As a leading supplier of PDC drill bits and drilling accessories, we consistently engage with drilling contractors and operators worldwide. We’ve seen firsthand how crucial every detail is in achieving efficient and safe drilling operations. One often-underestimated yet profoundly important aspect of our clients’ frequently consulted us on is the PDC drill bit make-up torque.
It’s not just about tightening a connection; it’s about establishing a secure, stable, and durable interface that directly impacts drilling performance, bit longevity, and ultimately, the success of your well. In this post, we’ll share our insights on why proper make-up torque is so vital and how we, as your supplier, help you get it right every time.
Why PDC Drill Bit Make-Up Torque is Non-Negotiable for Your Drilling Success
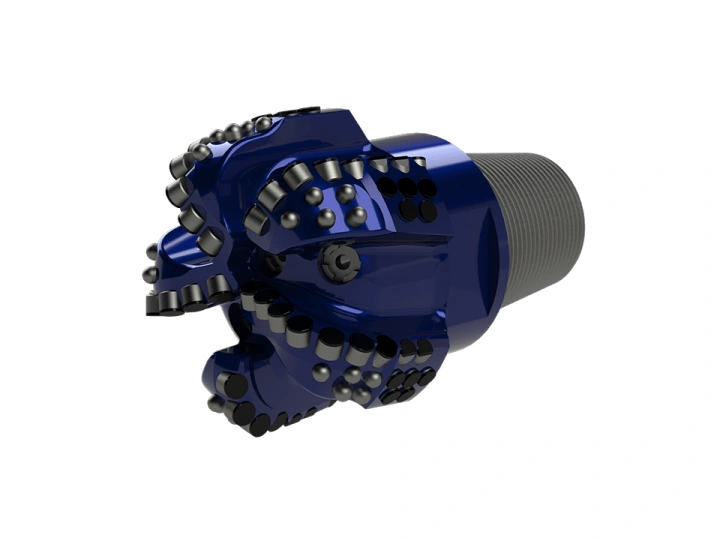
When you invest in our PDC drill bits, you’re acquiring sophisticated tools designed to cut through some of the toughest geological formations. The connection between our bit and your drill string is the lifeline that transmits power, weight, and rotational force. If this connection isn’t torqued correctly, you face a cascade of potential problems, from minor inefficiencies to catastrophic failures. We prioritize educating our clients on why getting this right is absolutely non-negotiable.
The Risks of Insufficient Torque: When Loose Connections Lead to Costly Failures
Under-torquing a PDC drill bit from our inventory is like driving a car with loose lug nuts – it might work for a while, but disaster is always looming. When the make-up torque is too low, the connection between our bit and your drill string isn’t fully engaged. This leads to a series of detrimental effects that can severely impact your drilling operations and lead to costly downtime. We guide our clients through these risks to help them avoid preventable issues.
- Connection Loosening and Back-off: The most immediate and obvious risk is the bit backing off the drill string downhole. This can lead to the bit becoming lost in the wellbore, requiring expensive fishing operations or even sidetracking the well. This is a scenario we help our clients avoid through proper torque guidance.
- Reduced Bit Stability and Vibrations: An under-torqued connection can cause our bit to be unstable during drilling. This instability leads to excessive vibrations, commonly known as “bit whirl” or “stick-slip.” These vibrations are not just annoying; they are incredibly destructive, causing premature wear on the PDC cutters and the bit body itself, compromising the investment you’ve made in our products.
- Thread Damage and Washouts: The constant movement and friction in a loose connection can quickly damage the threads on both our bit and your drill string. This damage compromises the integrity of the connection and can lead to washouts, where drilling fluid erodes the metal around the threads, further weakening the joint. We engineer our threads for durability, but they still require proper make-up.
- Premature Bearing Failure: The increased shock and vibration transmitted through a loose connection can significantly reduce the lifespan of our bits’ bearings, leading to premature bit failure and the need for an early trip out of the hole, impacting your operational efficiency.
- Inefficient Drilling Performance: When our bit isn’t stable, it can’t transmit the applied weight and rotational energy efficiently to the rock. This results in slower rates of penetration (ROP), increased drilling time, and ultimately, higher operational costs for you.
The Dangers of Excessive Torque: When Over-Tightening Harms Your Investment
While under-torquing is problematic, over-torquing a PDC drill bit presents its own unique set of dangers. It’s a common misconception that “tighter is always better.” In reality, applying excessive PDC drill bit make-up torque can be just as, if not more, damaging to our bit and your drill string. We often advise clients against this to prevent irreversible damage to their equipment.
