In the intricate world of drilling, few metrics hold as much sway as the Rate of Penetration (ROP). This crucial indicator directly impacts project timelines, operational costs, and overall efficiency. A higher ROP means faster well completion, translating into significant savings and quicker access to valuable resources, making its optimization paramount for any drilling operation.
Let’s delve deep into the multifaceted factors influencing ROP. We will explore everything from bit selection and drilling parameters to downhole conditions and fluid dynamics. Our aim is to equip you with the knowledge to consistently maximize drilling speed and performance.
What is the Rate of Penetration in Drilling?
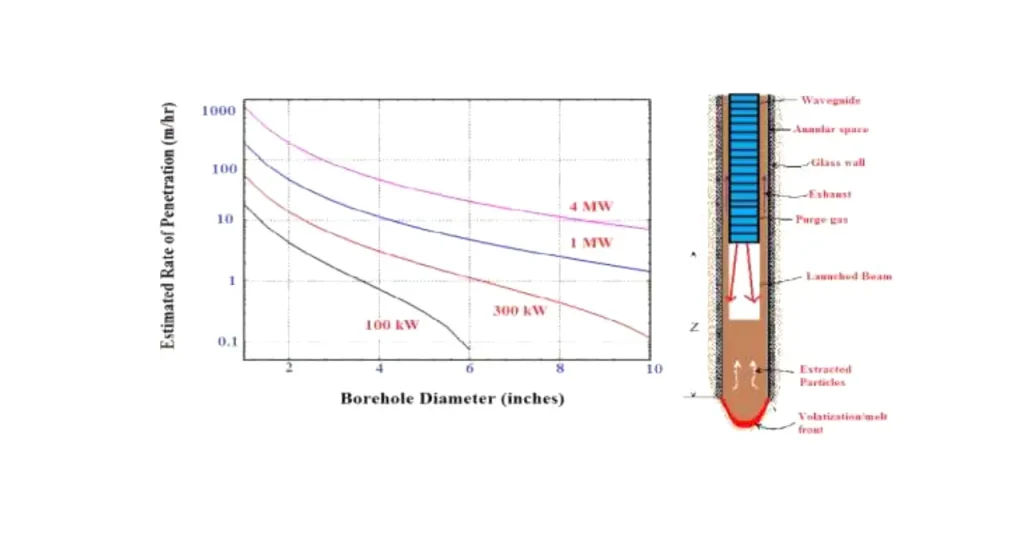
The Rate of Penetration (ROP) in drilling refers to the speed at which a drill bit advances through rock or other geological formations.
It is typically measured in feet per hour (ft/hr) or meters per hour (m/hr). ROP is a crucial performance metric in drilling operations, directly impacting the overall time and cost of a well. Optimizing ROP involves balancing various factors such as bit type, weight on bit, rotary speed, drilling fluid properties, and formation characteristics to achieve the most efficient and economical drilling process.
How to Calculate the Rate of Penetration?
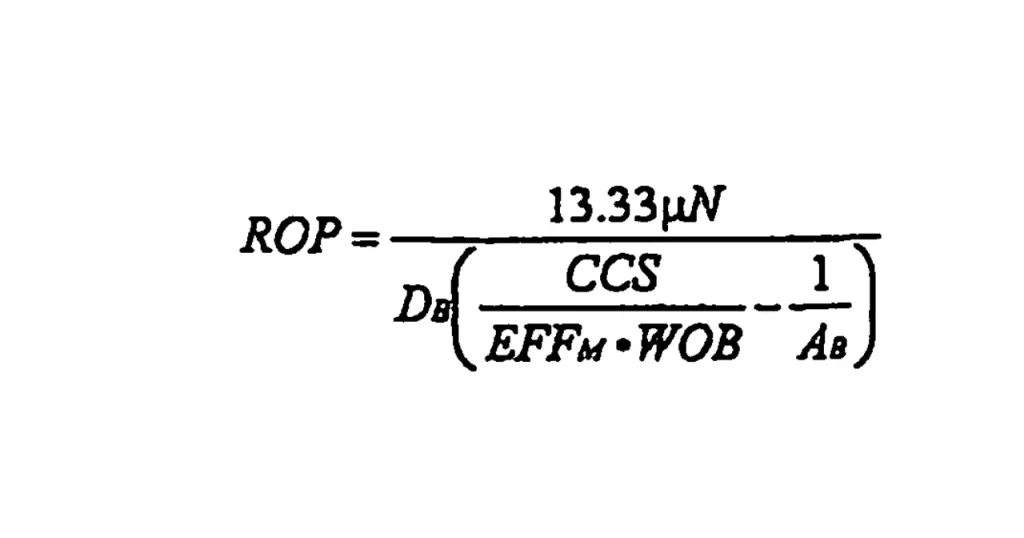
Calculating the Rate of Penetration (ROP) is fundamental to evaluating drilling efficiency. It provides a clear metric for how quickly the drill bit advances through the formation. Understanding this calculation is crucial for optimizing drilling parameters and making informed decisions to enhance operational performance.
