PDC (Polycrystalline Diamond Compact) drill bits are a game-changer in the world of drilling, known for their exceptional efficiency and durability. This guide will explore the fundamental question: “What is a PDC drill bit?” We will delve into their unique design and the key features that set them apart from traditional drill bits.
Understanding the technology behind PDC bits is crucial for anyone involved in drilling operations. By learning about their construction and how they function, you can make informed decisions that improve your drilling performance, reduce costs, and achieve faster penetration rates in various geological formations.
What is a PDC Drill Bit?
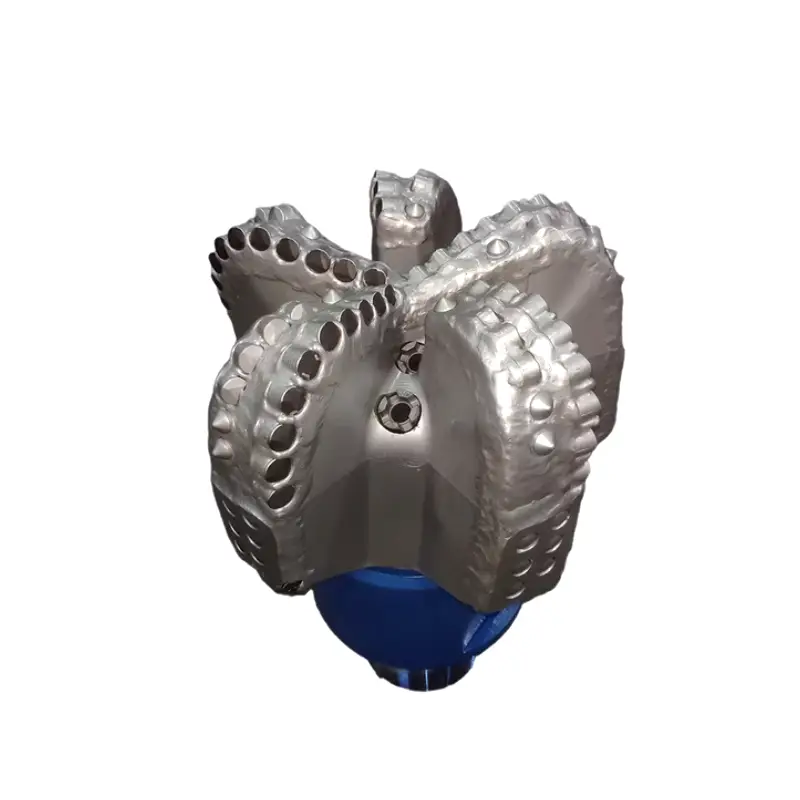
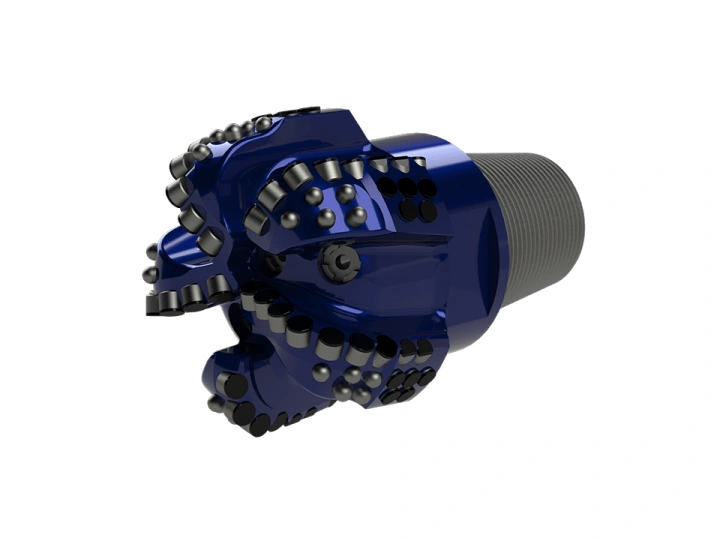
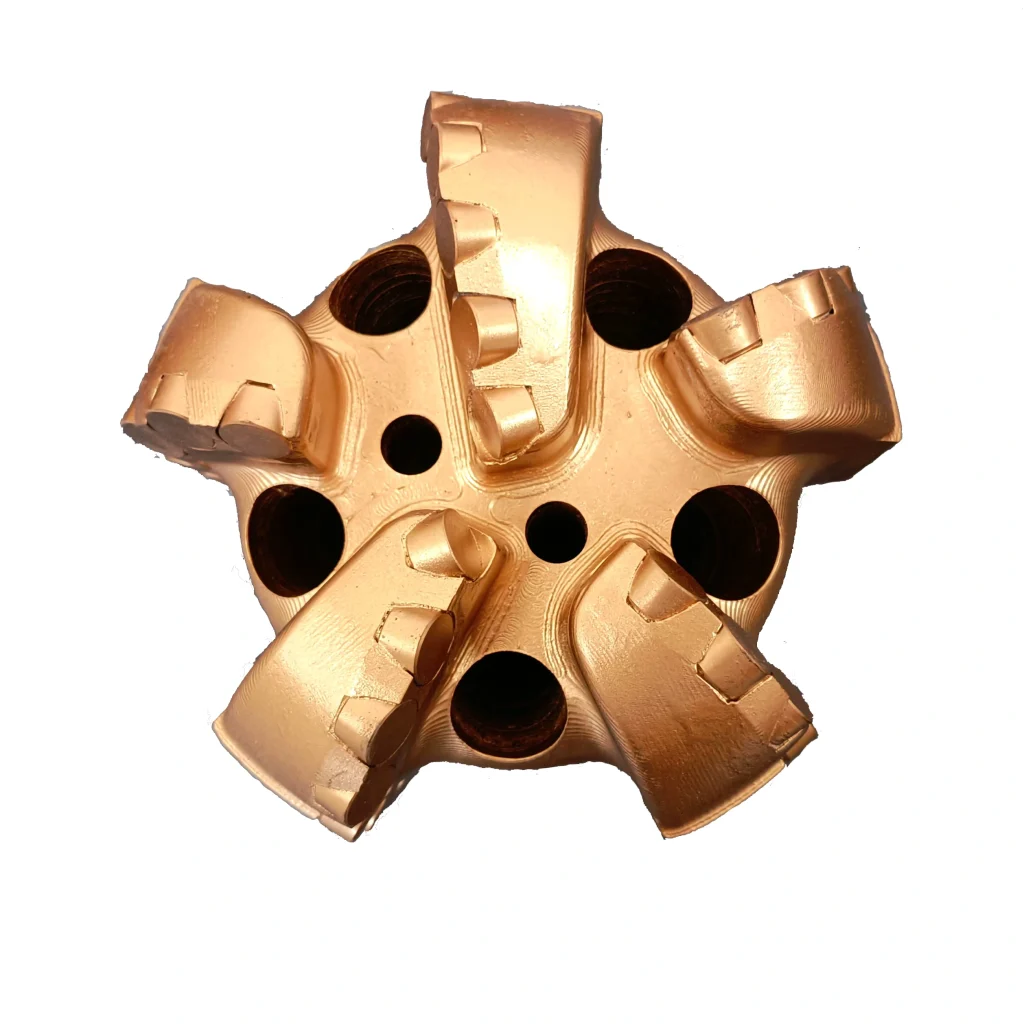
A PDC (Polycrystalline Diamond Compact) drill bit is a type of fixed-cutter drill bit widely used in drilling applications, especially in the oil and gas industry. Unlike traditional roller cone bits that crush rock, PDC bits feature industrial-grade synthetic diamond cutters bonded to a tungsten carbide substrate, which shear and scrape rock formations with a continuous motion.
