In the world of drilling, efficiency and stability are paramount. Traditional methods often struggle with challenging ground conditions, leading to delays and increased costs. This blog post delves into Symmetrix drilling, an innovative system designed to overcome these hurdles by simultaneously drilling and casing boreholes, offering a streamlined approach to various construction and civil engineering projects.
Symmetrix drilling stands out for its unique concentric design, where a drill bit and a casing tube work in unison. This method minimizes the risk of borehole collapse and ensures a clean, stable hole from the outset. We will explore the core principles behind Symmetrix, understand its key components, and discover how this ingenious technology is transforming drilling operations across the globe.
What is Symmetrix Drilling?
Symmetrix Drilling, also known as the symmetric drilling method, is a specialized technique designed for simultaneously drilling and casing boreholes, particularly effective in challenging geological conditions like loose soils, sand, clay, and hard rock formations with large boulders.
This system utilizes a unique drill bit design featuring a central pilot bit surrounded by symmetrically arranged radial wings or cutters.
As the pilot bit creates a smaller hole, the wings progressively enlarge it to the desired diameter, while a casing tube is simultaneously installed directly behind the drill bit. This continuous casing advancement provides immediate support and stability to the borehole, preventing collapse and ensuring a clean, stable hole from the outset, which is crucial for applications such as foundation drilling, micropiling, and anchoring.
Odex and Symmetrix Drilling Methods
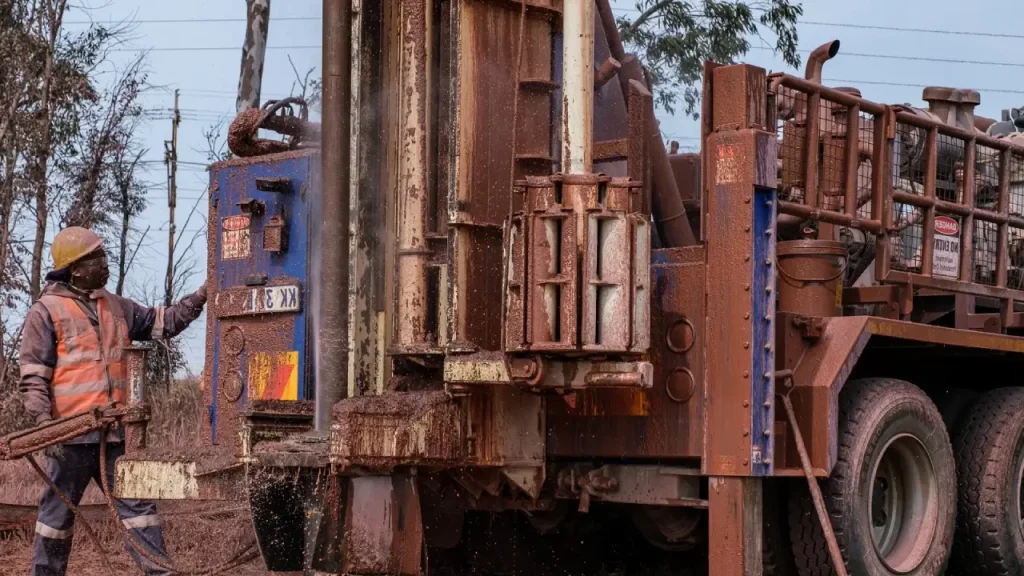
When tackling challenging ground conditions, choosing the right drilling method is crucial for project success. Two prominent overburden drilling systems often considered are Odex and Symmetrix. Both are designed to advance casing simultaneously with drilling, but they achieve this through distinct mechanisms. Understanding their differences is key to selecting the optimal approach for your specific geotechnical needs.
Odex Drilling Method
Odex drilling is an eccentric overburden drilling system primarily used for simultaneously drilling and casing boreholes in unconsolidated or unstable ground conditions. It employs a drill bit with an eccentric reamer that swings out to create a hole slightly larger than the casing. This allows the casing to be driven concurrently with the drilling, providing immediate support and preventing borehole collapse, making it highly effective for water wells and shallow micropiling.
Symmetrix Drilling Method
Symmetrix drilling is a concentric casing advancement system designed for drilling through difficult overburden and hard rock formations. It features a central pilot bit and a symmetrical ring bit that work together to drill a hole large enough for the casing to follow. This method ensures a straight hole and is particularly suited for deeper and larger diameter boreholes, offering high precision and efficiency in diverse geological conditions.
Symmetrix Overburden Drilling System
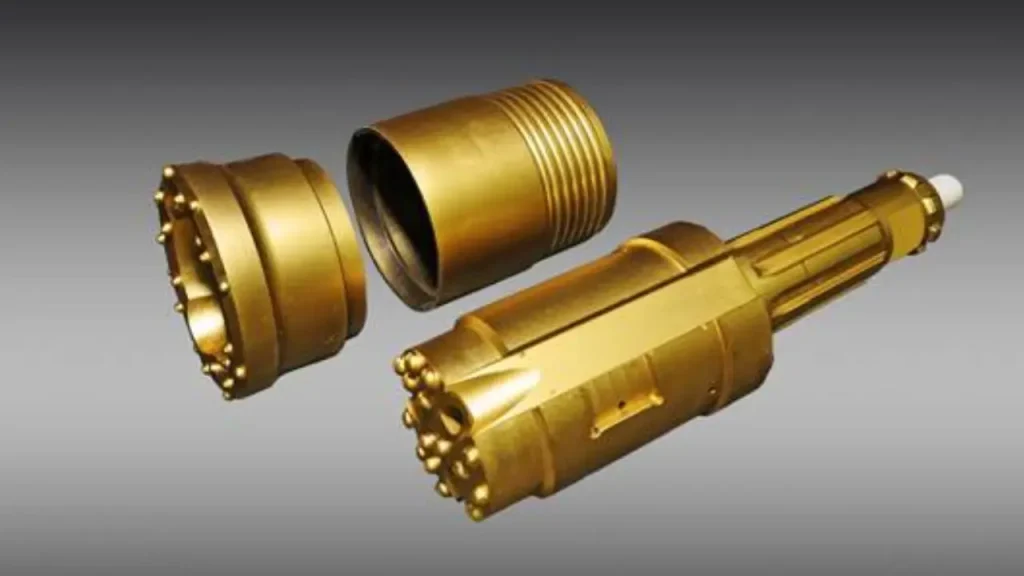
The Symmetrix Overburden Drilling System is an advanced and robust method for simultaneously drilling and casing boreholes, excelling in challenging ground conditions ranging from loose soils to solid rock. It operates on a concentric principle where a pilot drill bit and a symmetrical ring bit work in unison, ensuring the casing follows immediately behind the drilling action.
