PDC (Polycrystalline Diamond Compact) drill bits are essential, high-performance tools in the drilling industry, known for their efficiency and speed. However, even the most robust bits can suffer wear and tear, or damage, during demanding operations. Replacing these valuable assets frequently can significantly inflate drilling costs and impact project profitability.
This blog post explores the vital process of PDC bit repair, a smart and sustainable solution designed to breathe new life into damaged drill bits. We’ll delve into how professional repair services can effectively restore a bit’s cutting efficiency and extend its operational lifespan, saving you time and considerable financial resources.
PDC Bit Damage Reasons
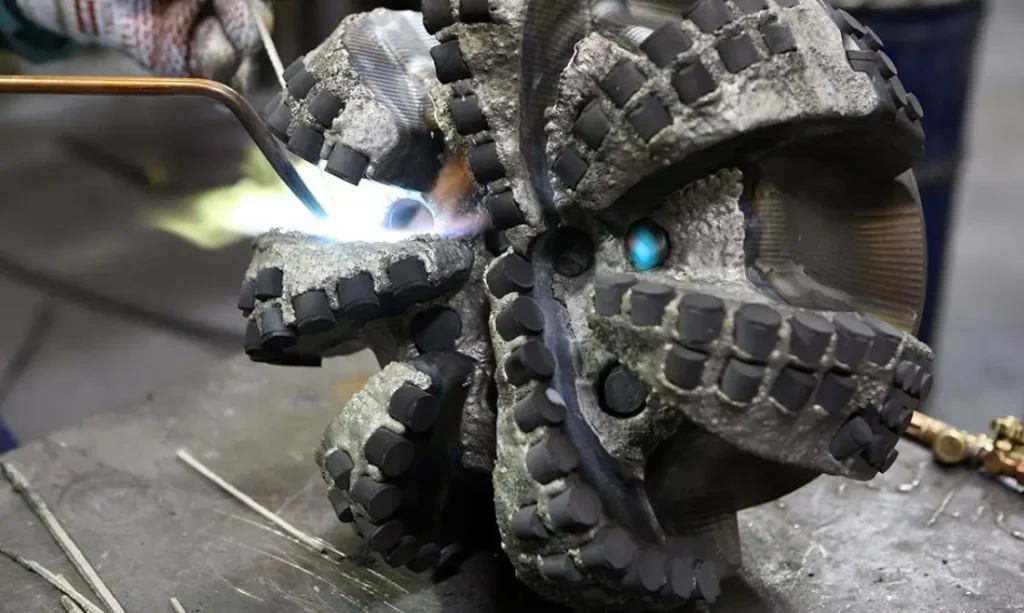
PDC drill bits are engineered for extreme durability, yet they can still experience breakage due to the harsh and unpredictable downhole environment. Understanding the common causes of PDC bit damage is crucial for preventing costly downtime and optimizing drilling operations.
Impact Damage
PDC drill bits can break due to sudden, high-impact forces encountered when drilling through highly fractured formations, interbedded hard streaks, or encountering unexpected inclusions like chert or pyrite. These impacts can cause the brittle diamond layer of the PDC cutters to chip, crack, or even detach from the tungsten carbide substrate, leading to premature bit failure.
Thermal Degradation
Excessive heat generated by friction during drilling, especially in hard or abrasive formations, can lead to thermal degradation of PDC cutters. The diamond layer can lose its hardness and wear resistance at high temperatures, causing it to soften and wear rapidly. This thermal damage weakens the cutter, making it more susceptible to breakage under normal drilling loads.
Wear and Abrasion
Continuous contact with abrasive rock formations, such as sandstone or quartzite, causes gradual wear on the PDC cutters. As the diamond layer wears down, the cutting edge becomes dull, increasing friction and heat. Eventually, the worn cutters lose their ability to efficiently shear the rock, leading to increased stress on the remaining cutters and ultimately, breakage.
Bit Whirl and Vibrations
Dynamic dysfunctions like bit whirl (when the bit rotates eccentrically) and stick-slip (intermittent sticking and freeing of the bit) induce severe torsional and lateral vibrations. These uncontrolled vibrations generate high stress concentrations on the PDC cutters and the bit body, leading to fatigue cracks and eventual breakage, often far exceeding normal operational stresses.
Manufacturing Defects
Although rare with reputable manufacturers, inherent manufacturing defects can contribute to PDC bit breakage. These might include inconsistencies in the bonding of the diamond layer to the substrate, micro-cracks within the PDC cutter itself, or flaws in the bit body material. Such defects can create weak points that fail under normal drilling conditions.
How to Repair PDC Drill Bits?