Step 1: Identify Key Data
To calculate ROP, the primary data required are the change in measured depth and the corresponding time taken to drill that interval. Accurate depth readings from drilling instruments and precise time measurements are essential. This data forms the basis for any ROP calculation, ensuring reliability.
It is crucial to record these measurements carefully, noting the start and end depths for a specific drilling period. Any interruptions, such as connections or equipment adjustments, should be excluded from the drilling time to ensure the calculation reflects the actual time the bit was on bottom and making hole.
Step 2: Apply the Formula
The basic formula for Rate of Penetration (ROP) is straightforward: ROP = Distance Drilled / Time Taken.
The “Distance Drilled” is the difference between the final measured depth and the initial measured depth of the interval. The “Time Taken” is the total active drilling time for that same interval.
For example, if the drill bit advanced 100 feet in 2 hours of actual drilling time, the ROP would be 100 feet / 2 hours, which equals 50 feet per hour. This simple division provides the average penetration rate over the specified drilling period, offering a clear performance indicator.
Step 3: Ensure Consistent Units
Consistency in units is paramount for accurate ROP calculation. If depth is measured in feet, time should typically be in hours, resulting in ROP in feet per hour (ft/hr). Similarly, if meters are used for depth, then meters per hour (m/hr) would be the resulting unit.
Before performing the calculation, always verify that both your distance and time measurements are expressed in compatible units. Mismatched units will lead to incorrect ROP values, rendering the data unreliable for performance analysis or comparison with industry benchmarks, thus hindering optimization efforts.
What Are the Factors Affecting the Rate of Penetration in Drilling?
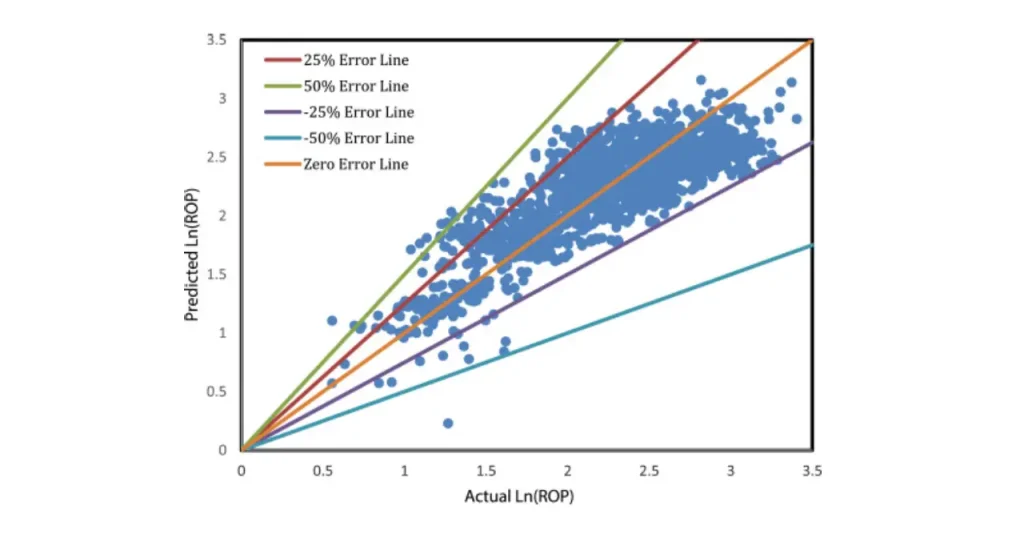
The Rate of Penetration (ROP) is a dynamic metric influenced by a complex interplay of factors, dictating drilling efficiency and project costs. Understanding these variables is crucial for optimizing operations. By effectively managing them, drillers can significantly enhance drilling speed, minimize downtime, and ensure successful well delivery.
Drill Bit Type and Condition
The choice of drill bit (PDC vs. roller cone) and its specific design, including cutter type, size, and layout, fundamentally impacts ROP. A bit designed for the specific formation being drilled will maximize cutting efficiency. Furthermore, the bit’s dull condition, such as worn, chipped, or lost cutters, directly reduces its ability to penetrate, thus lowering ROP.