This design allows for higher drilling efficiency, extended lifespan due to excellent wear resistance, and faster penetration rates in suitable formations like shales, limestones, and sandstones.
PDC Bit Design Parts
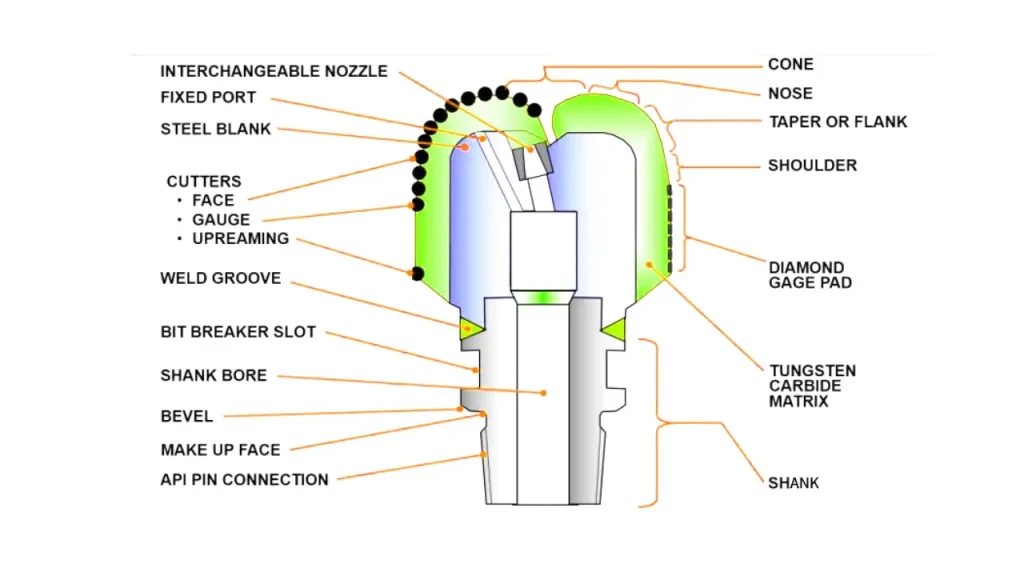
PDC drill bits are sophisticated tools, and their effectiveness is a result of the careful integration of several key components working in unison. Each part plays a vital role in the bit’s ability to cut rock efficiently, manage drilling fluids, and maintain structural integrity throughout the drilling process. These essential PDC bit components include:
- Shank: The threaded connection that attaches the bit to the drill string, transmitting torque and weight.
- Bit Breaker Slot: A recess on the shank designed for safely making up and breaking out the bit from the drill string using specialized tools.
- Weld Groove: Grooves or channels for welding different bit sections together, ensuring structural integrity and facilitating manufacturing or repair.
- Cutters (Face, Gauge, Upreaming): The primary cutting elements made of polycrystalline diamond, strategically placed on the bit face, gauge, and sometimes for upreaming, to shear rock.
