In the world of drilling, choosing the right bit is paramount for efficiency and success. Two primary types dominate the industry: Polycrystalline Diamond Compact (PDC) and traditional roller cone bits, each engineered for distinct geological challenges.
Understanding their fundamental differences is key to optimizing performance. This blog explores their unique features, operational advantages, and ideal applications, guiding you to make informed decisions for your next drilling project.
What are PDC Bits?
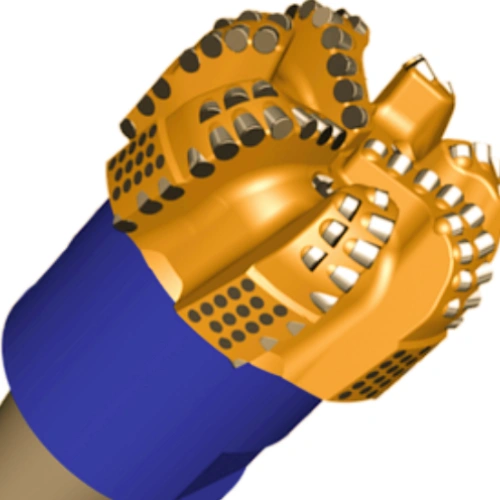
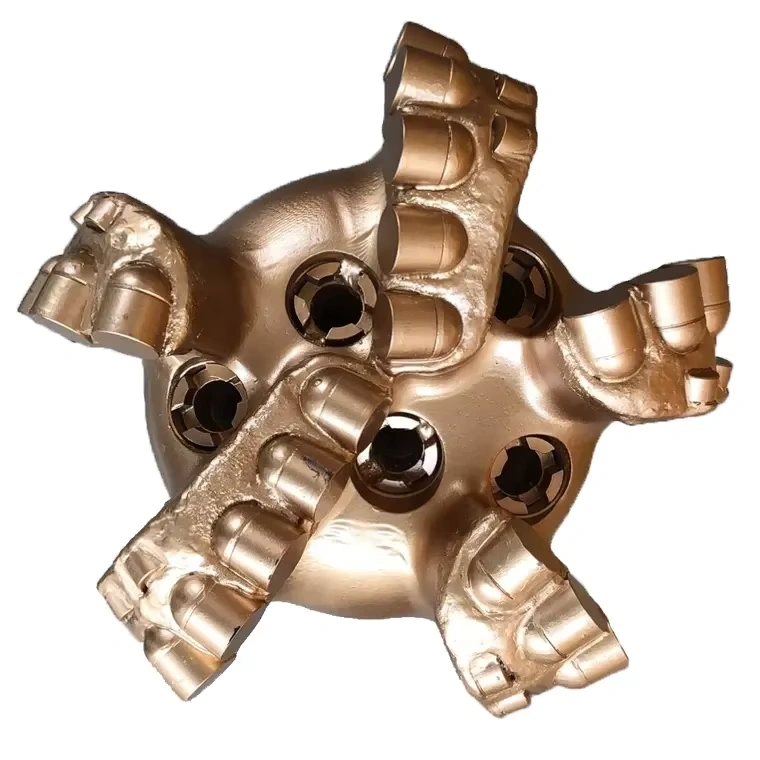
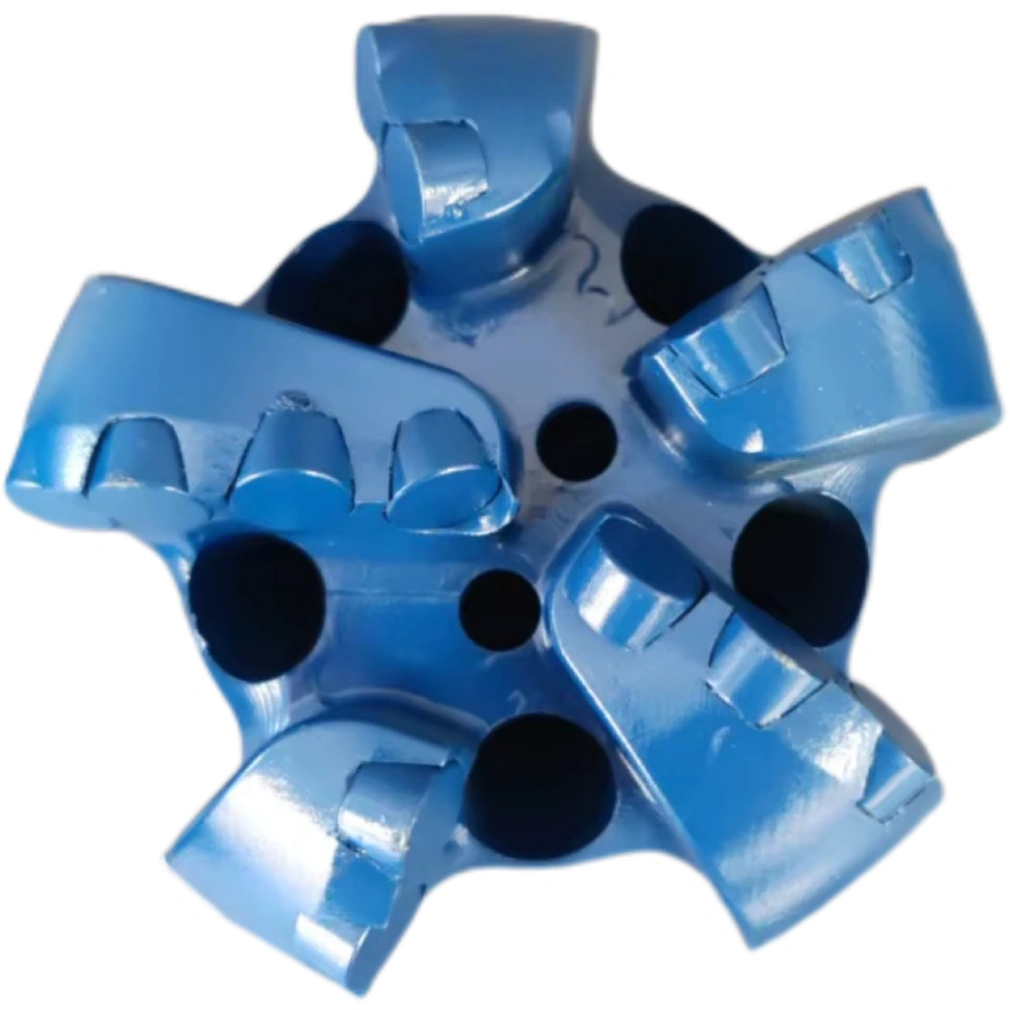
A Polycrystalline Diamond Compact (PDC) bit is a type of drill bit used in drilling operations, particularly in the oil and gas industry. It features synthetic diamond cutters that are fused onto a tungsten carbide substrate, providing exceptional hardness and abrasion resistance.
