In the world of precision manufacturing and construction, creating a hole is often just the first step. While drilling forms the initial bore, achieving exact dimensions, superior surface finish, and true roundness requires an additional, crucial process: reaming.
This guide will delve into what reaming entails in drilling operations, explaining its purpose, how it differs from simple drilling, and why it’s indispensable for applications demanding high-quality, precise holes.
What is Reaming in Drilling?
In drilling, reaming is a precision finishing process that follows the initial creation of a hole by a drill bit or coring.
Its primary purpose is not to create a new hole, but to enlarge, true, and smooth an existing one to very accurate dimensions and a superior surface finish. This is particularly crucial in applications like horizontal directional drilling (HDD) for rock, where the final bore must meet strict specifications for pipeline installation.
Key aspects of reaming in drilling include:
- Precision Enlargement: Reaming removes only a minimal amount of material from the walls of a pre-drilled hole, bringing it to a highly exact and consistent final diameter.
- Improved Hole Quality: It significantly enhances the roundness, straightness, and concentricity of the bore, correcting any inaccuracies left by the initial drilling process.
- Smoother Surface Finish: The multiple cutting edges of a reamer shave the bore walls, resulting in a much smoother internal surface compared to a drilled hole.
- Application in Rock Drilling: For HDD in rock, reaming involves specialized rock reamers that progressively enlarge the pilot bore to the required size, creating a stable and clean pathway for product installation.
- Preparation for Installation: A reamed hole ensures a proper fit for components like pipes, bearings, or pins, minimizing friction and potential damage during installation and throughout the product’s lifespan.
What is a Reamer Drill Bit Used For?
While a “reamer drill bit” might sometimes be used loosely to describe a tool that combines aspects of both, it’s crucial to understand their distinct primary functions in the industry of professional rock drilling.
A drill bit is engineered for the initial act of creating a hole, breaking through solid rock formations to establish a pilot bore or the full production hole. It prioritizes aggressive material removal and penetration rate, using designs like tricone cutters or PDC elements to crush, cut, or abrade the rock.
A reamer, particularly an HDD rock reamer, is then used in a subsequent operation. Its purpose is not to start a new hole but to enlarge and refine an existing one to a precise diameter and achieve a smoother, more stable bore wall. This is vital for installing pipelines or conduits where accurate sizing and a clean path are critical for successful pull-back and long-term integrity. Therefore, while both tools create or expand holes, their applications are sequential and focused on different aspects of the hole-making process.
Here’s what each is used for:
What a Drill Bit is Used For (in Rock Drilling):
- Creating Pilot Holes: Drill bits are fundamental for boring the initial, smaller diameter hole that establishes the trajectory and path for the entire project. This is the first step in most directional drilling operations.
- Production Drilling: In some cases, drill bits are used to create the final production hole directly, especially in conventional vertical drilling or when the final hole tolerance is less critical.
- Geological Exploration: Drill bits are used to extract core samples or cuttings to understand the subsurface geology and plan subsequent drilling and reaming operations.
- Setting Casing: Drill bits can also be integral to operations that involve drilling and setting initial casing strings in unstable formations.
What a Reamer is Used For (in Rock Drilling, specifically HDD Rock Reamers):
- Hole Enlargement (Reaming): The primary use of an HDD rock reamer is to systematically enlarge a previously drilled pilot bore to the desired final diameter, ready for the product pipeline or conduit. This often involves multiple passes with progressively larger reamers.
- Borehole Stabilization: As reamers enlarge the hole, they also help to condition and stabilize the bore walls, removing irregularities and creating a smoother, more consistent path for the product.
- Efficient Cuttings Management: Reamers are designed to facilitate the efficient flow and removal of rock cuttings by the drilling fluid, preventing blockages and ensuring a clean bore.
- Facilitating Product Pull-Back: By creating a precisely sized and clean bore, reamers significantly reduce friction and resistance during the critical phase of pulling the product pipe through the enlarged hole.
How to Use a Reamer Drill?
