Rock drilling and blasting are fundamental processes in various industries, from mining and quarrying to civil engineering projects. These techniques are essential for efficiently breaking and excavating hard rock formations, paving the way for construction and resource extraction.
This ultimate guide will delve into the intricacies of rock drilling and blasting, covering everything from the initial planning and drilling operations to explosive selection, blast design, and crucial safety considerations. Master these techniques to optimize your rock excavation projects.
What is Rock Drilling and Blasting?
Rock drilling and blasting is a fundamental and highly effective method used across various industries, including mining, quarrying, and civil engineering, for the controlled fragmentation and excavation of hard rock formations. This two-part process begins with rock drilling, where precise boreholes are created in the rock mass using specialized equipment and drill bits. The accuracy of these holes in terms of their depth, diameter, and spatial arrangement is crucial, as it directly influences the efficiency and safety of the subsequent blasting operation.
Following the drilling phase, blasting involves strategically placing explosive materials and initiation systems within the boreholes. These explosives are then detonated in a carefully timed sequence, generating powerful shock waves and rapidly expanding gases that fracture and displace the rock. The primary objective of this controlled detonation is to break the rock into manageable sizes, creating a muck pile that can be easily loaded and transported, while simultaneously minimizing unwanted side effects such as excessive ground vibrations, air blast, and uncontrolled flyrock.
What is Rock Drilling?
Rock drilling is the essential first step in the rock excavation process, involving the creation of precise holes, known as blast holes or boreholes, into a rock mass.
This is achieved using specialized drilling equipment, such as drill rigs, which utilize various types of drill bits (e.g., PDC bits, tricone bits, DTH hammers) to penetrate the rock. The accuracy of these holes in terms of their depth, diameter, and exact positioning is critical, as it directly determines the effectiveness and safety of the subsequent blasting operation.
What is Rock Blasting?
Rock blasting is the controlled use of explosives to fragment and displace rock formations that have been prepared by drilling. Once boreholes are precisely drilled into the rock, they are loaded with specific types and quantities of explosive materials, along with detonators and a carefully designed initiation system.
These explosives are then detonated in a timed sequence, generating powerful shock waves and rapidly expanding gases that fracture the rock into manageable pieces, creating a muck pile suitable for excavation, while aiming to control vibrations, noise, and flyrock.
Why is Drilling and Blasting Important?
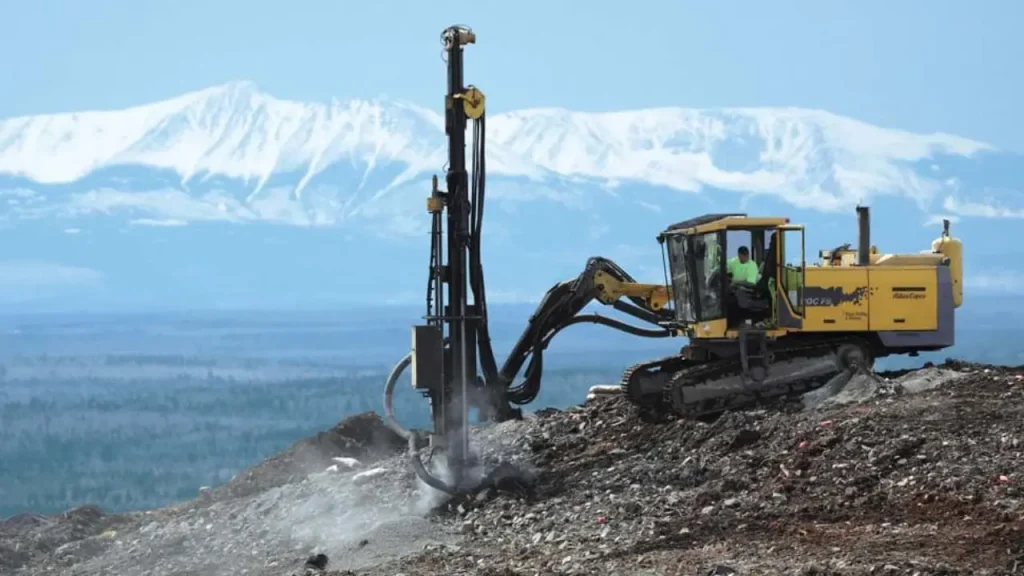
Drilling and blasting are paramount in modern heavy industries due to their unparalleled efficiency and cost-effectiveness in rock excavation. These methods allow for the rapid and large-scale removal of hard rock that would be impractical or significantly more expensive using mechanical means alone. Their importance stems from:
- Economic Efficiency: It provides the most cost-effective solution for breaking vast quantities of hard rock, minimizing per-unit excavation costs.
