Underground drilling in hard rock environments presents unique challenges, demanding specialized tools that can withstand immense pressure and abrasion. The performance of your entire operation hinges on selecting the right drill bits. This guide will delve into the critical aspects of choosing and utilizing drill bits specifically designed to conquer the toughest subterranean formations.
From deep exploration to precise tunneling, efficient hard rock drilling is non-negotiable for safety and productivity. Understanding the nuances of drill bit technology—from robust TCI (Tungsten Carbide Insert) designs to advanced gauge protection—is key to maximizing penetration rates and extending bit life, ultimately saving you time and money.
What is Underground Drilling?
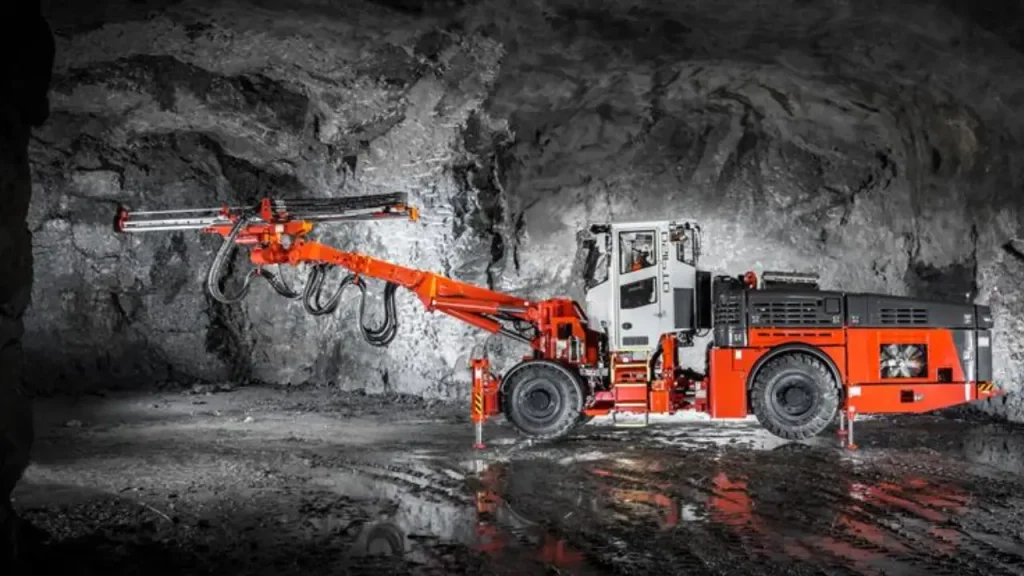
Underground drilling refers to the process of creating boreholes or tunnels beneath the Earth’s surface using specialized drilling rigs and tools. Unlike surface drilling, which operates in open environments, underground drilling is conducted within confined spaces such as mineshafts, tunnels, or subterranean chambers.
Its primary applications include mineral exploration and extraction, creating passages for utilities like pipelines and cables (often via trenchless methods like directional drilling), and geotechnical investigations for construction and infrastructure projects. This drilling method is crucial when surface access is impractical, environmentally sensitive, or simply too costly, allowing access to resources and spaces deep underground.
Drilling Techniques in Underground Mining
Underground mining relies on precise and efficient drilling techniques to extract valuable minerals and create safe working environments. The choice of drilling method is highly dependent on factors like rock type, desired hole size and depth, and the specific mining method employed. Key techniques include:
- Blast Hole Drilling: Creating holes for explosive charges to fragment rock, a fundamental step in most underground mining operations.
- Production Drilling: Drilling long, narrow holes to facilitate the extraction of ore, often in methods like sublevel stoping.
- Exploration Drilling: Obtaining core samples to analyze geological formations and identify mineral deposits.
- Rock Bolting/Support Drilling: Drilling holes to install rock bolts and other ground support systems, ensuring tunnel stability and miner safety.
Underground Drill Bits
Underground drilling relies heavily on specialized drill bits designed to withstand the harsh conditions and diverse rock formations encountered beneath the Earth’s surface. Choosing the correct bit is paramount for efficiency, safety, and project success, directly impacting penetration rates, bit life, and overall operational costs.
Tricone Drill Bits
Tricone drill bits are highly versatile and widely used in underground drilling, particularly for softer to medium-hard rock formations. These bits feature three rotating cones equipped with either milled steel teeth or tungsten carbide inserts (TCI). The rolling action of the cones helps to crush and shear the rock, making them effective for achieving high penetration rates and extended bit life in varying ground conditions, from shales to limestone.