- Thread Stretching and Deformation: Threads are designed to withstand a specific amount of force. Exceeding this force can cause the threads to stretch, deform, or even strip. Once threads are damaged in this way, the connection’s integrity is permanently compromised, and our bit’s reusability may be jeopardized.
- Pin or Box Swelling/Cracking: The excessive stress can lead to the “pin” (male end) of our bit swelling or the “box” (female end) of your drill string cracking. This is a critical failure that can render our bit or your drill string component unusable and create significant safety hazards.
- Reduced Fatigue Life: Even if immediate failure doesn’t occur, over-torquing introduces residual stresses into the material. These stresses significantly reduce the fatigue life of the connection, making it more susceptible to cracking and failure under subsequent drilling loads.
- Difficulty in Breakout: After a drilling run, breaking out an over-torqued connection can be extremely difficult and time-consuming. This can lead to damaged tools, increased rig time, and frustration for your crew.
- Damage to Internal Bit Components: In some cases, excessive torque can transmit stresses internally, potentially damaging our bit’s internal components, such as seals or bearings, even before drilling begins, negating the advanced design features we’ve incorporated.
The Science Behind Optimal PDC Drill Bit Make-Up Torque
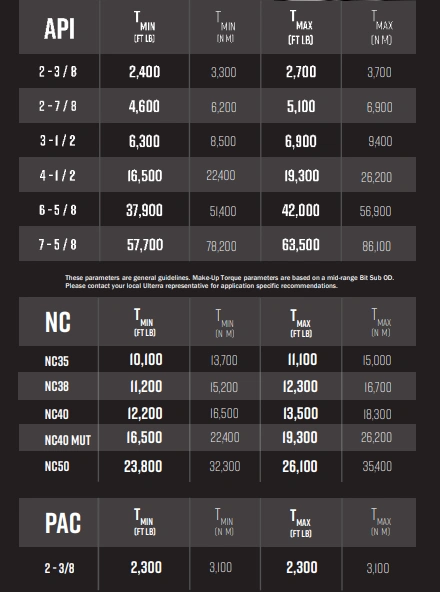
So, what’s the sweet spot? The optimal PDC drill bit make-up torque isn’t arbitrary; it’s a carefully calculated value based on metallurgical properties, thread design, and specific operating conditions. As bit manufacturers and suppliers, we provide recommended torque values for a reason – they are derived from extensive testing and engineering principles to ensure maximum performance and longevity of the products you receive from us.
Factors Influencing Make-Up Torque Values
Several factors influence the ideal make-up torque for a PDC drill bit. Understanding these helps us guide you on why a “one-size-fits-all” approach simply doesn’t work.
- Bit Size and Connection Type: Larger bits with larger connections (e.g., 6 5/8″ API REG vs. 4 1/2″ API REG) will naturally require higher make-up torque due to their increased surface area and load-bearing capacity. Different thread forms also have varying torque requirements, all of which are considered in our bit designs.
- Thread Compound (Dope): The type and quality of thread compound used significantly affect the friction between the threads. Thread compounds reduce friction, allowing for a more consistent and accurate make-up. We always recommend using the correct API-recommended dope.
- Material Strength: The strength of the steel used in both our bit connection and your drill string is a critical factor. Our bits are made from high-strength materials, but exceeding their yield strength must be avoided.
- Operating Conditions: While not directly influencing the initial make-up torque, the downhole temperature and pressure can affect the connection over time. However, the initial torque must be set to handle these conditions effectively, which our bit designs account for.
- Manufacturer’s Recommendations: This is the most crucial factor. We, as your bit manufacturer, conduct rigorous testing to determine the optimal torque values for our specific bit designs and connections. Always refer to our guidelines, typically provided with each bit.
The Role of Thread Compound (Drill Pipe Dope)
Thread compound, often referred to simply as “dope,” plays a far more critical role in achieving proper PDC drill bit make-up torque than many realize. It’s not just a lubricant; it’s an integral part of the connection’s design and functionality, ensuring our bit performs as intended.