- Speed and Scale: Enables rapid advancement in projects requiring significant rock removal, such as large-scale mining operations, quarrying, and major infrastructure development.
- Versatility: Applicable across a wide spectrum of rock types, from soft shales to extremely hard granites, where mechanical excavation might be too slow or ineffective.
- Controlled Fragmentation: When properly designed, blasting can achieve desired rock fragmentation, optimizing downstream processes like crushing and hauling.
- Access Creation: Essential for creating access roads, foundations, tunnels, and shafts in challenging rocky terrains, facilitating further construction or resource extraction.
Rock Drilling and Blasting Tools Needed
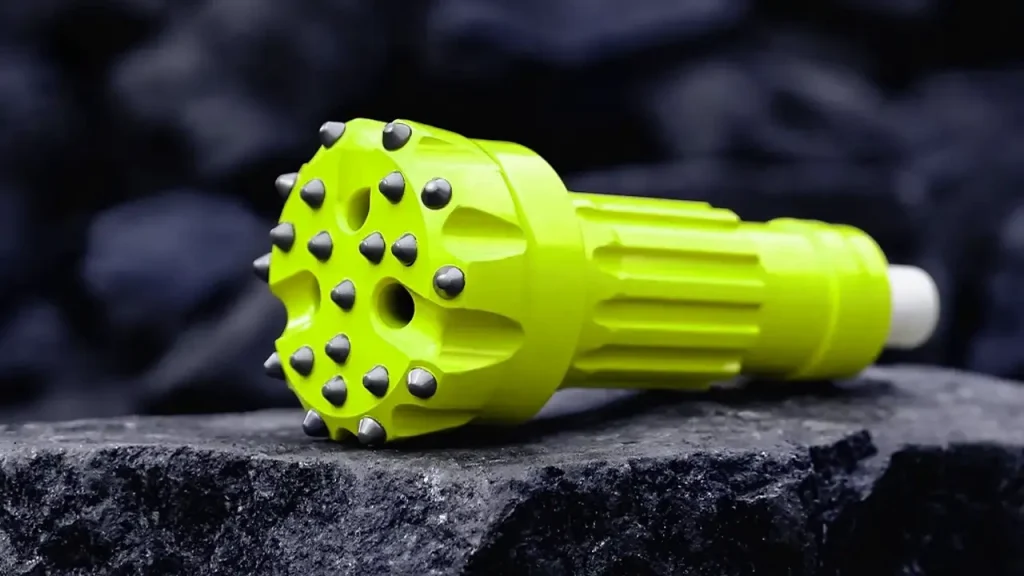
Executing effective rock drilling and blasting operations requires a specific array of specialized tools and equipment. Each plays a vital role in preparing the rock, ensuring precise explosive placement, and managing the blast safely.
Drilling Equipment
This category encompasses the machinery used to create the boreholes.
Drill Rigs: These are heavy-duty machines, often track-mounted or truck-mounted, designed to power the drilling process. They vary in size and capability, from smaller units for civil construction to massive rigs used in large-scale mining, providing the necessary thrust and rotation for drilling.
Drill Rods/Pipes: These are hollow, robust steel tubes that connect the drill rig to the drill bit, transmitting rotation and percussive energy. They come in various lengths and diameters, and multiple rods are coupled together to achieve the required borehole depth.