DTH (Down-The-Hole) Drill Bits
DTH drill bits are integral to percussive drilling, especially effective in hard and abrasive rock formations. These bits work in conjunction with a DTH hammer, which delivers powerful blows directly to the bit face. The impact energy, combined with rotation, pulverizes the rock, allowing for fast penetration and straight holes in granite, basalt, and other tough geological structures, commonly used in blast hole drilling.
Top Hammer Drill Bits
Top hammer drill bits are designed for applications where the drilling force is applied from the top of the drill string, through a drifter. These bits utilize tungsten carbide inserts (buttons) and come in various shapes like spherical, ballistic, or conical, suited for different rock types and drilling objectives. They are commonly used for short-hole drilling, rock bolting, and tunneling in both hard and medium-hard rock conditions.
PDC (Polycrystalline Diamond Compact) Drill Bits
PDC drill bits utilize fixed cutters made of synthetic polycrystalline diamond compacts bonded to a carbide substrate. These bits are highly effective for drilling in softer to medium-hard, non-abrasive formations like shales, sandstones, and limestones, where they can achieve extremely high penetration rates by shearing the rock. Their lack of moving parts makes them durable, reducing the risk of bit failures in challenging underground environments.
Diamond Core Bits
Diamond core bits are specifically designed for geological exploration and sampling. They feature industrial diamonds embedded in a metal matrix on their cutting face. These bits are annular (ring-shaped), allowing them to cut a cylindrical core of rock rather than pulverizing the entire hole. They are highly effective for drilling in extremely hard and abrasive formations, providing high-quality, intact core samples essential for detailed geological analysis and mineral discovery.
Drag Bits
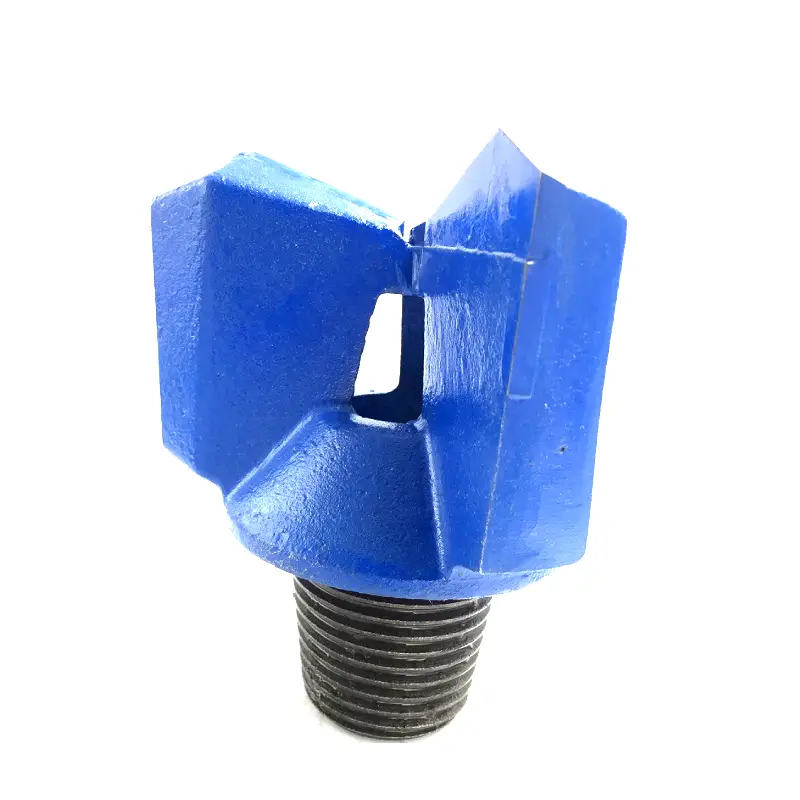
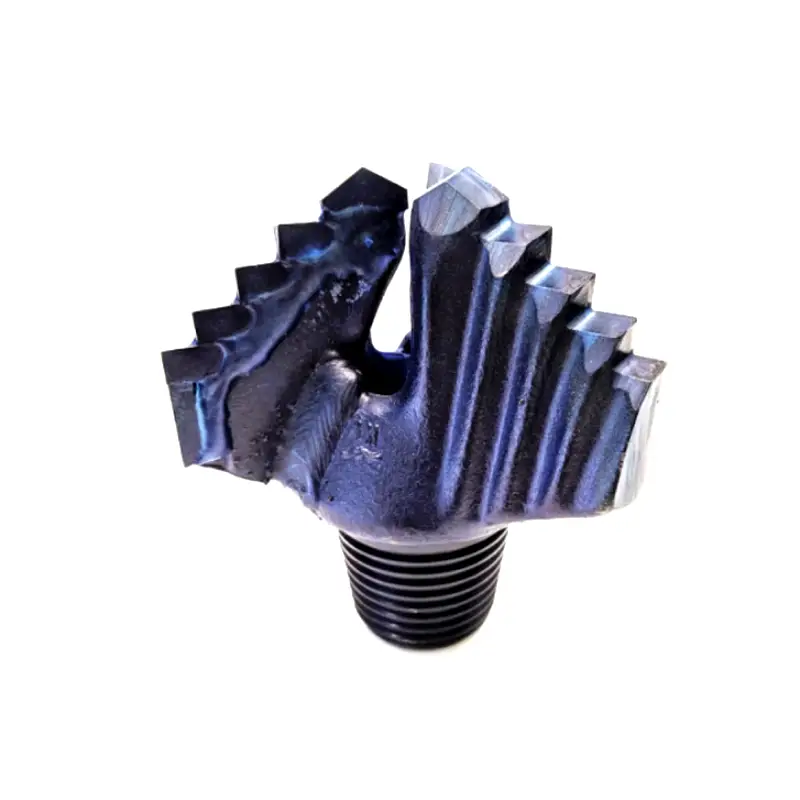
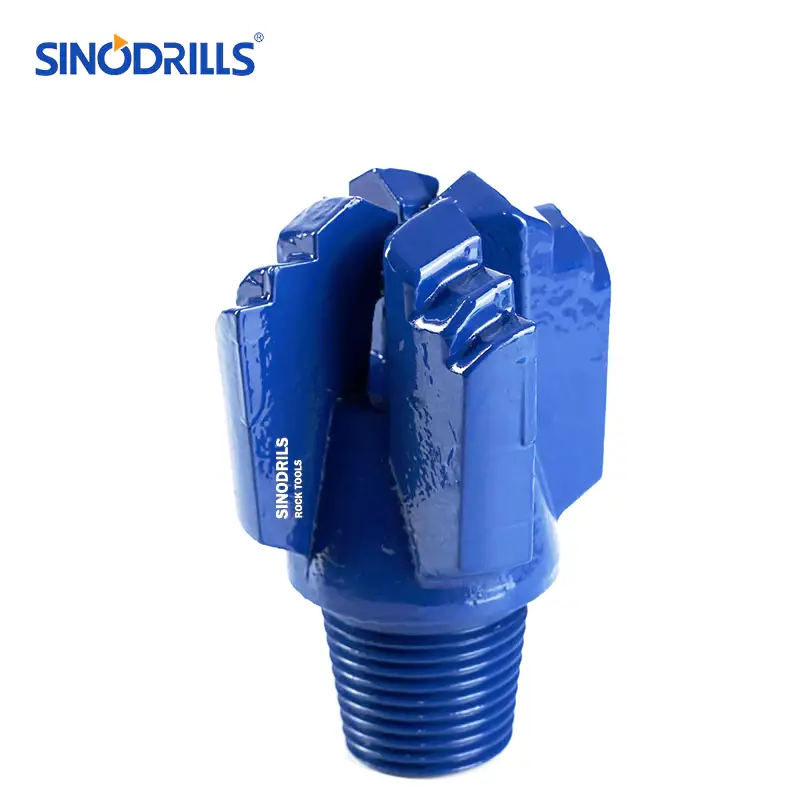
Drag bits are among the simplest and most economical drill bits, typically used in very soft, unconsolidated formations such as clay, sand, or soft shale. They consist of a steel body with fixed blades or wings that shear and scrape the formation as the bit rotates. While not suitable for hard rock, their simplicity and efficiency make them a cost-effective choice for shallow drilling and pilot holes in appropriate ground conditions.
Underground Core Drilling Rigs
Underground core drilling rigs are specialized machines designed to extract cylindrical rock or soil samples (cores) from subterranean environments. These underground drilling rigs are essential for geological exploration, mineral prospecting, and geotechnical investigations within confined spaces like mines, tunnels, and deep boreholes.
They are typically compact and highly maneuverable, often featuring hydraulic systems and advanced controls to operate efficiently and safely in challenging conditions.
Key characteristics and types include:
- Compact Design: Built to fit and operate in the limited space of underground workings.
- Modular Systems: Many rigs are designed with interchangeable components for easier transport and setup in tight areas.