This provides continuous support to the borehole, preventing collapse and ensuring a clean, stable hole from the outset.
- Simultaneous Drilling and Casing: Eliminates the need for separate drilling and casing operations, saving time and resources.
- Concentric Design: Utilizes a pilot bit and a symmetrical ring bit, ensuring a straight and stable borehole.
- Versatile Application: Highly effective in various challenging ground conditions, including sand, gravel, boulders, and hard rock.
- Improved Borehole Quality: Provides immediate casing support, preventing caving and ensuring a clean hole for subsequent operations like grouting or anchor installation.
- Enhanced Efficiency: Reduces the risk of stuck drill strings and lost equipment, leading to faster project completion.
Symmetrix Bits
Symmetrix Bits
Symmetrix drilling relies heavily on its specialized bit design, which is central to its ability to simultaneously drill and case. These bits are engineered for concentric overburden drilling, allowing for seamless penetration through various geological formations.
Understanding the components and types of Symmetrix bits is crucial to appreciating the system’s efficiency and reliability in creating stable boreholes.
- Pilot Bit: This is the leading part of the Symmetrix bit assembly, responsible for initially penetrating the ground. It guides the entire drilling string and establishes the path for the following components. Its robust construction ensures efficient breaking of rock and overburden, initiating the borehole precisely.
- Ring Bit (Reamer Bit): The ring bit, also known as the reamer bit, is positioned behind the pilot bit and is crucial for enlarging the borehole to the desired casing diameter. It effectively reams the hole, ensuring a smooth passage for the casing tube. Its design guarantees a consistent diameter and reduces friction during casing advancement.
- Internal Flush Tube: An integral part of some Symmetrix bit designs, the internal flush tube directs the flushing medium (air or water) to the cutting face of both the pilot and ring bits. This efficiently clears cuttings from the hole, preventing blockages and ensuring continuous drilling progress. Effective flushing is vital for optimal performance and bit life.
- Guide Device (for Casing): While not strictly part of the bit, a guide device is often integrated into the overall Symmetrix system, directly interacting with the bit assembly. It ensures that the casing pipe follows the drilled hole precisely and is advanced smoothly. This component is key to maintaining borehole stability and straightness as drilling progresses.
How to Choose Suitable Symmetrix Drill Bits
Choosing the suitable Symmetrix drill bits is crucial for optimizing drilling performance and achieving desired results in specific ground conditions.
The selection process should consider the geological formation, the required hole diameter, and the capabilities of your drilling rig to ensure efficient penetration and a stable borehole. Mismatching the bit to the application can lead to slower progress, increased wear, and potential damage.
- Geological Formation: Consider the type and hardness of the ground you’ll be drilling through. For softer soils and loose overburden, bits designed for high penetration rates are ideal. For hard rock or mixed formations with cobbles and boulders, more robust bits with aggressive cutting structures and wear-resistant inserts are necessary to ensure durability and effective breakage.
- Hole Diameter and Casing Size: The Symmetrix bit chosen must match the required final borehole diameter and the outer diameter of the casing to be installed. The ring bit component is specifically sized to ream a hole that allows the casing to follow directly behind the pilot bit, ensuring a precise fit and continuous support.
- Drilling Depth: For deeper holes, bit longevity and consistent performance become even more critical. Bits with enhanced wear protection and robust designs are preferred to withstand the extended operational time and abrasive conditions encountered at greater depths, minimizing the need for frequent bit changes.
- Drilling Rig Capabilities: Ensure the chosen Symmetrix drill bit’s size and required torque/thrust are compatible with your drilling rig’s power and hydraulic capabilities. An undersized rig may struggle to operate larger or more aggressive bits effectively, leading to inefficient drilling and potential equipment strain.
Conclusion
Symmetrix drilling offers a robust and reliable solution for a multitude of geotechnical challenges. Its ability to achieve high penetration rates while maintaining borehole integrity makes it an invaluable asset in difficult ground conditions, ensuring project timelines are met and safety standards are upheld. The versatility of Symmetrix extends to various applications, from anchoring and micropiling to water well drilling and exploration.
The advantages of implementing Symmetrix technology are clear: reduced material waste, increased operational speed, and superior bore hole quality. These benefits translate directly into significant cost savings and enhanced project efficiency, making Symmetrix an increasingly popular choice for forward-thinking construction and engineering firms worldwide. Embrace the future of drilling by considering Symmetrix for your next project.
For those seeking reliable and high-quality solutions for slope stabilization, look no further. Sinodrills offers a comprehensive range of wholesale self-drilling anchors designed to complement the efficiency of Symmetrix drilling. Our anchors provide exceptional performance and durability, ensuring long-term stability for your critical infrastructure. Get wholesale self-drilling anchors for slope stabilization from our Sinodrills to secure your projects with confidence.