Drill Bits: The cutting tools at the end of the drill string that penetrate the rock.
Recommended Drill Bits
- PDC (Polycrystalline Diamond Compact) Bits: Known for high rates of penetration in softer to medium-hard formations, utilizing synthetic diamond cutters.
- Tricone Bits: Feature three rotating cones with teeth (steel or tungsten carbide inserts) that crush and chip rock, effective in a wide range of formations from soft to very hard.
- DTH (Down-The-Hole) Hammers: These tools use compressed air to deliver rapid percussive blows directly to the drill bit, ideal for hard and abrasive rock formations, often paired with button bits.
- Button Bits: Tungsten carbide buttons embedded in a steel body, used with DTH hammers or top hammer drills, offering excellent wear resistance.
- Chisel Bits: Simpler, often used for softer rock or small-diameter holes.
Compressors: Provide the high-pressure air necessary to power DTH hammers and clear cuttings from the borehole.
Dust Collection Systems: Crucial for managing airborne dust generated during drilling, improving visibility and worker safety.
Blasting Accessories
These are the components essential for safely and effectively initiating the explosives.
- Explosives/Blasting Agents: The chemical compounds that, when detonated, fragment the rock. Examples include ANFO (Ammonium Nitrate Fuel Oil), emulsions, and slurries, chosen based on rock type and desired fragmentation.
- Detonators: Devices used to initiate the main explosive charge. They can be non-electric (shock tube), electric, or electronic, with electronic detonators offering precise timing control.
- Initiation Systems: The network of detonators, lead lines, and trunk lines that connect the explosive charges and control the sequence of detonation. This includes detonating cord, shock tube systems, and electronic blasting systems.
- Blasting Machines/Initiators: Devices used to send the electrical signal or shock wave to activate the detonators in a controlled manner, ensuring safety and precise timing.
- Stemming Material: Inert material (e.g., drill cuttings, gravel) used to fill the top portion of the blast hole above the explosive charge. It helps to confine the explosive energy, directing it into the rock for better fragmentation and reducing flyrock and air blast.
- Blasting Mats/Covers: Heavy, durable mats placed over blast sites in sensitive areas to contain flyrock and reduce noise and vibration.
Safety and Monitoring Equipment
Safety is paramount in blasting operations, requiring specialized tools for monitoring and protection.
- Vibration Monitors (Seismographs): Devices used to measure ground vibrations and air blast levels generated by the blast, ensuring they remain within regulatory limits and prevent damage to nearby structures.
- Personal Protective Equipment (PPE): Includes hard hats, safety glasses, hearing protection, high-visibility clothing, and steel-toed boots for all personnel on site.
- Communication Devices: Radios and other communication tools are essential for coordinating operations and ensuring all personnel are aware of safety procedures and blast warnings.
- Warning Systems: Sirens, flags, and other visual or audible signals used to alert personnel and the public about an impending blast.
- Explosives Storage and Transport Equipment: Specialized, secure containers and vehicles designed for the safe handling, storage, and transportation of explosive materials, adhering to strict regulations.
Functions of Rock Drilling and Blasting
Rock drilling and blasting serve several critical functions across various heavy industries, enabling the efficient and controlled removal of rock. These functions include:
- Excavation and Fragmentation: The primary function is to break large, solid rock masses into smaller, manageable fragments, making them suitable for loading, hauling, and further processing (e.g., crushing).
- Site Preparation: It’s essential for preparing construction sites, creating foundations, trenches, and cuts for roads, railways, and other infrastructure in rocky terrain.
- Resource Extraction: In mining and quarrying, it facilitates the extraction of valuable minerals, ores, and aggregates by breaking up the rock overburden or the ore body itself.
- Tunneling and Underground Development: Blasting creates tunnels, shafts, and underground chambers for various purposes, including mining operations, hydropower projects, and transportation routes.
- Controlled Demolition: It can be used for the precise and safe demolition of rock structures or unwanted rock formations in a controlled manner.