- Steel Blank: The underlying steel structure for matrix body bits, providing the foundation for the tungsten carbide matrix and cutter placement.
- Fixed Port / Interchangeable Nozzle: Passages for drilling fluid to clean the bit face, cool cutters, and evacuate cuttings, with interchangeable options allowing for flow customization.
- Tungsten Carbide Matrix: A highly wear-resistant composite material forming the body of matrix bits, protecting the cutters and enduring abrasive formations.
- Diamond Gage Pad: Wear-resistant inserts on the bit’s outer diameter, often diamond-impregnated, to maintain the desired hole size and prolong bit life.
- Shoulder: The transitional area between the bit’s cone/nose and the gauge, contributing to stability and housing cutters.
- Taper or Flank: The conical or curved surface extending from the nose to the shoulder, aiding in hole enlargement and guiding the bit.
- Nose: The central, leading-edge section of the bit that first engages the rock, initiating the cutting action and significantly influencing penetration rate.
- Cone: The overall conical profile of the bit’s cutting structure, influencing how weight on bit and cutting forces are distributed across the formation.
PDC Drill Bit Working Principle
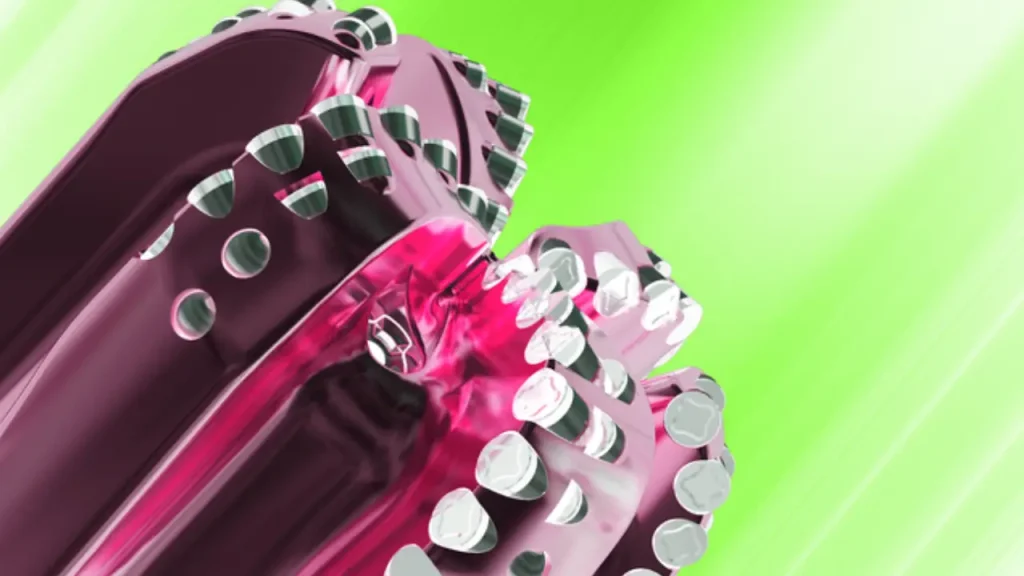
PDC drill bits operate on a fundamental shearing principle, rather than the crushing and grinding action of traditional roller cone bits. The bit’s face is embedded with numerous Polycrystalline Diamond Compact (PDC) cutters, which are small, fixed-cutter elements made of a synthetic diamond layer bonded to a tungsten carbide substrate.
As the bit rotates, these cutters engage the rock formation and slice away thin layers, a highly efficient process that requires less weight on bit and generates less heat than other drilling methods. The specific arrangement and angle of the cutters, along with the bit’s hydraulic design, are engineered to optimize this shearing action and efficiently channel drilling fluid to cool the cutters and remove rock cuttings from the wellbore.
- Shearing Action: The PDC cutters slice and shave away rock formations, providing a highly efficient method of rock destruction.
- PDC Cutters: Fixed, non-moving cutters with a diamond layer bonded to a tungsten carbide substrate for exceptional hardness and durability.
- Bit Body Design: The geometry and cutter placement are meticulously engineered to optimize rock removal and withstand high drilling forces.
- Hydraulic Efficiency: Strategically placed nozzles direct drilling fluid to cool the cutters and flush rock cuttings away, preventing bit balling and improving penetration.