These PDC bits are highly effective for drilling through various rock formations, offering faster penetration rates and longer tool life compared to conventional roller cone bits, thereby improving overall drilling efficiency.
What are Roller Cone Bits?
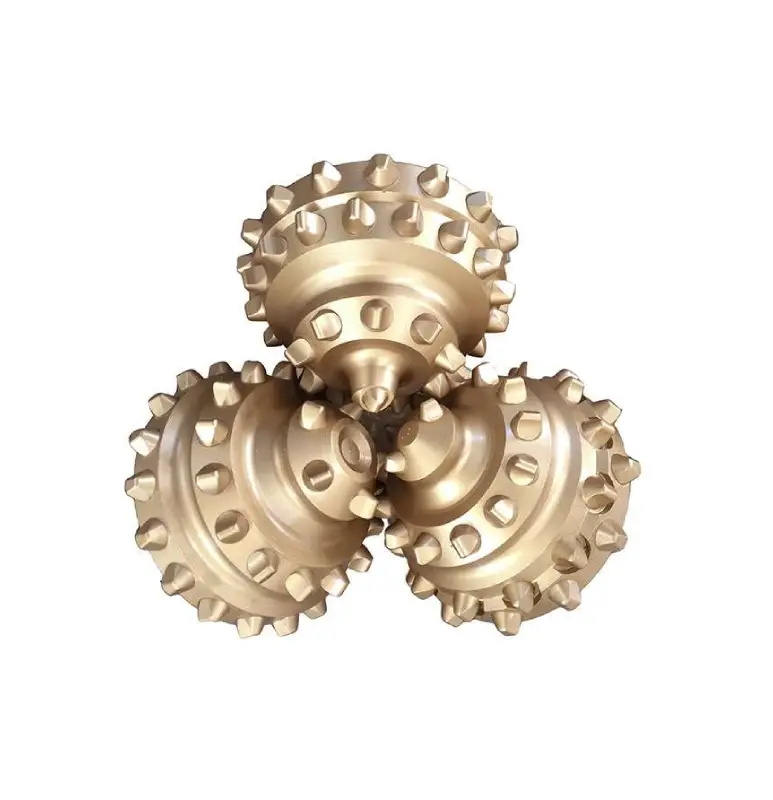
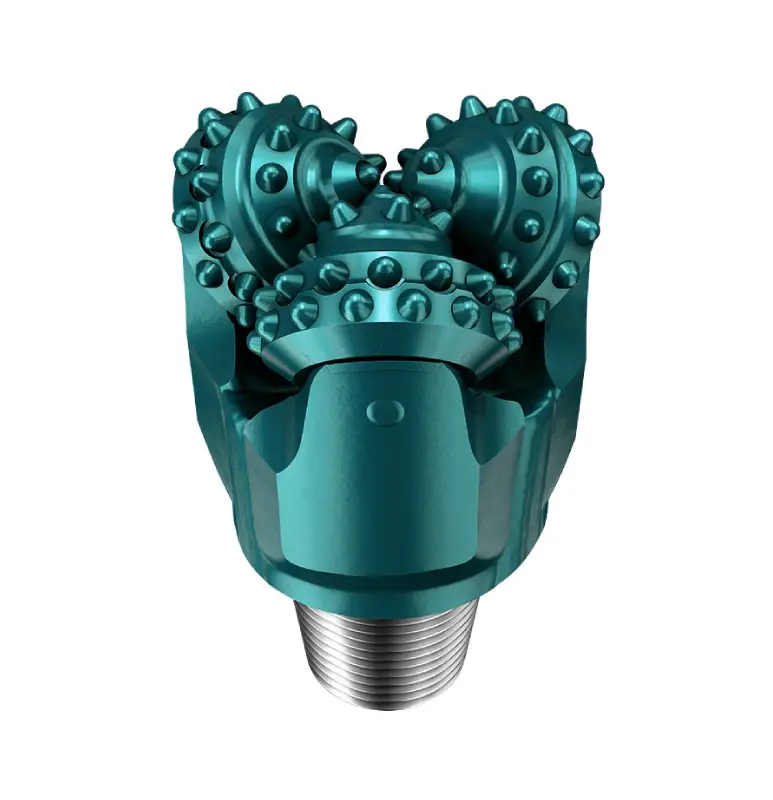
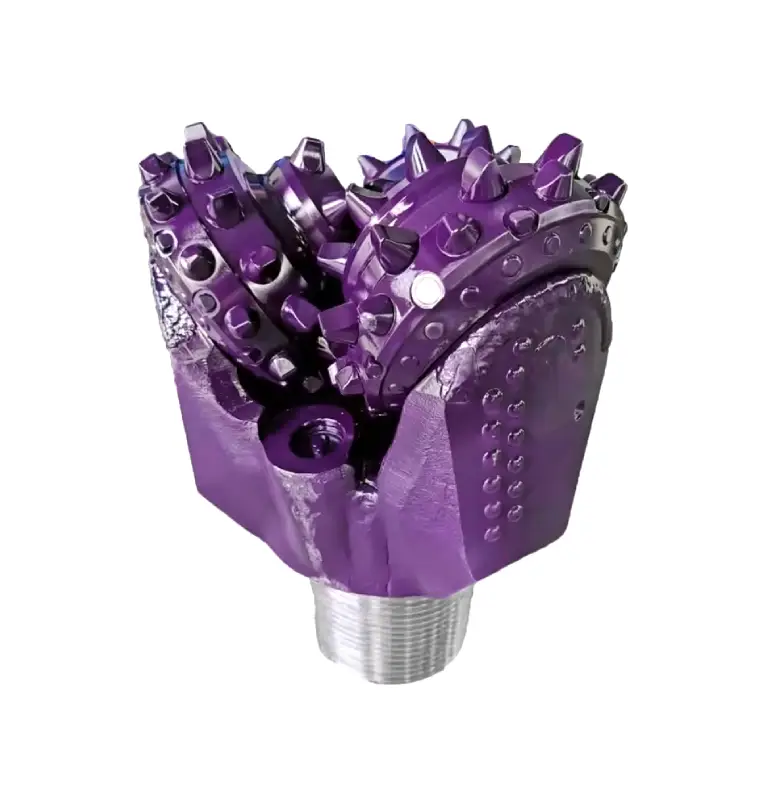
A roller cone bit is a type of drill bit that uses two or more rotating cones fitted with cutting elements to break rock.
