Selecting the correct PDC drill bit size is a fundamental decision that directly impacts the efficiency and success of any drilling operation. An undersized bit won’t achieve the required bore, while an oversized one can lead to costly delays and operational issues. This guide will clarify the importance of accurate sizing and introduce you to the essential PDC bit size chart.
Understanding the various PDC bit sizes and how to interpret a PDC bit size chart is critical for drilling professionals. This knowledge ensures you select a bit that not only fits your drilling equipment but also aligns perfectly with your wellbore specifications, ultimately leading to optimal penetration rates and a perfectly sized hole every time.
What Size PDC Bit to Use for Horizontal Drilling
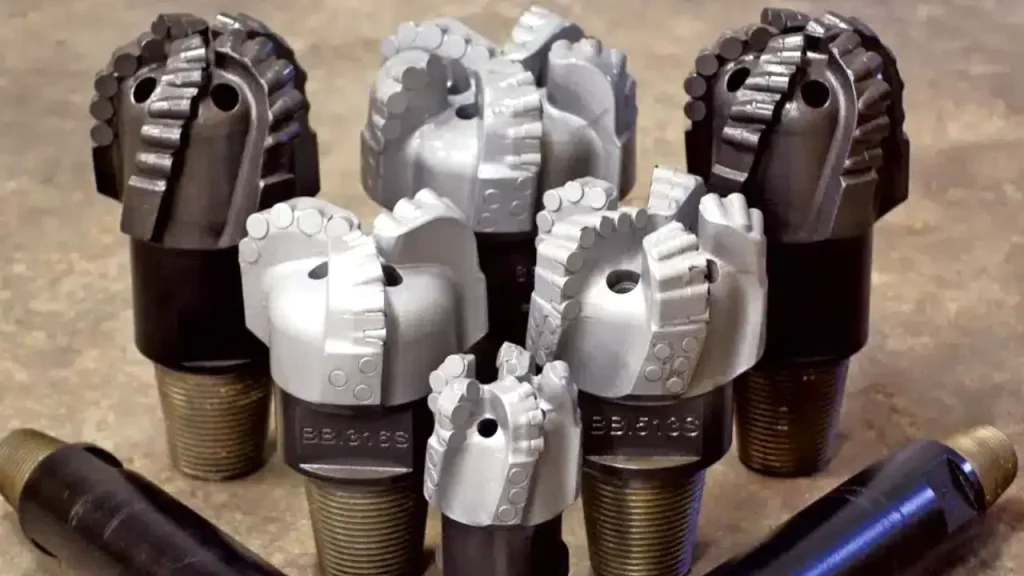
When choosing a PDC bit for horizontal drilling, the size primarily depends on the project’s requirements, including the final hole diameter and the type of geological formation. Smaller bits are typically used for initial pilot holes, while larger bits or reamers are employed to enlarge the hole to its final dimensions.
Here are key considerations for PDC bit sizes in horizontal drilling:
- Pilot Hole Bits: For creating the initial pilot hole, smaller PDC bits, generally ranging from 3-1/2 inches (89 mm) to 6-1/2 inches (165 mm), are used. These bits are designed for steerability, often featuring concave heads and short skirts to protect the cutters and minimize side pressure.
- Reaming Bits: To enlarge the pilot hole to its final diameter, larger bits or reamers are utilized. These can range significantly in size, up to 27.56 inches (700 mm).
- Formation Type: The choice of bit size also depends on the formation type. Smaller, more aggressive bits are often preferred for softer formations, while more durable designs are selected for harder ones.
- Common Applications: For instance, a 12 1/4″ PDC bit with 5 or 6 blades is frequently used in horizontal directional drilling (HDD) for medium-hard formations, providing a balance of cutting efficiency and directional control.
PDC Drill Bit Specifications
PDC drill bit specifications are crucial for matching the bit to the drilling application, ensuring peak performance and efficiency. These detailed parameters outline the bit’s physical characteristics, material composition, and design features, all tailored to specific drilling environments.