Weight on Bit (WOB)
Weight on Bit (WOB) is the axial force applied to the drill bit, pressing it against the formation. Increasing WOB generally leads to higher ROP, as it provides more energy for the bit to break rock. However, excessive WOB can cause bit damage, reduce stability, and lead to unwanted drilling dysfunction like stick-slip, ultimately hindering penetration.
Rotary Speed (RPM)
Rotary speed (RPM) is the rotational velocity of the drill bit. Higher RPM typically increases the frequency with which cutting elements engage the formation, thereby boosting ROP. There is an optimal RPM range for each bit and formation; exceeding this can cause excessive heat, premature bit wear, vibration, or bit whirl, negatively affecting ROP and bit life.
Drilling Fluid Properties (Hydraulics)
Drilling fluid properties, including density, viscosity, and most critically, hydraulics (flow rate and nozzle velocity), significantly influence ROP. The fluid’s ability to effectively clean the bit face, transport cuttings away from the bottom of the hole, and cool the cutters is paramount. Poor hydraulics can lead to bit balling, re-drilling of cuttings, and overheating, all of which drastically reduce ROP.
Formation Characteristics
The geological properties of the rock being drilled are primary determinants of ROP. Factors such as rock strength, abrasiveness, ductility, porosity, and presence of fractures or interbeds directly influence how easily the formation can be drilled. Softer, more homogeneous formations generally allow for higher ROPs compared to hard, abrasive, or highly fractured rock.
Bottom Hole Assembly (BHA) Design
The design and stability of the Bottom Hole Assembly (BHA) profoundly affect ROP by influencing weight transfer, bit stability, and downhole vibration. A well-designed BHA provides proper stiffness, weight, and stabilization, ensuring optimal force application to the bit. An unstable BHA can induce harmful vibrations (e.g., bit whirl, stick-slip), leading to inefficient cutting, bit damage, and reduced ROP.
Bit Cleaning (Nozzle Optimization)
Effective bit cleaning, primarily achieved through optimized drilling fluid hydraulics and nozzle design, is critical for maintaining ROP. Nozzles direct high-velocity fluid jets to clear cuttings from the bit face and cool the cutters. Sub-optimal nozzle configuration, insufficient flow rates, or plugged nozzles can lead to cuttings accumulation (bit balling), preventing cutters from engaging new rock and severely reducing ROP.
How Drilling Fluid Properties Affect the Rate of Penetration?
Drilling fluid properties significantly influence the Rate of Penetration (ROP) by affecting how effectively cuttings are removed, how well the bit is cooled, and the overall downhole environment. Optimizing these properties is crucial for maximizing drilling efficiency:
- Viscosity: High viscosity can hinder cutting removal, leading to bit balling and reduced ROP, while too low viscosity might not adequately transport cuttings.
- Density: Fluid density impacts hydrostatic pressure, which can affect differential pressure across the bit and influence how easily rock breaks.
- Filtration/Filter Cake: Poor fluid loss control can lead to a thick filter cake, increasing friction and potentially sticking the drill string, thereby slowing ROP.
- Solids Content: High solids content, especially fine, low-gravity solids, can increase fluid viscosity and abrade bit components, negatively impacting ROP.
- pH and Chemical Composition: The fluid’s chemistry can affect rock stability and the bit’s interaction with the formation, influencing drilling efficiency.
How to Optimize the Rate of Penetration in Drilling?