As the drill string rotates, the cones also rotate on their own axes, allowing the cutting elements—which can be steel teeth or tungsten carbide inserts—to crush, chip, and shear the rock. These bits are versatile and widely used across various formations, from soft and sticky to hard and abrasive, making them a staple in many drilling operations.
PDC vs Roller Cone Bit
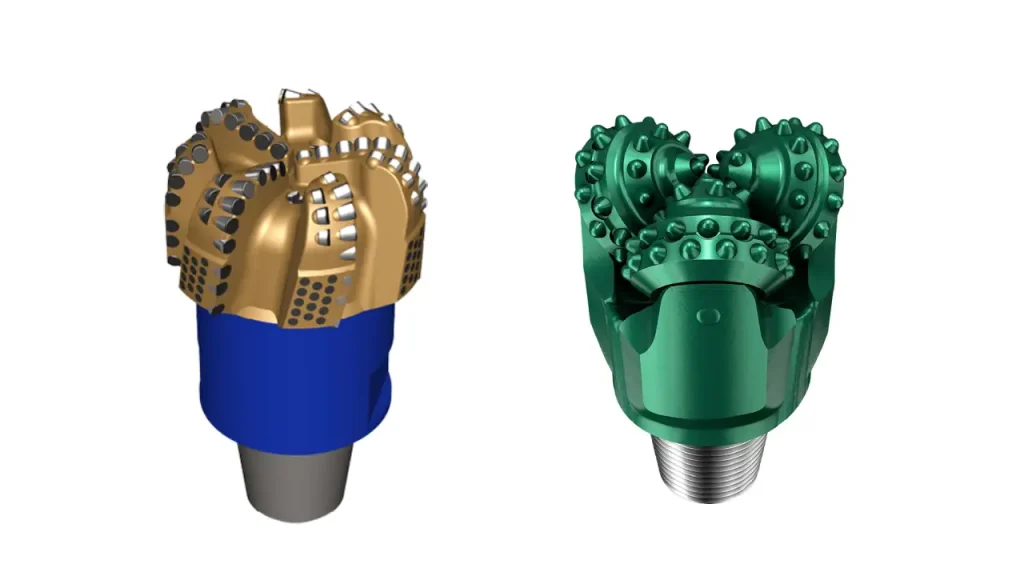
Choosing between PDC and roller cone drill bits is a critical decision in any drilling operation. Each bit type offers distinct advantages tailored to specific geological conditions and project goals. Understanding their fundamental differences is essential for optimizing performance and achieving drilling success.
Cutting Mechanism
PDC (Polycrystalline Diamond Compact) bits operate through a shearing action. Their fixed, synthetic diamond cutters continuously scrape and shear the rock as the bit rotates. This design allows for a very efficient and continuous cutting process, minimizing the need for crushing and grinding, which contributes to higher rates of penetration in suitable formations.
In contrast, roller cone bits utilize a crushing and chipping action. Their independently rotating cones are equipped with either steel teeth (milled tooth bits) or tungsten carbide inserts (TCI bits) that interact with the formation. As the drill string rotates, the cones roll across the bottom of the hole, applying compressive stress to break and dislodge rock fragments.
Formation Suitability
PDC bits are generally most effective in homogeneous, soft to medium-hard formations such as shales, siltstones, and limestones, where their shearing action can efficiently remove rock. They are less prone to balling in sticky formations due to their open design and continuous cutting, making them a preferred choice in many conventional drilling applications.
Roller cone bits, particularly those with robust tungsten carbide inserts, are highly versatile and excel across a broader range of formations, from very soft to extremely hard and abrasive igneous or metamorphic rocks. Their crushing action makes them more tolerant to heterogeneous formations, interbedded layers, and conditions prone to impact loading.