Key PDC bit specifications include:
- Bit Diameter: The precise measurement of the bit’s cutting face, which directly determines the size of the borehole, ranging from small exploration holes to large production wells.
- API Pin Connection: Specifies the standardized threaded connection at the top of the bit, ensuring compatibility with the drill string and reliable transmission of torque and weight.
- Body Type (Matrix or Steel): Defines the material of the bit’s main structure; matrix bodies (tungsten carbide) offer high abrasion resistance, while steel bodies provide toughness and are often repairable.
- Number of Blades: Indicates how many cutting structures extend from the bit body, influencing stability, cuttings removal, and the distribution of cutting forces across the formation.
- Cutter Size and Type: Details the dimensions and specific geometry of the PDC cutters, which are chosen based on rock hardness and abrasiveness to optimize shearing efficiency and wear resistance.
- Nozzle Quantity and Size: Specifies the number and diameter of the fluid ports, which control the flow rate and jet velocity of drilling fluid for effective bit cleaning and cuttings evacuation.
PDC Bit Sizes for Horizontal Drilling (HDD)
Bit Size (inches) | Bit Size (mm) | Application |
3-1/2 | 89 | Pilot hole |
4-1/2 | 114 | Pilot hole |
5-1/2 | 140 | Pilot hole |
6 | 152 | Pilot hole |
6-1/2 | 165 | Pilot hole |
Up to 27.56 | 700 | Reaming |
How Do Size and Blade Count Relate to Performance
The size and blade count of a PDC drill bit are critical design features that profoundly influence drilling performance, affecting penetration rates, stability, and durability in various geological formations. Selecting the optimal combination ensures efficient operation and extended bit life.
- Bit Size: Larger bits (e.g., 12 1/4″ to 26″) provide increased stability and durability, distributing cutting loads over a greater surface area, which is ideal for deep wells and harder formations, though they may demand higher torque.
- Smaller Bit Size: Conversely, smaller bits (e.g., 3-1/2″ to 6″) offer more aggressive cutting and achieve higher rates of penetration (ROP) in softer formations like shale or sandstone, but can experience faster wear in abrasive conditions.
- More Blades: Bits with a higher blade count (e.g., 6-9 blades) enhance stability and durability by spreading the cutting load across numerous cutters, making them highly effective for hard or abrasive formations where wear resistance is paramount.
- Fewer Blades: Bits with fewer blades (e.g., 3-5 blades) enable more aggressive cutting in soft formations, significantly improving the rate of penetration; however, they might compromise stability in very hard formations, risking increased wear.
Most Common PDC Bit Sizes in the Market
In the market, PDC bits come in various standardized sizes to accommodate diverse drilling applications, primarily in the oil and gas industry, where they correspond to casing programs for optimal hole sizing. These common sizes ensure compatibility and efficiency across different drilling phases, from surface to production sections, and are designed to maintain hole specifications even with bit wear.
Here are some of the most common PDC bit sizes:
- 3 7/8″ (3.875 decimal): Often used in surface sections.
- 4 1/4″ (4.25 decimal): Also common for surface sections.
- 4 3/4″ (4.75 decimal): Frequently applied in intermediate sections.
- 5 3/8″ (5.375 decimal): Another popular size for intermediate drilling.
- 6 1/4″ (6.25 decimal): A common choice for intermediate sections.
- 6 3/4″ (6.75 decimal): Often utilized in intermediate drilling.
- 7 7/8″ (7.875 decimal): Widely used in production sections.
- 8 3/4″ (8.75 decimal): A key size for production sections.
- 9 7/8″ (9.75 decimal): Another common size for production drilling.
- 12 1/4″ (12.25 decimal): Typically employed for deep wells.
- 17 1/2″ (17.5 decimal): Also used for deep well applications.
- 26″ (26 decimal): Commonly found in surface sections, particularly for larger casings.