- Hydraulic Power: Utilizes hydraulic systems for powerful drilling, precise control, and robust performance.
- Wireline Coring: A common method allowing core retrieval without pulling the entire drill string, increasing efficiency.
- Types: Include small, portable units for shallow exploration, and larger, more robust models for deep hole drilling, often categorized by their feed length, boom configuration, and size class.
Underground Drilling and Blasting
Underground drilling and blasting are foundational processes in hard rock mining and tunneling, working in tandem to excavate rock. This integrated approach allows for the controlled fragmentation and removal of material, creating the necessary space for mineral extraction or infrastructure development in subterranean environments.
Purpose
The primary purpose of underground drilling and blasting is to break large rock masses into manageable sizes for efficient removal. Drilling creates precisely placed holes, which are then loaded with explosives. Blasting, the subsequent detonation, fragments the rock, allowing for the excavation of tunnels, shafts, and stopes, crucial for accessing ore bodies or constructing underground facilities.
Drilling Process
The drilling process involves boring a series of holes into the rock face according to a meticulously designed pattern. Specialized underground drill rigs, such as jumbos or longhole drills, are used to create these boreholes with specific diameters, depths, and angles. The accuracy of drilling is paramount, as it directly influences the effectiveness and safety of the subsequent blast.
Blasting Process
Following drilling, the blasting process entails loading the drilled holes with explosives and detonating them in a controlled sequence. Engineers carefully design the blast pattern, charge quantity, and delay timings to achieve optimal rock fragmentation, minimize ground vibration, and ensure the stability of surrounding rock. This controlled detonation breaks the rock into sizes suitable for loading and hauling.
Equipment Used
A range of specialized equipment is vital for these operations. Drilling relies on powerful underground drill rigs (e.g., face drilling jumbos, longhole drills) and various drill bits (tricone, DTH, top hammer, PDC). Blasting requires explosives, detonators, and blasting machines, along with charging equipment to safely load the boreholes. Support equipment like ventilation systems and mucking machines are also crucial.
Safety Considerations
Safety is paramount in underground drilling and blasting due to the inherent risks. Strict protocols are followed, including comprehensive ventilation to clear fumes, ground support installation (e.g., rock bolting) to stabilize excavated areas, and exclusion zones during blasting. Advanced monitoring systems and remote-controlled equipment are increasingly used to minimize human exposure to hazards.
Outcome
The immediate outcome of underground drilling and blasting is fragmented rock, known as “muck,” which can then be loaded by LHDs (Load-Haul-Dump machines) or other equipment and transported out of the mine. Ultimately, these processes enable the safe and efficient excavation required for mineral production, mine development, and the construction of underground infrastructure.
Here are the differences between underground drilling and blasting:
Aspect | Drilling | Blasting |
Primary Action | Creating precise holes in rock. | Fragmenting rock through controlled detonation of explosives. |
Purpose | Prepares the rock for blasting; facilitates ground support. | Breaks rock into manageable sizes for excavation. |
Tools Used | Drill rigs (jumbos, longhole drills), drill bits (TCI, DTH, PDC, etc.), drill rods. | Explosives, detonators, blasting machines, charging equipment. |
Energy Source | Mechanical (rotation, percussion) from drill rig. | Chemical energy stored in explosives. |
Output | Boreholes (empty or with ground support installed). | Fragmented rock (muck). |
Timing | Precedes blasting; can also be done for support post-blast. | Follows drilling; a rapid, controlled event. |
Main Risk | Equipment malfunction, dust, noise, vibration, hole deviation. | Ground vibration, air blast, flyrock, toxic fumes, uncontrolled detonation. |
Conclusion
Mastering the selection and application of drill bits is paramount for any successful underground hard rock drilling project. By carefully considering factors like rock type, drilling method, and desired performance, you can significantly enhance your operational efficiency, reduce downtime, and achieve optimal penetration rates. The right bit isn’t just a tool; it’s a strategic asset for challenging subterranean environments.
Ultimately, maximizing the lifespan and performance of your drill bits translates directly into tangible cost savings and increased productivity for your underground drilling operations. Investing time in understanding the unique characteristics of different bit designs and how they interact with specific hard rock formations will always yield a strong return, ensuring smoother and more profitable projects.
Ready to equip your underground drilling operations with top-tier drill bits? At Sinodrills, we offer a comprehensive range of wholesale underground drill bits and drilling tools engineered for durability and peak performance in hard rock. Contact us today to explore our selection and find the perfect solutions for your next project, ensuring you get the robust tools you need, directly from a trusted manufacturer.