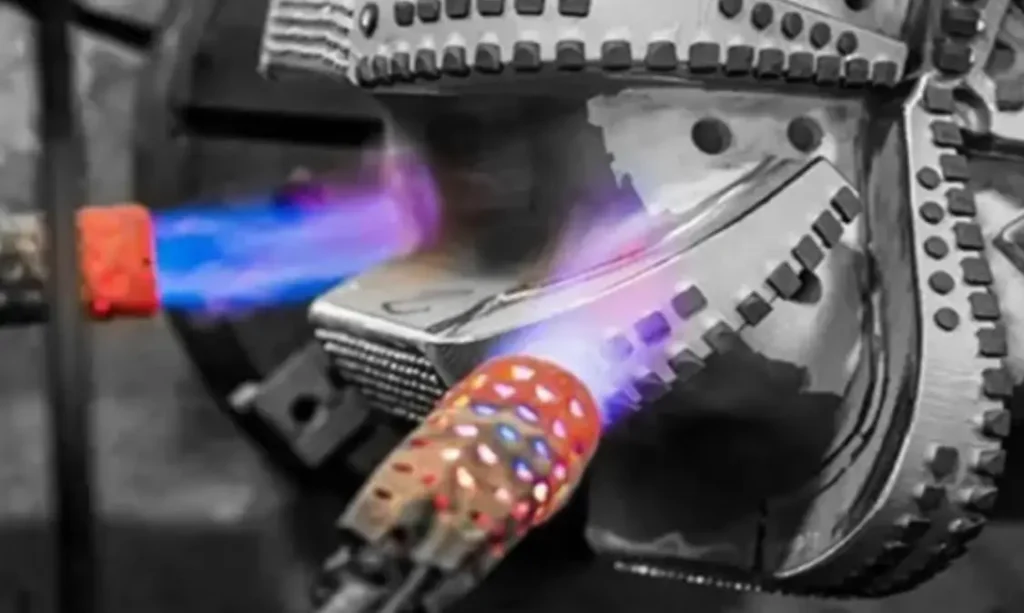
Repairing PDC drill bits is a specialized process that can significantly extend their lifespan and restore performance. It involves several meticulous steps, from initial assessment to final quality control, ensuring the bit is ready for continued demanding downhole operations.
Step 1: Initial Inspection and Cleaning
The first step involves a thorough visual inspection of the damaged PDC drill bit to identify all forms of wear, chipping, cracking, and missing cutters. This initial assessment helps determine the extent of the damage and feasibility of repair.
Following inspection, the bit undergoes a rigorous cleaning process to remove all drilling mud, rock cuttings, and debris. This ensures that hidden damages are revealed and prepares the surface for subsequent repair procedures.
Step 2: Cutter Removal and Surface Preparation
Damaged or worn-out PDC cutters are carefully removed from their pockets on the bit body. This process requires precision to avoid further damage to the bit structure. Specialized tools are often used to extract the compromised cutters precisely.
Once the old cutters are removed, the cutter pockets and surrounding areas are meticulously cleaned and prepared. This involves grinding or machining the surfaces to create a clean, stable, and optimally shaped base for the new PDC cutters to be brazed onto.
Step 3: Cutter Replacement and Brazing
New PDC cutters, matching the original specifications or upgraded for improved performance, are then carefully positioned into the prepared pockets. The selection of the correct cutter type and size is crucial for restoring the bit’s cutting efficiency.
The new cutters are then securely brazed into place using high-temperature brazing alloys. This creates a strong metallurgical bond between the PDC cutter and the bit body, ensuring durability and optimal performance in downhole conditions.
Step 4: Body Repair and Reinforcement
Beyond cutter replacement, the bit body itself might require repair for cracks, erosion, or material loss. Advanced welding techniques and specialized hardfacing materials are used to rebuild and reinforce damaged sections of the bit.
This body repair not only restores the structural integrity of the bit but also enhances its resistance to future wear and tear. Proper reinforcement ensures the bit can withstand the rigors of continued drilling operations effectively.
Step 5: Final Grinding and Quality Control
After all repairs are complete, the bit undergoes precision grinding to ensure the proper exposure and geometry of the new and existing cutters. This step is crucial for achieving optimal cutting efficiency and balanced bit performance.
Finally, the repaired PDC drill bit undergoes a comprehensive quality control inspection. This includes checks for cutter alignment, braze integrity, body soundness, and overall dimensional accuracy, ensuring it meets strict performance standards for safe and efficient redeployment.
