When it comes to creating holes in materials, drill bits and reamers are two fundamental tools, yet they serve distinct purposes. While both remove material, their design and function are optimized for very different stages of the hole-making process.
Understanding these differences is crucial for achieving desired precision and surface finish in various applications, from construction to manufacturing. This guide will clarify the unique roles of drill bits and reamers, helping you select the right tool for every task.
What is a Reamer?
A reamer is a precision rotary cutting tool used in machining to enlarge and refine pre-drilled or cored holes. Unlike a drill bit that creates the initial hole, a reamer’s purpose is to remove a minimal amount of material to achieve highly accurate dimensions, improved roundness, and a smooth surface finish.
What is a Drill Bit?
A drill bit is a cutting tool designed to create cylindrical holes in various materials. It works by rotating and pressing into the workpiece, with cutting edges at its tip shearing away material to form a hole. Drill bits come in diverse types, each optimized for different materials and hole-making applications.
Reamer vs Drill Bit
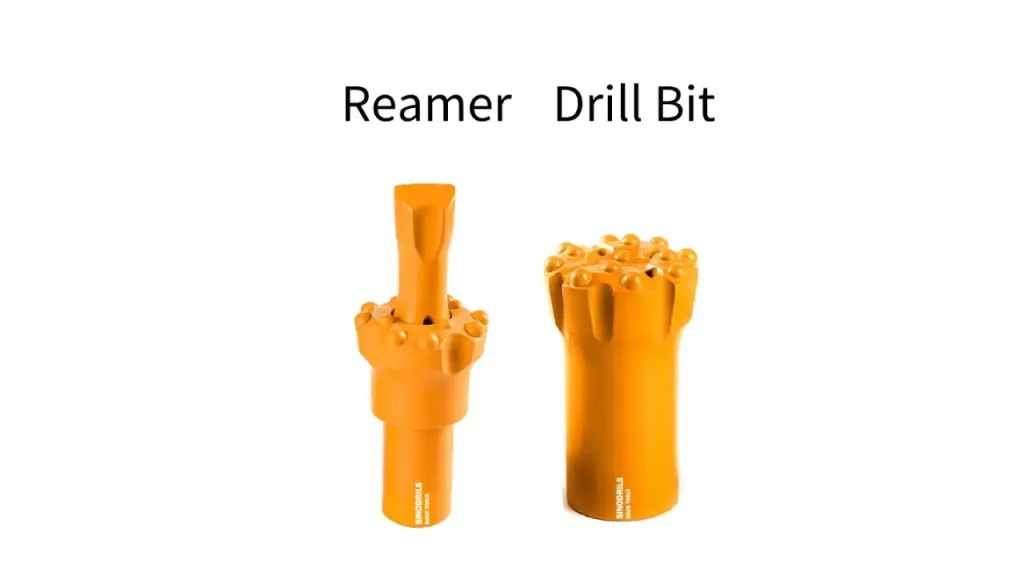
Understanding the fundamental differences between reamers and drill bits is essential for any precision machining or construction task within the rock drilling industry. While both tools create holes, their design, function, and the quality of the resulting bore are markedly distinct.
This comparison will detail their unique roles, helping you select the appropriate tool for achieving optimal results in your rock drilling projects.
Purpose
Drill bits are primary hole-making tools in the rock drilling industry, designed for efficient material removal to create an initial bore in rock formations. Their main objective is to quickly penetrate the geological strata and establish a pilot hole or production bore, often as a first pass.
Reamers, conversely, are finishing tools in rock drilling, especially in horizontal directional drilling (HDD) or similar applications. Their purpose is not to create a hole from scratch, but to refine and enlarge an existing pilot bore. They are used to achieve a very precise diameter, improve the bore’s concentricity, and prepare it for pipeline or conduit installation.
Material Removal
Drill bits in rock drilling are designed for aggressive material removal. Their cutting elements (e.g., tricone cones, PDC cutters) are engineered to efficiently crush, shear, and abrade rock, enabling rapid progression through dense geological formations. The bit’s design prioritizes penetration rate and footage.