Function of Thread Compound | Description |
Lubrication | Reduces friction between the threads during make-up, allowing the connection to reach the desired preload with the applied torque. This ensures a more consistent and accurate torque application, crucial for maximizing our bit’s lifespan. |
Sealing | Fills the microscopic gaps between the threads, creating a pressure seal that prevents drilling fluids from leaking through the connection, which could lead to washouts. This protects the integrity of our bit’s connection. |
Corrosion Protection | Prevents galling (cold welding) of the metal surfaces, particularly under high contact pressures and rotational forces. This makes it easier to break out our bits’ connection after drilling, saving you time and effort. |
Gall Prevention | Prevents galling (cold welding) of the metal surfaces, particularly under high contact pressures and rotational forces. This makes it easier to break out our bit’s connection after drilling, saving you time and effort. |
Load Distribution | Helps to distribute the load more evenly across the engaged threads, reducing stress concentrations and improving the overall fatigue life of the connection, directly benefiting the durability of our bits. |
Using the correct API-certified thread compound and applying it properly (ensuring full coverage without excess) is as important as the torque wrench itself for ensuring our products deliver peak performance.
Practical Steps for Achieving Correct PDC Drill Bit Make-Up Torque
Knowing the theory is one thing; putting it into practice consistently and accurately is another. As your supplier, we understand the challenges of maintaining precision in a dynamic rig environment. We equip our clients with the knowledge and support necessary to ensure optimal PDC drill bit make-up torque.
Essential Tools and Equipment We Recommend
Having the right tools is fundamental. Without them, achieving accurate torque is simply guesswork, and that’s a risk we advise against. We can guide you on selecting the right equipment.
- Torque Wrench/Tong System: This is the primary tool. It must be properly calibrated and capable of applying the required torque range for the bit size you are using. Manual torque wrenches, hydraulic torque wrenches, or rig floor tong systems with calibrated gauges are all used, depending on your application and rig setup.
- Thread Cleaners: Before applying dope and making up the connection, both our bit pin and your drill string box threads must be thoroughly cleaned of old dope, dirt, and debris.
- Thread Brushes: For applying thread compound evenly and completely.
- Bit Breaker/Sub: A stable platform to secure the drill bit during the make-up process. We can help you identify compatible bit breakers.
- Safety Equipment: Always ensure proper PPE, including gloves, safety glasses, and hard hats.
The Make-Up Procedure: Our Recommended Step-by-Step Guide
Precision and attention to detail are key during the make-up procedure. Shortcuts here can lead to significant problems down the line. We provide comprehensive guidance to our clients on these critical steps.
- Inspect Threads: Before anything else, thoroughly inspect the threads on both our bit pin and your drill string box. Look for any signs of damage, wear, corrosion, or foreign material. If threads are damaged, they must be repaired or the component replaced – we can assist with evaluations if needed.
- Clean Threads: Use appropriate thread cleaners and brushes to remove all old dope, dirt, and debris from both sets of threads. A clean connection is vital for proper engagement and accurate torque transfer, ensuring our bit connects perfectly.
- Apply Thread Compound: Apply a thin, even coat of the recommended API-certified thread compound to both the pin and box threads. Ensure complete coverage, but avoid excessive application, which can hydraulically lock the connection or mask thread damage. We can advise on the best compounds for our bits.
- Stab the Bit: Carefully stab our bit onto your drill string. Ensure it’s perfectly aligned to prevent cross-threading.
- Initial Hand-Tightening: Spin our bit onto your drill string by hand until it’s hand-tight. This ensures proper thread engagement before applying mechanical torque.
- Apply Make-Up Torque: Using a calibrated torque wrench or tong system, apply our manufacturer’s recommended PDC drill bit make-up torque. This should be done in a smooth, continuous motion, avoiding sudden jerks. For tongue systems, observe the gauge carefully. For manual wrenches, listen for the click or reach the set value.
- Verify Torque (If Possible): If using a system that allows for real-time torque monitoring, verify that the set torque value was achieved and held.
- Record Data: Log the make-up torque applied, the bit serial number (from our product), and the drill string connection used. This data is invaluable for troubleshooting and performance analysis, and we encourage our clients to maintain thorough records.
Conclusion
In the world of drilling, precision is paramount. The seemingly simple act of applying PDC drill bit make-up torque is, in fact, a highly critical procedure that directly influences drilling efficiency, bit longevity, and operational safety.
As your trusted supplier, we are committed to providing you not only with high-quality PDC drill bits but also with the expertise, recommendations, and support needed to ensure that every bit performs to its full potential. It’s an investment in attention to detail that pays dividends in reduced downtime, lower costs, and ultimately, more successful wells. Overlooking this crucial step is a risk no drilling operation can afford to take, and we are here to help you mitigate that risk.