PDC Efficiency
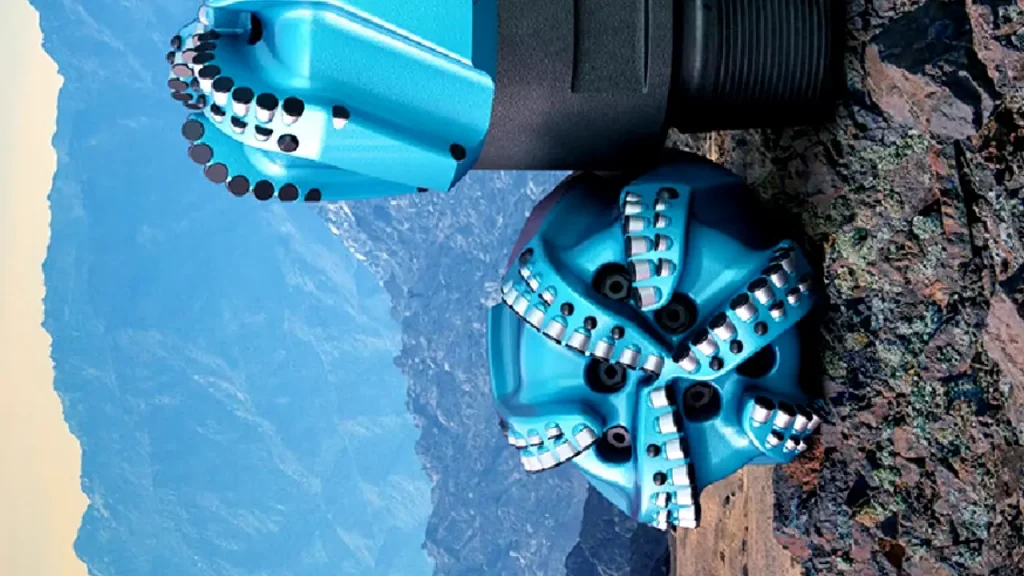
PDC bits significantly enhance drilling efficiency by leveraging a superior cutting mechanism that provides a faster and more durable solution compared to traditional roller cone bits. Unlike roller cone bits that crush and grind rock, PDC (Polycrystalline Diamond Compact) bits use a shearing action. This method is far more efficient at removing rock, resulting in a higher Rate of Penetration (ROP), which can be up to 50% faster in suitable formations.
This increased speed, combined with the exceptional hardness and wear resistance of the synthetic diamond cutters, allows for longer drilling runs without needing to pull the drill string out of the hole to replace the bit. This reduces downtime and operational costs, making them a highly cost-effective choice for modern drilling projects.
- Higher Rate of Penetration (ROP): PDC bits’ shearing action allows them to drill much faster, particularly in soft to medium-hard formations like shale, reducing the overall time required to complete a well.
- Reduced Downtime: The durability and longevity of PDC cutters mean fewer trips out of the hole to change bits. This saves significant time and money, as pulling and replacing a bit is a major logistical and financial effort.
- Improved Hole Quality: The smooth cutting action of PDC bits creates a cleaner, more stable borehole with fewer chips and cracks, which helps reduce the risk of stuck pipes and makes subsequent casing and cementing operations easier.
- Versatility: PDC bits are adaptable to various geological conditions and can be optimized for specific applications by changing the cutter layout and blade design, allowing for efficient drilling in both straight and directional wells.
What is PDC Drill Bit Used for?
PDC (Polycrystalline Diamond Compact) drill bits are versatile and highly efficient tools primarily used in a variety of drilling operations due to their superior cutting action and durability. Their design, featuring synthetic diamond cutters, allows them to shear and scrape rock formations rather than crush them, leading to faster penetration rates and longer bit life.
These bits are widely employed across several industries and for specific geological conditions:
Oil and Gas Drilling: This is a primary application, where PDC bits are crucial for drilling exploration and production wells. They are particularly effective in drilling through:
- Shale
- Sandstone
- Limestone
Geothermal Drilling: PDC bits are well-suited for the extreme heat and abrasive conditions encountered in geothermal wells, offering reliable performance and longevity.
Mining Operations: They are used for exploration drilling to identify mineral deposits and for drilling through hard rock formations in mines, ensuring faster penetration and reduced downtime.
Water Well Drilling: PDC bits are effective for quickly penetrating various formations, from soft clays to hard rock, reducing drilling time and costs for water well projects.
Construction Projects: They find application in drilling foundation piles and other structural elements.
Oil and Gas PDC Drilling Tools
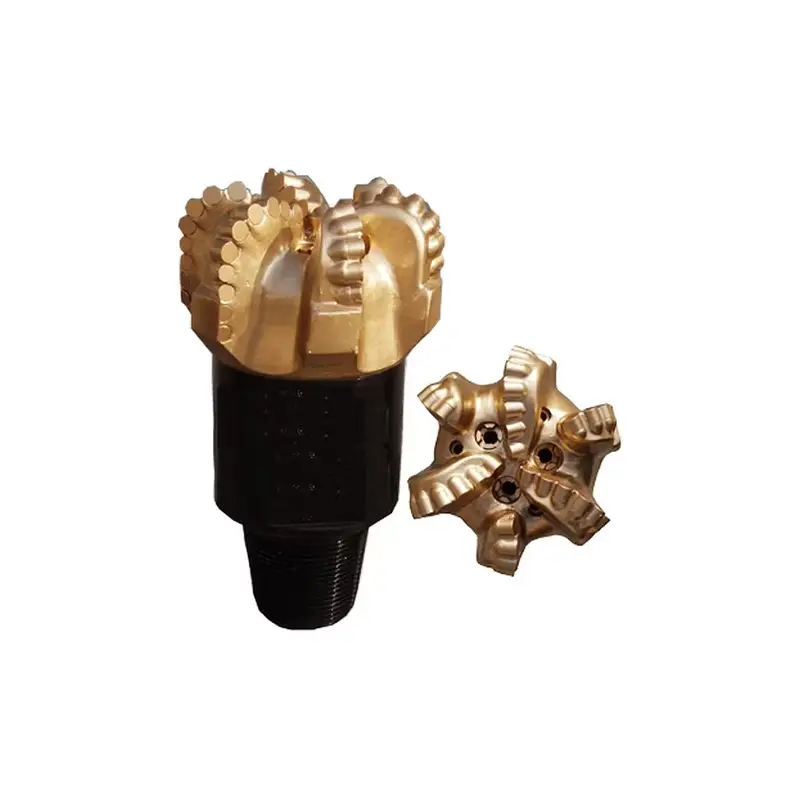
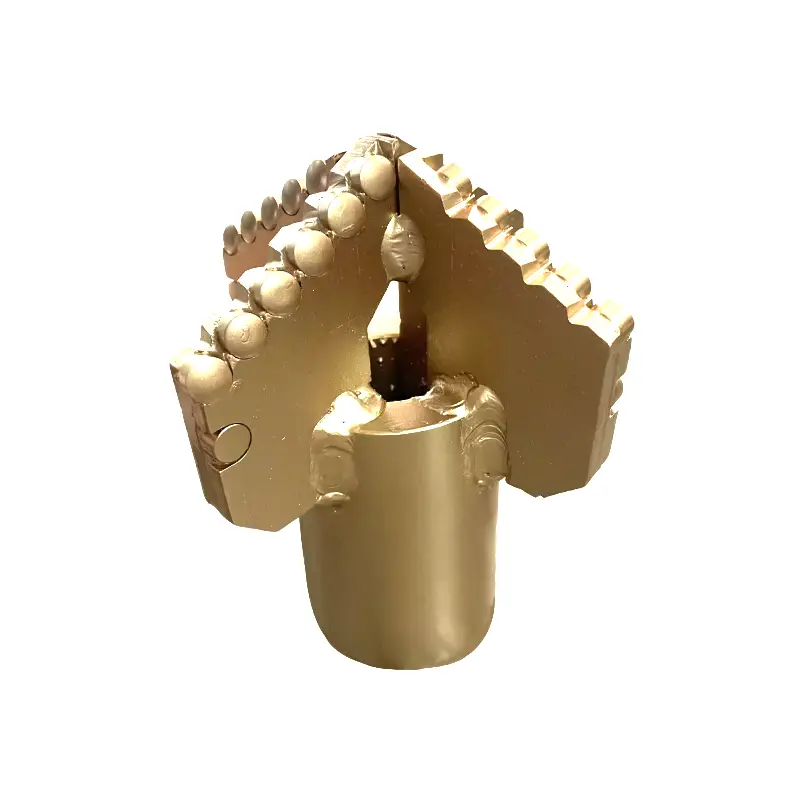
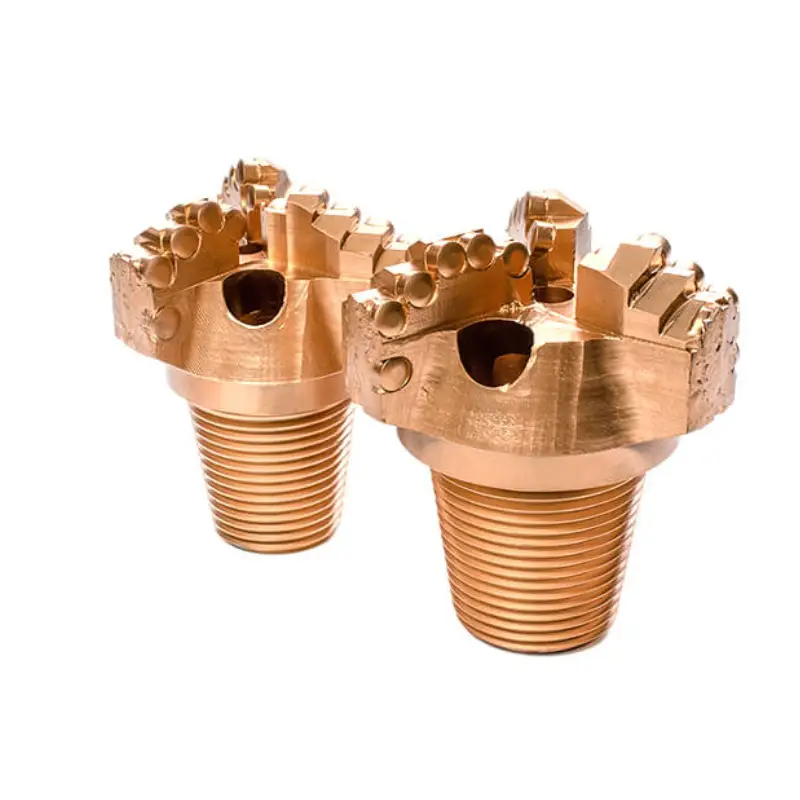
Polycrystalline Diamond Compact (PDC) drilling tools, particularly PDC drill bits, have become essential in the oil and gas industry due to their exceptional durability and efficiency. They are engineered with synthetic diamond cutters bonded to a tungsten carbide substrate, allowing them to shear through rock formations rather than crushing them. This shearing action results in a higher rate of penetration (ROP), which significantly reduces drilling time and costs.
PDC bits are highly versatile and are particularly effective in drilling through softer-to-medium rock formations such as shale, sandstone, and limestone. They are widely used in both conventional vertical drilling and advanced directional and horizontal drilling applications.
- Steel-Body PDC Bits: These bits are made from high-strength steel and are known for their durability and ease of repair. Their design allows for large junk slots, which improve the removal of cuttings in soft, sticky formations like shale.
- Matrix-Body PDC Bits: Made from a tungsten carbide powder matrix, these bits offer superior resistance to erosion and impact. They are ideal for drilling in highly abrasive formations where steel-bodied bits would wear out quickly.