Reamers, particularly HDD rock reamers, remove a larger volume of material than typical machining reamers, but they are still refining an existing bore. Their multiple cutting structures crush and cut the rock from the pilot hole’s diameter to the desired final diameter, ensuring a stable and appropriately sized tunnel. This process is about controlled enlargement rather than initial penetration.
Hole Quality and Precision
The holes produced by drill bits in rock drilling can have variations in diameter and may not always be perfectly round, especially in inconsistent rock formations. While adequate for many initial drilling purposes, they often require further processing for final product installation.
Reamers in rock drilling are specifically engineered to achieve high precision for the final bore. They produce holes with very consistent diameters, improved roundness, and a stable bore wall, which is crucial for successful pipeline pull-back and long-term integrity of the installed product.
Cutting Edges/Structures
Drill bits for rock drilling feature robust cutting structures tailored to specific rock types. This can include rotating cones with tungsten carbide inserts (TCI) or milled teeth (for tricone bits), or fixed cutters (PDC bits) with synthetic diamond elements. These are designed for high impact, crushing, and shearing forces.
Rock reamers, especially those for HDD, also feature robust cutting structures (e.g., roller cones with TCI, or fixed cutter designs). They are designed to progressively enlarge the bore with multiple cutting faces or elements, often arranged to provide balanced cutting and bore stability as they are pulled or pushed through the rock.
Application Sequence
In almost all rock drilling operations requiring hole enlargement, drill bits are used first to create the initial pilot hole. This preliminary hole establishes the trajectory and removes the bulk of the rock, providing the necessary path for subsequent reaming operations.
Reamers in rock drilling are always used after a pilot hole has been drilled. They are the subsequent step, sometimes one of several passes with increasing reamer sizes, to achieve the final desired bore diameter for the installation of utilities like pipelines, conduits, or cables.
Comparison Table: Reamer vs. Drill Bit (Rock Drilling Industry)
Aspect | Reamer (e.g., HDD Rock Reamer) | Drill Bit (e.g., Tricone Bit, PDC Bit) |
Primary Purpose | Hole enlargement and finishing for installation | Initial hole creation/penetration |
Material Removal | Controlled enlargement from pilot hole | Aggressive initial penetration and boring |
Hole Quality | Consistent diameter, stable, suitable for product pull-back | Initial bore, can be less precise/rough |
Cutting Edges/Structures | Multiple cutting elements designed for crushing/cutting existing bore | Designed for direct rock destruction/penetration |
Application Order | Always follows pilot drilling | First tool used to create a bore |
Difference Between Drilling and Reaming
While both drilling and reaming are hole-making processes, they serve distinct purposes and are typically performed sequentially in the rock drilling industry. Drilling is the initial process of creating a bore, whereas reaming is a finishing process to enlarge and refine that bore.
Here are the key differences between drilling and reaming in the following:
Purpose:
- Drilling: The primary goal of drilling is to create an initial pilot hole or a production bore from solid rock. It focuses on rapid penetration and establishing the general path for the project.
- Reaming: The purpose of reaming is to enlarge and precisely finish a pre-drilled pilot hole to the required diameter for product pipe installation. It focuses on achieving accurate bore size, stability, and smooth walls.
Material Removal:
- Drilling: Drill bits are designed for aggressive material removal, cutting, crushing, and breaking large volumes of rock to create the initial cavity. Efficiency in penetration is paramount.
- Reaming: Reamers remove material in a more controlled and systematic way, gradually enlarging the existing bore. They are designed to achieve a specific final diameter and often prepare the bore for the product pull-back.
Tool Design:
- Drilling: Drill bits (e.g., tricone, PDC) have cutting structures optimized for penetrating untouched rock, often with pointed or aggressively angled elements for initial engagement.
- Reaming: Reamers (e.g., roller cone reamers) have multiple cutting elements spread across a larger diameter, designed to progressively cut and crush the rock from the pilot hole’s circumference outwards.
Hole Quality:
- Drilling: Holes created by drilling can be somewhat rough, with varying diameters and potentially irregular shapes, especially in inconsistent rock formations.
- Reaming: Reaming produces a more precise, stable, and consistently sized bore with smoother walls, crucial for the successful and safe installation of pipelines or conduits.
