The profile of a PDC drill bit is a critical design element that profoundly influences its drilling performance, stability, and suitability for different geological formations. Understanding the distinctions between common profiles, particularly flat and parabolic designs, is essential for optimizing drilling efficiency and extending bit life.
This blog will delve into the characteristics of the flat PDC bit profile and the parabolic PDC bit profile, exploring how their unique geometries affect penetration rates, directional control, and resistance to wear. By comparing these two prominent designs, we aim to guide you in selecting the ideal bit profile for your specific drilling challenges.
What is PDC Bit Profile?
The PDC bit profile refers to the overall shape or contour of the bit’s cutting face, extending from the nose to the gauge pads. This three-dimensional design dictates how the bit interacts with the rock formation, influencing factors such as cutting aggressiveness, stability, directional control, and cleaning efficiency.
Different PDC drill bit profiles, like flat or parabolic, are engineered to optimize performance for specific drilling conditions, rock types, and desired wellbore trajectories by strategically distributing cutters and managing drilling fluid flow.
Flat PDC Bit Profile
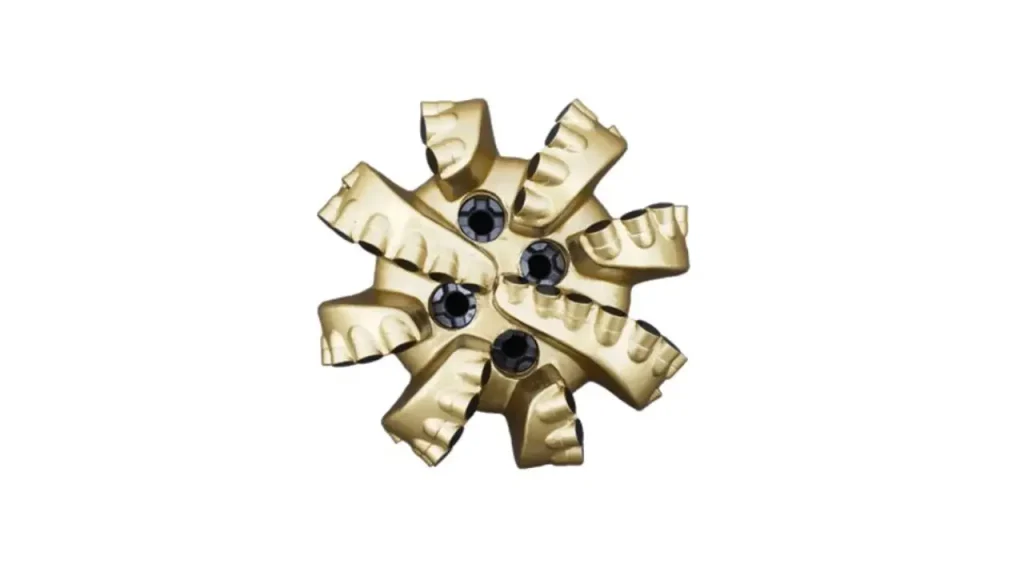
Flat PDC bit profiles are characterized by a relatively shallow, flatter face, with cutters distributed more evenly across the bit’s entire cutting surface rather than concentrated at the center. This design promotes a more consistent weight distribution across the cutters and typically features a larger number of blades.
- Characteristics: Features a shallow profile with cutters spread across a broader, flatter face.
- Performance: Generally provides excellent stability and durability in abrasive or interbedded formations due to more balanced load distribution.
- Applications: Best suited for drilling harder, more abrasive, or interbedded formations where bit stability and wear resistance are prioritized over maximum penetration rate.
- Cuttings Removal: The larger junk slots often associated with flatter profiles aid in efficient cuttings evacuation, reducing the risk of bit balling in sticky formations.
Parabolic PDC Bit Profile
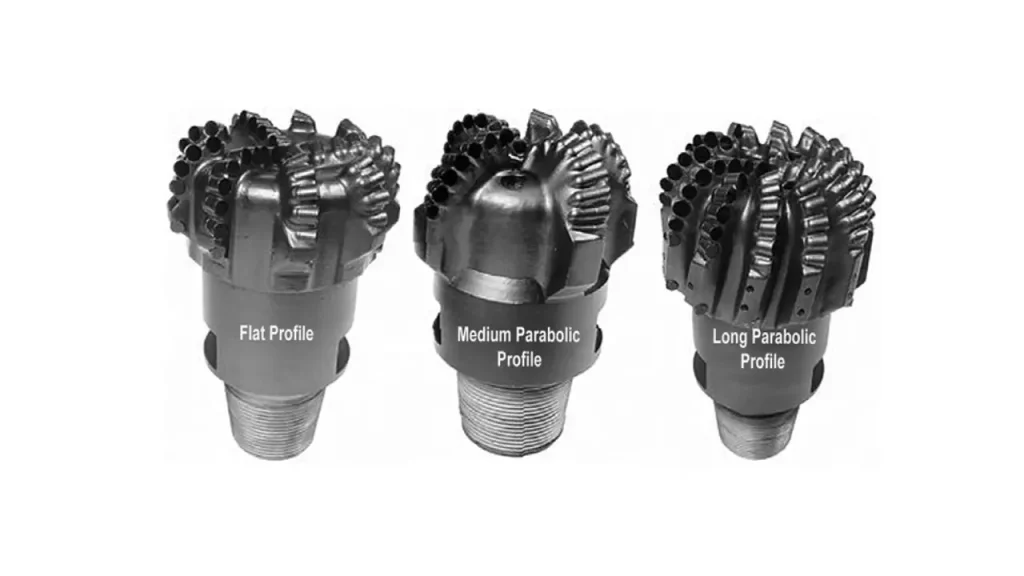
Parabolic PDC bit profiles feature a more aggressive, curved shape, with the cutting structure designed to concentrate more force on the center or nose of the bit. This creates a higher point of attack, often leading to increased penetration rates, particularly in softer or medium formations.