- Hybrid PDC Bits: Combining the continuous shearing action of PDC cutters with the crushing action of rolling cones, hybrid bits are designed for maximum versatility. They excel in interbedded formations where layers of hard and soft rock are present.
- Coring PDC Bits: These specialized bits feature a hollow center that allows them to cut a cylindrical rock sample, or core, as they drill. This is crucial for geological analysis and reservoir evaluation in exploration.
Enhance Drilling Efficiency With the PDC Arc Drill Bit-5 Wings
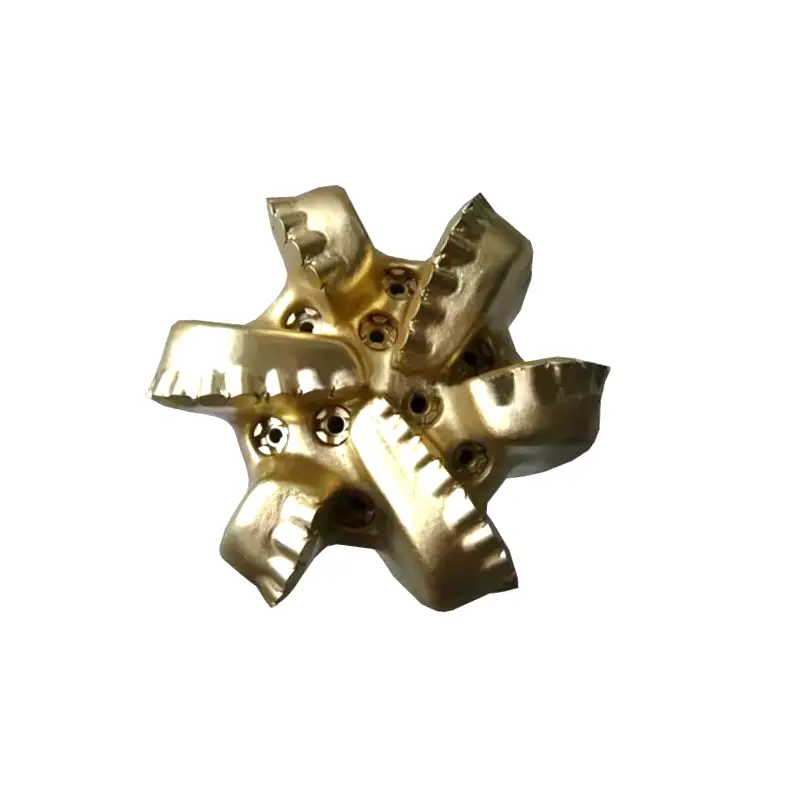
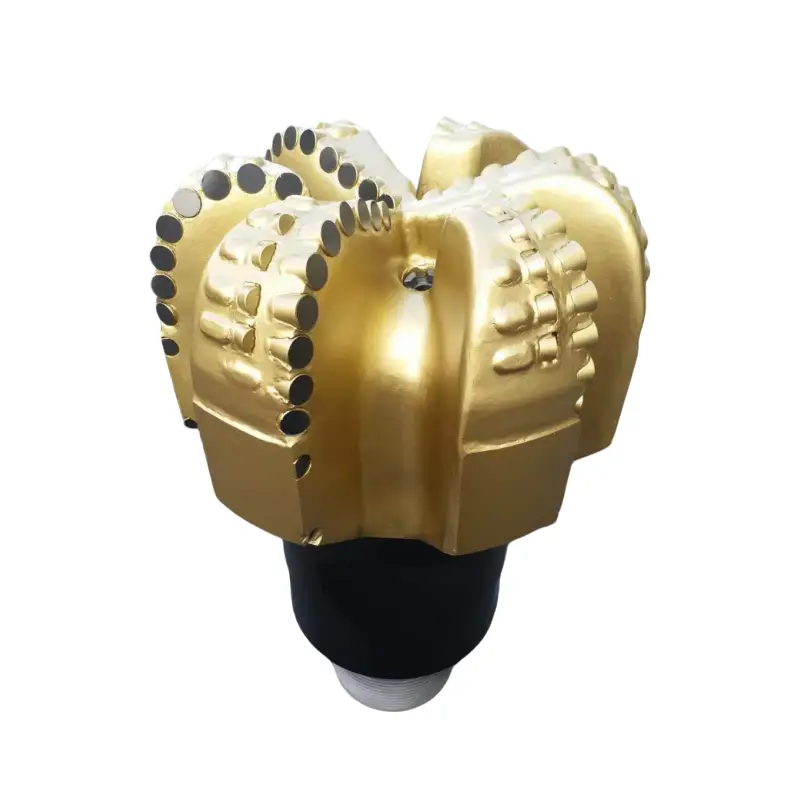
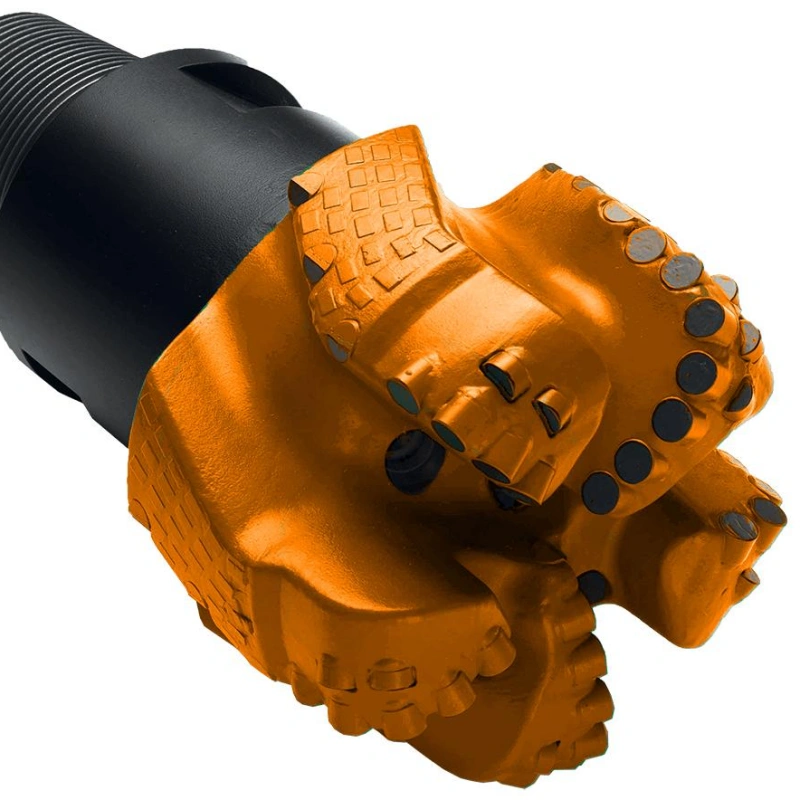
The PDC arc drill bit with 5 wings is a specialized design engineered to significantly enhance drilling efficiency, particularly in soft to medium-hard formations such as mudstone, limestone, shale, and sandstone.
The “arc” profile refers to the curved shape of the bit face, which aids in optimizing the cutting action and improving directional control. The inclusion of five wings, or blades, further distributes the cutting forces, contributing to smoother operation and extended bit life.
This configuration offers several key advantages that contribute to improved drilling performance:
- Increased Rate of Penetration (ROP): The optimized arc design combined with multiple cutting wings allows for more aggressive and continuous shearing of the rock, leading to faster drilling speeds. The five-blade design provides more cutting elements in contact with the formation, enhancing the overall cutting efficiency.
- Enhanced Stability and Reduced Vibration: The symmetrical distribution of five wings helps to balance the bit, minimizing torsional and lateral vibrations during drilling. This leads to a smoother drilling operation, reducing wear and tear on drilling equipment and improving overall wellbore quality.
- Improved Cuttings Evacuation: The design of the arc and the spaces between the five wings are engineered to optimize fluid flow. This efficient hydraulic design ensures better removal of rock cuttings from the bottom of the hole, preventing “bit balling” (where cuttings accumulate and hinder the bit’s performance) and maintaining a clean cutting face.