Application Sequence:
- Drilling: Drilling is always the first step in creating a hole in rock. It establishes the initial bore path and dimensions.
- Reaming: Reaming always follows drilling. It is a secondary or subsequent step, often performed in multiple passes with increasing reamer sizes, to achieve the final desired bore diameter.
Reaming Speed vs Drilling Speed
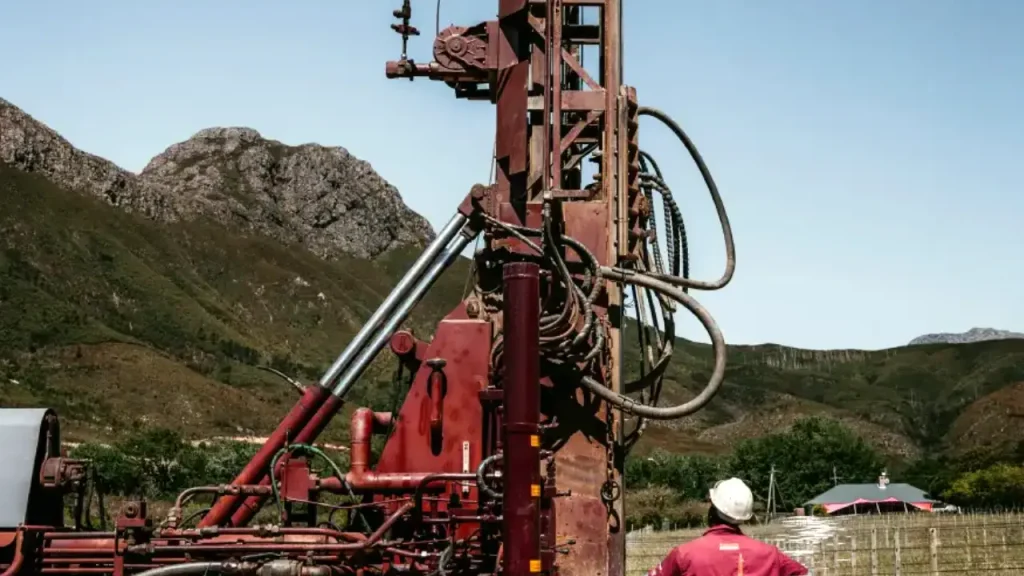
In rock drilling, “speed” refers to the rotational speed of the drill string (measured in revolutions per minute, RPM) and the rate of penetration (ROP), which is how quickly the tool advances through the rock.
Reaming and drilling operations, due to their distinct purposes and cutting mechanisms, typically require different optimal speeds to achieve efficiency, extend tool life, and ensure hole quality.
Here’s a breakdown of reaming speed vs. drilling speed in the context of rock drilling:
Drilling Speed (ROP and RPM for Drill Bits):
- Higher ROP is often desired: Drill bits are designed to penetrate virgin rock quickly. Operators aim for high rates of penetration (ROP) by balancing RPM, weight on bit (WOB), and drilling fluid flow.
- RPM varies with rock type: In softer formations, higher RPMs can be used to maximize cutting action. In harder, more abrasive rock, RPMs are often reduced to prevent excessive wear on cutters and to allow for proper rock crushing.
- Factors influencing: Rock hardness, abrasiveness, drill bit type (tricone, PDC), WOB, drilling fluid properties, and rig power all significantly influence the optimal drilling speed.
Reaming Speed (ROP and RPM for Rock Reamers):
- Lower RPM generally preferred: For HDD rock reamers, the rotational speed (RPM) is typically lower than that used for the initial pilot drilling. This reduced speed helps in achieving a smoother, more precise bore and minimizes wear on the reamer’s cutting structures.
- Controlled ROP for quality: While still aiming for efficiency, the rate of penetration (ROP) during reaming is carefully controlled to ensure the reamer properly enlarges the bore to the target diameter with minimal deviation and good wall stability.
- Factors influencing: Reamer diameter (larger reamers have higher peripheral speeds at the same RPM), rock type, reamer design (roller cone, fixed cutter), and the required bore quality dictate optimal reaming speeds. Excessive speed can lead to chatter or premature wear.