For a detailed overview, here is a PDC bit size chart:
Bit Size (inches) | Bit Size (Decimal) | Common Application |
3 7/8 | 3.875 | Surface sections |
4 1/4 | 4.25 | Surface sections |
4 3/4 | 4.75 | Intermediate sections |
5 3/8 | 5.375 | Intermediate sections |
6 1/4 | 6.25 | Intermediate sections |
6 3/4 | 6.75 | Intermediate sections |
7 7/8 | 7.875 | Production sections |
8 3/4 | 8.75 | Production sections |
9 7/8 | 9.75 | Production sections |
12 1/4 | 12.25 | Deep wells |
17 1/2 | 17.5 | Deep wells |
26 | 26 | Surface sections |
Can a Single PDC Bit Size Work for Multiple Projects?
While it’s generally not advisable to use a single PDC bit size for multiple drilling projects, there can be exceptions. The suitability of a bit size is highly dependent on the unique requirements of each project. Here’s a breakdown:
Generally Not Recommended: Using one PDC bit size across diverse projects is typically not practical. Each drilling operation has specific needs related to geological formations, wellbore design, and equipment.
Factors Influencing Bit Size Choice:
- Formation Variability: Different rock types (soft vs. hard) require specific bit designs and sizes for optimal penetration and durability.
- Casing Program Differences: The bit size must align precisely with the casing program, which can vary significantly between wells and projects.
- Depth and Rig Capabilities: Deeper wells often necessitate larger bits for stability, and rig limitations can restrict the range of usable bit sizes.
Exceptions for Identical Conditions: A single bit size might be feasible if multiple projects share nearly identical conditions, such as drilling several wells in the same field with consistent casing programs and geological formations.
Potential Trade-offs: While using a single size might reduce inventory costs, it could compromise drilling efficiency if the bit is not optimized for the specific formation, potentially increasing overall drilling time and costs.
How to Customize Your Desired PDC Bit Size?
Customizing a PDC bit ensures optimal performance for specific drilling challenges. This process involves a detailed assessment of operational needs and geological conditions to tailor the bit’s dimensions and features precisely to your project’s requirements.
Step 1: Define Your Drilling Requirements
Begin by clearly outlining your project’s needs. This includes the exact hole diameter, anticipated rock formations (hardness, abrasiveness), desired penetration rates, and specific wellbore trajectory, all crucial for determining the appropriate bit size and design.
Step 2: Consult with Manufacturers
Engage with experienced PDC bit manufacturers or suppliers, such as Sinodrills. Provide them with your detailed drilling requirements and data. Their expertise is invaluable for recommending optimal designs and confirming feasible customization options for your specific bit size.
Step 3: Review Design Proposals
Carefully examine the bit design proposals from the manufacturer. These will detail the proposed bit size, cutter layout, blade count, and nozzle configuration. Ensure the proposed design aligns perfectly with your defined drilling objectives and operational parameters.
Step 4: Finalize Specifications and Production
Once satisfied, approve the final bit specifications. The manufacturer will then proceed with the production of your customized PDC bit. This ensures you receive a tool precisely engineered for your unique drilling environment, maximizing efficiency and performance.
Conclusion
Navigating the nuances of PDC bit sizes and effectively utilizing a PDC bit size chart are indispensable skills for successful drilling. We’ve explored how precise sizing impacts everything from drilling efficiency to wellbore integrity, emphasizing that a well-chosen bit is a cornerstone of a productive and cost-effective operation.
The information gleaned from a detailed PDC bit size chart empowers you to make informed decisions, ensuring your drilling project proceeds smoothly and meets all technical specifications. Mastering bit sizing prevents common pitfalls, optimizes your equipment’s performance, and ultimately contributes to the overall profitability of your drilling ventures.
For all your drilling needs, including a wide array of PDC drill bits in various sizes and other high-quality drilling tools, look no further than Sinodrills. We offer wholesale solutions designed to deliver superior performance and reliability. Partner with Sinodrills to ensure you always have the right size and the best tools for the job.