- Extended Bit Life: By distributing the cutting load across more blades and ensuring efficient cooling and cleaning, the 5-wing arc bit experiences less localized wear. This translates to a longer service life for the bit, reducing the need for frequent bit trips and ultimately lowering drilling costs.
What is the difference between PDC and PCD?
While often used interchangeably in casual conversation, “PDC” and “PCD” refers to distinct but related concepts in the context of drilling and cutting tools. The key difference lies in what each acronym represents:
- PCD (Polycrystalline Diamond): This refers to the material itself. PCD is a synthetic superhard material created by sintering together many micro-sized single diamond crystals under high pressure and high temperature, often with a metallic binder. It’s essentially a solid mass of randomly oriented diamond grains.
- PDC (Polycrystalline Diamond Compact): This refers to a composite cutting element that incorporates PCD. A PDC cutter consists of a layer of PCD bonded to a much tougher, less brittle tungsten carbide substrate. This compact design leverages the extreme hardness and wear resistance of the PCD layer for cutting, while the carbide backing provides structural integrity and impact toughness, making it suitable for demanding industrial applications like drill bits.
PDC Drill Bit vs Tricone
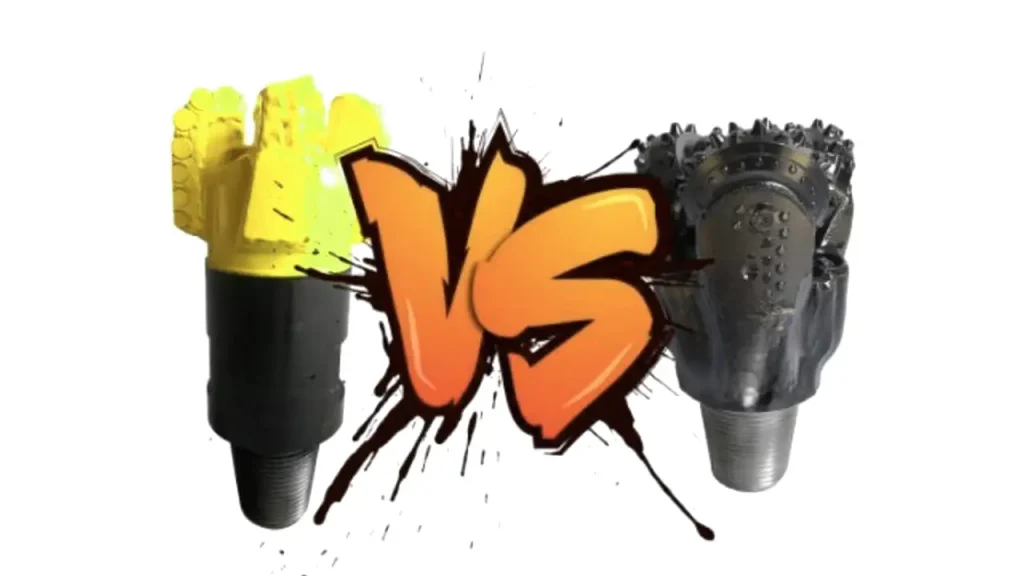
PDC (Polycrystalline Diamond Compact) and Tricone drill bits represent the two primary technologies in modern drilling, distinguished by their fundamental working principles and optimal applications. PDC bits are fixed-cutter tools that operate by a shearing action, with synthetic diamond cutters scraping and slicing the rock away. This makes them exceptionally efficient in soft to medium-hard, non-abrasive formations, where they can achieve very high rates of penetration and offer a long service life.
