear Resistance Enhancements
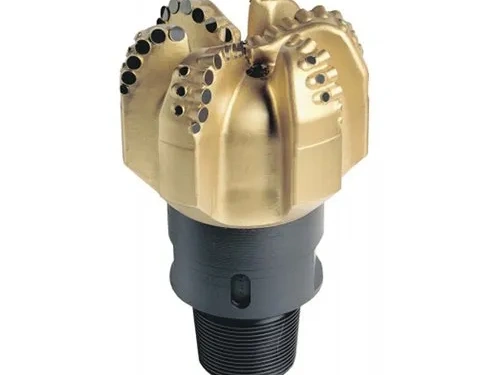
Maintaining the drilled hole’s diameter, or “gauge,” is essential for smooth drilling operations and subsequent wellbore activities. Therefore, incorporating robust gauge protection and wear resistance enhancements is a vital part of the PDC bit manufacturing process. These features prevent premature wear on the bit’s outer diameter, ensuring the wellbore remains at the desired size.
We often integrate additional wear-resistant elements along the bit’s gauge pads. This can include:
- PDC gauge cutters: Small PDC inserts embedded along the gauge pads provide superior abrasion resistance, ensuring the bit maintains its diameter.
- Tungsten carbide inserts: These durable inserts further enhance the wear resistance of the steel or matrix body in critical areas.
- Hardfacing materials: Applying a layer of highly wear-resistant material, often using specialized welding techniques, to exposed areas of the bit body that are prone to abrasion.
These enhancements extend the bit’s operational life, reduce the need for frequent bit changes, and contribute to a more efficient and cost-effective drilling program.
Step 7: Inspection and Quality Control
Quality is critical in drilling. Every PDC bit leaving our facility undergoes strict inspections to meet our high standards, ensuring reliability and client trust.
Our multi-faceted checks include visual inspections for surface flaws, proper cutter placement and brazing; advanced NDT like ultrasonic and dye penetrant tests to detect hidden internal issues; and precise measurements of critical dimensions (diameter, cutter protrusion, blade profile) against specs. Only after passing all these does a PDC bit ship for field use.
Step 8: Finishing and Packaging
The final stages of the PDC bit manufacturing process involve meticulous finishing touches and secure packaging, ensuring that the bit arrives at its destination in perfect condition, ready for immediate deployment. These steps might seem minor, but they are crucial for protecting our precision-engineered tools.
Finishing involves cleaning the bit thoroughly to remove any residues from the manufacturing process. We may also apply a protective coating to prevent corrosion during storage and transport. Each bit is then carefully packed into custom-designed protective containers or crates. These containers are robust and often include cushioning materials to prevent any damage during transit, safeguarding the bit’s delicate cutters and critical surfaces. Proper packaging also includes clear labeling with essential information such as bit size, type, and serial number, facilitating easy identification and inventory management at the rig site.
Conclusion
The PDC bit manufacturing process is constantly evolving. As drilling challenges become more complex and the demand for efficiency increases, we are continuously investing in research and development to push the boundaries of what’s possible. From advanced material science to artificial intelligence-driven design optimization, the future holds exciting possibilities.
Do you have any more questions about PDC bits or the drilling industry? We’d love to hear from you!