Durability and Lifespan
PDC bits typically offer a longer lifespan compared to roller cone bits in optimal conditions. The inherent hardness and abrasion resistance of their diamond cutters allow them to drill for extended periods without needing to be pulled from the hole for bit changes, thus saving significant rig time and associated costs.
However, PDC cutters are susceptible to damage from impact loading, especially in fractured or highly abrasive formations, which can lead to chipping or breaking. Roller cone bits, with their robust steel or TCI structures, often demonstrate superior impact resistance and can better withstand shock loads in challenging environments.
Rate of Penetration (ROP)
PDC bits generally achieve significantly higher rates of penetration (ROP) in formations where their shearing mechanism is effective. Their continuous cutting action and efficient junk removal allow for rapid drilling, directly translating to reduced drilling time and improved overall project economics.
While roller cone bits may have lower average ROPs compared to PDC bits in optimal conditions, their versatility allows them to maintain consistent penetration across a wider range of rock strengths and types. In very hard or abrasive formations, a roller cone bit might achieve a more sustained ROP than a PDC bit prone to cutter damage.
Cost
The initial purchase price of a PDC bit is typically higher than that of a comparable roller cone bit. This higher upfront investment reflects the advanced materials and manufacturing processes involved in creating the synthetic diamond cutters and the complex bit body designs.
Despite the higher initial cost, PDC bits often deliver a lower cost per foot drilled due to their extended lifespan and higher ROP, which reduce expensive tripping time. Roller cone bits, while cheaper to buy, may incur higher overall costs if frequent bit changes are required due to wear or damage in challenging formations.
Here are differences between PDC drill bits and roller cone bits in the following:
Feature | PDC Bits | Roller Cone Bits |
Cutting Mechanism | Shearing (fixed cutters scrape/shear rock) | Crushing/Chipping (rotating cones break rock) |
Formation Suitability | Soft to medium-hard, homogeneous, shales, siltstones, limestones | Very soft to extremely hard, heterogeneous, interbedded, abrasive |
Durability / Lifespan | Longest in optimal conditions; susceptible to impact damage | Good impact resistance; shorter lifespan in abrasive formations |
Rate of Penetration (ROP) | Generally higher in suitable formations (fast) | Variable; consistent across wide range; lower than PDC in optimal conditions |
Cost | Higher initial cost; often lower cost per foot | Lower initial cost; can be higher cost per foot if frequent changes needed |
How to Choose PDC and Roller Cone Bit?
Choosing the optimal drill bit, whether PDC or roller cone, is a critical decision that significantly impacts drilling efficiency, cost, and overall project success. This selection process requires a thorough understanding of downhole conditions and operational goals.
Key considerations revolve around the geological formation’s characteristics, drilling trajectory, and desired rate of penetration.
To make an informed choice, consider the following factors:
- Formation Type: For soft to medium-hard, homogeneous formations like shales and limestones, PDC bits excel due to their shearing action. For varied, hard, or abrasive formations with interbedded layers, roller cone bits (especially TCI) are often more robust and versatile due to their crushing mechanism.
- Drilling Environment: High-impact environments or fractured rock can cause PDC cutter damage; roller cone bits might be more resilient here. Conversely, if minimizing trips is paramount and conditions allow, the extended life of PDC bits offers significant economic advantages.
- Desired Performance: If maximizing Rate of Penetration (ROP) in suitable formations is the priority, PDC bits generally offer superior speed. If consistent, albeit slower, performance across highly variable rock types is needed, roller cone bits can provide greater reliability.
- Cost vs. Efficiency: While PDC bits have a higher initial cost, their longevity and high ROP often lead to a lower cost per foot. Roller cone bits are cheaper upfront but might necessitate more frequent changes, increasing overall operational expenses.
Conclusion
In conclusion, the strategic choice between PDC and roller cone bits profoundly impacts drilling efficiency, cost-effectiveness, and overall project success. Each bit type excels within specific geological formations and operational parameters.
Understanding their distinct cutting mechanisms, inherent advantages, and operational limitations is absolutely vital for meticulous well planning and flawless execution, ultimately maximizing your operational effectiveness downhole.
For reliable performance and to acquire wholesale PDC drill bits and robust roller cone bits meticulously engineered to meet your project’s precise demands, we invite you to choose Sinodrills. We are committed to providing quality drilling solutions.