In contrast, Tricone bits use three rotating cones with either milled steel teeth or tungsten carbide inserts that crush, chip, and grind the rock as they roll. This crushing action makes them more versatile and particularly effective in hard, abrasive, and interbedded formations where the shearing action of a PDC bit might be less efficient or cause premature wear.
- Working Principle: PDC bits shear rock, while Tricone bits crush and grind rock.
- Formation Suitability: PDC bits excel in soft to medium, non-abrasive formations; Tricone bits are more versatile and perform well in hard, abrasive formations.
- Penetration Rate (ROP): PDC bits generally achieve a higher ROP in suitable formations.
- Durability: PDC bits have no moving parts, leading to longer bit life in ideal conditions. Tricone bits have bearings that can fail.
- Cost: The initial purchase price of a PDC bit is often higher, but its longer lifespan and faster ROP can result in a lower cost per foot.
PDC Drill Bit Cost
The cost of PDC drill bits can vary significantly, influenced by a range of factors that reflect their advanced engineering, material quality, and specialized design.
Understanding these elements is crucial for budgeting and making informed procurement decisions for drilling operations. Key factors affecting PDC bit cost include:
- Bit Size: Larger diameter bits require more raw materials and complex manufacturing processes, naturally leading to a higher cost compared to smaller bits, reflecting the increased material and labor inputs.
- Design Complexity: Bits with more intricate designs, such as those with specialized cutter layouts, unique body profiles (e.g., hybrid designs), or advanced hydraulic features, typically command a higher price due to the increased R&D and manufacturing precision involved.
- Material Quality: The grade and quantity of PDC cutters, the type of bit body material (e.g., premium matrix vs. standard steel), and other wear-resistant inserts directly impact the cost, as higher quality materials offer superior performance and longevity.
- Customization: Custom-designed PDC bits, tailored for specific geological formations or unique drilling challenges, will incur additional costs due to specialized engineering, unique tooling, and limited production runs compared to standard off-the-shelf options.
- PDC Bit Manufacturer and Brand: Reputable manufacturers with extensive research and development, stringent quality control, and established brand recognition often price their PDC bits higher, reflecting their proven performance, reliability, and support services.
Why Choose Our PDC Drill Bits
Choosing the right PDC drill bit is paramount for optimizing drilling operations and achieving cost-efficiency. Our PDC drill bits are designed with advanced technology and high-quality materials to deliver superior performance across a wide range of geological formations. We prioritize durability, efficiency, and consistent results, ensuring that our bits can withstand challenging drilling conditions and provide an extended lifespan.
Here’s why our PDC drill bits stand out:
- Exceptional Durability and Extended Life: Crafted with premium polycrystalline diamond compact cutters bonded to robust tungsten carbide substrates, our bits offer unparalleled wear resistance and impact toughness. This construction minimizes premature wear and reduces the frequency of bit replacements, significantly cutting down on non-productive time and overall drilling costs.
- Superior Rate of Penetration (ROP): Our PDC bits feature optimized cutter placement and hydraulic designs that maximize cutting efficiency. This results in significantly faster penetration rates, allowing you to complete drilling projects more quickly and efficiently, saving both time and fuel.
- Enhanced Stability and Wellbore Quality: The balanced design of our PDC bits helps to reduce vibration during drilling. This leads to smoother operations, less stress on drilling equipment, and the creation of a cleaner, more consistent wellbore, which is crucial for subsequent operations.
- Versatility Across Formations: While excelling in soft to medium-hard formations like shale, sandstone, and limestone, our PDC bits are also engineered to perform effectively in a variety of other challenging geological conditions, offering adaptability for diverse drilling projects.
- Optimized Cuttings Evacuation: Our bit designs incorporate efficient fluid channels that ensure rapid and effective removal of rock cuttings from the borehole. This prevents “bit balling” and maintains a clean cutting face, further enhancing drilling efficiency and bit longevity.
Conclusion
PDC drill bits are essential for efficient and cost-effective drilling in various formations. Understanding their design and applications can significantly improve drilling operations. For reliable and high-performance PDC drill bits, consider partnering with a trusted wholesale supplier like Sinodrills.
Sinodrills offers a comprehensive range of PDC drill bits designed to meet diverse drilling needs. Their commitment to quality and innovation ensures you receive durable and effective tools for your projects.
Optimize your drilling performance by choosing Sinodrills for your wholesale PDC drill bit requirements.