Benefits of Rock Drilling and Blasting
Rock drilling and blasting offer a multitude of benefits that make them indispensable in industries requiring large-scale rock excavation. These advantages contribute significantly to project efficiency, safety, and economic viability:
- High Productivity: Blasting allows for the rapid fragmentation of vast volumes of rock, significantly accelerating project timelines compared to mechanical excavation methods.
- Cost-Effectiveness: For large-scale rock removal, drilling and blasting typically offer the lowest cost per cubic meter of excavated material, making projects more economically feasible.
- Versatility Across Rock Types: This method is effective across a wide spectrum of rock hardness, from soft to extremely hard formations, providing a flexible solution where other methods might struggle.
- Optimized Fragmentation: With proper blast design, the rock can be broken into a desired size range, which optimizes downstream processes like loading, hauling, and crushing, reducing overall operational costs.
- Reduced Equipment Wear: By fragmenting the rock, the strain on subsequent loading and hauling equipment is reduced, leading to less wear and tear and lower maintenance costs for machinery.
- Creation of Stable Excavations: Controlled blasting techniques can be employed to create stable rock faces and slopes, which is crucial for safety and the long-term integrity of civil engineering and mining structures.
What Kind of Engineers Are Involved in the Process of Drilling and Blasting?
Many types of engineers collaborate to ensure the safe and efficient execution of drilling and blasting operations. Their combined expertise covers the entire lifecycle of a project, from initial geological assessment to final rock excavation. Key engineering disciplines involved include:
Mining Engineers:
These engineers are central to the overall planning and management of drilling and blasting in mining and quarrying operations. They design blast patterns, select appropriate explosives, ensure compliance with safety regulations, and optimize fragmentation for efficient mineral extraction and processing. They consider the economic viability and environmental impact of the entire mining cycle.
Geotechnical Engineers:
Geotechnical engineers assess the rock mass properties, including its strength, structure, and geological discontinuities (like faults and joints). Their analysis is critical for understanding how the rock will behave during drilling and blasting, informing blast design to prevent instability, excessive vibrations, or unwanted ground movement. They also design ground support systems.
Explosives Engineers:
Specializing in the science and application of explosives, these engineers design the precise explosive charges, select the correct detonators and initiation systems, and determine the timing sequences for blasts. Their expertise ensures optimal rock fragmentation while controlling blast effects such as ground vibration, air blast, and flyrock, adhering to strict safety standards.
Civil Engineers:
In construction projects (e.g., roads, tunnels, dams), civil engineers are involved in planning and overseeing rock excavation to create stable foundations and structures. They work closely with other engineers to integrate drilling and blasting plans into the overall construction schedule and ensure the excavated rock meets project specifications.
Geologists:
While not strictly engineers, geologists play a foundational role by providing detailed information about the rock type, stratification, and structural features. This geological data is indispensable for engineers to design effective drilling and blasting plans that are responsive to the specific characteristics of the rock mass.
Mechanical Engineers:
Mechanical engineers design, maintain, and troubleshoot the drilling equipment and other machinery used in the process. They ensure that drill rigs, compressors, and other heavy equipment operate efficiently and safely, and they are often involved in developing new, more effective drilling tools and technologies.
Environmental Engineers:
These engineers focus on minimizing the environmental impact of drilling and blasting operations. They develop strategies to control dust, noise, and vibrations, manage water runoff, and ensure compliance with environmental regulations, particularly in sensitive areas or near populated zones.
Conclusion
In conclusion, mastering rock drilling and blasting techniques is paramount for safe, efficient, and cost-effective rock excavation. By carefully planning, selecting appropriate drilling tools and explosives, and adhering to rigorous safety protocols, projects in mining, construction, and quarrying can achieve optimal results.
Continuous learning and adaptation to new technologies and methods are key to improving productivity and minimizing environmental impact in this critical field.
For all your rock excavation needs, look no further. Get wholesale rock drilling tools directly from us at Sinodrills. Contact us to explore our extensive range of reliable equipment.