How to Choose Reamer and Drill Bits?
Choosing the right reamer and drill bit for your rock drilling project is critical for optimizing efficiency, ensuring bore integrity, and controlling costs. The selection process depends heavily on the specific geological conditions, the desired final bore size, and the type of drilling rig being used. Careful consideration of these factors will prevent delays, premature tool wear, and project setbacks.
For both drill bits and reamers, matching the tool’s design and material to the rock formation is paramount. Incorrect choices can lead to slow penetration, excessive torque, deviation from the bore path, or even tool breakage. This is why a thorough understanding of the ground conditions is the first step in making an informed decision.
Here’s how to choose:
For Drill Bits:
Rock Hardness and Abrasiveness:
- Soft to Medium Rock (e.g., shale, soft limestone): Milled tooth (MT) tricone bits are often effective, as their steel teeth can gouge and shear softer formations. PDC (Polycrystalline Diamond Compact) bits with larger cutters can also be efficient.
- Hard to Very Hard Rock (e.g., granite, basalt, hard quartzite): Tungsten Carbide Insert (TCI) tricone bits with robust, closely spaced inserts are preferred for crushing and grinding hard rock. PDC bits designed for hard rock with smaller, more numerous cutters are also an option, particularly for abrasive conditions.
- Rotary Drilling: Tricone and PDC bits are standard.
- Down-the-Hole (DTH) Hammer Drilling: Specific DTH hammer bits are used, chosen based on hammer size and rock type for percussive drilling.
- Hole Size and Depth: Larger diameter bits require more robust construction and suitable rig power. Deep holes may necessitate bits designed for extended wear life and efficient cuttings evacuation.
- Fluid Compatibility: Consider how the bit’s design (e.g., nozzle placement) integrates with the drilling fluid program for optimal cooling and cuttings removal.
For Reamers (specifically HDD Rock Reamers):
Geological Conditions:
- Consolidated Hard Rock (e.g., granite, basalt, solid sandstone): Roller cone rock reamers with TCI cutters are the most common and effective choice. The number and type of cones (e.g., chisel, conical) will vary based on rock strength.
- Fractured Rock or Cobble: Reamers with robust body designs and well-protected cutters are essential to handle irregular fragments and prevent damage. Certain basket or fly cutter designs might also be considered for clearing larger debris.
- Abrasive Rock (e.g., quartzite, chert): Reamers with high-quality, wear-resistant TCI cutters are critical to maximize tool life and maintain cutting efficiency.
Desired Bore Diameter and Product Pipe Size: The reamer’s final cutting diameter must be appropriate for the product pipe being installed (typically 1.2 to 1.5 times the product pipe’s outer diameter). For larger diameters, a series of progressively larger reamers (staging) may be necessary.
Back-Reaming vs. Fly-Cutting:
- Back-reaming: Most common, where the reamer is pulled back through the bore. The reamer’s design should facilitate efficient cuttings removal during pullback.
- Fly-cutting (often with roller cones): Can be used for initial enlargement with aggressive cutting action.
Connection Type: Ensure the reamer’s pin or box connection is compatible with your drill string’s tool joints to guarantee a secure and reliable connection.
Drilling Rig Capacity: The reamer’s size and cutting aggression must be matched to the drill rig’s pullback force and rotational torque capabilities to ensure efficient operation and prevent overload.
Fluid Management: The reamer’s design should allow for optimal drilling fluid flow to cool cutters, lubricate the bore, and effectively transport cuttings out of the hole.
Conclusion
Drill bits are your go-to for initial hole creation, designed for efficient material removal and establishing a bore. Reamers, on the other hand, are precision finishers, refining existing holes for exact dimensions, superior roundness, and smoother surface finishes.
Choosing between them hinges on whether your goal is simply to make a hole or to achieve a highly precise, ready-to-use bore. Both are indispensable, but their applications are distinct.
For all your hole-making needs, from initial drilling to final reaming precision, remember Sinodrills. We offer a comprehensive range of high-quality wholesale reamers and drill bits, manufactured to meet demanding industry standards.