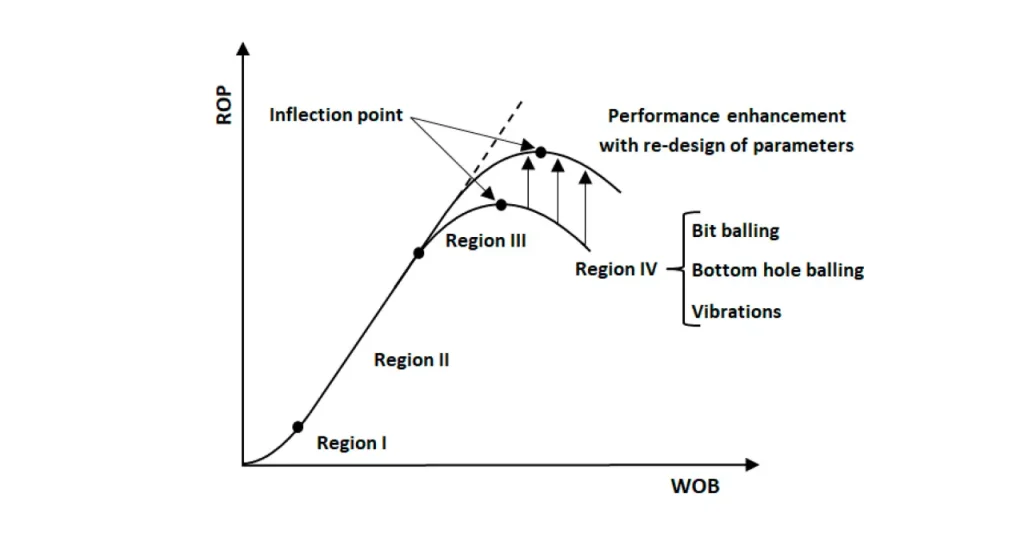
Optimizing the Rate of Penetration (ROP) is paramount for efficient and cost-effective drilling operations. It involves a systematic approach to fine-tuning various parameters. By applying key strategies, drillers can significantly enhance drilling speed, reduce well completion times, and improve overall project profitability.
Step 1: Select the Right Drill Bit
Choosing the appropriate drill bit type and design for the specific geological formation is fundamental. This involves matching bit cutter type, size, and aggressiveness to the rock’s hardness, abrasivity, and homogeneity. The right drill bit ensures efficient rock removal, minimizing energy waste and maximizing penetration capability for faster drilling.
Step 2: Optimize Weight on Bit (WOB)
Applying the optimal Weight on Bit (WOB) is crucial. Too little WOB results in insufficient cutter engagement, leading to low ROP. Conversely, excessive WOB can damage the bit, induce undesirable vibrations, and compromise stability. Fine-tuning WOB ensures cutters efficiently break rock without risking premature bit wear or failure.
Step 3: Adjust Rotary Speed (RPM)
Properly adjusting the Rotary Speed (RPM) works in conjunction with WOB to maximize ROP. Higher RPM increases cutter engagement frequency. However, exceeding an optimal range can generate excessive heat, accelerate bit wear, and cause harmful vibrations. Finding the sweet spot for RPM enhances cutting efficiency and extends bit life.
Step 4: Enhance Hydraulics and Fluid Properties
Optimizing drilling fluid properties and hydraulics is vital for effective bit cleaning and cooling. Sufficient flow rate and nozzle velocity ensure cuttings are efficiently removed from the bit face, preventing balling. Well-managed fluid properties also minimize friction and maintain downhole stability, directly contributing to higher ROP.
Step 5: Manage Drilling Dynamics
Controlling drilling dynamics, such as avoiding bit whirl, stick-slip, and excessive vibration, is critical for sustained ROP. These dysfunctions waste energy, damage the bit, and reduce cutting efficiency. Utilizing stabilization tools, adjusting drilling parameters, or employing rotary steerable systems helps maintain smooth, efficient drilling.
Step 6: Understand Formation Characteristics
Thorough understanding of the geological formation’s properties—including strength, abrasiveness, and rock type—is key to optimizing ROP. This knowledge allows for proactive adjustment of drilling parameters and bit selection. Adapting to changes in lithology ensures the bit remains efficient, preventing unexpected ROP drops and maximizing progress.
Step 7: Implement Real-time Monitoring
Utilizing real-time drilling data acquisition and analysis systems allows for immediate adjustments to optimize ROP. Monitoring parameters like torque, drag, ROP trends, and vibration levels in real-time enables drillers to identify and mitigate issues promptly. This proactive approach ensures continuous optimization and maximizes drilling performance throughout the wellbore.
Conclusion
Ultimately, mastering the Drilling Rate of Penetration is a continuous journey of optimization and adaptation. By diligently applying the principles discussed in this ultimate guide, you can significantly enhance your drilling operations, achieve superior efficiency, and unlock substantial economic benefits, transforming potential challenges into successes downhole.
From meticulously selecting the right drill bit and fine-tuning drilling parameters to expertly managing hydraulics and understanding formation characteristics, every decision impacts ROP. Continuous monitoring and data analysis are key to refining your approach, ensuring each drilled foot is achieved with maximum speed and minimal cost.
For all your drilling needs, including wholesale drill bits and comprehensive drilling tools that empower superior ROP and overall operational excellence, look no further than Sinodrills. Our commitment to quality and performance ensures you have the right equipment to tackle any challenge and optimize your drilling projects.