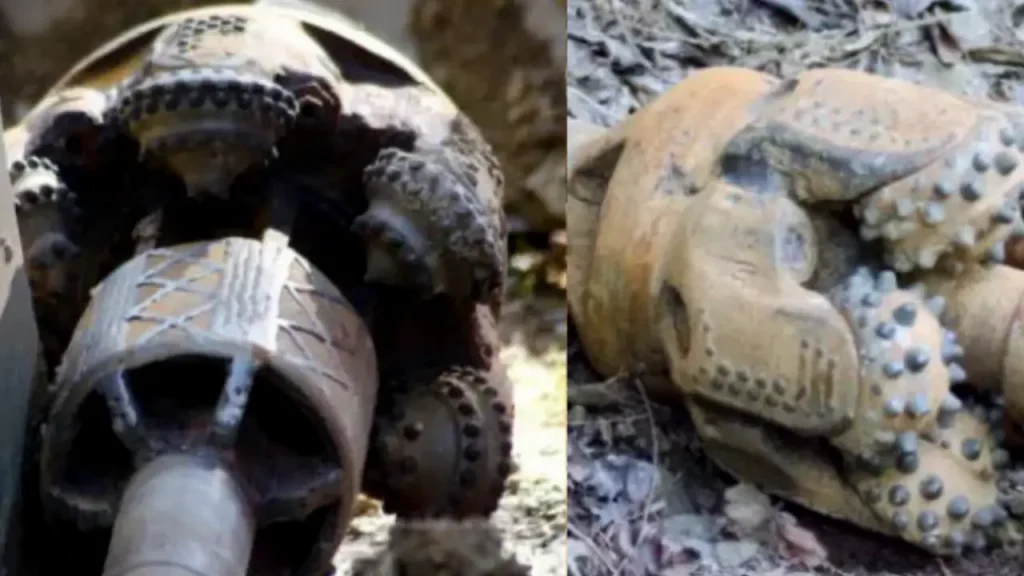
Using a reamer in rock drilling, particularly an HDD rock reamer, is a multi-step process crucial for enlarging and finishing a bore after the initial pilot hole has been drilled. Proper technique ensures efficiency and a high-quality finished bore.
This guide outlines the key steps involved in effectively using a reamer for rock drilling applications, ensuring successful pipeline or conduit installation.
Step 1: Pre-Drill Pilot Hole
Before reaming, an initial pilot hole must be drilled along the precise path. This smaller diameter hole establishes the exact trajectory and removes the bulk of the rock, creating a guide for the subsequent reaming operation. The pilot hole ensures the reamer follows the intended design.
The pilot hole’s accuracy is critical, as any deviation here will affect the final reamed bore. The drill bit used for this step is selected based on the rock type and required penetration rate, focusing on establishing the initial path efficiently.
Step 2: Select the Correct Reamer
Choosing the appropriate reamer is paramount. This involves matching the reamer’s type (e.g., roller cone, fixed blade) and cutter configuration to the specific rock formation’s hardness and abrasiveness. The desired final bore diameter also dictates the reamer’s size.
Consider the product pipe’s outer diameter; the reamer’s size should provide adequate annular space for fluid flow and pullback. Incorrect reamer selection can lead to excessive wear, reduced efficiency, or an improperly sized bore.
Step 3: Attach Reamer to Drill String
Once selected, the reamer is securely attached to the drill string. This connection is typically made at the exit side of the pilot hole (for pullback reaming). Ensure all threads are clean and properly torqued according to the rock reamer manufacturer’s specifications to prevent disconnection during operation.
A secure connection is vital for safety and operational efficiency. Any weakness in the connection can lead to tool loss downhole or catastrophic failure, causing significant project delays and costs.
Step 4: Initiate Reaming Operations
Begin rotating the drill string while simultaneously applying pullback force. The reamer’s cutting structures engage the rock at the pilot hole’s circumference, progressively enlarging the bore. Maintain a consistent rotational speed (RPM) and pullback rate.
Pumping drilling fluid is crucial during this step. The fluid cools the reamer, lubricates the bore, and most importantly, carries the rock cuttings back to the surface, keeping the hole clean and preventing blockages.
Step 5: Monitor and Adjust
Continuously monitor drilling parameters such as torque, pullback pressure, drilling fluid pressure, and penetration rate. These readings provide real-time feedback on the reamer’s performance and rock conditions.
Adjust RPM, pullback speed, and fluid flow as needed to optimize performance and prevent overloading the rig or reamer. If significant changes in rock type are encountered, parameters may need fine-tuning for efficiency.
Step 6: Multiple Passes (if necessary)
For very large diameter bores or extremely hard rock, it may be necessary to perform multiple reaming passes. This involves using progressively larger reamers, each enlarging the bore in stages until the final desired diameter is achieved.
Staging the reaming process reduces stress on the equipment and allows for more controlled enlargement. It also improves bore stability by gradually expanding the tunnel, minimizing the risk of collapse.
Conclusion
In essence, reaming transforms a basic drilled hole into a precise bore. It’s a critical finishing step that ensures proper sizing, superior surface finish, and improved roundness, indispensable for applications demanding tight tolerances and reliable performance, especially in challenging rock formations.
Understanding the distinct role of reaming versus initial drilling is vital for successful project execution and maximizing the longevity of installed components. This process significantly contributes to the overall integrity and efficiency of your drilling operations.
For all your rock drilling needs, including top-quality wholesale rock reamer tools designed for durability and precision, look no further than Sinodrills. Based in Qingdao, Shandong, China, we are your trusted partner for robust drilling solutions.