- Characteristics: Distinguished by a deep, curved profile that focuses cutting action towards the bit’s center or nose.
- Performance: Excels at achieving high rates of penetration (ROP) in softer to medium-hard, non-abrasive formations due to its aggressive cutting action.
- Applications: Ideal for drilling applications where maximizing ROP is the primary goal, especially in consistent, less abrasive rock types like shales or soft sandstones.
- Directional Control: The more aggressive nose and deeper cone can sometimes offer better directional response, making them suitable for certain steerable drilling applications.
Flat vs Parabolic PDC Bit
Choosing between a flat and parabolic PDC bit profile is crucial for optimizing drilling performance. Each design offers distinct advantages and disadvantages depending on the specific drilling environment and objectives. Understanding these differences is key to making an informed decision.
Here are key aspects to compare when considering flat versus parabolic PDC bit profiles:
- Penetration Rate (ROP): Parabolic profiles generally offer higher penetration rates in softer to medium formations due to their aggressive, concentrated cutting action at the bit’s nose, efficiently breaking rock and advancing the wellbore faster.
- Stability and Durability: Flat profiles typically provide superior stability and durability, especially in harder or interbedded formations. Their broader cutting face distributes impact loads more evenly, reducing localized wear and extending bit life.
- Abrasiveness Resistance: Flat profiles tend to be more resistant to abrasive wear due to a larger number of cutters exposed to the formation and a more uniform load distribution, which prevents rapid dulling of individual cutters.
- Directional Control: Parabolic profiles can offer better directional control, particularly for steerable applications, as their more aggressive nose facilitates quicker changes in wellbore trajectory and easier steering through formations.
- Cuttings Removal (Cleaning): Flat profiles often feature larger junk slot areas, which are more effective at clearing cuttings, especially in sticky or high-volume drilling, preventing bit balling and maintaining optimal drilling efficiency.
Aspect | Flat PDC Bit Profile | Parabolic PDC Bit Profile |
Penetration Rate (ROP) | Generally lower ROP, but more consistent in varying formations due to broader contact. | Higher ROP in softer to medium formations due to aggressive, concentrated cutting action at the nose. |
Stability & Durability | Higher stability and durability, especially in hard/interbedded formations, as loads are evenly distributed. | Potentially lower stability in very hard formations; can be more susceptible to vibration due to aggressive nose. |
Abrasiveness Resistance | Superior resistance to abrasive wear due to more uniform load distribution across numerous cutters. | Can experience faster wear in highly abrasive formations due to more concentrated cutter loading. |
Directional Control | Generally less aggressive for directional changes; prefers drilling straight holes due to stable, broad contact. | Often provides better directional control, facilitating quicker wellbore trajectory changes and steering. |
Cuttings Removal (Cleaning) | Larger junk slots typically found in flat profiles improve cuttings evacuation and reduce bit balling risk. | May have slightly smaller junk slots, which could impact cleaning in very high volume or sticky formations. |
How to Choose Suitable PDC Bits?
Choosing the most suitable PDC drill bit involves a careful assessment of several factors to optimize drilling performance and maximize bit life. The ideal selection balances the bit’s design features with the specific demands of the drilling environment. Considerations include:
- Formation Type: Identify the geological characteristics, including rock hardness, abrasiveness, and unconfined compressive strength, as these dictate the required cutter strength, bit body material (steel vs. matrix), and overall aggressiveness.
- Drilling Parameters: Consider available weight on bit (WOB), rotary speed (RPM), and flow rate, as these parameters influence bit design choices like cutter size, blade count, and nozzle configuration for optimal energy transfer.
- Hole Size and Profile: The desired bore diameter and any specific wellbore trajectory requirements (e.g., straight hole, directional drilling) will determine the bit’s gauge protection, shoulder design, and steerability features.
- Drilling Fluid Properties: Evaluate the type and properties of the drilling mud, as this impacts the selection of nozzle sizes and junk slot area to ensure effective cuttings removal and prevent bit balling in various fluid systems.
- Cost vs. Performance: Balance the initial cost of the bit with its expected performance, including penetration rate, footage drilled, and potential for reduced trip times, aiming for the most cost-effective solution over the entire drilling interval.
Conclusion
The choice between a flat PDC bit profile and a parabolic PDC bit profile is not arbitrary; it’s a strategic decision that directly impacts drilling success. Each profile offers distinct advantages tailored to specific rock formations and drilling objectives, from maximizing penetration in soft, non-abrasive rock to enhancing stability and durability in harder, more complex environments.
Ultimately, understanding the nuances of these bit profiles empowers drillers to make informed selections, leading to improved efficiency, reduced operational costs, and superior wellbore quality. The right bit profile ensures that the cutting elements engage the formation optimally, minimizing wear and maximizing the drilling rate for every foot drilled.
For a comprehensive range of high-performance PDC drill bits, including various profiles like flat and parabolic, and other essential PDC drilling tools, trust Sinodrills. Located in Qingdao, Shandong, China, we are committed to providing wholesale solutions that meet the rigorous demands of the global drilling industry, ensuring your projects achieve peak performance.