PDC Drill Bit Refurbishment
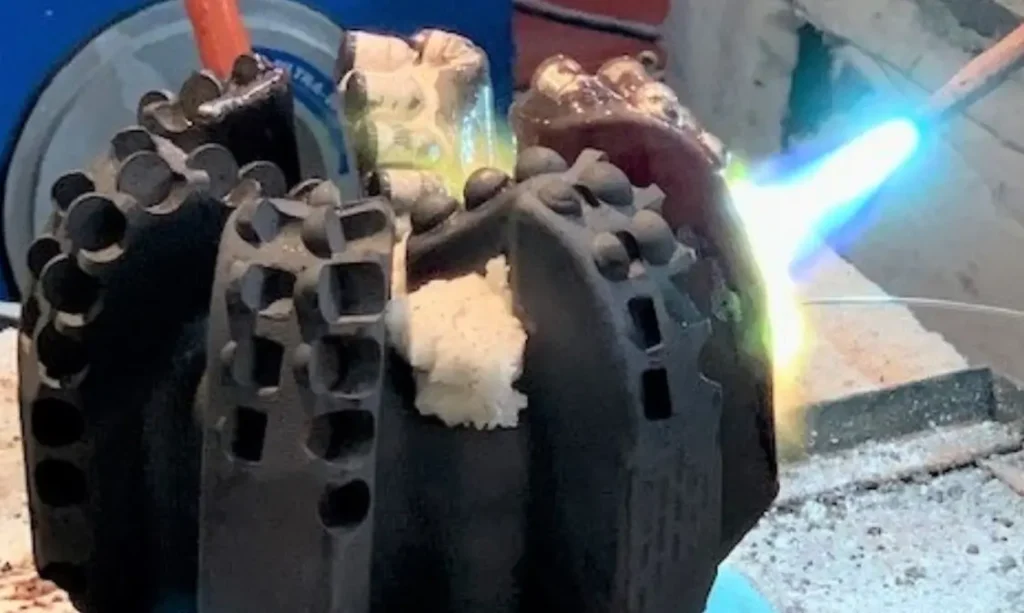
PDC drill bit refurbishment is a vital process that restores damaged or worn PDC bits to near-original condition, significantly extending their service life. This cost-effective solution minimizes the need for new bit purchases, enhancing operational efficiency and sustainability within the drilling industry.
- Inspection and Assessment: Thoroughly inspect the bit for cutter wear, chips, cracks, and body damage. This initial stage determines the feasibility and scope of the refurbishment, identifying all areas needing attention.
- Cutter Removal and Replacement: Carefully remove damaged or worn PDC cutters from their pockets. New, high-quality PDC cutters are then precisely brazed into place, restoring the bit’s cutting efficiency and aggressiveness.
- Body Repair and Reinforcement: Address any cracks, erosion, or material loss on the bit body. Advanced welding and hardfacing techniques rebuild and strengthen the bit’s structure, enhancing durability and preventing future damage.
- Nozzle and Gauge Repair: Ensure optimal hydraulic performance by repairing or replacing worn nozzles. The bit’s gauge area is also restored to maintain proper hole size and stability during drilling operations.
- Final Grinding and Quality Control: Precision grinding ensures proper cutter exposure and geometry. A rigorous final inspection verifies the refurbishment quality, ensuring the bit meets performance standards before redeployment.
How to Extend Your PDC Bit Lifespan?
Extending the lifespan of your PDC drill bits is paramount for maximizing drilling efficiency and reducing operational costs. By implementing best practices for selection, operation, and maintenance, you can significantly enhance their durability and performance in the demanding downhole environment.
Here are some key tips to help you maximize your PDC bit’s lifespan:
- Select the Right Bit for the Formation: Matching the bit’s design (cutter type, size, layout, and blade count) to the specific geological conditions and rock properties is crucial. An improperly matched bit will wear prematurely.
- Optimize Drilling Parameters: Adjusting weight on bit (WOB), rotational speed (RPM), and hydraulic flow rates to suit the formation prevents excessive stress, heat buildup, and vibrations, all of which can damage cutters.
- Maintain Proper Hydraulics: Ensure adequate drilling fluid flow through the nozzles for effective bottom-hole cleaning and cooling of the cutters. Poor hydraulics can lead to cutter wear, bit balling, and overheating.
- Monitor and Mitigate Vibrations: Implement strategies to minimize bit whirl, stick-slip, and other dynamic dysfunctions. These vibrations cause significant impact damage and fatigue to PDC cutters and the bit body.
- Conduct Regular Inspections and Maintenance: After each run, thoroughly inspect the bit for cutter wear, damage, or body erosion. Promptly address any issues through professional repair to prevent further deterioration and extend usable life.
- Proper Handling and Storage: Always handle PDC bits with care to avoid accidental impact damage to the cutters. Store them in a clean, dry environment, protected from physical impact and environmental factors.
Conclusion
In conclusion, investing in professional PDC bit repair is a strategic decision that offers substantial benefits beyond simply fixing a broken tool. It’s about optimizing your drilling budget, reducing environmental impact through extended tool life, and ensuring that your operations maintain peak efficiency. Timely and expert repair can significantly reduce your overall tooling expenses.
By choosing to repair rather than constantly replace, you contribute to a more sustainable drilling practice while simultaneously enhancing your project’s profitability. A well-repaired PDC bit performs comparably to a new one in many aspects, delivering the cutting power and stability you need for successful operations.
For all your drilling needs, including high-quality PDC bit repair services or if you’re looking to get wholesale PDC drill bits or drilling tools from our Sinodrills, we are your trusted partner. Contact us today to learn more about how we can help you maximize performance and extend the lifespan of your valuable drilling assets.